Making Offices and Construction Sites Safer From the COVID-19 Virus
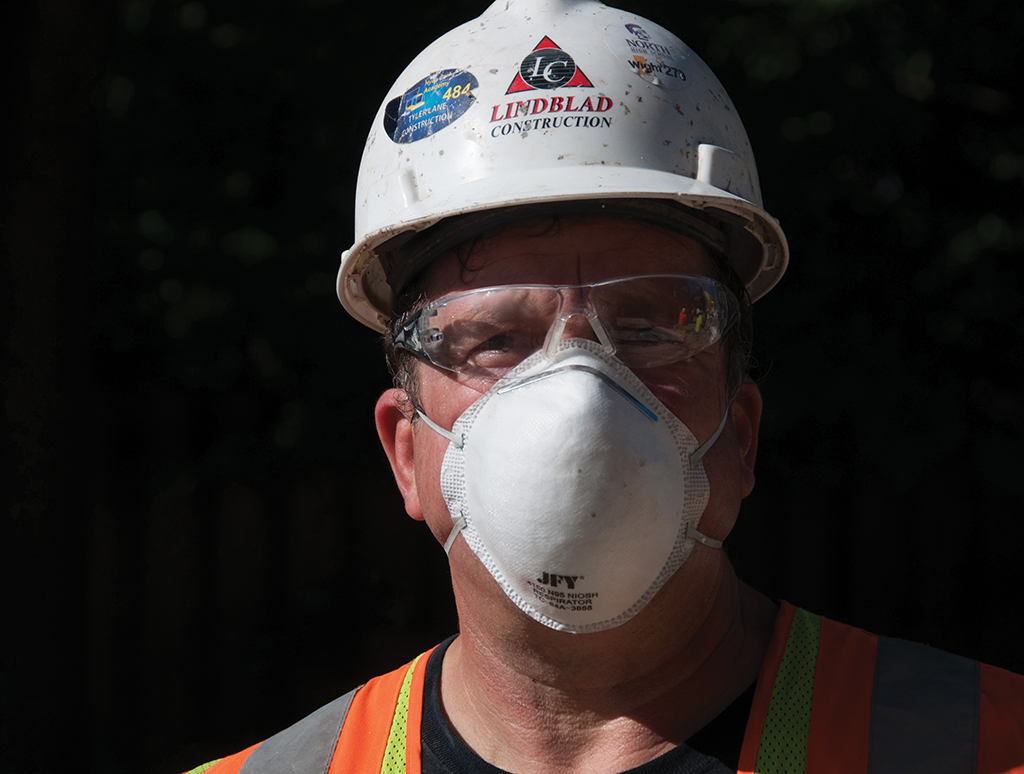
The current pandemic is changing the way we organize for work on construction jobsites. Along with a hardhat, safety vest, steel toed boots, and safety glasses workers must now wear a cloth face covering or an N95 respirator or equal—the new normal. Wearing a mask helps to trap tiny water droplets in your breath so that others don’t inhale them. Others wear masks to protect you when they breathe. When people exposed to the SARS-CoV-19 Virus breathe the droplets they create contain the virus particles. Photo Credit: Joe Nasvik
by Joseph Nasvik
Epluribus unum—out of many, one. This is the Latin motto the United States adopted in 1776 to signify the joining of states to form one national government. At the time, it was a difficult concept for people to accept because it meant that states and individuals would have to give up some of their personal rights to serve a greater cause. Today, the threat to life posed by the new coronavirus brings the e pluribus unum concept back into sharp focus as the country and its people consider personal rights versus one’s responsibility to others.
As social beings, this pandemic preys on our natural instincts to be close to friends and family, and it challenges our ability to work and earn a living. As time passes, it is hard to know if the first tool for fighting a pandemic — distancing ourselves from one another — is working. There is a huge number of victims, and the end is not in sight. The end, when it comes, will likely come through the development of an effective vaccine, the tool that will end the threat of the pandemic.
Construction is regarded as an essential industry in many states, and it is currently challenged to keep workers safe on the job site. “Social distancing” — the current phrase being used for keeping physical distance between people and the first line of defense — requires workers to be a minimum of six feet apart from one another. But construction, especially concrete construction, often requires teams to be much closer together for some work functions, so other safety measures become crucial. Here are some ways construction work is being made safer.
Editor’s Note: Read Concrete Facts online for information about the science behind the virus spreading.
