2014 Projects of the Year: Private Residence Foundation < 2000 sq.ft.
Private Residence Foundation <2000
Marietta Home
Herbert Construction
Marietta, Georgia
The project award this year for foundations under 2,000 square feet goes to Herbert Construction of Marietta, Ga. for a very complex foundation system that accommodated severe elevation change and complex forming heights for such a relatively small footprint.
Most projects of this size are simple, straightforward foundations. The overall dimensions of the house were merely 39-foot wide by 68-foot-6-inches deep. However, the sloping lot made this a challenging foundation to construct. From the top of wall in the front to the top of footing in the rear, there was 31-feet of vertical change. This drop in elevation in just 62-feet equates to a slope on the site of 2 to 1 (2:1 slope). To make things more difficult, rock was encountered during excavation. This made the construction of the footings more challenging.
“With a multitude of steps in the excavated grade and the steep drop-off of the site, there weren’t many areas to place our form baskets,” stated Doug Herbert, president of Herbert Construction. “When the baskets were placed on level plateaus, they hindered the wall crew from setting the wall forms efficiently. When we stripped the wall forms, many had to be hand-carried up several plateaus to get them back into the form baskets.”
The project totaled only 1,782 square feet with nearly 100 cubic yards of concrete and 3.25 tons of steel. A total of ten different wall heights were required in this complex foundation ranging from 3 feet to 15 feet with four variations in thickness from 8 inches to 14 inches.
“To us, the success on a project like this is found in two critical steps,” stated Herbert. “The first is working with the client and devising a cost-effective way to construct the foundation of interest, producing a CAD plan for all geometries. The second is to consistently layout and check the foundation with robotic total station layout instruments from excavation to final wall plumbing. This was crucial on this project because of the numerous elevation changes. Without these precision instruments, the layout would have taken three men over six hours to layout the footing, and then another five hours to layout the wall. The robotic total stations were more accurate and much faster than convention layout with measuring tapes and string lines.”
For more information on this foundation project, contact CFA Member, Doug Herbert, Herbert Construction Company, at Doug@herbertconstruction.com or (770) 795-0103.
Project Specifications:
- Total Size: 1,782 sq.ft.
- Concrete Used: 73 cu.yd. (walls) 26 cu.yd. (footings)
- Steel Used: 2.5 tons (walls), .75 tons (footings)
- Wall Heights: 10 total, 3 ft. to 15 ft.
- Wall Thickness: 4 total, 8″ to 14″
2014 Projects of the Year: Commercial/ Multi Family
Commercial/Multi-family
Condominium Project
Basement Contractors of Edmond, Oklahoma
Oklahoma City, Oklahoma
Entered by Basement Contractors of Edmond, Okla., this year’s recipient of the Project of the Year for commercial and multi-family projects is a complex and impressive foundation system for condominiums in an urban setting in Oklahoma City.
“The original plan called for a half walk-out basement,” stated Mike Hancock, president of Basement Contractors. “We proposed a full walk-out basement that reduced the project cost by $100,000 from the original design. We then provided full engineering details for making the changes.”
The project consists of more than 9,200 square feet of area and incorporated 360 cubic yards of concrete with 17.5 tons of steel. A variety of wall heights from 2 feet to 10 feet and thicknesses from 12 inches to 22 inches were required.
“The primary reason we proposed this change to the builder,” stated Hancock, “was to give them the advantage of safe rooms for each of the condos located here in the heart of ‘Tornado Alley’. Seven safe rooms were built into the foundation with varying wall thicknesses and odd forming heights of 8 feet 4 inches and 9 feet 8 inches.”
Setting up the forms for the offsets, wall thickness variations and the monolithic “lids” for the safe rooms was the biggest challenge for this contractor. The odd wall heights made the forming module a challenge and incorporated a tremendous number of fillers from their inventory. “This was a much larger scope for us but a better solution for the customer along with the added benefit of safe rooms for their tenants,” stated Hancock.
For more information on this foundation project, contact CFA Member, Mike Hancock, Basement Contractors, at mike@basementcontractorsok.com or (405) 359-0269.
Project Specifications:
- Total size: 9,204 sq.ft.
