One of our #CFAConcretePros Receives Local Recognition

MUDco Ready-Mix Concrete
KRISTI EGENBACHER
Current position: Chief Administrative Officer
Years in business: I started my career in the restaurant sector in the early 1990s, launched my own bookkeeping business in 1997 to begin my journey of a “working-from-home mom,” began my concrete/construction career in 2007, and most recently partnered to open MUDco in 2015.
Education: Bachelor of Science in Marketing, Texas Tech University
Claim to fame: I am proud of the fact that I have helped more than a dozen women begin their business careers and balance the joy of earning a living with the responsibilities that come with raising children. Being a stay-at-home mom who also works from home presents unique challenges. I’m fortunate that throughout my life some very special people have encouraged and supported me while cheering for my success.
Business philosophy: Find great people and train them to pursue excellence through efficiency in every aspect of their role in the operation.
Greatest professional accomplishment: I was one of the first two women to pass an extremely challenging exam and receive a much-sought-after certification through the American Concrete Institute and Concrete Foundations Association.
Greatest personal accomplishment: Applying FlyLady, Marie Kondo, and 2-Second Lean Methods to balance the following titles: “Wife,” 24 years, “Mom,” 21 years, and multiple business owner/ entrepreneur.
Community involvement: Our business is always looking for ways to reduce our impact on the environment through recycling efforts and limiting our footprint. Lubbock is my home and the entire MUDco team strives to keep it beautiful!
Competitive edge: My desire is to look for ways to do things differently through innovation and technological advances.
A word of advice: Know your “why.”
Letter From the Director
Fear vs Caution
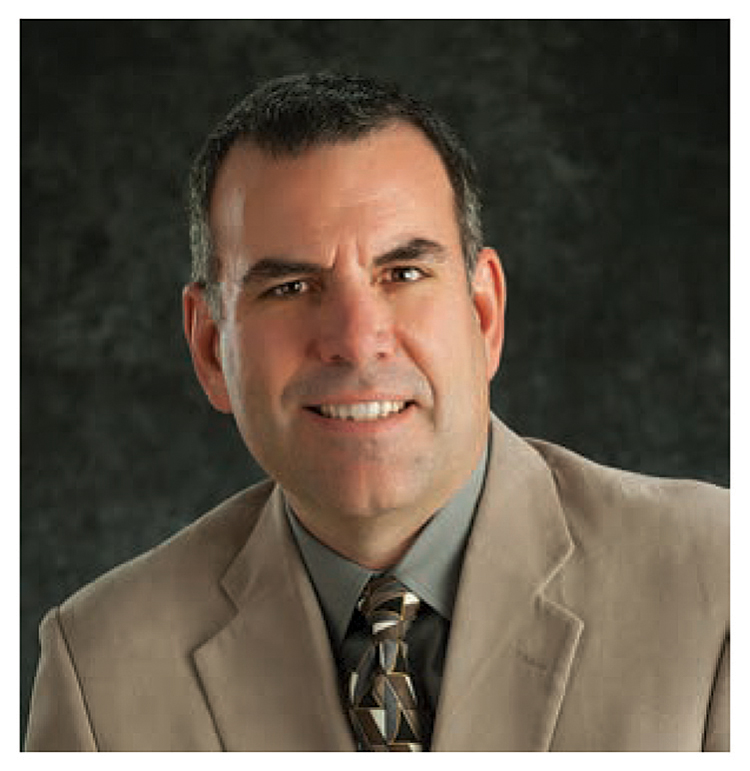
We are now gripped by the global news of COVID-19, and we are being asked to remain flexible and nimble in our reactions and expectations. This pandemic is reaching into every aspect of our worlds, and, no doubt, you can already list numerous disruptions to your businesses and personal lives. One of the most responsible things any business or organization can do at this time is to minimize risk by participating in the efforts to flatten the curve of the spread of the virus by following CDC and WHO recommended guidelines. So, what is the Concrete Foundations Association doing about it?
I read a recent post about the difference between fear and caution. The prior paralyzes individuals and populations and results in no progress, no way forward, and even no defense. The latter, however, urges common sense and encourages the mind to propose solutions, find alternatives, and rationalize opportunities. Franklin D. Roosevelt famously said:
“First of all, let me assert my firm belief that the only thing we have to fear is fear itself — nameless, unreasoning, unjustified terror, which paralyzes needed efforts to convert retreat into advance.”
CFA leadership has already been challenged organizationally by the risks associated with carrying on business as normal. The American Concrete Institute (ACI) was forced to cancel the Spring Concrete Convention, only the second time in history the bi-annual event has been canceled (the other instance was after 9/11). Usually, the board of directors uses this event for two of their four meetings, and several directors participate in some of the technical committee activities that are advancing residential concrete codes, cold weather concrete best practices, and even certification. Like ACI, however, the board is pivoting and planning to carry on business as usual instead of business as normal.
In today’s age of technology, we have continued to desire face-to-face meetings. There is no doubt that the greatest value of in-person gatherings is the ability to set aside technology long enough to invest in relationships, in listening, in reading facial expressions, and in simply hearing others’ voices. It is in times like these, however, that technology becomes our facilitator, permitting business to be conducted, and it is up to us to stop long enough (even with the distractions around us) to listen for what we know those facial expressions might be. That is, unless we are using video conferencing, which is also there for us to take advantage of during this time.
The question many may be tempted to ask is, “What about Concrete Foundations Convention 2020?” Well, what about it? — is the only answer that can be given at this time. The rapidly changing national and international response to this pandemic currently leaves us knowing we should establish social distancing and protect our most vulnerable and communicable populations. This way, our medical communities will be better equipped to respond quickly with available resources. While this happens, we will continue to strengthen our plans for this next great gathering of #CFAConcretePros in Charleston, South Carolina, July 23-25. As we get into summer months, we will either be assured of having a safe physical environment for us all to gather at, or we will have an alternative plan of action that will, by that point, have been put together from rational, considerate contemplation.