The Tools for Fighting Pandemics
Public health professionals who focus on fighting pandemic diseases recognize four basic tools: social distancing, testing, tracing, and modeling. Keeping people separated from one another is the first major step in preventing the wide spread of the disease. Distancing has been a tactic for preventing the spread of communicable diseases for thousands of years, often by separating the diseased person from the larger group. But when it is unclear who has the disease, the first preventative measure involves isolating each person from every other person.
Developing accurate tests to quickly determine who has been infected and who has not, followed by tracing who has been in contact with who, makes it possible to quarantine only the sick. By tracing and quarantining everyone an infected person was in contact with, the spread of the disease can be limited. Iceland, for example, has tested all its citizens, quarantined those exposed, and effectively used tracing to keep COVID-19 death counts close to zero.
Editor’s Note: Read Concrete Facts online for information about modeling practices being developed.
CDC Recommendations
As a non-regulatory agency, the CDC makes recommendations that are discretionary, not mandatory. But contractors are mandated by other government agencies, such as OSHA, who use CDC’s recommendations (see CDC guidance recommendations for construction at https://www.osha.gov/SLTC/covid-19/construction.html). Unions, and sometimes construction site owners, can also require that contractors provide safe work conditions based on CDC recommendations.
Here are some useful CDC recommendations for contractors and businesses creating their own company guidelines and policies:
- Employers should have a COVID-19 response plan to protect workers.
- Workers should stay home and notify their employer if they are experiencing COVID-19 symptoms. They should not return to work until they meet the criteria determined by their employer, healthcare providers and state and local health departments.
- Workers should notify their employer if a family member living in their home has COVID-19.
- Contractors should limit contact between employees and have them maintain a minimum distance of six feet apart as much as possible. The number of workers sharing small areas — such as at construction sites, in elevators, in trailers, and in vehicles — should be limited if possible.
- Workers should wear cloth face coverings where social distancing is not possible. Cloth coverings should not be substituted for respirators where respirators are recommended or required.
- Frequently touched surfaces should be regularly cleaned and disinfected. On job sites, this includes shared tools, machines, vehicles, handrails, doorknobs, and portable toilets. Cleaning should be done periodically throughout the workday, before and after every shift, and after anyone uses your vehicle, equipment, or workstation.
- Tool sharing should be limited when possible.
- Workers should wash their hands regularly with soap and water for at least 20 seconds or use an alcohol-based hand sanitizer that is at least 60% alcohol. Contractors should supply handwashing stations with clean running water, soap, and disposable towels or conveniently placed hand sanitizer stations.
- Workers should clean their hands before and after work shifts and breaks; after blowing their nose, coughing, or sneezing; after using the restroom; before and after eating; before donning and after removing work gloves; after putting on, touching, or removing cloth face coverings; before donning or doffing eye or face protection (like safety glasses, goggles, or face shields); and after touching objects that have been handled by others.
- Use disposable tissues when you cough, sneeze, or touch your face.
- Employers should provide workers with accurate information about COVID-19, how it spreads, what the risks are, and what protective measures are in place.
- Employers should limit face-to-face contact by limiting meetings, using internet training options, and teleworking when possible.
- Employers should consider increasing the distance between employees by staggering work schedules, limiting access to work areas like trailers and break areas, rearranging tables and chairs in offices, and reducing the number of workers at meetings.
For more information, see the CDC’s guidance for businesses and employers on the website: https://www.cdc.gov/coronavirus/2019-ncov/community/guidance-business-response.html.
Cloth Face Coverings
The CDC recommends wearing cloth face coverings (see https://www.cdc.gov/coronavirus/2019-ncov/prevent-getting-sick/diy-cloth-face-coverings.html) in public settings where other social-distancing measures are difficult to maintain, especially in areas where there is significant community-based transmission of COVID-19. When cloth masks are worn all day, or worn at a location where the wearer may have been exposed, they should be washed with soap and water before their next use.
Cloth face coverings are not surgical masks or respirators and are not appropriate substitutes in workplaces where surgical masks or respirators are recommended or required.
Personal Protection Equipment
Due to the shortage of N95 respirators, some contractors are using KN95 respirators. These are made in China and in most ways are considered equal to N95 respirators. KN95s are generally recommended for occupational use in situations that would typically require an N95. However, if you choose to buy KN95s, be careful to choose a reputable supplier, because there are products on the market that do not meet the standards they claim to meet and come with exorbitant price tags. The CDC has a recorded webinar (https://www.youtube.com/watch?v=w7tVnjrmAmc) with information about what to look for when purchasing respirators from international sources. Respirators, including N95s and KN95s, should be incorporated as part of a regular respiratory protection program (including fit testing) to protect against occupational respiratory hazards.
