CORNERED BUT NOT CONFINED
Commercial Foundation Structure | Carlson Landing
TALPEY CONSTRUCTION, WESTBROOK, CONNECTICUT
CFA Contractor Member
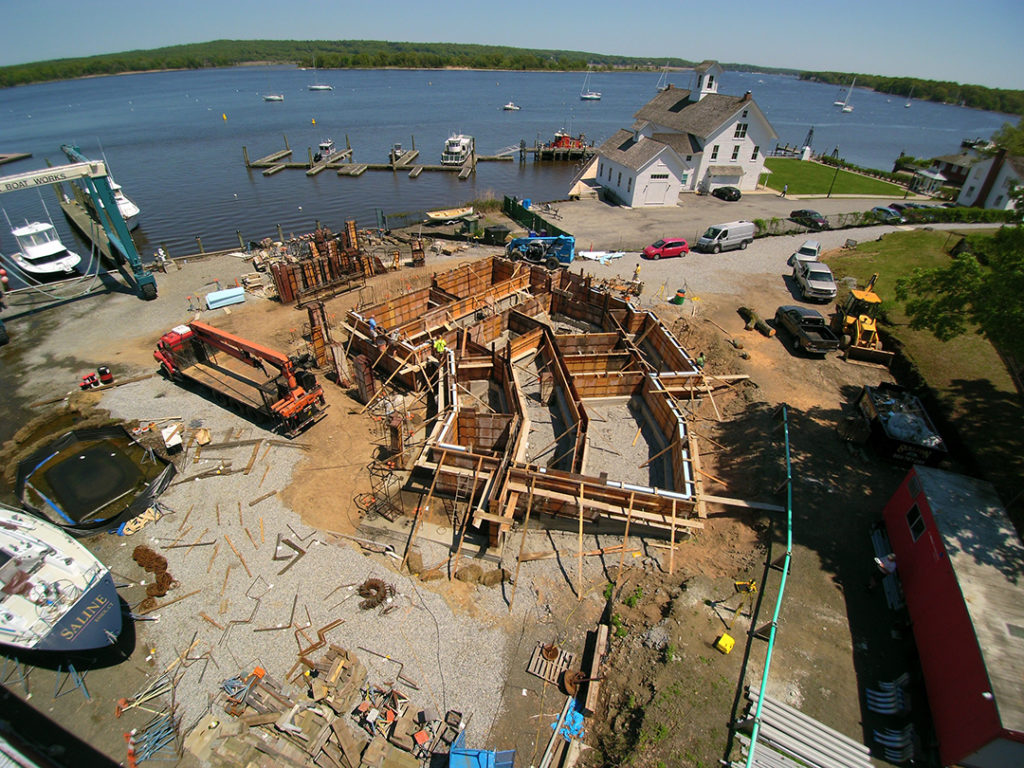
The winning entry for the Commercial Foundation Projects category comes from the Connecticut-based CFA member, Talpey Construction. Known as Carlson Landing, this commercial foundation presented the extreme challenge of tight spaces, excessive corners, and an extensive rebar schedule.
The foundation is for a new restaurant and office building at a local marina located on the Connecticut River. “Given the proximity to the river,” explained Russ Talpey, owner of Talpey Construction, “the water table level coincided with the fluctuation of the tides. This required us to use a dewatering system running around the clock the duration of the project.”
On a scale of 1 to 10, Talpey rated this project an 11. “There was just so much going on and in not that big of a space. My guys were great; they enjoy these jobs instead of looking at them as a hassle. It was a cold, wet spring and we worked through it the best we could. The owners were understandably antsy after the permitting delays set them back. We tried to do our part by going a little further for them. There’s a fine line between getting the most out of your crew and totally killing morale… not an option on this job, as there was just too much to do.” The four-man crew at Talpey described the challenge as not only within their wheelhouse but also the way they like it. At the same time, a compressed schedule and anxious owners really challenged their small team, and they could not overcome the difficulties by simply adding more labor. “Sometimes on these jobs you need to fight up a weight class,” Talpey said. “My guys were awesome, never complaining. “We passed every single inspection and not once were we asked to redo a single thing.”
Detailing this project’s complexity is a chore in and of itself. With a footprint just over 4,200 square feet, the project had 500 yards of concrete and 39,000 pounds of steel reinforcement. The footings consisted of a grade beam that capped more than 80 steel H-beam piles that were driven down to the bedrock. Because the site is on a hillside, this grade beam footing stepped up and down over thirty times, and each step had an engineered rebar detail approved by the structural engineer. These footings consisted of 4,500 psi concrete and were detailed with a formed keyway (adding to the insanity), and then dowels were prepared for the double-mat of #5 rebar putting verticals in each face of the wall.