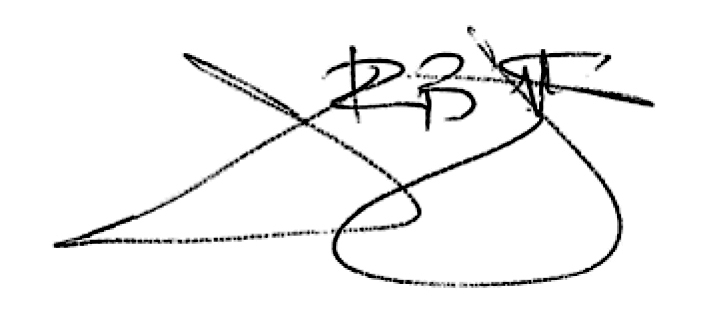
Letter from the President
Waging Battles
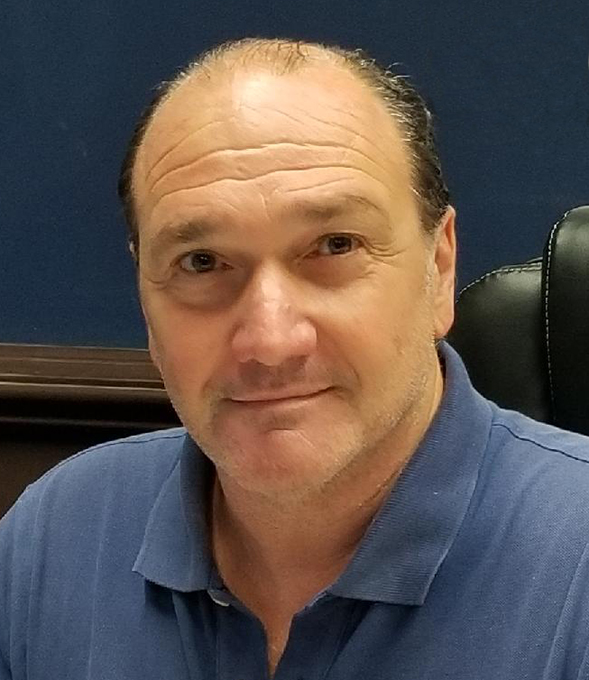
Dear CFA Members and Associates,
By the time you read this article, we will all have experienced something that has never before happened to any of us. On March 12, 2020, the world changed (seemingly overnight) both in business and socially. I assume we will be feeling the ramifications of this change for some time to come!
First, let me say that I hope all of you are faring well and successfully navigating this tough road. Things are, once again, changing fast politically and in our businesses. Unfortunately, many challenges lie ahead for us.
Observing the political climate feels like being on a seesaw. Concrete and aggregate pricing continues to rise above inflation levels, the labor pool is tough for various reasons, and most of us are experiencing pricing competition that, at times, defies rational logic! Additionally, the cost of insurance, particularly umbrella coverage, will be an increasing concern.
It is in times like these that we can rely on the CFA and our members for help and guidance. As a group, we need to push harder and further to improve our organization and help each other survive the pressures that impact us, helping us survive and thrive.
To do our part, our board meeting this spring will be held via videoconferencing, due to the coronavirus affecting national meetings and particularly changing the business environment in Chicago. The executive committee made this decision for everyone’s safety and to make sure we participate responsibly amid this pandemic.
I personally wish the best for you, your families and businesses during the challenges of this crisis.
Sincerest regards,
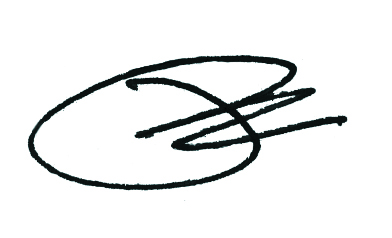
Phillip Marone
#CFAConcretePros Now Have Virtual Mixed Groups
Mt. Vernon, Iowa (April 1, 2020) — The Concrete Foundations Association (CFA) – the voice and established authority for the residential concrete industry – has announced the availability of a new member resource instituted as part of the COVID-19 response. Virtual Mixed Groups (VMGs) have been started combining members at-large with Board members to combat isolation, share experiences and help grow resources.
During their Spring Board meeting held virtually this week, the Board of Directors considered the benefit that meeting together in a virtual conference had for them personally.
Taking this a step further, the decision was made to begin creating some small sessions that would permit us to create vital connection during this time of uncertainty, sharing between members and help us make sure we know what needs are out there as well as ways of meeting all our members where you are.
Beginning this Thursday, we are offering spaces using our our virtual meeting space at Zoom for five members at-large to meet with two of our Board members and a staff member (initially). During this time, it is all about sharing. Nothing else is on the agenda. This is a check in to see what is going on your state, your business…find out what your struggles and pressure points are both professionally and personally.
“One of the greatest statements of CFA membership resources is the sharing that takes place within our peer circles,” states Board President, Phillip Marone of Marone Contractors, Philadelphia, PA. “During this time of great need, just to be known and in conversation can be one of the most powerful resources and benefits to you and we have an unanimous Board desiring to take the lead on connecting.”
Please contact CFA staff as soon as possible to find out more about getting involved and to receive the sign-up link. Additional VMGs are spinning up each week to support the widening participation as the Association goal is to find every member into a group for regular meetings. Meetings are encouraged to take place bi-weekly but each group further defines what this is and what the individual interest goals should be.
WHAT LEADING CONSTRUCTION COMPANIES ARE DOING IN THE WAKE OF COVID-19
This article made possible by ConExpo-Con/AGG 2020 as part of industry participation by your Concrete Foundations Association. For more information on business practices by contractor members of the Concrete Foundations Association, reach out to CFA Executive Director, James Baty
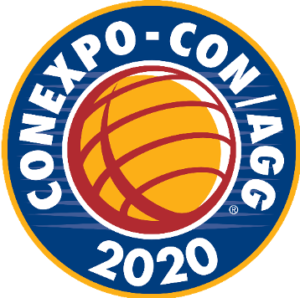
MILWAUKEE — As COVID-19 (coronavirus) brings countless businesses to a grinding halt, the construction industry remains resilient — even in the face of tremendous challenge.
Unlike many industries where “working from home” and “drive-thru service” are feasible countermeasures, construction firms have jobsites to run. Chris Hopper, executive vice president and general manager of Skanska, told the Cincinnati Business Courier, “You can’t hang drywall from your house.”
Skanska is a New York-based construction and development firm with projects throughout the country. The company employs more than 10,000. Skanska has developed a multi-faceted COVID-19 response plan to help keep employees safe and jobsites operational.
We looked at what Skanska and other leading construction firms are doing in the wake of COVID-19.
14 ESSENTIAL ELEMENTS OF A COVID-19 RESPONSE PLAN FOR CONTRACTORS
- Understand and follow CDC guidelines
- Place restrictions on travel
- Develop screening measures for employees who have recently traveled
- Instruct employees to stay home if they are feeling sick
- Place restrictions on in-person meetings and other employee gatherings
- Encourage employees to work from home if feasible
- Train all employees on the 6-foot distancing rule, no handshakes, etc.
- Establish thorough cleaning protocols at offices and jobsites
- Increase availability of cleaning supplies and handwashing stations at offices and jobsites
- Donate N95 respirator masks to local hospitals
- Tell elected officials to put partisan bickering aside in this very critical moment of national crisis
- Establish dedicated and empowered COVID-19 response teams
- Stay up to date on both federal and local COVID-19 developments
- Maintain clear, honest and ongoing communication with employees and subcontractors, and perhaps clients and suppliers
BEST PRACTICES TO HELP MITIGATE EXPOSURE
Social distancing is a critical component of any COVID-19 response plan. Turner Construction Company, a New York-based firm that employs roughly 10,000, has begun limiting the size of employee gatherings and has already put a stop to large group meetings. Attending events such as conferences has also been suspended. Remote conferencing technology is now being utilized for meetings. On that note, Turner Construction has expanded its network capacity and training tools to accommodate this surge in online network activity.