- Concrete Used: 238 cu.yds. (walls), 122 cu.yds. (footings)
- Steel Used: 14 tons (walls), 3.5 tons (footings)
- Wall Heights: 2′, 3′, 8’4″, 9′, 9’8″, 10′
- Wall Thickness: 12″, 16″, 20″, 22″
2014 Projects of the Year Overall Grand Prize: Private Residence Foundation (2,000 to 5,000 sq.ft.)
Private Residence Foundation 2000-5000 sq.ft.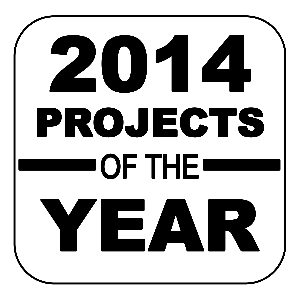
Private Residence
Hottmann Construction Company, Inc
Dane, Wisconsin
This year’s overall grand project was completed by Hottmann Construction Company, Inc. of Dane, Wis. It is also the winning entry in the single-family residence category for 2,000 to 5,000 square foot projects. Peers viewing this project during the World of Concrete display of entries repeatedly noted they thought this foundation for a new home in Madison was that of a swimming pool. A closer look at this project reveals that it is not only a house foundation but part of a strong architectural aesthetic that pays homage to the rich heritage of its historical setting.
The house in essence is a garden wall, representative of the likelihood that 100 years ago, a garden wall could have sat here. As the neighborhood grew and filled in, the homeowner wanted to reimagine how the home played a role in neighborhood history. And, while embracing a progressive architecture style, the home is faithful to the eternal spirit of the site itself.
The architect for the project, Eric Richey of Thomas Phifer and Partners of New York, N.Y., noted that their “desire was to extract the sequential experience of these spaces and ground these spaces independently to the landscape. A byproduct of this decision-making maximized the amount of natural daylight and views into each space of the house. The shape is expressed by the foundation images and defined the spaces much like organic garden walls. Our desire to connect the house to nature and maintain the garden-like quality of the site was well received by the surrounding community.”
The pictures of the curves in this house explain this better than any words. The longest “straight” wall is 15-feet (at the garage doors). The entire project also has a brick ledge around it and the curves prevented the use of a traditional blocking system. The major complexities were the shape, as well as a forming system that consisted of three layers of ¼-inch Luan plywood as the forms. The shape was handled with transferring the plan into a robotics layout system to set the project out on the site. The contractor took a risk with a new forming system, knowing it was likely be the only way to complete the organic curves, consisting of the layered plywood. They had to have confidence that it would withstand the pressures of the concrete being poured into the forms, and not blowout.
The location was another challenge. The house is located in a well-established 100-year-old neighborhood in downtown Madison. The lot size required that the foundation was completed in stages so the excavator could use dirt from digging the next section of the house to backfill the area recently poured.
Project Manager for Hottmann, Mike Thole, stated, “The forming system allowed us to create even flowing curves in the foundation, as well as a plumb wall. We have done several curved wall projects in the past, but most of them had 15 to 20 feet of curved walls at the most.”
The total area of the foundation is 2,938 square feet. Concrete totaled more than 170 cubic yards in the walls and footings with nearly five tons of steel. The challenging walls with brickledge throughout were 5 feet 9 inches and 8 feet 9 inches in height and all were 11 inches in thickness before the ledge reductions.
For more information on this foundation project, contact CFA Member, Ken Kurszewski, Hottmann Construction, at kenk@hottmannconstruction.com or (608) 849-1155. Additional information can also be obtained in an interview with the project team at the CFA’s website at http://bit.ly/1lNS55K.
Project Specifications:
- Total Size: 2,938 sq.ft.
- Concrete Used: 114.5 cu.yds. (walls), 57 cu.yds. (footings)
- Steel Used: 3.03 tons (walls), 1.93 tons (footings)
- Wall Heights: 5’9″ and 8’9″
- Wall Thickness: 11″
Thomas Bradley (Brad) Barnes – (1951-2014)
The CFA loses a strong friend and ally.
