Making Offices and Construction Sites Safer From the COVID-19 Virus
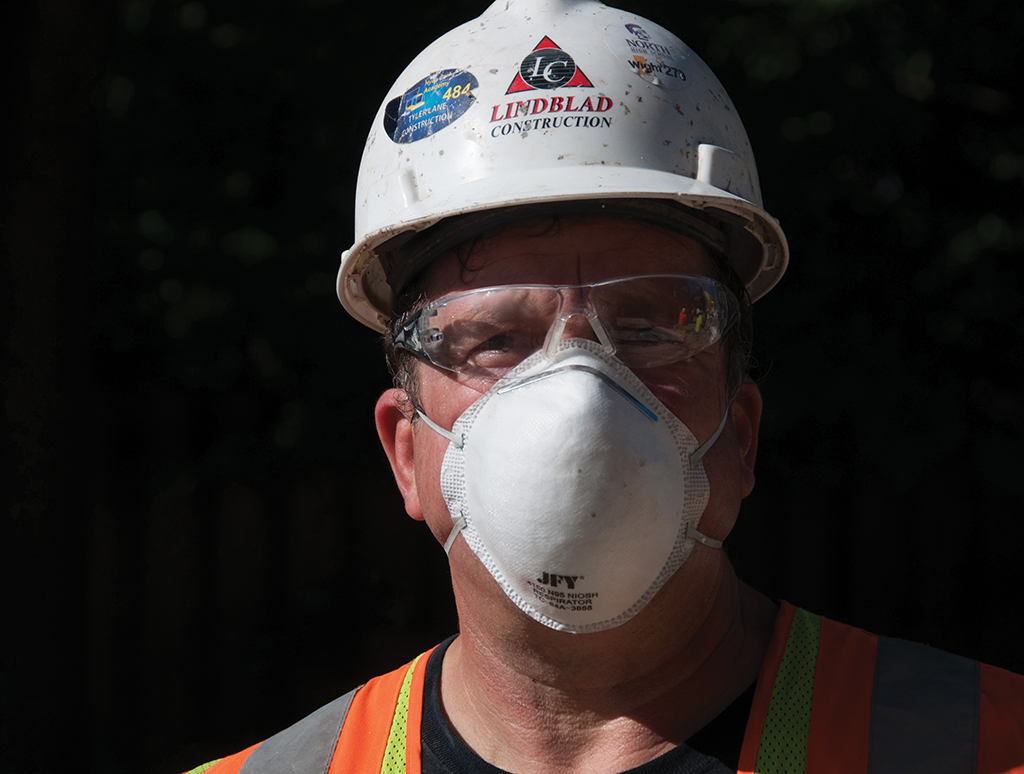
The current pandemic is changing the way we organize for work on construction jobsites. Along with a hardhat, safety vest, steel toed boots, and safety glasses workers must now wear a cloth face covering or an N95 respirator or equal—the new normal. Wearing a mask helps to trap tiny water droplets in your breath so that others don’t inhale them. Others wear masks to protect you when they breathe. When people exposed to the SARS-CoV-19 Virus breathe the droplets they create contain the virus particles. Photo Credit: Joe Nasvik
by Joseph Nasvik
Epluribus unum—out of many, one. This is the Latin motto the United States adopted in 1776 to signify the joining of states to form one national government. At the time, it was a difficult concept for people to accept because it meant that states and individuals would have to give up some of their personal rights to serve a greater cause. Today, the threat to life posed by the new coronavirus brings the e pluribus unum concept back into sharp focus as the country and its people consider personal rights versus one’s responsibility to others.
As social beings, this pandemic preys on our natural instincts to be close to friends and family, and it challenges our ability to work and earn a living. As time passes, it is hard to know if the first tool for fighting a pandemic — distancing ourselves from one another — is working. There is a huge number of victims, and the end is not in sight. The end, when it comes, will likely come through the development of an effective vaccine, the tool that will end the threat of the pandemic.
Construction is regarded as an essential industry in many states, and it is currently challenged to keep workers safe on the job site. “Social distancing” — the current phrase being used for keeping physical distance between people and the first line of defense — requires workers to be a minimum of six feet apart from one another. But construction, especially concrete construction, often requires teams to be much closer together for some work functions, so other safety measures become crucial. Here are some ways construction work is being made safer.
Editor’s Note: Read Concrete Facts online for information about the science behind the virus spreading.
The Tools for Fighting Pandemics
Public health professionals who focus on fighting pandemic diseases recognize four basic tools: social distancing, testing, tracing, and modeling. Keeping people separated from one another is the first major step in preventing the wide spread of the disease. Distancing has been a tactic for preventing the spread of communicable diseases for thousands of years, often by separating the diseased person from the larger group. But when it is unclear who has the disease, the first preventative measure involves isolating each person from every other person.
Developing accurate tests to quickly determine who has been infected and who has not, followed by tracing who has been in contact with who, makes it possible to quarantine only the sick. By tracing and quarantining everyone an infected person was in contact with, the spread of the disease can be limited. Iceland, for example, has tested all its citizens, quarantined those exposed, and effectively used tracing to keep COVID-19 death counts close to zero.
Editor’s Note: Read Concrete Facts online for information about modeling practices being developed.
CDC Recommendations
As a non-regulatory agency, the CDC makes recommendations that are discretionary, not mandatory. But contractors are mandated by other government agencies, such as OSHA, who use CDC’s recommendations (see CDC guidance recommendations for construction at https://www.osha.gov/SLTC/covid-19/construction.html). Unions, and sometimes construction site owners, can also require that contractors provide safe work conditions based on CDC recommendations.
Here are some useful CDC recommendations for contractors and businesses creating their own company guidelines and policies:
- Employers should have a COVID-19 response plan to protect workers.
- Workers should stay home and notify their employer if they are experiencing COVID-19 symptoms. They should not return to work until they meet the criteria determined by their employer, healthcare providers and state and local health departments.
- Workers should notify their employer if a family member living in their home has COVID-19.
- Contractors should limit contact between employees and have them maintain a minimum distance of six feet apart as much as possible. The number of workers sharing small areas — such as at construction sites, in elevators, in trailers, and in vehicles — should be limited if possible.
- Workers should wear cloth face coverings where social distancing is not possible. Cloth coverings should not be substituted for respirators where respirators are recommended or required.
- Frequently touched surfaces should be regularly cleaned and disinfected. On job sites, this includes shared tools, machines, vehicles, handrails, doorknobs, and portable toilets. Cleaning should be done periodically throughout the workday, before and after every shift, and after anyone uses your vehicle, equipment, or workstation.
- Tool sharing should be limited when possible.
- Workers should wash their hands regularly with soap and water for at least 20 seconds or use an alcohol-based hand sanitizer that is at least 60% alcohol. Contractors should supply handwashing stations with clean running water, soap, and disposable towels or conveniently placed hand sanitizer stations.
- Workers should clean their hands before and after work shifts and breaks; after blowing their nose, coughing, or sneezing; after using the restroom; before and after eating; before donning and after removing work gloves; after putting on, touching, or removing cloth face coverings; before donning or doffing eye or face protection (like safety glasses, goggles, or face shields); and after touching objects that have been handled by others.
- Use disposable tissues when you cough, sneeze, or touch your face.
- Employers should provide workers with accurate information about COVID-19, how it spreads, what the risks are, and what protective measures are in place.
- Employers should limit face-to-face contact by limiting meetings, using internet training options, and teleworking when possible.
- Employers should consider increasing the distance between employees by staggering work schedules, limiting access to work areas like trailers and break areas, rearranging tables and chairs in offices, and reducing the number of workers at meetings.
For more information, see the CDC’s guidance for businesses and employers on the website: https://www.cdc.gov/coronavirus/2019-ncov/community/guidance-business-response.html.
Cloth Face Coverings
The CDC recommends wearing cloth face coverings (see https://www.cdc.gov/coronavirus/2019-ncov/prevent-getting-sick/diy-cloth-face-coverings.html) in public settings where other social-distancing measures are difficult to maintain, especially in areas where there is significant community-based transmission of COVID-19. When cloth masks are worn all day, or worn at a location where the wearer may have been exposed, they should be washed with soap and water before their next use.
Cloth face coverings are not surgical masks or respirators and are not appropriate substitutes in workplaces where surgical masks or respirators are recommended or required.
Personal Protection Equipment
Due to the shortage of N95 respirators, some contractors are using KN95 respirators. These are made in China and in most ways are considered equal to N95 respirators. KN95s are generally recommended for occupational use in situations that would typically require an N95. However, if you choose to buy KN95s, be careful to choose a reputable supplier, because there are products on the market that do not meet the standards they claim to meet and come with exorbitant price tags. The CDC has a recorded webinar (https://www.youtube.com/watch?v=w7tVnjrmAmc) with information about what to look for when purchasing respirators from international sources. Respirators, including N95s and KN95s, should be incorporated as part of a regular respiratory protection program (including fit testing) to protect against occupational respiratory hazards.