Sometimes an essential meeting that requires in-person attendance must take place. Turner Construction mandates that these meetings occur in spaces allowing for adequate social distancing. The CDC recommends that people remain roughly 6 feet apart. Additionally, Turner Construction is adapting standard operating procedures to limit the number of employees in an elevator or hoist at a given time.
Harkins, an employee-owned construction company based in Maryland, constantly reminds employees about the 6-foot rule. Additionally, sick employees are sent home immediately. All gatherings such as lunches are forbidden, and all meetings are now conducted remotely via Microsoft Teams.
Monitoring employees who travel has been another point of focus for construction companies.
Skanska issued a ban on all international travel through at least April. Domestic travel has also been greatly limited.
Turner Construction has restricted all business travel to any CDC Level 3 country, which is a country deemed to have widespread transmission. Also, if any employee had traveled to or had close contact with anyone who traveled to one of these countries, that employee is not allowed onto a Turner jobsite or office for 14 days from the date of contact. Taking it a step further, any employee who exhibits any of the common COVID-19 symptoms is instructed to stay away from Turner jobsites and facilities. Symptoms include fever, cough and restricted breathing.
PROMOTE GOOD HYGIENE
Hygiene has also been at the top of the list for Turner Construction. All jobsites are required to provide access to handwashing stations. Additionally, staff has been trained to religiously clean and disinfect frequently touched objects such as lunch tables, coffee machines and door knobs.
Harkins has instituted a long list of jobsite protocols to help improve awareness. For example, CDC and OSHA guidelines are now posted in all conspicuous locations on jobsites. Furthermore, jobsite leaders are trained to closely monitor employee behavior to ensure that the guidelines are being followed.
Harkins has also taken steps to step up jobsite cleaning. Trailers are now cleaned daily. Furthermore, a commercial cleaning service is brought in to clean and disinfect certain areas of a jobsite if COVID-19 exposure is suspected to have taken place. Harkins has also increased the volume of hand sanitizing products deployed to jobsites.
ESTABLISH DEDICATED TEAMS — AND EMPOWER THEM
Skanska has established a Coordination Response Team in each market it serves. Teams are tasked with monitoring COVID-19 developments, sharing information with employees and business partners, and implementing protocols.
Turner Construction has also established a dedicated COVID-19 Action Team. Efforts to support employees are an essential part of this team’s focus. Support is a key element that can get overshadowed in the midst of everything that is going on. This crisis has been taking a tremendous toll on many. Employers can play a constructive role in helping people cope.
On that note, Turner’s COVID-19 Action Team has gathered information to help employees guard against coronavirus-related scams, which are unfortunately emerging on a regular basis. The company has established a “fraud alert page” where employees can receive up-to-date information.
MAINTAIN OPEN, HONEST COMMUNICATION
Skanska is utilizing its internal company website (intranet) to provide general updates on COVID-19. The intranet is also being used to reinforce guidelines and standard operating procedures. This same information is also available through the company’s mobile app.
As reported by the Cincinnati Business Courier, telling employees to stay home when they are not feeling well is a critical piece to maintaining a safe, functioning jobsite. To reinforce the importance of this policy, HGC Groups, a large regional general contractor based in Cincinnati, has temporarily stopped recording unscheduled absences. In other words, an employee who thinks they may have COVID-19 symptoms will not be penalized for calling in sick to work.
LIFE HAS CHANGED, BUT STILL GOES ON
In Orlando, Fla., work on a $2.15 billion airport project continues amidst the COVID-19 crisis. As reported by the Orlando Business Journal, several guidelines have been put into place so work can continue:
- Employees showing signs of illness are sent home
- Additional handwashing stations have been made available
- More frequent cleaning of high touch point areas like stairwells
- Administrative staffs are evaluated for possible shift adjustments to limit personal interaction
The economic toll of COVID-19 has already set in. That said, some financial analysts expect that industries like manufacturing and construction will be among the last to begin issuing layoffs. That is due to the significant shortage of skilled workers these industries have been experiencing.
Rather, construction firms are expected to take proactive measures to help protect their workers and ongoing projects. The best practices outlined in this article showcase what leading construction firms are already doing in this regard.
LOBBY FOR RELIEF … AND LEAD BY EXAMPLE
The Associated General Contractors of America (AGC) says it has been lobbying for the construction industry to be deemed “essential” as government officials issue new mandates for certain business closures. AGC has also expressed support for a $2 trillion relief package that, as of March 23, the U.S. Senate had failed to pass on numerous occasions.
In addition, the Association of Equipment Manufacturers (AEM), show owner and producer of CONEXPO-CON/AGG, says it is working closely with federal, state and local officials to make sure they take immediate steps to contain the spread of COVID-19, support equipment manufacturers and their employees, maintain vital supply chains and ensure the country’s economic resilience. AEM sent a letter to the President requesting that the federal government designate equipment manufacturers, suppliers, and dealers as “essential” and providing state and local jurisdictions with a clear and consistent federal directive moving forward.
AEM continues to urge Congress and the President to take action on the following policies that would support the construction industry:
- AEM and the other members of the Transportation Construction Coalition (TCC) urged Congressional leaders to take immediate action on surface transportation reauthorization in order to stabilize and resuscitate the U.S. economy during this time of crisis.
- AEM joined the members of the Beyond the Runway Coalition and other trade associations and industry groups in letters to Congressional leadership calling for an immediate infusion of capital to help meet airport needs during the COVID-19 pandemic and an additional $10 billion in Airport Improvement Grants (AIP) to help continue airport capital projects and programs that are currently under way.
It is important for construction companies to help bring this message to state and federal leaders. The sooner Congress comes together to pass relief, the sooner financial markets can be stabilized.
While businesses and citizens wait for our nation’s leaders to put their partisan bickering aside and come together in the face of this unprecedented national crisis, the construction industry is showing that it is possible to put the nation’s interests ahead your own.
The CEO of 3M recently told CNBC that he was disappointed that N95 respirator masks are still on store shelves while hospitals face a shortage. To be fair, that could simply be the result of inventory that already existed in the pipeline. Regardless, it is up to retailers to decide if it is in the nation’s best interest to redirect that inventory to local health care facilities.
Some construction companies have already determined that it is in the nation’s best interest.