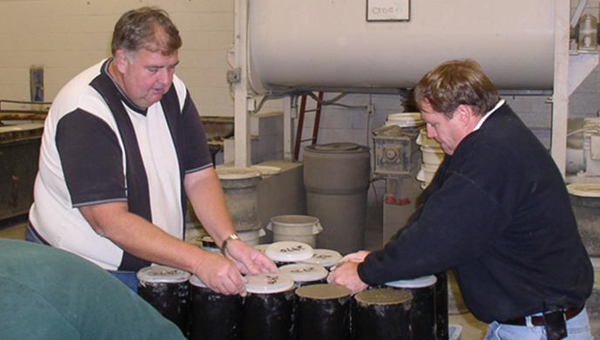
Brad Barnes (left) and CFA Member, Scott Smith of MPW Construction Services (right) hard at work preparing cylinders for Phase I cold weather research at Master Builders Lab in Ohio.
Thomas Bradley (Brad) Barnes, 63, of Medina passed away suddenly, following complications from surgery on Friday, July 4, 2014. He was born May 29, 1951 in Fairmont, W.Va. to Ed and Dean Barnes. Brad graduated from Fairmont Senior High School in 1969 and received a B.S. and Masters Degree in Civil Engineering and MBA from West Virginia University. Brad was the owner of North Central Engineering in Canton, Ohio which is an engineering and consulting firm. He enjoyed golfing, WVU sports, gardening and spending time with his family and friends.
He is survived by his beloved wife, Kathryn (Kitty) Austin Barnes; loving sons, Troy Barnes and wife, Julie of Medina, Ohio and Bryan Barnes and wife, Amy of LaGrange, Ohio; grandsons, Jake and Luke Barnes and Michael and Andrew Lade of Medina; sister, Rutha (Ruthie) Barnes of Fairmont, W.Va.; mother-in-law, Bonnie Austin of Thornton, W.Va.; brothers-in-law, Danny Austin, Marty and Marie Austin, and Terry and Michelle Austin; and many aunts, uncles, nieces and nephews. He was preceded in death by his parents, Ed and Dean Barnes and father-in-law, Neil Austin.
Friends and family may call on Wednesday, July 9, 2014 from 1-8 p.m. at Waite & Son Funeral Home, 3300 Center Road, Brunswick 44212. Services will take place at 8 p.m. on Wednesday at the funeral home. A memorial service and interment will take place in West Virginia at a later date. Contributions may be made in Brad’s memory to the Granger Fire Department, 3737 Ridge Road, Medina, OH 44256. Online condolences may be left at www.waitefuneralhome.com, Waite & Son, 330-225-1770
– See more at: http://www.legacy.com/obituaries/cantonrep/obituary.aspx?pid=171623537#sthash.eXx0sWd8.dpuf
A CFA Legacy
Brad was an instrumental part of the leadership team that developed and delivered cold weather research for residential cast-in-place foundation walls. This research began in 2001 and concluded with the 75 page report published in 2004. Since then, this report has revolutionized the approach contractors, ready mix producers and building inspectors take toward constructing concrete foundations in northern climates during the fall and winter months. This research has also had a shaping influence on the modern version of ACI 306 and is a foundational element to the ACI/CFA Residential Foundation Technician Certification.
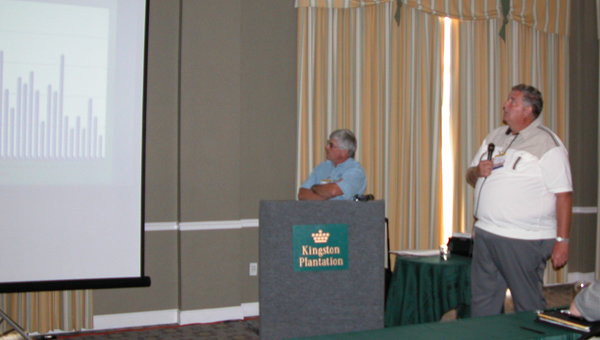
Brad Barnes and former CFA Member, Terry Lavy of Lavy Concrete (left) present the preliminary findings of the cold weather research during the CFA Annual Convention in Myrtle Beach, SC (2003).