The primary purpose of a mask is to prevent droplets of water containing the virus from spreading. Virus particles by themselves are too small to get trapped in the mask’s filtering material. Wearing a mask protects others from inhaling contaminated water droplets expired by the wearer as he or she breathes, talks, shouts, sings, coughs, or sneezes. Others wear their masks to protect you.
N95-quality masks also offer some protection to the wearer from bioaerosols such as bacteria, some viruses, fungi, and pollen if they are fit carefully around the nose and mouth. They should be replaced when they are physically damaged, there is increased breathing resistance, or if there are other hygiene issues.
Some contractors believe that using face shields can be a substitute for breathing masks. These shields can block splashes and sprays, but they do not provide respiratory protection. Even though the shields can be easily cleaned and reused, they are not currently rated as adequate replacements for face masks or respirators. Therefore, if they are used, they should be considered an additional protection.
For more information about each of these three different tools, see the CDC infographic on facemasks and respirators at https://www.cdc.gov/niosh/npptl/pdfs/UnderstandingDifference3-508.pdf and the CDC’s information about cloth face coverings.
How One Contractor Is Making His Job Sites Safer
Mark Stadalsky, the vice president of Lindblad Construction located in Joliet, Illinois, says his company specializes in industrial concrete in several states, serving the pipeline industry, electrical power distributors, and heavy industrial companies. In Illinois, construction is considered an essential industry, so Lindblad has been able to work throughout the pandemic. Stadalsky says their team became very curious when news of the COVID-19 pandemic first appeared, and they decided it would likely become a major threat to the construction industry and their workforce. So the company’s management, safety experts, and consultants engaged in six weeks of collaborative discussions to work out a company protocol guideline with carefully defined pathways they could use to guide decisions about how to treat worker health issues. For example, if an employee called in to say he or she was ill but did not have COVID-19 symptoms, the company protocol defined a specific pathway to follow. If an employee did have COVID-19 symptoms but had not been tested, there was another defined guideline. If an employee tested positive for the COVID-19 virus, there was yet another set of procedures to follow.
Lindblad also correctly predicted early on that wearing breathing masks would become mandatory, so they bought a supply of N95 masks before they were scarce and then explored possible sources for securing a steady supply of KN95 masks. At the same time, the company hired people to make cloth masks for use by all company employees.

Some of Lindblad’s clients specify how workers on their job sites will be protected with regards to the COVID-19 virus, and Lindblad accommodates their specifications, so long as they meet Lindblad’s protocol. “For example,” Stadalsky said, “one of our clients requires workers to wear N95 or KN95 masks instead of cloth masks, so we follow their requirements.”
Lindblad protocol includes the following:
- They office staff follow a network of guidelines tailored to their duties.
- In the construction yard, everyone wears a mask.
- As much as they can, workers on job sites distance themselves from others.
- On job sites, Lindblad regularly cleans all touch points and common areas.
- They have full-time and part-time safety inspectors in the field at all times.
- During the first six weeks of the pandemic, they sent out a daily COVID-19 message designed to give workers accurate information and put them more at ease.
- They provide daily wellness checks for all employees and send them home if they have relevant symptoms.
- They are planning for the possibility of a pandemic resurgence in the fall.
A Word About Aerosols
The word “aerosol” is currently being used by the media primarily to describe the smaller droplets created when people (and animals) exhale. Aerosols are defined as droplets that are smaller than five microns in size. Anything larger than five microns is a non-aerosol droplet. All droplet sizes can contain the COVID-19 virus or other viruses.
Aerosol droplets are formed in the very small airways of the lower lung during normal breathing processes. They consist of moisture combined with mucus and surfactants, and because they are so light, they can remain airborne for several hours. This can be especially dangerous in closed environments with reduced ventilation.
Cloth face coverings can trap droplets larger than five microns, but only N95 breathing masks can trap aerosol droplets down to about one micron in size. Droplets smaller than one micron cannot be trapped by masks.
Recent research suggests that the smallest aerosol droplet sizes can contain one virus while large droplets created by rapid exhalation can carry many. There are many more small aerosol droplets created than there are larger droplets, so the risk of infection from aerosols is higher, especially because aerosols can remain airborne for so long.
2020 PROJECTS OF THE YEAR
A Crop of Excellence During a Time of Pandemic
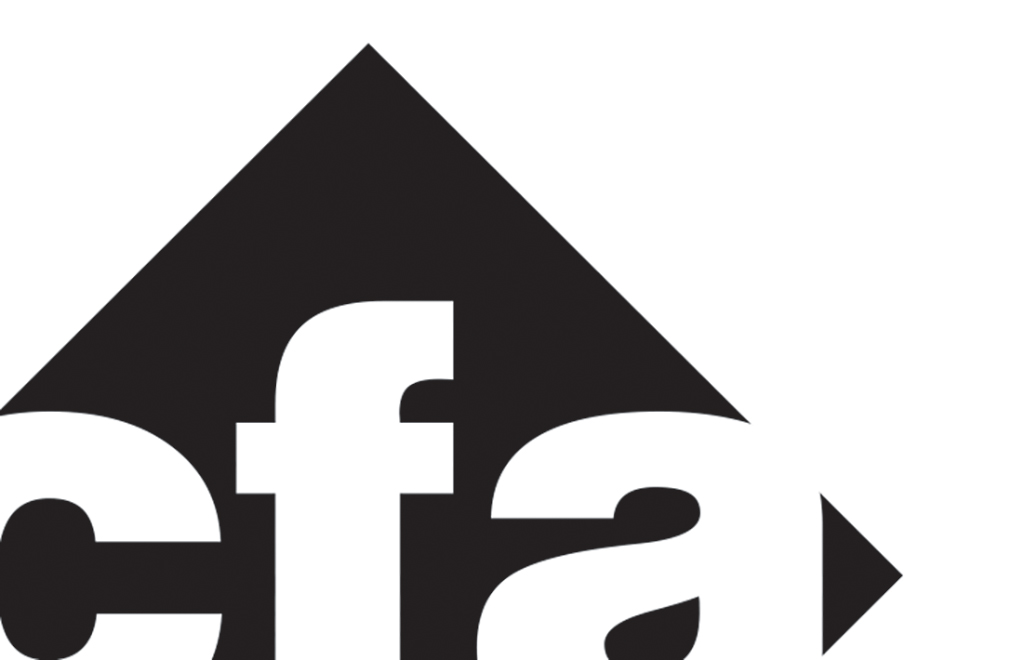
Each year, the Concrete Foundations Association offers to its members a chance to tout their accomplishments and reward their teams for jobs well done through the annual “Projects of the Year” awards. In addition to recognizing noteworthy projects, these awards expose people to the breadth of work completed by some of the industry’s top cast-in-place concrete companies.
Among the submittals every year are projects that can be described as massive and ones that are more representative of a modest size. Members are encouraged to keep track of projects that were complex challenges and projects that leave a team taking a breath to enjoy a job well done. Additionally, the categories are revisited each year to make sure there are openings appropriate for recognizing any new, diverse applications, which tend to showcase the creative growth of the cast-in-place concrete industry.
Formerly known as “The Basement From Hell,” the Association initiated this program under the direction of the long-time executive director, Ed Sauter. “Quite frankly, we initiated this program as a way of helping give annual marketing content to the Association,” Sauter said. “‘The Basement From Hell’ was coined to represent some truly remarkable, and at times monstrous, projects that challenged member companies the most.”
Each year, the top project was determined based on how challenging it was to estimate, build, and achieve some measure of profitability. This changed over time as project variety grew. “Today, contractor members of this Association are experts in residential and commercial foundations; they are taking on industrial slabs, tilt-up buildings, post-tensioned foundations, above-grade homes, and multi-family complexes,” said executive director for the CFA, James Baty. “As we have advanced the program, contractors have continued to ask us whether a project of one type or another would fit. This has resulted in broadening our categories to where, today, we have eight different categories and annually award at least half of them.”
The following pages represent this year’s awarded projects, selected for the first time in several years by popular vote by Association members. During #CFAAtTheEcho, participants had an opportunity to roam the Showcase Pavilion and watch three-minute videos about each project. After this, each project had a quick five-question survey with a point and click rating scale. This was an opportunity for the industry to come together to give contractors a chance to display their very best, and a chance to participate collaboratively in recognizing truly unique accomplishments.
______________________________________________________________________________
OVERALL GRAND PROJECT OF THE YEAR
Single-Family Residential Foundation Over 5,000 sq. ft.
SABO IN NEWPORT BEACH, CALIFORNIA
Member Since 2006

This project, nicknamed “Sabo,” is the type of job that would put many companies out of business if they did not know what they were doing. The project seems to have everything: caissons, shoring, mat slab, battered shotcrete walls, waterproofing, radius poured-in-place walls, outrageous rebar details, two pan decks with lightweight concrete, a radius driveway deck (above grade), waterproofing concrete additives, and epoxy-coated rebar.
The project’s footprint is 9,000 square feet, and its material details are incredible, with over 2,400 cubic yards of concrete, including over 1,100 yards each in the mat slab and caissons. There is 910,000 pounds of steel reinforcement, with 720,000 pounds in the caissons alone. Basement wall heights ranged from 11 to 26 feet and the wall thicknesses range from 12 to 18 inches.