An ABC television affiliate in Columbus, Ohio, recently reported that area construction companies have answered Vice President Mike Pence’s call to redirect respirator masks to hospitals. More construction companies around the country can follow suit by simply reaching out to their local hospitals and health care facilities.
That is leadership by example, and the construction industry does it as well as anybody.
By adopting the COVID-19 prevention protocols outlined in this article, construction companies can continue leading by example — all while helping to “flatten the curve” and help the nation emerge from this crisis.
Join over 40,000 industry peers who receive construction industry news and trends each week. Subscribe to CONEXPO-CON/AGG 365.
Residential Construction now labeled an “Essential Infrastructure Business” by DHS
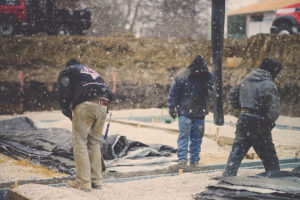
Over the past couple of weeks, the Concrete Foundations Association, in combination with the North American Concrete Alliance (NACA), NAHB and many others in both the residential construction sector and other labor organizations have been working tirelessly to demonstrate the need to keep construction moving forward. We are proud to report that the Department of Homeland Security (DHS) today designated construction of single-family and multifamily housing as an “Essential Infrastructure Business.”
The designation will enable many foundation contractors to keep their businesses open during the COVID-19 pandemic and help to stabilize the housing industry and its supply chain in the near term. More detail about the construction workers who qualify as essential can be found in both the “Public Works and Infrastructure Support Services” and “Residential/Facilities and Services” sections of the guidance.
“This is an important step in the work stream of our economy,” states James Baty, CFA Executive Director. “We have been in communication with a large number of concrete foundation companies who have devised practical and plausible work systems to maintain the health and welfare of their work crews while keeping the progress moving forward for one of this nation’s primary infrastructure needs.”
The NAHB, in their public release of this notice alerted all to “keep in mind that there is no mandatory federal order on what is an essential business, and many states have their own rules.” The guidance document produced by the DHS is a tool or an advisement that states can follow, if they so choose. Several states are restricting work to only those deemed “essential businesses,” which allows such businesses to keep operations going during the coronavirus epidemic. In this movement, the coalition effort establishes that residential construction workers should continue to be allowed to stay on the job.
While CFA was not on the frontline of this effort, ceding to the impact that NAHB, NACA and labor unions have, “we were definitely supportive of these efforts and contributed both our name and our attention as these efforts were underway,” states Baty. In addition, CFA and many other proponents of this effort are working through grassroots measures to support likewise designations to the various state governors.
In a quote from the NAHB release on this success; “Americans depend on a functioning residential construction sector to provide safe, affordable housing for our citizens, and this need is especially acute during this pandemic,” said NAHB Chairman Dean Mon. “Moreover, a healthy housing market is critical to maintain a sound economy. I commend DHS for heeding the urgent concerns of the housing community and taking this decisive action to assure the men and women of the industry will be able to stay on the job and serve the needs of the American people at this critical time.”
On March 26, in an effort spearheaded by NAHB, 90 companies and organizations, including the CFA, sent a joint letter to Acting Secretary of Homeland Security Jack Wolf urging him to designate the construction of single-family and multifamily housing as an Essential Infrastructure Business.
“As cities and states issue declarations and public health orders as a result of the crisis, it is essential that communities have access to our professionals to build and maintain essential services including: building, plumbing, residential property management, rental housing operators, roofing, electrical, HVAC systems, waste/wastewater treatment plants and power generations,” the letter stated. “Home construction, including those industries listed above, should be designated as ‘essential’ because it is necessary to maintain safety, sanitation, and economic security.”
Congress Proposes Expansion to Paid Sick Time and Leave
Coronavirus Relief Act to be signed by President March 19. Bigger direct aid package up next for week of March 23.
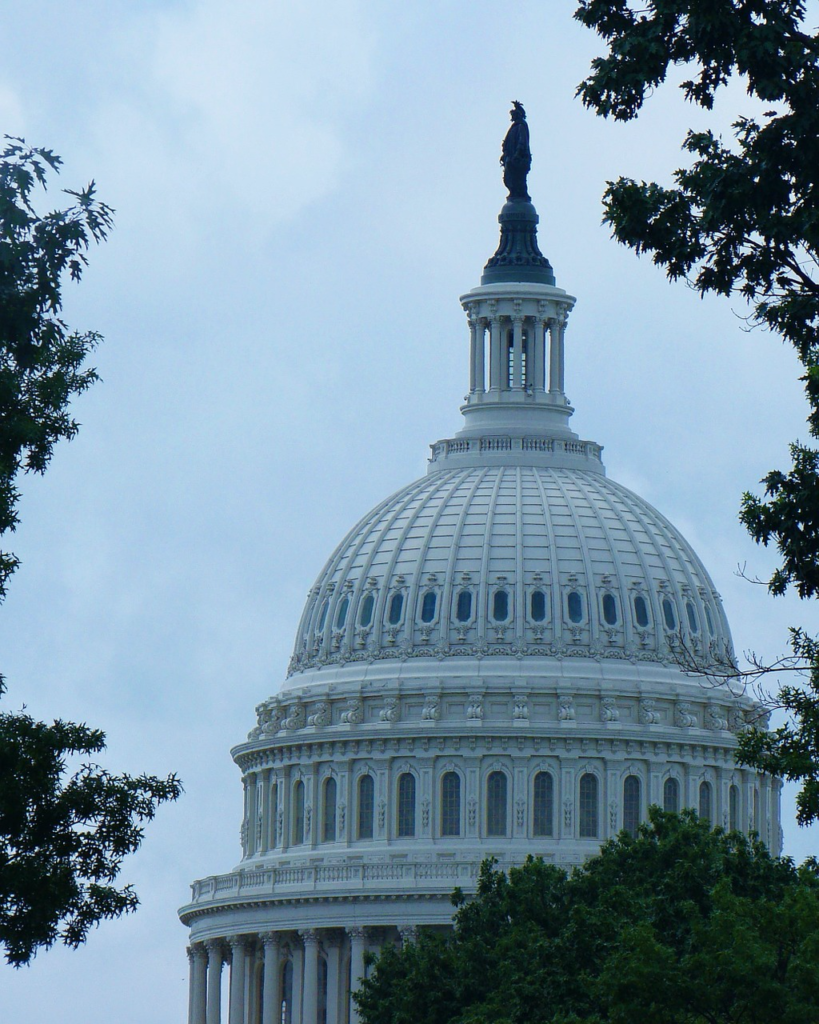
New legislation, signed into law on March 18, places significant new responsibilities on small- and medium-sized employers, including a large portion of the remodeling and home improvement industry, as the nation copes with growing numbers of sick and those who are quarantined due to suspected illness. In return employers are set to receive aid in the form of tax credits to cover this cost.