“It is hard to imagine the success of one of this industry’s most defining contributions without Brad’s leadership and professionalism,” states Jim Baty, Managing Director for the CFA. “Exemplary in all aspects of his participation and leadership of the research team, Brad contributed a tireless effort for the good of an entire industry.”
Barnes was honored in 2004 by the Concrete Foundations Association with the inaugural offering of the MVP Award, for his contributions to the Cold Weather Research effort. He went on to conduct many seminars for the CFA and Ohio Concrete to promote the benefits of the research. Many contractors throughout the Association benefitted from one-on-one communication with him to develop a core approach to cold and frozen weather conditions. Barnes also participated with contractors as far as Alaska, meeting with code departments and discussing the parameters of cold weather performance to establish more effective and reasonable guidelines for such work.
“Brad played such a great part in the cold weather testing,” stated CFA Member, Sean Smith of MPW Construction Services. “Which all of us, at least us northerners, benefited so greatly.”
Barnes and North Central Engineering, the firm he started and managed, was a member of the CFA from 2002 to 2009.
Monarch Materials Group to Release New Product Catalog
ADEL, IOWA – June 24, 2014 – Monarch Materials Group, Inc. (www.monmatgrp.com), the premier window system supplier to the homebuilding and remodeling industry, is releasing the New Monarch Product Catalog. Monarch is the leader in producing high quality, specially engineered solutions for below grade basement applications.
Monarch provides a full-line of products for basement window systems, egress access and ventilation. In response to the growing market, the New Monarch Catalog will feature increased product offerings such as:
- Knock Down Steel Frames – Developed to reduce shipping costs and storage needed for steel frames. These frames are engineered for strength and have the tightest fit in the industry. They are also easy to assemble using unique Snap Lock Tabs.
- Sandalwood finished products – In a variety of product categories including windows, wells, covers, grates and ladders.
- Egress Package Builder – Created to make sourcing and matching products easy. The most frequently ordered sizes and combinations are itemized. Bucko Packages are also included.
The new catalog is produced in an easy-to-use format for researching products, coordinating window systems and placing orders. The 2014 Catalog features new sections for remodeling, repair products and custom windows, wells, covers and ladders.
# # #
About Monarch Materials Group, Inc.
Established in 1960, Monarch Materials Group, Inc. provides superior quality basement window systems to the residential home building and remodeling industry. Monarch is known as the national leader in quality manufacturing, innovative products and specially engineered egress solutions. Monarch operates its headquarters in Adel, Iowa and has an additional distribution location in Englewood, Colorado.
For the nearest distributor of Monarch products and more information, visit www.monmatgrp.com or call 800-343-9370.
Contact:
Steve Privitera, President
Monarch Materials Group, Inc.
515-993-4651
sprivitera@monmatgrp.com
A New American National Standard For Material Placement Safety
RESPONSIBILITIES FOR ALL PERSONNEL ON A CONCRETE POUR ARE NOW SPECIFIED IN ASME B30-2014
The American National Standard for material placement system safety is ASME B30.27. (Material placement systems are concrete pumps and concrete conveyors.)
ASME has released B30.27-2014. It is currently available as an electronic download and as a printed booklet. The date of issuance was March 26, 2014. It becomes effective one year after the date of issuance.
The major changes in B30.27-2014 versus the 2009 edition are the addition of translation requirements for companies importing equipment into the United States from other countries, and the addition of responsibilities for all personnel when a material placement system is used on a concrete pour, from the general contractor to the concrete mixer truck driver and everybody in between.
The responsibilities section was adapted for use in B30.27 from the B30.5-2011 (mobile cranes) standard, which has been in effect since January 2012. The reason for the responsibility delineation is to give everyone involved in a concrete pour the knowledge needed to complete the pour safely. If specialized training is required, it is shown. Expectations of setup locations are spelled out. What an operator should know, and the items a contractor should consider when ordering a machine are listed. The only way everyone can go home safely after the pour is if everyone knows their piece of the safety puzzle and works to accomplish it.
ASME B30.27-2014 contains information that should be of interest to everyone involved with concrete pumping or concrete conveying. It is advisable to obtain a copy and implement any changes necessary to ensure compliance with the specifications. It is assumed that the specifications will be used by regulatory (OSHA) and legal entities (attorneys) as a benchmark against which the players on a concrete pour will be judged.