“While gathering all of the data and information for this submission, I was left feeling very content with the amount of teamwork performed at Ekedal in a highly efficient manner,” stated Ryan Ekedal, president of Ekedal Concrete.
Rather than using traditional footings, this project has a 15,000-square-foot, 30-inch-thick mat slab. The slab features two layers of #6 reinforcement bars at 9-inch spacing each way, and all rebar was epoxy coated due to the proximity of the ocean below.
Since the project sits right on the bay front in Newport Beach and consists of a 9,000-square-foot basement foundation with the bottom of the slab sitting at 17 feet below sea level, we had to install a shoring and dewatering system. We drilled 109 30-inch caissons with a combined drilling depth of 6,000 feet. This was followed by the installation of a “secant” soldier pile system that used interlocked hard and soft piles, eliminating the need for the more common lagging technique used on shoring projects not in the water table. The reinforcing steel cages were over 48 feet long, each with eighteen #9 verticals with ties.
Once the caissons were drilled and poured, 17 “well points” with 18-inch diameters were drilled 50 feet deep, creating a dewatering system that brought the water table below the bottom elevation of the mat slab. This dewatering went on for six months.
The mat slab was used in lieu of footings, since the elevation is 17 feet below sea level. Once completed, the rest of the complex foundation, with curved walls and other architectural features, could progress.
“Receiving this award is such an honor, as it is voted on by my peers in the industry, which means a lot,” states Ekedal. “We try to deliver such an amazing experience to all of our clients, and to be acknowledged for this great work we are able to provide feels great! At Ekedal, we love concrete and the opportunities of building the impossible, so for other amazing people and companies in the industry to appreciate that is huge! This speaks volumes to the culture which is vital to the success and/or failures of a project or company. I try to always ensure the culture at Ekedal is one where all the employees know the mission and have the same goals and desire to be the best!”
______________________________________________________________________________
SINGLE-FAMILY RESIDENTIAL FOUNDATION 2-5k SQ. FT.
Private Residence in Atlanta, Georgia
HERBERT CONSTRUCTION COMPANY, MARIETTA, GEORGIA
Member Since 1992
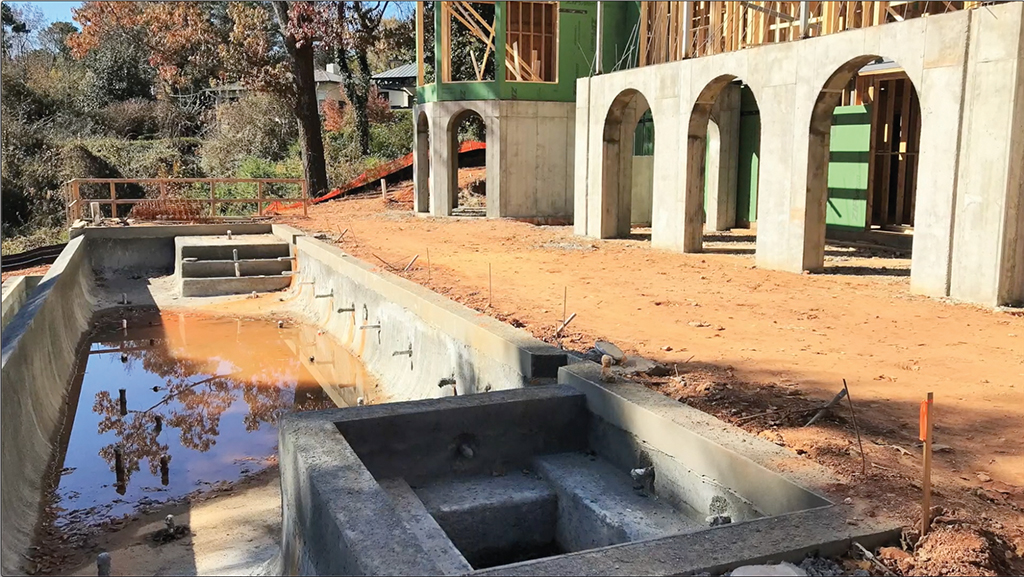
This project required considerable custom-built features. There were seven phases, each with its own estimate, and the company had to deal with bad soil (which had to be removed and replaced with stone) and install retaining walls to build up the road for access before beginning the foundation proper.
A total of 830 linear feet frame this 4,169-square-foot plan. The project required 562 cubic yards of concrete and over 56,000 pounds of steel. Wall heights stepped a total of eleven times (from 2 feet up to 15 feet) for five wall thicknesses (from 8 to 16 inches).
The phases of construction were carefully planned so as to keep the site and the complicated design under control. The first phase saw the construction of a 14-inch-thick by 4-foot-tall wall made for the pool with multiple radius walls. During phases two and three, two retaining walls were built — these were required for site access and for building the roadway up. One wall had a 106-foot radius with a heavy design and 378 vertical feet of radius corners, the other wall was 16 inches thick and 16 feet tall with a radius section sloping 13 feet downward to 7 feet.
Phase four was constructing the main basement walls, which were 11 feet tall and approximately 400 linear feet.
In phase five, the basement slab, thickened to six inches in some areas with additional reinforcing and helical piers due to poor soil conditions, totaled 3,770 square feet with a double-mat grid of #5 rebar.
The sixth phase consisted of building arched walls and footings for the back patio area. In all, 16 arched openings of six different sizes were placed in walls from 12 inches to 16 inches in thickness. The custom-built arched wood blockouts were crafted from Luan plywood to ensure a smooth finish, and seven beam pockets were included to hold I-beams for the covered patio above.
The final phase, phase seven, saw the installation of a retaining wall designed to build up the site for a driveway and to create a walkway to the basement level. This wall sloped from 4 feet to 12 feet tall.
This job required technical elevations because of jumps and radius walls. The arched openings did not have an assigned set radius, so, through trial and error, the arch was determined using CAD. Combined with the rest of our station, the result was unmatched accuracy.
______________________________________________________________________________
SINGLE-FAMILY RESIDENTIAL FOUNDATION < 2k SQ. FT.
Sweetwater Lake in Ninevah, Indiana
CUSTOM CONCRETE OF WESTFIELD, INDIANA
Member Since 1986
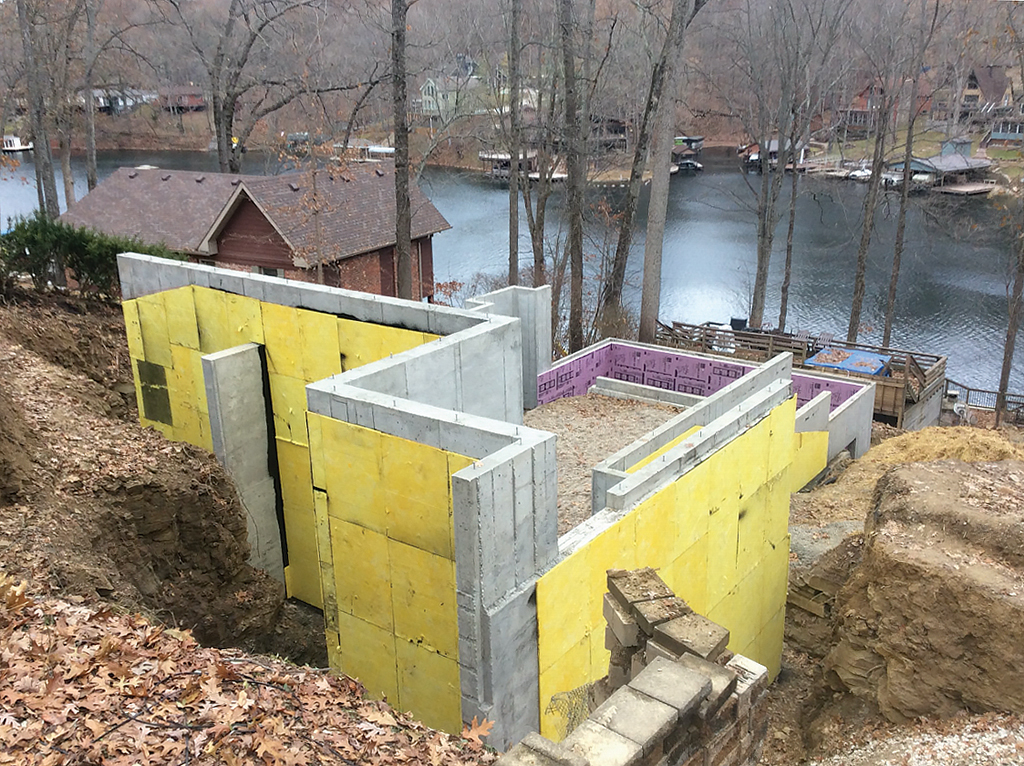
With a name like Sweetwater Lake, it should not come as a surprise that this project is located on a lake lot in southern Indiana, which is known for hard shale and limestone. The lot had a substantial amount of fall toward the lake, and the owner was hoping to save a portion of the lot’s pre-existing block basement foundation. The original plan was to add to the front of this existing basement.