The Families First Coronavirus Response Act (FFCRA) requires employers of fewer than 500 people to add two weeks of sick pay to full-time employees on top of whatever they currently offer. In addition, the expected law will include an expansion of the Family and Medical Leave Act to allow for up to 12 weeks of “public health emergency leave” in order to comply with a recommendation or order of a public health official, to care for a family member, and to care for children under age 18 whose schools have been closed.
The legislation would be critical to helping small businesses, like the cast-in-place concrete contractor found throughout this country, continue operations through a period of great uncertainty. A number of measures contemplated by state, local, and federal government officials could severely curb the operation of “nonessential” businesses. Those actions have not been taken, but industry business leaders are discussing the implications.
Significantly, the act provides the U.S. Department of Labor with the authority to issue regulations “for good cause” to exempt small businesses with fewer than 50 employees when the imposition harms “the viability of the business as a going concern.” No guidance from the DOL has been issued as of yet.
The emergency provisions of the law would stay in place through the end of 2020. When signed by the President, the law goes into effect 15 days after enactment or April 2, 2020.
The following summary of the FFCRA, prior to Senate ratification and enactment, comes from the DeWitt law firm, www.dewittllp.com. You can read their full post here.
Emergency Paid Sick Leave – Employer Obligations
Covered employers are required to provide all of their employees with a new amount of paid sick leave for the following purposes, through December 31, 2020:
- To self-isolate because the employee is diagnosed with “coronavirus” (defined as “SARS-CoV-2 or another coronavirus with pandemic potential”);
- To obtain a medical diagnosis or care if such employee is experiencing the symptoms of coronavirus;
- To comply with a recommendation or order by a public official with jurisdiction or a health care provider on the basis that the physical presence of the employee on the job would jeopardize the health of others because of: a) the exposure of the employee to coronavirus; or b) exhibition of symptoms of coronavirus by the employee;
- To care for or assist a family member of the employee: a) who is self-isolating because the family member has been diagnosed with coronavirus or is experiencing symptoms of coronavirus and needs to obtain diagnosis or care; b) who is the subject of an order/recommendation from a public health official or health care provider to stay out of the community because the family member has been exposed to and/or is exhibiting symptoms of the coronavirus; and
- To care for the child(ren) of the employee if his/her/their “school or place of care has been closed, or the child care provider of such child is unavailable, due to coronavirus.”
- Amount of Paid Sick Leave. Full-time employees of covered employers are entitled to up to 80 hours of emergency paid sick leave; part-time employees of covered employers are entitled to an amount of emergency paid sick leave up to the average number of hours they work over a two-week period. Employees are able to take this leave regardless of the length of their service with their current employer.
Level of Compensation Required for Paid Sick Leave. Covered employers are required to pay every employee who takes emergency paid sick leave at a rate of compensation no less than the employee’s “regular rate” of pay (as that term is defined under the Fair Labor Standards Act (“FLSA”)) for leave taken for any of the first three reasons identified above (i.e., for the employee’s own coronavirus-related conditions). For every employee who takes emergency paid sick leave for the fourth and fifth reasons identified above (i.e., for the care of sick family members and/or children), covered employers are required to pay the employee at a rate of compensation no less than two-thirds of his or her “regular rate” of pay.
Emergency Paid Leave Adds to any Leave Already Offered by Covered Employers. Unlike many other paid/unpaid leave laws enacted by various state and local governments, covered employers must provide emergency paid sick leave under the FFCRA in addition to any other paid time off the employers may already offer to their employees. The FFCRA specifically provides that employers “may not change” their current paid leave policies – i.e., employers may not reduce the amount of leave ordinarily available under their own policies – in order to avoid the impact of the law. In addition, employers may not require employees to take/exhaust any of their employer-provided leave time before taking emergency paid sick leave time under the FFCRA. Employers also may not require employees who take emergency paid sick leave to find any replacement employees to take the absent employees’ place at work during their absence.
Emergency Family and Medical Leave Expansion Act – Employer Obligations
Pursuant to the FFCRA, eligible employees will be able to take up to 12 weeks of “public health emergency leave” in the following circumstances:
- To comply with a recommendation or order of a public health official who has appropriate jurisdiction or a health care provider on the basis that a) the “physical presence of the employee on the job would jeopardize the health of others” because the employee has been exposed to coronavirus or exhibited symptoms, and b) the “employee is unable to both perform the functions of the position of such employee and comply with such recommendation or order”;
- To care for a family member with respect to whom a public health official having jurisdiction or a health care provider “makes a determination that the presence of the family member in the community would jeopardize the health of other individuals in the community because of” the exposure of the family member to coronavirus or exhibition of symptoms by that family member of coronavirus; and
- To care for their child(ren) (under age 18) if their child(ren)’s school or place of care has been closed, or their child(ren)’s child care provider is unavailable, due to a public health emergency.
Unpaid Leave for 14 Days. According to the FFCRA, covered employers may choose not to pay an employee for the first fourteen (14) days of his or her public health emergency leave. Just as under the previously established portion of the FMLA, employees may choose to substitute any accrued vacation or sick time they may have during the unpaid portion of their leave; however, covered employers may not require employees to use such paid time during the emergency leave. On the other hand, it appears very likely that the emergency paid leave allotment provided through the FFCRA (and outlined in the first section above) can be substituted for the first two weeks of (otherwise unpaid) public health emergency leave.
Paid Leave Beyond 14 Days. Critically, if an employee continues to be eligible for and continues to take public health emergency leave in excess of that first fourteen-day period, covered employers are required to provide the employee with paid leave for the duration of the qualifying leave. This paid leave must consist of an amount of pay that is not less than two-thirds of an employee’s “regular rate” of pay (per the FLSA) for “the number of hours the employee would otherwise be normally scheduled to work.” Please note that these rules are slightly modified for employees who have schedules that vary from week to week.
Employee Eligibility. A much larger number of employees will be eligible for this leave than are currently eligible for the other types of leave provided by the FMLA. In particular, employees are eligible simply if they have been employed by their current employer for a minimum of thirty (30) calendar days.
Employers That Must Comply. The obligation to provide this new public health emergency leave applies to all employers with fewer than 500 employees. Consequently, even employers with fewer than fifty employees, who, until now did not need to comply with the leave provisions of the FMLA, will need to become familiar with and correctly administer this new bucket of leave.
Please note, however, that the FFCRA also provides the U.S. Department of Labor with the authority to issue regulations “for good cause” to: 1) prohibit “certain health care providers and emergency responders” from taking public health emergency leave; and/or 2) “exempt small businesses with fewer than 50 employees … when the imposition of requirements would jeopardize the viability of the business as a going concern.” To date, no such regulations have been issued, but we will try to provide updated information on the potential exemptions as soon as they are.