B30.27 is republished on a five-year cycle. The 2009 version of B30.27 became active in June, 2010 and will be in effect until March 26, 2015. The 2014 version will remain in effect until one year after the next revision is published.
Copies can be obtained from the American Society of Mechanical Engineers (ASME). Go to http://www.asme.org/ use the ‘codes and standards’ link; then enter B30.27 into the ‘keywords’ field. The standard is also available from Global and other standards retailers. Because of severe restrictions placed on the .pdf version (one user, no printing), I recommend the paper version.
Questions or requests for interpretation regarding the ASME standard should be addressed to: Secretary of the B30 committee, ASME, Three Park Avenue, New York, NY 10016-5990.
Management Corner: Drug and Alcohol Testing Clearinghouse Comments
CFA MEMBER, FOLEY CARRIER SERVICES HAS SUBMITTED COMMENTS TO THE FEDERAL MOTOR CARRIER SAFETY ADMINISTRATION REGARDING THE PROPOSED DRUG AND ALCOHOL TESTING CLEARINGHOUSE.
While there was a lot to like about the rules, they feel that FMCSA needs to make some practical changes before they are ready. This update is republished from their Fast-FaxTM to keep you better informed. Contact Ryan Fagan, liaison to the CFA and Senior Compliance Specialist, at 860-815-0735 or Ryan.Fagan@Foleyservices.com for more information. Matt Wrobel will be presenting at the CFA Annual Convention in Sandusky, Ohio this summer.
As we reported in February, the Federal Motor Carrier Safety Administration has unveiled its long-awaited proposal for a Drug and Alcohol Testing Clearinghouse. This week, Foley Carrier Services submitted comments to FMCSA regarding the proposal and made some recommendations to help improve it based on our two decades of experience in this industry.
In general, we feel that carriers should welcome the clearinghouse. The broad idea is a very good one and will help streamline the hiring process and protect carriers against litigation. Looking at a driver’s safety history is routine after an accident. Even if drugs or alcohol played no part in the crash, if a driver had an incident in his history, its a safe bet that the carrier will be explaining to a jury why they hired the individual. Anything that helps carriers avoid that is a good move.
On the other hand, we strongly feel that regulations should not be overly burdensome to companies nor should they make compliance more difficult. Some of the regulations proposed, we felt, would have an unintended but highly disruptive effect on both drug and alcohol testing and hiring new drivers.
It is important to remember that these rules are in a very early stage. We have included highlights of our comments below and you can read the full document here: http://goo.gl/Ok49jl.
BACKGROUND CHECKS
We believe the burden of paperwork could become overwhelming and costly for Motor Carriers. We believe that drivers should sign a consent form for the initial and annual checks as a one-time action at the start of employment and that that consent should last for the life of employment. This system is already in place for Motor Vehicle Reports and FCRA covered checks. In the interest of safety and security we believe that the annual check should be a complete, detailed check. We would also like to expedite the process through the acceptance of electronic signatures on the required documents.
Finally, we believe that performing Clearinghouse checks should be opened up to third-party background check providers. These businesses often act as agents on behalf of Third- Party Administrators. We believe that FMCSA should make performing these checks as effortless as possible, including assigning duties to an agent for employers considering the enormous safety-improvement potential they hold.
CUSTODY AND CONTROL FORM
We have very serious concerns regarding the proposed usage of the Federal Custody and Control Form. Our experience with the requirement for listing DOT mode on the CCF tells us that relying on Collection Sites and drivers to comply is problematic and could result in incorrect, incomplete forms. Factoring in the lack of a dedicated field for this information, we predict disaster. Since the MRO is the last role in the chain of custody, uncorrected errors on forms would become an unintended burden for MROs. In this case, given the amount of information that FMCSA is requiring that does not have a prompt or instruction on the CCF, we believe that missing and incorrect information will become endemic.
Given that the likelihood of a significant number of donors failing to disclose the correct information is high, we would like clarification regarding procedure when information is missing or incorrect. Is it a correctable flaw as in the DOT Mode requirement? Would it be considered a fatal flaw given how disruptive the missing information would be to the Clearinghouse and to future background checks?