The primary purpose of a mask is to prevent droplets of water containing the virus from spreading. Virus particles by themselves are too small to get trapped in the mask’s filtering material. Wearing a mask protects others from inhaling contaminated water droplets expired by the wearer as he or she breathes, talks, shouts, sings, coughs, or sneezes. Others wear their masks to protect you.
N95-quality masks also offer some protection to the wearer from bioaerosols such as bacteria, some viruses, fungi, and pollen if they are fit carefully around the nose and mouth. They should be replaced when they are physically damaged, there is increased breathing resistance, or if there are other hygiene issues.
Some contractors believe that using face shields can be a substitute for breathing masks. These shields can block splashes and sprays, but they do not provide respiratory protection. Even though the shields can be easily cleaned and reused, they are not currently rated as adequate replacements for face masks or respirators. Therefore, if they are used, they should be considered an additional protection.
For more information about each of these three different tools, see the CDC infographic on facemasks and respirators at https://www.cdc.gov/niosh/npptl/pdfs/UnderstandingDifference3-508.pdf and the CDC’s information about cloth face coverings.
How One Contractor Is Making His Job Sites Safer
Mark Stadalsky, the vice president of Lindblad Construction located in Joliet, Illinois, says his company specializes in industrial concrete in several states, serving the pipeline industry, electrical power distributors, and heavy industrial companies. In Illinois, construction is considered an essential industry, so Lindblad has been able to work throughout the pandemic. Stadalsky says their team became very curious when news of the COVID-19 pandemic first appeared, and they decided it would likely become a major threat to the construction industry and their workforce. So the company’s management, safety experts, and consultants engaged in six weeks of collaborative discussions to work out a company protocol guideline with carefully defined pathways they could use to guide decisions about how to treat worker health issues. For example, if an employee called in to say he or she was ill but did not have COVID-19 symptoms, the company protocol defined a specific pathway to follow. If an employee did have COVID-19 symptoms but had not been tested, there was another defined guideline. If an employee tested positive for the COVID-19 virus, there was yet another set of procedures to follow.
Lindblad also correctly predicted early on that wearing breathing masks would become mandatory, so they bought a supply of N95 masks before they were scarce and then explored possible sources for securing a steady supply of KN95 masks. At the same time, the company hired people to make cloth masks for use by all company employees.

Some of Lindblad’s clients specify how workers on their job sites will be protected with regards to the COVID-19 virus, and Lindblad accommodates their specifications, so long as they meet Lindblad’s protocol. “For example,” Stadalsky said, “one of our clients requires workers to wear N95 or KN95 masks instead of cloth masks, so we follow their requirements.”
Lindblad protocol includes the following:
- They office staff follow a network of guidelines tailored to their duties.
- In the construction yard, everyone wears a mask.
- As much as they can, workers on job sites distance themselves from others.
- On job sites, Lindblad regularly cleans all touch points and common areas.
- They have full-time and part-time safety inspectors in the field at all times.
- During the first six weeks of the pandemic, they sent out a daily COVID-19 message designed to give workers accurate information and put them more at ease.
- They provide daily wellness checks for all employees and send them home if they have relevant symptoms.
- They are planning for the possibility of a pandemic resurgence in the fall.
A Word About Aerosols
The word “aerosol” is currently being used by the media primarily to describe the smaller droplets created when people (and animals) exhale. Aerosols are defined as droplets that are smaller than five microns in size. Anything larger than five microns is a non-aerosol droplet. All droplet sizes can contain the COVID-19 virus or other viruses.
Aerosol droplets are formed in the very small airways of the lower lung during normal breathing processes. They consist of moisture combined with mucus and surfactants, and because they are so light, they can remain airborne for several hours. This can be especially dangerous in closed environments with reduced ventilation.
Cloth face coverings can trap droplets larger than five microns, but only N95 breathing masks can trap aerosol droplets down to about one micron in size. Droplets smaller than one micron cannot be trapped by masks.
Recent research suggests that the smallest aerosol droplet sizes can contain one virus while large droplets created by rapid exhalation can carry many. There are many more small aerosol droplets created than there are larger droplets, so the risk of infection from aerosols is higher, especially because aerosols can remain airborne for so long.