The Concrete Foundations Association is advancing opportunities during this time for its members to be focused on this rapidly-changing environment of regulations, laws and policies. Information is available in a new webinar series for members offered on Wednesday’s beginning March 25th and extending for the next four weeks. Webinars begin at 12:30 pm Eastern for an hour. For more information, contact CFA Executive Director, James Baty.
Original version of this article offered by Qualified Remodeler magazine.
Euclid Chemical Awarded New Patent for Low-Dust Epoxy Grout Aggregate
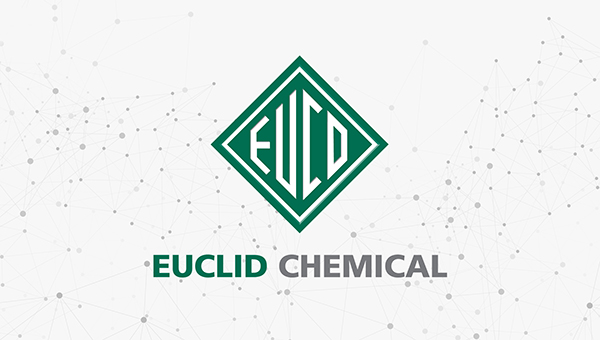
CLEVELAND (February 24, 2020) — The Euclid Chemical Company (Euclid Chemical), a leading manufacturer of products for the concrete and masonry construction industry, announced today it has been awarded a new patent for its dust- limiting aggregate, DL TechnologyTM, which is used in Euclid Chemical’s line of E3 epoxy grouts.
The patented technology was developed by Euclid Chemical researchers to support worker safety by reducing the amount of dust released into the environment during epoxy grout handling and mixing. This unique aggregate is a progressive approach to OSHA’s Respirable Crystalline Silica standard, which became effective in 2017 and requires employers to limit construction workers’ exposure to crystalline silica, a known cause of silicosis and other lung diseases.
In the industrial manufacturing market, re-grouting is an ongoing process as equipment is moved or replaced, and environmental factors affect even the most durable grout.
Euclid Chemical’s robust line of epoxy grouts is formulated with contractor-friendly features, including easy installation, flowability, and soap and water cleanup. Plus, it eliminates the need for workers to construct dust-free clean rooms around grouting areas. The products in the E3 line include:
This high-flow, high-strength epoxy grout is designed for large base plates and narrow configurations where flowability is crucial. With balanced physical properties and resistance to vibration and torque, E3-Flowable is formulated for easy installation, suitable for pouring or pumping, and can be mixed with a variable amount of aggregate to achieve the exact flow required.
Formulated for very deep placements of up to 18 inches (46 cm), E3-Deep Pour is ideal for grouting machine and equipment bases. This high-strength epoxy grout provides maximum bearing for bases of numerous configurations. It was specifically formulated to meet the requirements of the American Petroleum Institute Standard 610 for Baseplate and Soleplate Grouting.
E3-Xtreme is a three-component, high-flow epoxy grout with the highest compressive strength, low compressive creep and outstanding effective bearing area. It is characterized by extremely fast compressive strength development and excellent flowability, both of which are properties that are critical for extreme installations such as grouting of wind turbine column bases.
· E3-HCR
Developed for aggressive chemical environments where exposure to concentrated acids, alkali, corrosives or solvents can occur, E3-HCR is ideal for grouting in chemical processing plants and secondary chemical containment systems.A special resin and hardener formulation, E3-HCR has extremely high compressive strength, with ultra-low creep and outstanding effective bearing area.
About Euclid Chemical
Headquartered in Cleveland, Ohio, The Euclid Chemical Company has served the global building market as a worldwide quality supplier and manufacturer of specialty products and technical support services for the concrete and masonry construction industry for more than a century. Euclid Chemical provides products and technologies that include admixtures, fiber reinforcement, concrete repair products, flooring materials, decorative concrete systems and more. Learn more at www.euclidchemical.com.
Hoses are not all the same
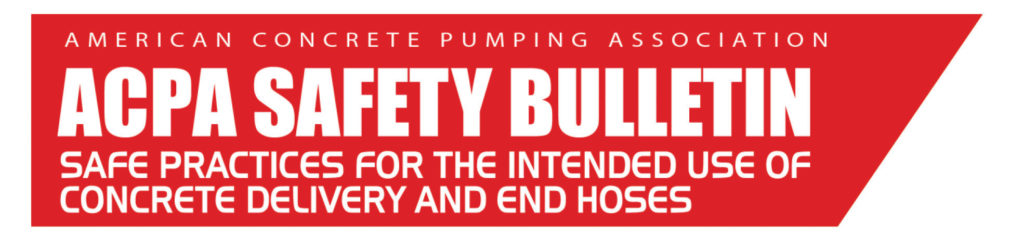
Concrete delivery hoses with two ends have different purposes than concrete delivery hoses with one end. See Figure 1.
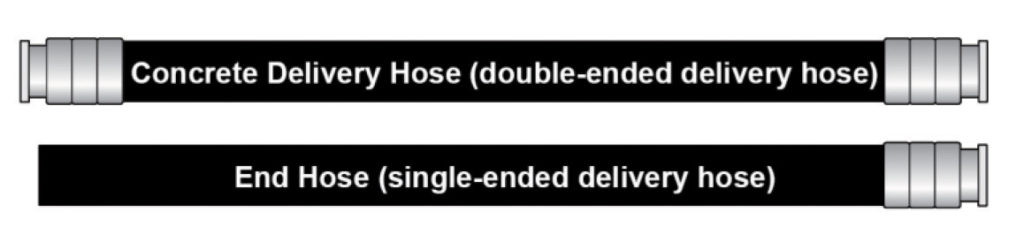
Hoses defined.
Double-ended concrete delivery hoses increase the potential for serious personal injury when used as an end hose. A double-ended concrete delivery hose has mass attached to the end of the hose, multiplies momentum, and has the potential to cause serious injury or even death to persons in its path, should the hose move unexpectedly or whip as a result of the release of trapped air. It is imperative that you only use a single-ended end hose at the discharge of the boom and on the discharge-end of lay-down placing line. (See Figure 2).