Furthermore, we are concerned that FMCSA would be proposing changes to the usage of the CCF without the partnership of the Office of Drug and Alcohol Policy and Compliance and the Department of Health and Human Services. We believe that any change to the usage of the CCF should come with changes to Part 40 and to the form itself.
The Social Age Evolutionary Workplace
…VERY LITTLE HAS CHANGED IN HOW WE HIRE AND MANAGE STAFF – WHICH HAS LED TO LOW EMPLOYEE ENGAGEMENT AND PRODUCTIVITY AND HIGH EMPLOYEE TURNOVER….WE MUST EVOLVE OUR BUSINESS PRACTICES…
by Kim Seeling Smith
The war for talent is over and talent has won. Technology and globalization have dramatically changed the way we work over the last 20 – 30 years. However, very little has changed in how we hire and manage staff – which has led to low employee engagement and productivity and high employee turnover.
Instead of doing the routine, tactical and predicable work of yesteryear, the Social Age requires us to be more strategic, creative and innovative – more solutions oriented. Yet, for the most part we are still hiring for skills and experience and using the same levers we have used for decades (if not centuries) to motivate and manage staff.
We must evolve our business practices to remain competitive in our digitally connected, globally oriented economy.
With any evolutionary process, a guide or roadmap proves invaluable. When your company decides to take the leap and join the Social Age, there are 5 C’s to adhere to so you can maximize employment efficiency and effectiveness, retain your staff and
ensure that your employees are fullyengaged
on a daily basis.
CORRECT HIRING
We must start this evolution with hiring the right people – without them, efforts to engage and retain staff become moot. The Industrial Age paradigm emphasized hiring for skills and experience. But skills can be taught and in today’s rapidly changing world, experience is far less important than agility and the ability to learn and adapt.
To not only survive, but thrive in the Social Age, companies need to hire for both culture fit and competencies – those innate abilities that can’t be taught but will make them successful in the job. Proper interviewing technique is essential to guaranteeing you get the right hire. Unlike the stock market, when it comes to potential job candidates, past performance is indicative of future results. The majority of interview questions have to be answered with past examples of how the candidate actually dealt with real-world scenarios.
Do not fall into the old trap of believing what a candidate would do is what they did do, or more importantly, will do.
CLASSIFY AND MANAGE APPROPRIATELY
Even when you do everything right during the hiring process, you may still be surprised once the employee comes on board. Team dynamics or changing personal circumstances can affect individual behavior and performance. You must continually keep your finger on the pulse of your staff – a daunting task to many managers who either try to devote equal time and energy across the board – or who spend time with the wrong people.
Employees typically come in three ‘flavors’: Critical People, Squeaky Wheels and the Fat Middle. Most managers end up spending most of their time trying to grease their Squeaky Wheels, which perpetuates poor performance or behavior. Counterintuitively, by devoting the majority of your attention to your Critical People, you will bolster the productivity of the whole team. Squeaky Wheels? Train, motivate or move them on. Quickly.
COMPENSATE FAIRLY
Many companies diligently strive to create attractive incentive programs in an effort to engage and retain staff. Unfortunately, these efforts actually may be counterproductive to accomplishing these goals.
Studies have suggested that rewards can narrow our focus, innovation, creativity, strategic thinking and problem solving – the very things needed from a Social Age Workforce. Higher pay does not necessarily equal higher productivity. Managers should set their salary benchmark at or a little above market rate for individual functions. Even more importantly, managers should ensure that employees feel they are being adequately compensated for the work they do, and this can only be accomplished by speaking to them directly.
CURRENCIES OF CHOICE
Once your staff feels well paid, real productivity and engagement can be unlocked by tapping into your their internal motivators or Currencies of Choice. What your staff really needs to be fulfilled and to ‘go the extra mile’ is to:
• Work for someone they trust and respect in a company they support • Be appreciated and have their voice and opinions respected • Have a firm career path that allows them to grow and develop • Realize their underlying motivators • Be able to do what they do best every dayBy understanding and acknowledging your team’s individual Currencies of Choice, you can help to keep them engaged and decrease turnover.