This small footprint only enclosed 1,840 square feet, and in only 346 linear feet of wall, the wall stepped thirteen times from 1 foot up to 19 feet and 8 inches. Wall thicknesses were 8, 10, and 12 inches for a total concrete volume of 136 cubic yards with 8,257 pounds of steel.
Due to county building code requirements, the original foundation could not be kept, so we moved into demolition and hauled materials off site. When we proceeded with excavation, we soon encountered hard shale and limestone, which required a large excavator with a hammer. This unexpected obstacle greatly slowed down the project’s excavation phase.
In order to maintain access on the small lot throughout construction, we left off the garage foundation until the end of the project, facilitating access for our form delivery truck cranes, concrete pumps, and gravel conveyors. Adding to the challenge, the existing gravel drive was steep and tight for large trucks and equipment. When the walls were finally poured and stripped, the gravel conveyed, and the basement slab poured, we proceeded to add the attached garage foundation, which required 12-by-16-inch-tall retaining walls.
The walk-out basement included nearly 200 feet of 24-by-12-inch footings with #5 dowels that were 12 inches o.c., all installed on limestone rock. The extreme terrain made navigating and forming these footings difficult, but with CAD and total station layout, we were able to install these footings with precision.
As mentioned earlier, our walls stepped 13 times, ranging from 19 feet and 8 inches tall to 1 foot tall. To retain the high upper grade despite the severe fall of the grade toward the lake, we had to pour a wall that was 12 inches by 19 feet and 8 inches at the front of the lot as a part of the basement wall. This wall extended up through the first floor, supporting the second-floor system. We worked with the framer to establish the correct wall height. The wall then stepped with the grade from 19 feet and 8 inches down to 9 feet; we kept that height through the fireplace and then stepped down further to 5 feet for the “four seasons” room. The garage’s side walls stepped from 19 feet and 8 inches down to a 16-foot common wall and then down to 9 feet. The walls continued at this height to a large window and concluded at the “four seasons” room.
This property overlooks a beautiful lake, so it is no surprise that the owners wanted to take full advantage of the view. With an abundance of topographical fall, we were able to install this walk-out basement to complement the lot’s terrain and the view.
______________________________________________________________________________
ABOVE-GRADE ALL-CONCRETE SINGLE-FAMILY RESIDENCE
North Tropical on the Intercoastal Waterway, Florida
TCB WALLS INC. OF MELBOURNE, FLORIDA
Member Since 2019
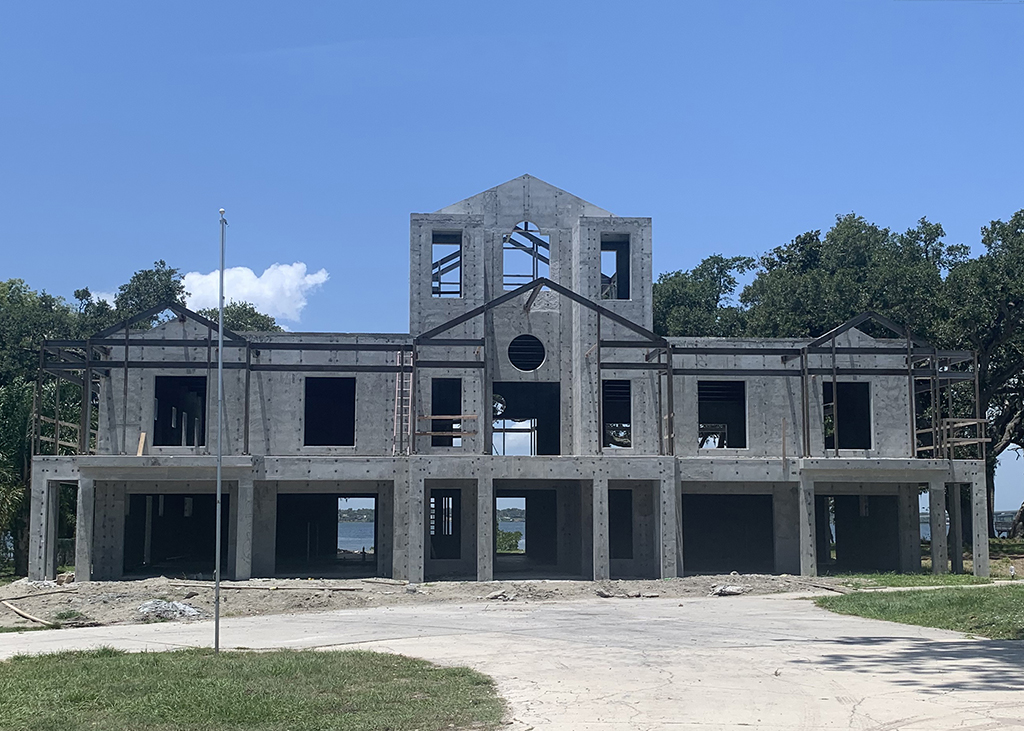
This above-grade concrete home was built in the state of Florida, where a reliable market is developing for the durability and security realized with all-concrete shells.
This job had a little bit of everything going on, and no single aspect was considered out of the ordinary. However, combining so many complicated items in one job made the project more unique in scope. The project consists of over 1,300 total linear feet of concrete wall throughout its 15,000-square-foot footprint, and the project totaled over 380 cubic yards of concrete.
The desire was for a stormproof “bunker” that would also provide protection from other potential threats. “It’s what we do, and we were involved from the initial conceptual drawings,” said Timothy Ball, president of TCB Walls Inc. “Extensive time was spent prior to each phase to allow the crews to run them smoothly.” This included working diligently and meticulously to have all questions answered and all info in hand before sending a crew out to start a phase.
One of the special materials incorporated in the project was helix-twisted micro-steel reinforcement (TSMR), which was used extensively in the structural design. MMFX rebar was used in the structural decks around the entire structure to mitigate future corrosion issues, since the project is located on an intercoastal waterway in a saltwater environment. All concrete on the project used a high-early 5,000-psi mix, and all 28-day breaks came in around 8,000 psi.
The use of a lull with personnel baskets and cranes was vital to being able to reach some of the places on this project, as there were access restrictions protecting trees (some of which are over 100 years old) growing all around the project area.
“It is just really cool for a small company like us to be recognized for all our hard work on a national platform,” said Ball. “I feel like all the members of our team will be even more proud of the work that we do than normal. It’s going to be something for all our employees to talk about with other trades and competitors. I believe this award will elevate the project locally for our customer as well.”
______________________________________________________________________________
COMMERCIAL FOUNDATION STRUCTURE
Crossover Work Foundation
CUSTOM CONCRETE OF WESTFIELD, INDIANA
Member Since 1986

This commercial structure project is the first industrial project undertaken by Custom Concrete. The move into this market segment challenged the team, both from a scheduling perspective and a safety perspective. The team drew from experience from past projects to help them successfully handle the challenges created by scheduling and access. Relying on the general contractor gave them confidence and understanding in managing all safety requirements.
Although small — just over 1,100 square feet — this project consisted of more than 600 cubic yards of concrete and 35 tons of steel reinforcement. The footings alone had over 6 tons, consisting of #8 and #10 bars. The cast-in-place walls were 8 feet tall, some of them at 12 and 16 inches in thickness.
The most significant challenge in this project’s construction was the restricted access. All deliveries were managed through security checks, and only the daily usage was permitted on site — no schedule storage was permitted. Since the equipment for handling the materials could not be used near the installation site, the location complicated the installation of steel reinforcement, requiring most of the 35 tons to be hand-delivered down into the forming. This distance also meant that all forming baskets had to be placed into the hole using a large crane. Most of the concrete was placed under roof at a considerable distance from safe access. Our team devised a plan to use two concrete pumps set in tandem, so deliveries to one could be pumped to the next and then on to the placement positions.
The pad itself was complicated at 24 inches in thickness with double-mat reinforcement. The placement alone was time-consuming and tedious. This pad required nearly 300 inertia blocks, each isolated using 4-inch foam with 1.5-inch gaps on both sides created using ¾-inch plywood. As this was an industrial foundation project, accuracy was critical for both the footing and the finished wall elevations. Angle iron was embedded around the entire interior perimeter at the seam where the wall meets the ceiling. Coordinating this with a general contractor whose schedule was much different from ours required careful communication to set expectations and manage conflict resolution.
______________________________________________________________________________
The Best of the Rest
With a near record number of entries this year, including a whopping 11 projects in the over-5,000-square-foot category, many great works of cast-in-place concrete were recognized by the participants evaluating the entries. This year, seven honorable mentions were also selected. These included:
ABOVE-GRADE CONCRETE HOME
Main Street Residence
PURINTON BUILDERS INC., EAST GRANBY, CONNECTICUT
Member Since 1999
______________________________________________________________________________
SINGLE-FAMILY RESIDENTIAL FOUNDATION, 2,000 TO 5,000 SQ. FT.