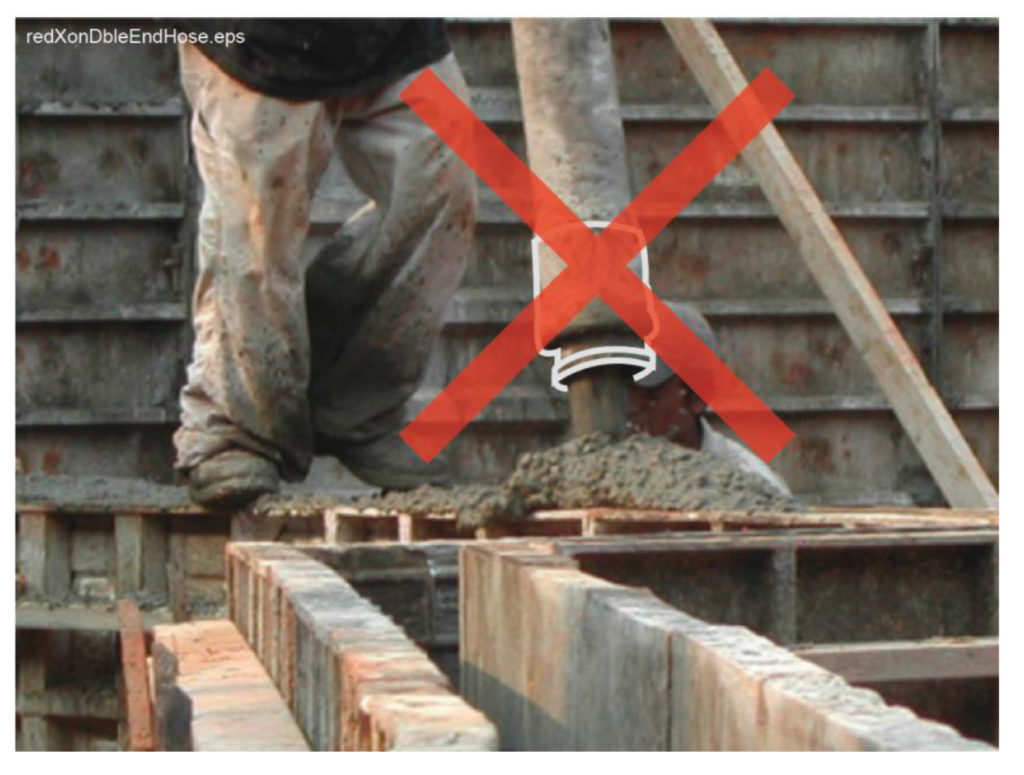
A double-ended concrete delivery hose improperly being used as an end hose.
Double-ended concrete delivery hoses have a place. There are situations where a double-ended concrete delivery hose is required. Here are some examples: If you will be laying out pipeline in addition to the boom, a double-ended concrete delivery hose must be used to connect the boom to the pipeline; this allows the boom to move independently of the pipeline. Without this hose, the boom could be damaged. (See Figure 3). Double-ended concrete delivery hoses are required when something must be attached to the line, yet it must remain flexible, like using a lay-down line with more than one hose after the pipe for distribution of the concrete, or for attaching the nozzle at the end of a shotcrete hose.
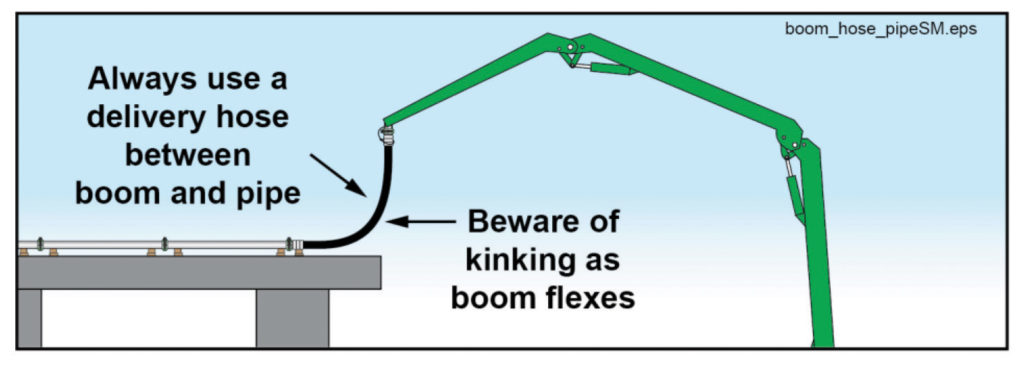
There are valid reasons to use a double-ended concrete delivery hose.
Keep the single-ended end hose on the end.
As pipe and hose are removed, a single-ended end hose must be used as the end hose at all times. This means that as you are removing hoses, you have to remove the next-to-last hose, and then slide the single-ended end hose in to hook up to the system that remains.
(See Figure 3). Once the last pipe is removed, the double-ended concrete delivery hose must be removed from the boom, and a single-ended end hose moved into its place.
According to ASME B30.27, paragraph 27-3.1.3.3.1(r), not using a concrete delivery hose as an end hose is an operator responsibility. ASME B30.27, Material Placement Systems, is the American National Standard for pumping and concrete conveyor safety.
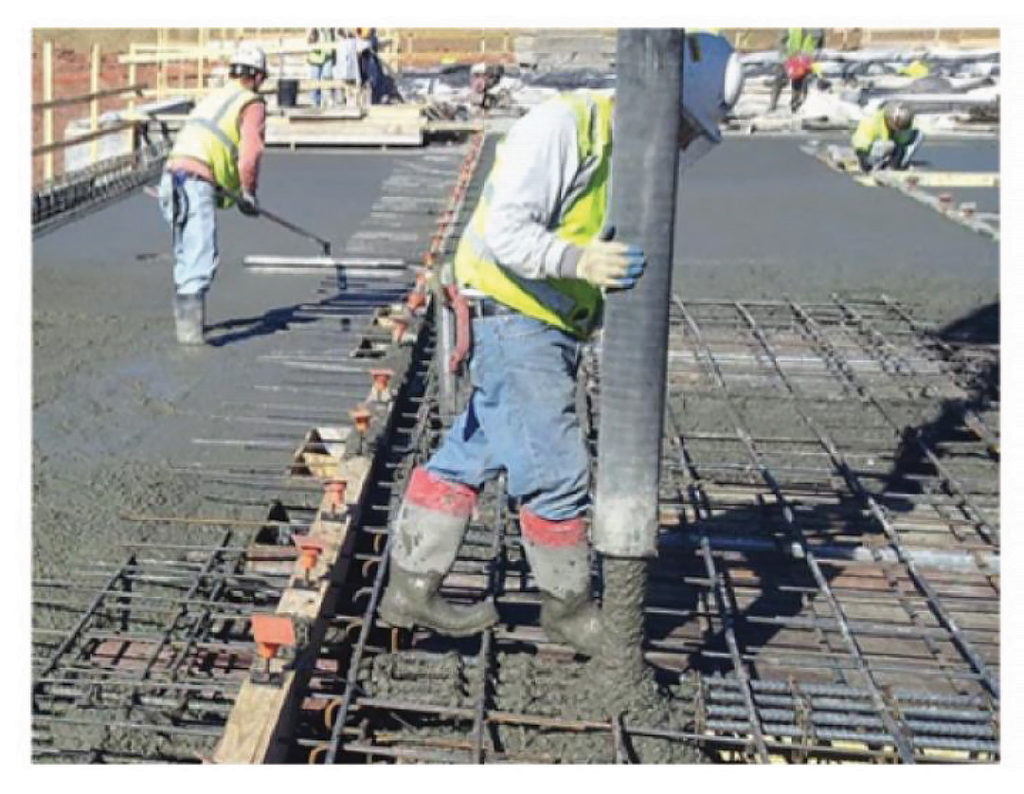
Be sure the discharge end is equipped with an end hose, not a delivery hose.