How do you recognize which Currencies of Choice will motivate your staff? By talking to them. Unfortunately, many managers don’t talk to their staff enough, don’t know what to talk about, or how to structure their conversations.
COMMUNICATE WITH FOCUS
FOCUS is an acronym that describes the best practices in leadership communication. Communication between staff and managers should revolve around:
• Feedback: Ensure your team is updated on company information, initiatives and new hires. Give praise when it is due, and maintain an open door for their questions, concerns or comments.
• Objectives: The heart of sterling performance management is structuring specific and measurable job objectives and holding staff accountable for achieving them.
• Career Development: Many studies list career development as a main factor that employees gauge to determine whether to stay with their current employer or seek a new position elsewhere.
• Underlying Motivators: What does your staff need to go the extra mile, and how do they respond to motivational techniques and rewards?
• Strengths: According to The Gallup Organization, those innate abilities that make them unique and good at what they do is the #1 predictor of success.
The process of changing the way you hire and manage your staff may appear daunting at first, but experience shows that by taking it step-by-step, you can make significant changes quickly. The result will be a lifetime of more engaged, happier and more productive staff, as well as more free time, less stress and higher job satisfaction for yourself and your team.
Are you up for the challenge?
ABOUT THE AUTHOR
Kim Seeling Smith is an international human resources expert and author of the forthcoming book, Mind Reading for Managers: 5 FOCUSed Conversations for Greater Employee Engagement and Productivity. With her expansive knowledge of human capital practices in today’s market, Kim helps companies build healthy work environments and increase employee engagement and productivity in our digitally connected, globally oriented world. For more information on Kim Seeling Smith, please visit http://igniteglobal.com.
Management Corner: 10 Steps to Reduce Employment Related Risk
ATTEND CFA CONVENTION IN SANDUSKY, OHIO FOR MORE FROM DAVID WHITLOCK ABOUT EMPLOYER ISSUES
As we are now about halfway through 2014, it is a perfect time to take the temperature of your employment compliance. There are a number of important changes in the law as well as compliance matters that you need to stay on top of. Here is a summary of the major ones.
FIRST, it is important to note that the Equal Employment Opportunity Commission (EEOC) has stepped up enforcement in several areas. These include age and disability discrimination, especially. In part this is because the baby boomer generation is reaching or passing retirement age, and in part this is because older workers are more prone to injury or disease. Because of the often strenuous nature of work in the concrete industry, employers must be especially careful when dealing with injury or disability issues.
The EEOC is also stepping up enforcement with respect to the Genetic Information Non-discrimination Act (GINA). The statute requires employers to avoid making employment-related decisions based upon genetic characteristics. Because this is a relatively new statute, EEOC is more aggressively enforcing claims against employers to create law and make employers better aware.
EEOC is also using litigation to regulate how employers are using criminal background checks. In essence, EEOC takes the position that you cannot use criminal background as the basis for not hiring someone unless you can demonstrate a clear correlation between the job and the crime. EEOC takes the position that an employer relying upon a criminal background check needs to demonstrate an individualized analysis of the relationship between a prior criminal record and the job requirement of the applicant or employee. The individual analysis may require employers to give the employee or applicant an opportunity to explain negative information in a background report. Note that you should never rely upon arrest information alone. EEOC takes the position that arrest records are meaningless and should never be relied upon.
SECOND, don’t ignore the elephant in the room – the Affordable Care Act (a/k/a Obamacare). Although the IRS announced that employers will not pay a penalty for failure to provide minimum essential coverage that is affordable and meets minimum value until January 1, 2015, the law specifically states that employers need to implement that coverage by January 1, 2014. This provision applies to “large” employers which is defined to mean employers with at least 50 full-time (FTE) and full-time-equivalent employees (FTEE). Remember that the ACA counts anyone who works 30 hours per week as a FTE. To determine how many equivalents you have, add up all the hours worked by non-FTEs and divide the total by 120. The whole number remainder is the number of FTEEs. If that, plus the FTEs, exceeds 50, you’re considered “large.”.