I-4 Chatham Hills
CUSTOM CONCRETE, WESTFIELD, INDIANA
Member Since 1986
K-83 Chatham Hills
CUSTOM CONCRETE, WESTFIELD, INDIANA
Member Since 1986
______________________________________________________________________________
SINGLE-FAMILY RESIDENTIAL FOUNDATION, OVER 5,000 SQ. FT.
Cook Residence
SCW FOOTINGS & FOUNDATIONS, SALT LAKE CITY, UTAH
Member Since 1978
Victory Ranch Lot #202
SCW Footings & Foundations, Salt Lake City, Utah
Member Since 1978
Private Residence
HERBERT CONSTRUCTION COMPANY, MARIETTA, GEORGIA
Member Since 1992
Deer Crossing Lot #33
SCW FOOTINGS & FOUNDATIONS, SALT LAKE CITY, UTAH
Member Since 1978
Chapin Concrete Anchors the Return of Certified Foundation Companies to South Carolina
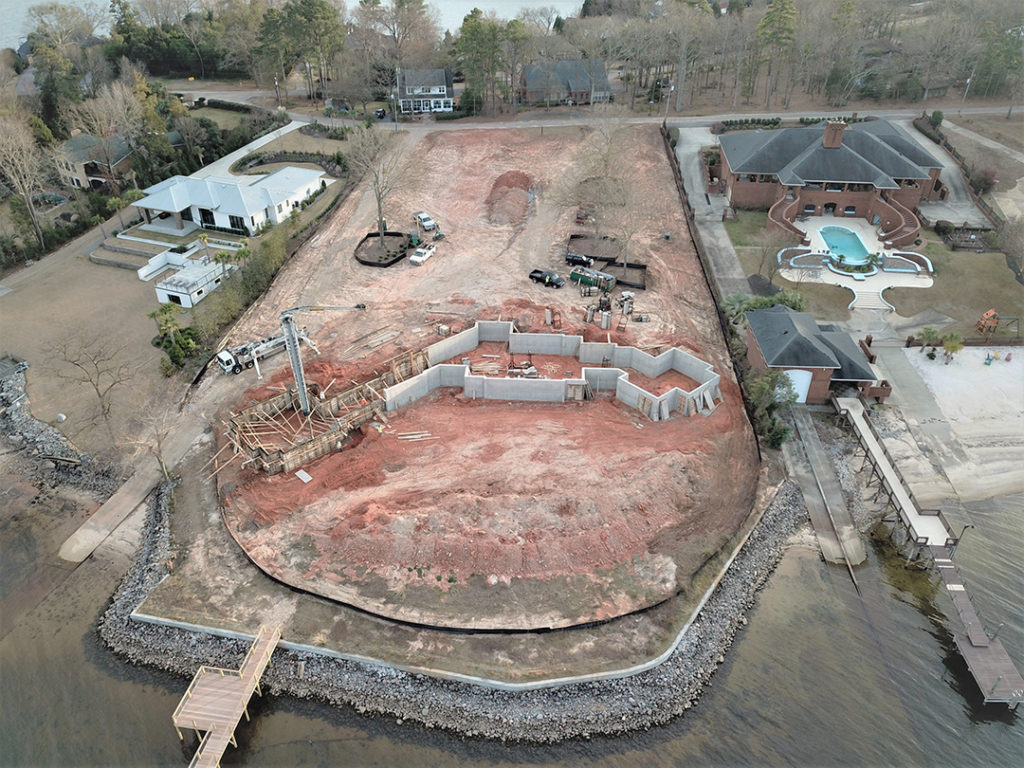
Some of the concrete foundations constructed in the state of South Carolina will once again be produced by the state’s only CFA-certified foundation company, Chapin Concrete Contractors Inc., a company based out of Chapin, South Carolina. “Certified Residential Foundation Company” is a program rating that offers third-party quality assurance for professional concrete foundation companies. This program rating was established by the Concrete Foundations Association (www.cfaconcretepros.org), an organization headquartered in Mount Vernon, Iowa.
Recognizing the need for a national program to establish a consistent base of knowledge and quality assurance for the cast-in-place concrete foundation industry, the Concrete Foundations Association™ of North America created the Certified Residential Foundation Company program over a decade ago. The program currently recognizes certified companies in the states of Georgia, Illinois, Indiana, Iowa, Maryland, Missouri, Nebraska, North Carolina, Ohio, Pennsylvania, Wisconsin, and, once again, South Carolina.
“The Certified Foundation Company program continues to elevate companies that choose one of the most professional paths for demonstrating their quality, craftsmanship, and commitment to the marketplace,” stated Jim Baty, Executive Director for the CFA. “The evolving program builds on the technical requirements of the Certified Residential Foundation Technician that is offered through the American Concrete Institute.”
Introduced in 2007, the technician program established a grueling examination of a company’s knowledge base in regards to their understanding of the codes and standards that make up the minimum requirements for today’s residential concrete foundations. However, having a person on staff (or multiple project managers) who knows the important code document sections was only a start to formally recognizing a concrete company’s competency. The industry needed a recognizable standard for how quality foundation companies should operate.
Chapin Concrete Contractors Inc., established in 2012, has stepped out to be recognized for the excellence they produce, having been a division of Ashmore Concrete Contractors Inc. up until now.
The company recognized that, in this aggressively growing economy, one of the clearest ways to show commitment to excellence and industry leadership is to be credentialed in the major segments of the industry’s services. Chris Marra, vice president for the company, became an ACI/CFA Certified Foundation Technician during a recent World of Concrete event. “The obvious next step for us to take was to pursue this company being recognized as a CFA Certified Foundation Company,” said Marra. “Chapin carries a lot of pride as we service our customers, and we want them to know our level of commitment to employing top-skill laborers as well as maintaining the strongest business practices.”
When the CFA’s certification program for companies first began, South Carolina saw an early market leader set the pace — Action Concrete Contractors, who are no longer serving the market. “Chapin has entered the landscape of concrete construction in the southeast that few can match,” said Baty. “We are very pleased to have the opportunity to evaluate their credentials and now represent them to the marketplace.”
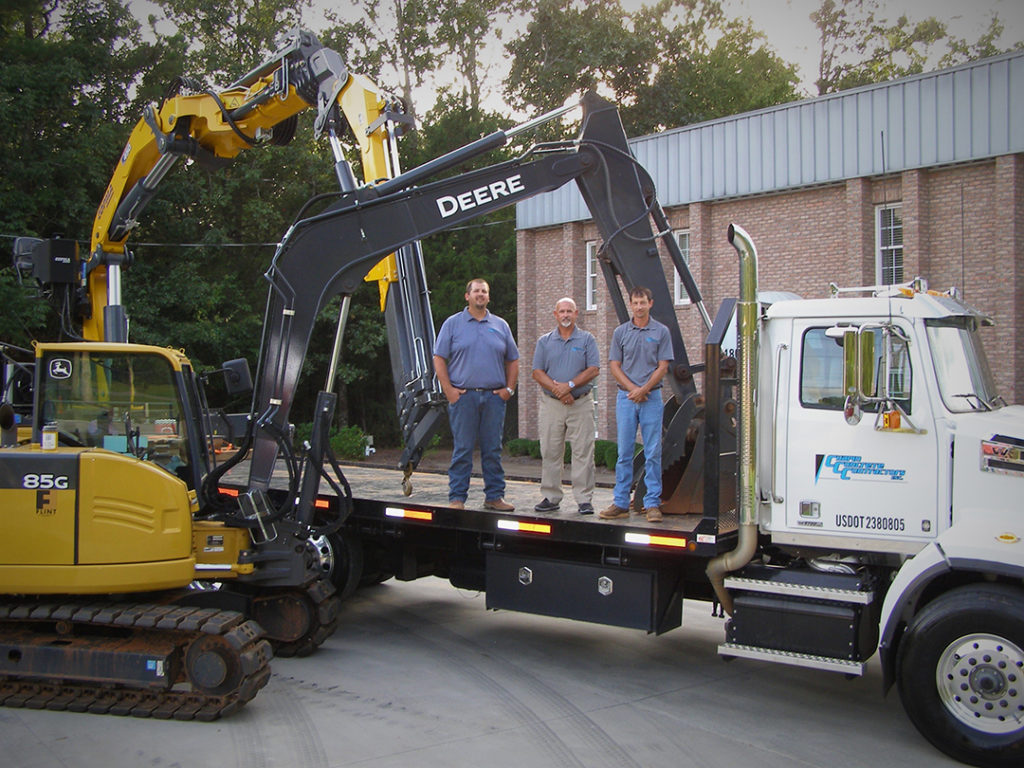
Chapin Concrete Contractors Inc. is proud to be able to hold a strong place in the southeast construction landscape. “We know the commitment to becoming certified is a combination of our statement to the marketplace as well as to the potential workforce,” said Marra. “We hope every potential hire that walks into our office recognizes the value this establishes for their commitment to the process.”