A double S-bend in use on a job, causing a needless hazard to the hose-person.
No place to attach banned accessories.
Eliminating the double-ended end hose makes a ‘ram’s horn’ or ‘double S-Bend’ device impossible to attach. (See Figure 5). These devices are also not acceptable or recommended. They add even more mass and multiply movement to a greater degree than a delivery hose alone. The ACPA has informed the DOT of the states that requires their use, (for prevention of air loss) that these devices are hazardous and must not be used. See the ACPA Safety Bulletin Double S-Bend/Rams Horn ©2009 ACPA, all rights reserved.
2019 PROJECTS OF THE YEAR
A Good Ground Game Is a Sound Game Plan
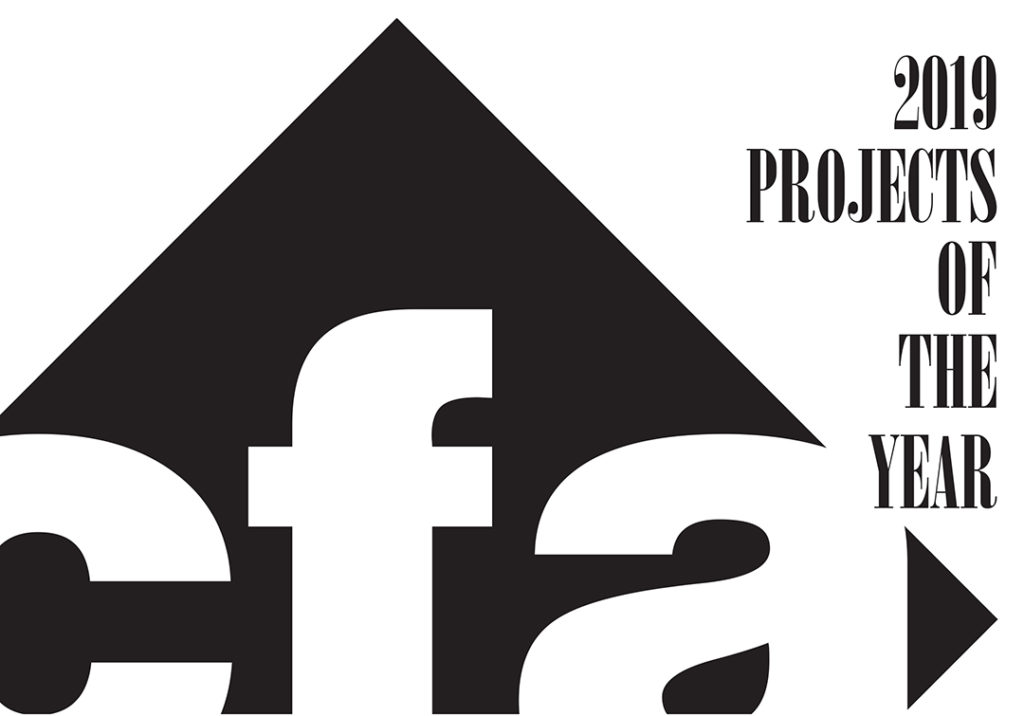
The recognitions for Projects of the Year were made during the Concrete Foundation Convention 2019 in Denver, Colorado this summer. Seen there was another crop of great projects constructed from some familiar CFA members who contribute annually to this competition, as well as some new and returning participants. If we imagine the country as a giant football gridiron, this year’s winners remind us of the sensibility of planning a marketing strategy like a good offensive scheme. You do need the occasional deep throw, a one-off project that captures excitement for your crews and the entire organization, one that projects your capabilities to the market. However, a steady regimen of recognizing regular contributions to the built environment, much the same as a solid running attack, will deliver unmistakable results to your market success as well as increase your recognition as a quality contractor.
While it may be cliché to suggest that you have to play to win, it is an appropriate statement for member-based opportunities like project awards. Only those projects that get photographed and submitted (with attention to the important and intriguing details that make it pride-worthy) can achieve recognition. In regard to project awards, a project not submitted is only marginally better than a project never built. Some of the best architectural and engineering designs are never able to come to fruition for lack of funding or a change in market conditions. More importantly, every year each of you has projects capable of vying for one of the categories and some projects that, perhaps, would create new categories. The 2019 Projects of the Year emphasize how each company is capable of honoring their crew’s commitment to accomplishing these impressive (even when common) works of concrete construction, week in and week out.
The Categories
Each year, the CFA encourages its membership and invites the market at large to become a member and be involved in this program. The breadth of categories continues to grow to accommodate the diversity of work accomplished by these companies each year. Submittals can be made to one of four categories for single-family residential foundations, including structures under 2,000 square feet, 2,000 to 5,000 square feet, over 5,000 square feet, and above-grade, all-concrete homes. Additional categories include commercial structures, agricultural structures, multi-family/townhome/apartments, and a non-wall structural element category. There is also an invitation to introduce a new category based on a project of interest.
EXPOSED CONCRETE MASTERY
Single-Family Foundation, 2,000–5,000 Square Feet | Browning-Plunkett Ski Lodge
SOLID CONCRETE WALLS, SALT LAKE CITY, UTAH
CFA Contractor Member
“UN-BRIDLED” SIZE AND PLAN COMPLEXITY
Single-Family Foundation, Over 5,000 Square Feet | 26 Bridlebourne
CUSTOM CONCRETE, WESTFIELD, INDIANA
CFA Contractor Member
100% PURE GRAIN CHALLENGE
Agricultural Foundation Structure | Robert’s Grain Facility
ATKINS BROTHERS CONCRETE, BEAVERCREEK, OHIO
CFA Contractor Member
CORNERED BUT NOT CONFINED
Commercial Foundation Structure | Carlson Landing
TALPEY CONSTRUCTION, WESTBROOK, CONNECTICUT
CFA Contractor Member
THE BIGGER SIDE OF CAST-IN-PLACE
Multi-Family Foundation Structure | Poplar Creek Apartments
VAN WYKS INC., WALDO, WISCONSIN
CFA Contractor Member
BIG BITES ARE NOT ALWAYS BIG PLATES
The 2019 Overall Grand Project of the Year | Lafond
TALPEY CONSTRUCTION, WESTBROOK, CONNECTICUT
CFA Contractor Member