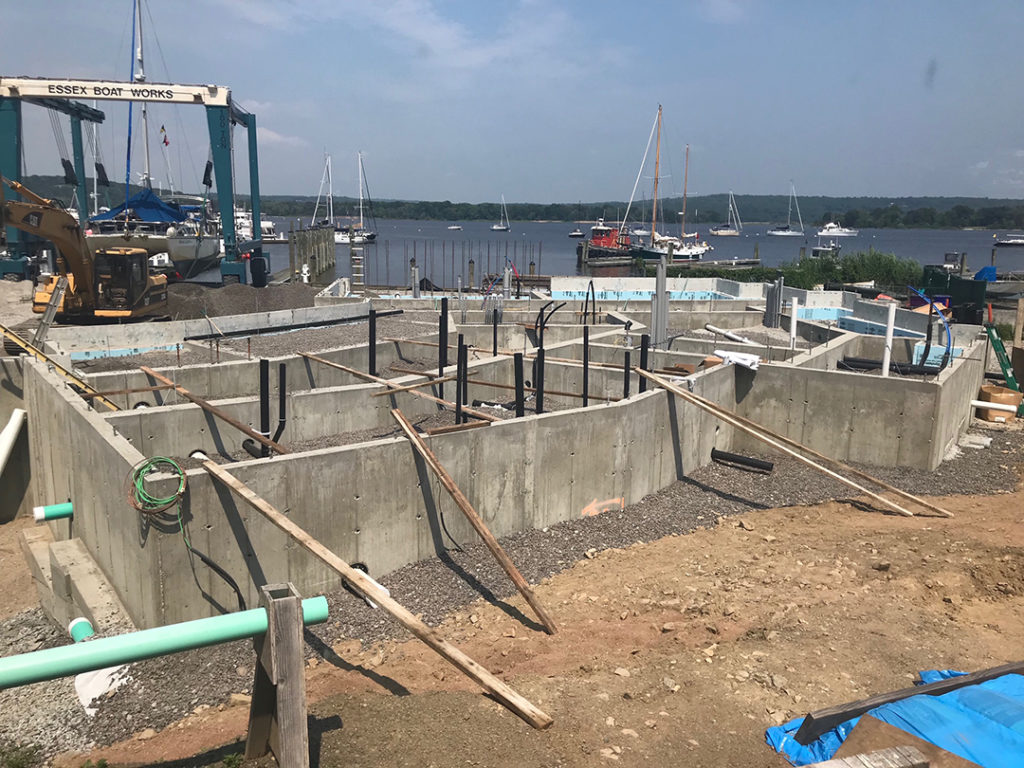
The foundation walls were as complicated as the double #5 rebar grids. They varied in height from an awkward 9 feet 8 inches down to 3 feet 6 inches, due to the steps in the footing, while maintaining roughly the same elevation along the perimeter. The foundation was not just an exterior perimeter, as there were numerous interior walls for slab support and hold-downs for shear walls. For fear of compromising the rebar in the walls, the structural engineer would not permit core-drilling the walls for utilities. Therefore, the mechanical engineer specified over 50 of these ¼ inch thick galvanized steel sleeves of varying diameters to be set into the forms with a rebar detail around each one. Finally, construction joints were mandated to limit pouring to no more than 50 feet of monolithic pour. Nevertheless, the joints could not be within 4 feet of any corner – not an easy task with so many corners.
Finishing off this project, Talpey had to install an 8-inch structural slab-on-ground set on an interior slab shelf. All anchoring systems had to be preset in the walls 12 inches below the structural slab, as the engineer would not permit wet setting.
“I would open this print for a little bit at a time, when I could, just to attempt to digest it,” Talpey said. “The job was supposed to start in the fall but was delayed in the permitting process. The delay moved it to the spring and gave me more time to get into the plans, find stuff that needed clarification and get it worked out. Not surprising, the plan dimensions were vague, to put it nicely.” When asked about the technical challenge of the layout accuracy, Talpey said, “I’ve used a Leica Icon from Scott Carter [CFA member] for years. It’s an invaluable tool. I do not have any CAD training and I like to draw our plans in by hand… It gives me a feel for the job and I can kind of get to know the prints.” Talpey says, though, this job was not possible to draw in with what they had on the plan. “Scott got me in touch with a CAD professional he works with, and we got the plan downloaded into the data collector. It was an absolute lifesaver. We did not have to make adjustments for a singular upright. Clearances were maintained everywhere and our success on the project extends now throughout our market.”
While figuring out this crazy project, Talpey has appreciated the interaction in his market and the opportunity afforded by the general contractor, AJ Shea, who selected him based on previous work. Exemplifying the importance of taking on challenges and finding ways to promote work, Talpey said that while they were on another job, a carpenter came out to the and asked if they were the ones responsible for the foundation at Carlson Landing. The carpenter exclaimed, “What a nice job you guys did! Very well done.” Talpey, however, knows that all the interior walls are underneath the slabs. Unless someone sees the photos, no one would even know those walls exist or how incredibly challenging they were.