Learning From Leading: Convention 2020 Wrapped Up

Each year, the Concrete Foundations Convention brings together concrete contractors, designers, and suppliers from across the country for three days of education, networking, awards, technology, and much, more! Although the global pandemic prevented gathering in-person in a normal fashion, that did not stop the Concrete Foundations Association from hosting a virtual event unlike any other. The event was complete with an expanded education program, a full expo hall, product demos, a showcase pavilion where attendees were able to vote on the Projects of the Year, and live entertainment. This year’s participants were able to engage in an environment that kept each person safe at home or in an office while also expanding the ideas of what practical networking can be all about.
The CFA partnered with VirBELA and Event Farm to provide an innovative alternative to connect people in this industry with their peers, helping everyone find ways to better their businesses! Concrete Foundations Convention took place in an avatar-based, virtual campus, with all of the professionalism, energy, and enthusiasm our members have come to expect. The event registered nearly 300 participants, 34 education sessions, 5 promotion partners, 19 sponsors, and 27 exhibiting companies, and it was reported by many to be a great success! 2020 has demanded that we be innovative in the ways we work, communicate, learn and gather. Although we were saddened by the harsh reality that we were unable to welcome attendees to Charleston, the decision to go virtual was not only an easy decision, but one the CFA was proud to make.
The staff spent countless hours researching the best platform for this event as we approached the moment for determining what to do with the scheduled Charleston convention. The CFA Board of Directors reviewed strategies offered by the CFA staff and ultimately supported the risk-management effort proposed as the leading option by the executive director. It was important to find a user-friendly platform with the ability to feature products in an exhibition hall that was engaging and allowed exhibitors the opportunity to chat with attendees throughout the event. Additionally, many companies were interested in broadening access to education, an ambition a virtual experience could facilitate — so the conditions were right for an avatar-based campus.
The expanded education program consisted of six education tracks, providing diverse ways for companies to benefit from the ease of access to learning. The six categories were: executives, safety managers, field crews and wall foremen, shop/facility managers, operations/HR, and project managers.
“Traditionally, this event brings together industry-leading owners and executives from across the country,” said James Baty, executive director of the CFA. “In going virtual, we were able to make attendance very economical, eliminate travel expenses, and expand our education tracks of interest to a very broad range that included management and workforce interests,” said Baty. “From concrete basics and construction practice to the trusted higher-level strategy sessions our regular attendees are accustomed to, we were thrilled to be able to draw attendees from the workforce who typically would not be able to attend an in-person event.”
In addition to the expanded education program, the event featured an expo hall with 27 exhibiting companies, many of which were event sponsors. “One of the reasons we host this event is for our supplier and manufacturer members to communicate new technologies and foster meaningful relationships with their customer base,” Baty“The amount of support we had for this event not only allowed us to offer deeply discounted registration prices and cover a lot of the expenses that came with the platform, but it gave attendees the chance to connect with new products and technologies that will make their next project safer and more cost efficient at a time when it’s needed the most.”
Going virtual came with many benefits: expanded programing, broadened participation, and deeply reduced registration costs and other expenses, to name a few. In addition to these benefits, for the first time ever, the CFA was able to showcase Projects of the Year videos in a space called the Showcase Pavilion. Each video featured the Projects of the Year nominations in great detail, showing the beauty and elements that are often hidden once the project is complete. Attendees were able to enter the space throughout the week to watch the videos and vote for the projects they deemed best for each category.
The three-day event wrapped up with live music on the beach stage from Full Moon Horizons. “You could definitely see a different side of our attendees as they made their avatars dance to the music on the beach,” said Baty. “I don’t think we would have seen nearly as much dancing at an in-person event. Although, when we’re able to gather in person again, I look forward to seeing everyone’s real dance moves at the closing social.”
“One of the highlights to my year is the CFA Summer Convention,” said Jason Ells, senior Vice President of Custom Concrete. “It’s a place that I get to meet people in similar roles dealing with similar issues in our industry. It’s an opportunity to learn about the latest and greatest in technology and equipment, and I get to hear from some of our industry experts on best practices to run our business safely and effectively,” said Ells. “I assumed this, like so many other exciting things, would be canceled due to the pandemic. To my surprise, Jim and the team at the CFA headquarters pulled a rabbit out of their hat. With this technology, we were able to meet and talk with people to catch up, we got to see the new technology and equipment, and learn from the best and the brightest in our industry.”
The companies that took a risk and rose to the challenge of helping in the development of this event included some CFA Platinum Sponsors, namely Irving Equipment Company, ICC Distributing LLC, Verizon Connect, and Form-A-Drain; some Gold Sponsors, namely GMX Waterproofing Solutions, GCI Stone Slingers, and Max USA; and some Silver Sponsors, namely White Cap, Crew Tracks, Fox Blocks, Thermomass, Euclid Company, Cranes and Equipment Company, Prinsco, Western Forms, Robotic Surveying Solutions, Badger Forms, Progressive Foam, and Boman Kemp.

“On behalf of the entire CFA staff and our Board of Directors, I want to express our sincere thank you to everyone who was a part of this year’s event,” Baty said. “While we look forward to someday being able to gather in person again, our network demonstrated an effective way we can come together during these uncertain times and generate significant leadership and learning that evidence why we are now advancing our #CFAConcretePros brand.”
Watch www.cfaconcretepros.org for more information on future events so as not to miss engaging with this practical and enjoyable approach to education, networking, and product development as the future of expanded access to learning becomes increasingly prevalent and sought out.
The Times They Are a-Changin’
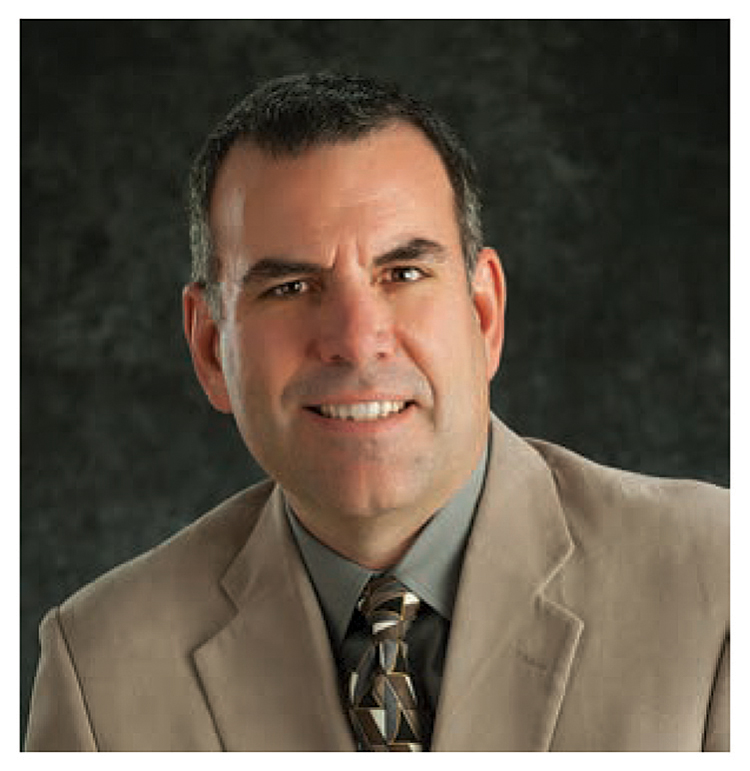
I have had this tumultuous and famous Bob Dylan ballad playing in my head for weeks now, as change is perhaps more noticeable during this season than during any other time of year. Color, temperature, atmosphere — all is evidencing a transformation. Serious storms, raging fires, a planet in stress — I wonder if Dylan would have added more stanzas to his poem if he had written it today. Funny how much of what is written these days gets at the same thoughts Dylan penned about the 1960s.
There is a peculiar counter idea to the lyrics written by Dylan, however; it is summarized in this quote written in the mid-1880s by Jean-Baptiste Alphonse Karr: “The more things change, the more they remain the same.” Karr, a teacher by profession, was at that point the editor of the newspaper Le Figaro and a monthly journal called Les Guêpes. Without getting into the politics of this particular phrase or risking applying it to either side of the present political environment, I will say that I find the comparison of these two epigrams electric. Caught in the middle is the even older theory held by Heraclitus of Ephesus, “panta rhei,” which is Greek for “life is flux”— the idea that everything, or all things, change. That is, even change changes.
So, in my wonderings during this time (paired with my lack of wanderings), we set sail on the latest course and the newest of changes for your Association. I favor change. I’m inspired by it, motivated by the opportunity it creates, and eager to work on aspects of resolving the threads initiated by it. For if change does not exist, particularly in an organization such as this, complacency can set in; or worse, we can become irrelevant.
One absolutely cannot describe the Concrete Foundations Association as irrelevant. We hosted the industry’s first virtual event, the #CFAAtTheEcho, and the experience was as much like a physical event as possible. Your staff has launched a new website solely aimed at interaction, a trusted place for you to participate in and bear witness to the CFA community. In this issue, we are excited to introduce new board members who are ready to answer the challenge of having a new executive committee turning up the heat on what we can be. Later this fall, the board will be entering a strategic planning session (which has not been undertaken since 2012) as we look for ways to advance the momentum established by such industry-leading efforts.
We know Dylan and Karr to be prophetic in every generation, and Heraclitus, in the end, to ring truest of all. Life is lived one moment of change after the other. It isn’t about resisting change or directing change, but about realizing that change is opportunity. Those who lead and follow through change will arrive at the end better because of it… just, perhaps, in very different places. I’m grateful for those of you in this Association who are participating in being part of the leading edge.
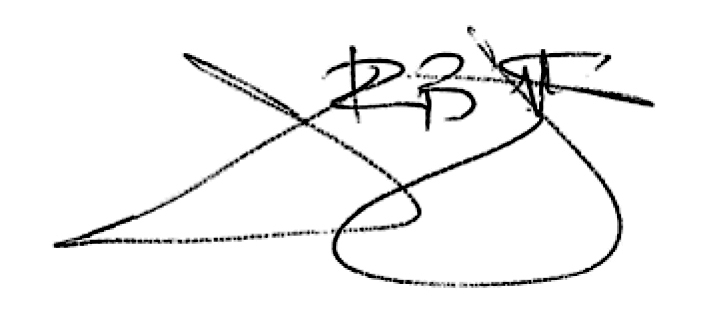
Moving the Association Forward
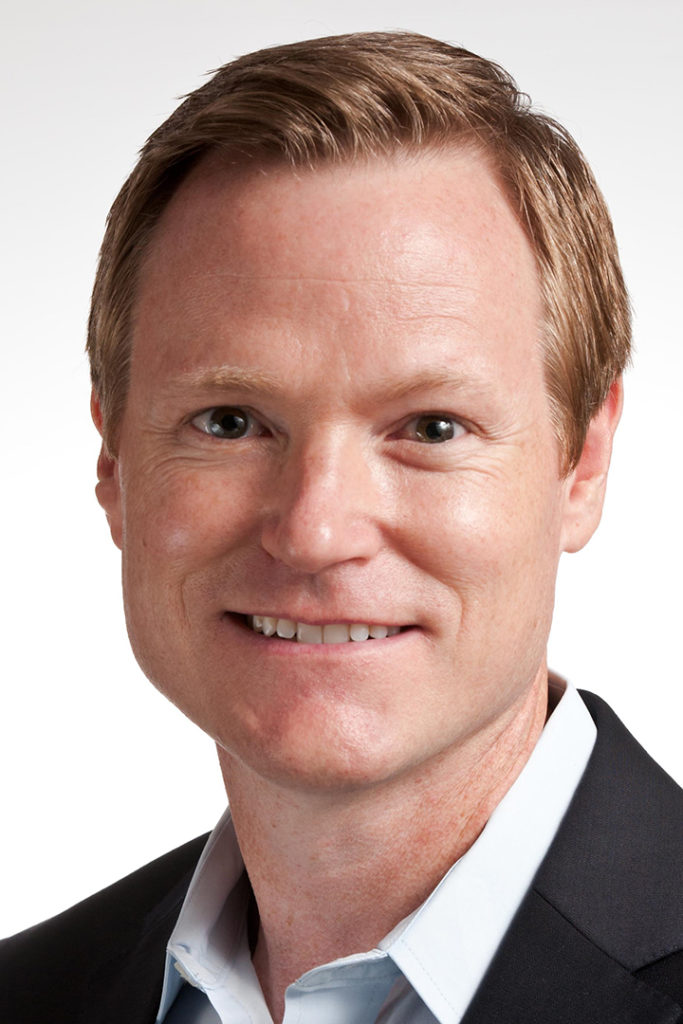
In July, the Concrete Foundations Association held our annual convention online. The virtual event was a big success and a bright spot in a summer filled with uncertainty.
During that convention, I was elected president of the association. I am incredibly honored to serve this association and to follow in the footsteps of past presidents. The list of past presidents is a long record of intelligent, enthusiastic leaders that have wanted to help their fellow contractor. With the past presidents’ hard work and dedication, this association has changed the entire industry for the better.
I’m excited to work with the CFA Board of Directors; the executive director, Jim Baty; and his staff to improve our industry and support cast-in-place contractors.
Thank you to Phil Marone, who served as president over the last two years. He now becomes the chairman of the board. I also want to thank Jason Ells, who will become vice president; Sean Smith, who is stepping in as secretary; and Ken Kurszewski, who is the new treasurer. And I extend a big thank you to the new and continuing board members, whose names are too many to list here but can be found on the previous page.
Those who serve on the board of directors give their time and money to attend meetings in an effort to determine the best direction for the association. For all of us, these are unpaid jobs that we squeeze in to our already busy lives. But, the payoff for the time and effort spent is immeasurable. For example, we form friendships with fellow members who we can call throughout the year to get an opinion or solve a problem, and we improve the entire residential concrete industry through educating and assisting cast-in-place contractors.
I look forward to my two-year term as president of the CFA, and I look forward to improving our association and our industry.
If there is something you’d like the association to focus on or if there is a way for us to assist you in your business, please send me an email. I’d like to hear what you have to say and figure out a way to help.
To your success,
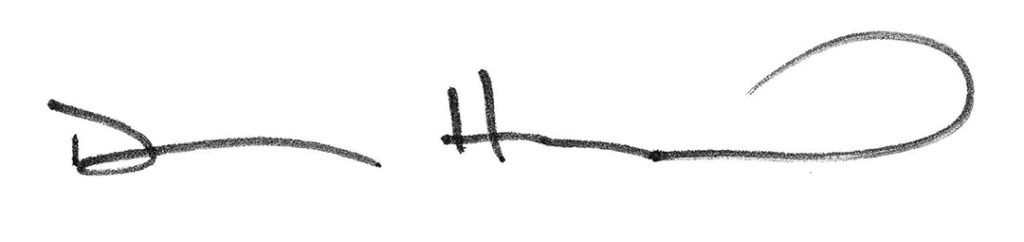
Doug Herbert, CFA President
Putzmeister, America, Inc. Announces Bob Bartholomew as President and Chief Executive Officer
Putzmeister America, Inc. announces Bob Bartholomew as President and CEO for Putzmeister America. Bob, who has served for over five months as interim CEO, provided strong leadership to the Putzmeister team and delivered excellent results during a challenging time.
A visionary leader, dedicated team player and action-oriented manager, Bob will lead the Putzmeister America business into a bright future by successfully navigating the challenges and opportunities of the current economic climate.
Bob joined the Putzmeister team in 2018 as CFO. He is a global finance leader with over 25 years of progressive leadership experience in diverse manufacturing and financial services industries. His background includes finance and operational leadership, multi-site accountability, emerging market development, and international experience in different areas of responsibility.

Putzmeister, America, Inc.
“I am very excited to be take on this role. Putzmeister has a talented management team and dedicated team members who are uniquely equipped to address these challenging times. Our market leadership resonates very strongly in the industry. Our team, together with our current and future product offerings, position Putzmeister well to capitalize on that market leadership. Every Putzmeister team member is focused on delivering the best and the highest quality products and services to our customers. My mission is to lead this team to even greater accomplishments.”
Bob Bartholomew – CEO, Putzmeister, America, Inc.
In his new role, Bob will report to Martin Knoetgen, CEO of Putzmeister Holding GmbH (Germany), and he will remain based at Putzmeister America’s headquarters in Sturtevant, Wisconsin. He can be reached at bob.bartholomew@putzmeister.com.
WHITE CAP AND CONSTRUCTION SUPPLY GROUP COMBINE TO CREATE $4 BILLION MARKET-LEADING DISTRIBUTOR OF CONCRETE ACCESSORIES AND SPECIALTY CONSTRUCTION PRODUCTS
Transaction Will Enhance Capabilities to Serve Professional Contractors with Broader Product & Service Offerings and Expanded Reach
ATLANTA, GA – October 19, 2020 – White Cap Supply Holdings, LLC (“White Cap”) and Construction Supply Group (“CSG”) announce today the successful separation of White Cap from HD Supply and its combination with CSG. The combined transaction, valued at approximately $4 billion and including an investment by Clayton, Dubilier & Rice (“CD&R”) funds, creates the leading North American distributor of a diverse mix of concrete accessories and specialty construction and safety products by revenues with more than $4 billion annually.
Following the transaction, CD&R funds hold a 65 percent ownership interest in the combined company, and the prior shareholders of CSG, led by The Sterling Group, hold a 35 percent interest.
CSG and White Cap have highly complementary product offerings and geographic footprints, aligned cultures and strong talent focused on providing exceptional customer service to professional contractors. John Stegeman, CEO of White Cap, and Alan Sollenberger, President of White Cap, will lead the combined business.
“Both White Cap and CSG share the same vision of continuous growth with the goal to relentlessly improve customer service,” said John Stegeman. “By joining together, our platform allows expansion of our product and service offerings across more than 400 locations in 46 U.S. States and 8 Canadian Provinces. Our goal is to provide even greater value for our customers and enhance our ability to serve with excellence. This is an incredibly exciting time for our associates, customers, and suppliers.”
The combined strength of White Cap and CSG will include:
- An outside sales force of over 850 associates with significant industry experience
- More than 1,000 inside and counter sales associates to deliver on our promise of two-hour ready will call at our locations
- Nearly 2,000 delivery vehicles to enable our same day or next day service to job sites
- A comprehensive offering of 400,000+ products from more than 4,500 suppliers
“Both businesses have incredible histories of exceptional customer service,” said Alan Sollenberger. “As we join together, we will continue to build on our vast experiences and stronger future by investing in focused local growth initiatives with the support of our national platform.”
“Our goal with this transformational combination is to bring to life the many benefits of our combination for our customers,” said John Stegeman.
About White Cap
White Cap serves as a one-stop shop providing concrete accessories and chemicals, tools and equipment, building materials and fasteners, erosion and waterproofing and safety products to professional contractors by meeting their distinct and customized supply needs in non-residential, residential and infrastructure end markets. White Cap operates 268 branches with approximately 5,300 employees and offers more than 400,000 SKUs to 200,000 customers. For more information, visit www.whitecap.com.
About Construction Supply Group
CSG is a leader in the distribution of specialty construction materials, accessories and tools, primarily for professional concrete and masonry contractors in the United States and Canada. With over 132 branches and approximately 2,000 employees, CSG offers over 60,000 SKUs to over 65,000 customers. For more information, visit www.constructionsupplygroup.com.
About Clayton, Dubilier & Rice
Founded in 1978, Clayton, Dubilier & Rice is a private investment firm. Since inception, CD&R has managed the investment of more than $30 billion in 95 companies with an aggregate transaction value of more than $150 billion. The Firm has offices in New York and London. For more information, visit www.cdr-inc.com.
About The Sterling Group
Founded in 1982, The Sterling Group is a private equity investment firm that targets controlling interests in basic manufacturing, distribution, and industrial services companies. Typical enterprise values of these companies range from $100 million to $750 million. Sterling has sponsored the buyout of 57 platform companies and numerous add-on acquisitions for a total transaction value of over $14.0 billion. Currently, Sterling has over $4.0 billion of assets under management. For further information, please visit www.sterling-group.com.
OSHA Webinar Launches 7th Annual National Stand-Down To Prevent Falls on Sept. 14, 2020
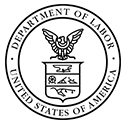
U.S. Department of Labor Occupational Safety and Health Administration Office of Communications Washington, D.C. www.osha.gov | For Immediate Release September 11, 2020 Contact: Office of Communications Phone: 202-693-1999 |
WASHINGTON, DC – The U.S. Department of Labor’s Occupational Safety and Health Administration (OSHA) announced today that it will host a webinar on Monday, Sept. 14, 2020, to kick-off the 7th annual National Stand-Down to Prevent Falls in Construction, Sept. 14-18, 2020. OSHA will conduct the webinar on Monday, Sept. 14 at 1 p.m. EDT. Featured speakers include:
- Loren Sweatt, Principal Deputy Assistant Secretary of Labor for Occupational Safety and Health
- Scott Ketcham, Director, OSHA Directorate of Construction
- John Howard, MD, Director, National Institute for Occupational Safety and Health (NIOSH)
- Scott Earnest, PhD, Director, NIOSH Office of Construction Safety and Health
- Chris Trahan Cain, Executive Director, Center for Construction Research and Training
Register in advance for the webinar. Follow the webinar at #StandDown4Safety and #2020kickoff.
The Stand-Down encourages companies and workers to pause during the workday for topical discussions, safety demonstrations, and training in hazard recognition and fall prevention. As a result of the coronavirus pandemic, OSHA is encouraging employers to promote fall safety virtually or while employing social distancing practices among small groups.
OSHA anticipates thousands of employers nationwide to participate this year. To guide their efforts, the agency is offering a National Fall Prevention Safety Stand-Down webpage with information on conducting a successful event, how to post local events, and additional educational resources in English and Spanish. Employers are encouraged to provide feedback after their events and to obtain a personalized certificate of participation.
For a list of the week’s activities, please visit the Stand-Down events page at https://www.osha.gov/StopFallsStandDown/calendar.html.
The fall-prevention stand-down is a national campaign that was developed in partnership between OSHA, National Institute for Occupational Safety and Health (NIOSH), National Occupational Research Agenda (NORA) and the Center for Construction Research and Training (CPWR). Also supporting the event this year are OSHA-approved State Plans, state consultation programs, American Society of Safety Engineers, National Safety Council, National Construction Safety Executives, U.S. Air Force, OSHA Training Institute Education Centers and several Hispanic organizations.
Under the Occupational Safety and Health Act of 1970, employers are responsible for providing safe and healthful workplaces for their employees. OSHA’s role is to help ensure these conditions for America’s working men and women by setting and enforcing standards, and providing training, education and assistance. For more information, visit www.osha.gov.
The mission of the Department of Labor is to foster, promote, and develop the welfare of the wage earners, job seekers, and retirees of the United States; improve working conditions; advance opportunities for profitable employment; and assure work-related benefits and rights.
# # #
U.S. Department of Labor news materials are accessible at http://www.dol.gov. The Department’s Reasonable Accommodation Resource Center converts departmental information and documents into alternative formats, which include Braille and large print. For alternative format requests, please contact the Department at (202) 693-7828 (voice) or (800) 877-8339 (federal relay). |
National Safety Stand-Down to Prevent Falls in Construction

Again this year, the Concrete Foundations Association is participating as a promotion and awareness partner with OSHA to bring contractors resources to improve their communication and practices for keeping workers safe.
The 7th annual National Safety Stand-Down to Prevent Falls in Construction next week (September 14-18, 2020), Doug Kalinowski, Directorate of Cooperative and State Programs has provided a wealth of new tools and resources to assist workplaces in participating in the Stand-Down:
- Official Stand-Down Kickoff: Monday Sept 14th 1 PM EST virtual webinar featuring:
- Loren Sweatt, Principal Deputy Assistant Secretary of Labor for Occupational Safety and Health
- Scott Ketcham, Director, OSHA’s Directorate of Construction
- John Howard, M.D., NIOSH Director
- Scott Earnest, PhD, PE, CSP, NIOSH, Director, Office of Construction Safety and Health
- Chris Trahan Cain, Executive Director, CPWR- The Center for Construction Research and Training
- Register here
- Drop-in banner: Download a banner [English or Spanish] designed for the Fall Stand-Down you can adapt for use in raising awareness about the Fall Stand-Down in newsletters, e-mail blasts, and even social media.
- Stand-Down Events: Stand-Down events and trainings that are free and open to the public are now being added to the Events section of the Stand-Down webpage. Find an event near you, or, if you plan to host a free event that is open to the public, submit the event details or contact your Regional Stand-Down Coordinator.
- Resources:
- New – [Videos] Stand Down Stories from the Outer Banks, North Carolina; Baker Roofing Company, Virginia Beach; and The Massachusetts Fatality Assessment and Control Evaluation (FACE) Program
- New – 2019 Data Analysis: Factsheet and Full Report
- New – Regional Hispanic Contractors Association Stand Down Virtual Training Opportunity English or Spanish Registration
- New– NECA Stand Down Webinar: NECA will be presenting a Falls Stand-Down on Tuesday, September 15th at 2pm EST. It appears to be on the heels of the NRCA 30 minute session that are on Tuesday, Wednesday and Thursday, (12:30 CST, 1:30 EST). Register here. (Flyer attached)
- New– CPWR podcast “7th Annual Safety Stand-Down Event” is now live. It can be streamed on various platforms (more info here). Embedded it in the One-Stop Stand-Down shop for easy access: https://stopconstructionfalls.com/one-stop-stand-down-shop/
- Dr. G. Scott Earnest, NIOSH Associate Director for Construction, discusses the National Campaign to Prevent Falls in Construction and 7th annual Safety Stand-Down event. The Stand-Down is scheduled for September 14-18, 2020. This year may look different due to COVID-19, but CPWR, NIOSH, and OSHA have plenty of ideas for participating virtually or at a safe social distance.
- New – Small Business Focus Postcard & Stand-Down site “Plan Provide Trade”Developed by the NORA Falls Work Group in conjunction with the postcard pilot project in both English and Spanish (Preventing Falls Post Cards attached)
- New – CPWR Generic Fall Protection Plan template available in English and Spanish
- Order your 2020 Stand-Down hard-hat stickers and fall-related hazard alert here
- 2020 Infographics
- Include Stand-Down hashtags! #StandDown4Safety #StopFalls #Construction
- OSHA Fall Stand Down Poster here (Spanish)
- Additional resources are available here
OSHA offers as a reminder, anyone who wants to prevent hazards in the workplace can participate in the Stand-Down. Companies can conduct a Safety Stand-Down by taking a break to have a toolbox talk or another safety activity such as conducting safety equipment inspections, developing rescue plans, or discussing job specific hazards. Managers are encouraged to plan a stand-down that works best for their workplace anytime. See Suggestions to Prepare for a Successful “Stand-Down” and Highlights from the Past Stand-Downs.