Now make the “pay or play” decision: Are you going to providing healthcare coverage that meets the law’s requirements (“play”), or are you going to “pay” the penalty for not doing so? If you haven’t already talked to your broker to obtain rates on your health insurance coverage, you need to do so ASAP. This is necessary so that you can decide which option makes the most business sense. Remember also that you only pay a penalty for not offering coverage to FTEs; this is why some employers are looking at ways to reduce the “pay” cost by outsourcing functions, using staffing companies, and reducing hours. Some companies in the concrete world are finding that reducing hours also decreases injuries and worker comp exposure (and costs), improves safety performance, and eliminates overtime costs.
THIRD, if you are a federal contractor or subcontractor you may run into the new affirmative action requirements in 2014. New requirements regarding utilization of disabled and Vietnam-era veterans are now in place. In essence, the Office of Federal Contract Compliance Programs (OFCCP) now requires that you strive to reach 7% utilization of these categories. The new rules also create a lot of paperwork and reporting obligations. You will certainly want to review your affirmative action plan to ensure that you are in compliance with these new rules.
FOURTH, the misclassification issue is still an active (and expensive) problem. Tax collectors at the state and federal level are looking for income they missed during the economic downturn. That comes from finding employers who have been treating workers as independent contractors — rather than employees — in order to avoid paying withholding, Social Security, Medicare, worker comp, etc. Today, states are much more aggressively auditing employer payrolls and practices. The concrete industry is especially vulnerable because government agencies believe that use of “1099” labor is rampant, particularly among smaller employers. Of more concern is the fact that at least 17 states have entered into arrangements with the federal government to share information. This means that if you are audited at either the state or federal level and found to have misclassified workers, the other level will soon be knocking on your door – effectively, a double whammy! Make certain that you are correctly classifying your workers. The bottom line is that if you tell the worker what to do and how to do it, then that worker is more than likely an employee rather than an independent contractor.
FIFTH, misclassification problems can also lead to wage or claims, but such wage claims can also arise independently. A growing number of plaintiff’s attorneys are willing to bring wage and hour claims against employers who do not correctly pay overtime, and typically, if an improper overtime pay practice is discovered, the claim quickly becomes a class/collective lawsuit. The claim nearly always asserts that the pay practice is deliberate and intentional as that leads to double damages plus attorney fees. The most common wage and hour complaints involve improper payment of overtime, working off the clock, automatic deduction for meal periods, and working before or after clocking in or out. The best advice for all employers is to make sure that your time records are very accurate and that employers must make you aware of any effort to work outside of normal “clocked” hours.
SIXTH, the National Labor Relations Board continues to attempt to regulate nonunion employers that the Board claims are interfering with employees’ Section 7 rights under the National Labor Relations Act. In essence, Section 7 of the Act protects employees engaging in protected, concerted activities for their mutual aid in connection with organizing or representation by a collective-bargaining agent. “Protected” conduct/activity relates to terms and conditions of employment. “Concerted” activities are undertaken by or in behalf of someone other than an individual. Thus, the Board seeks to prevent employers from limiting or stepping on employee communications or actions that have anything to do with terms or conditions of employment. The Board’s regulation extends to handbook policies, social media policies, and even “at will” language.
In recent decisions, the Board has taken the position that an employer cannot require employees to keep confidential information related to an ongoing investigation. In addition, the Board maintains that an employer cannot instruct employees not to discuss their compensation or bonuses. The Board also takes the position that employers cannot regulate what employees do with their personal social media. The bottom line is that concrete industry employers need to periodically review and update their employment policies and/or employee handbook.
SEVENTH, plaintiff’s attorneys are routinely investigating whether persons involved in vehicle accidents were using cell phones or texting while driving. Every concrete employer needs to have an absolute zero-tolerance policy in place that strictly forbids the use of any communications device while driving. This is especially the case with respect to employees driving company equipment, but should also apply when employees use their own vehicles on company business or when driving to and from work or a job site.
EIGHTH, prudent employers will put into place a properly drafted drug and alcohol policy. Think of it this way: if you do not have a good policy, guess who is going to apply for work at your place of business. Given the physical and demanding nature of work in the concrete industry, can you really afford the risk of having someone on your job site whose impaired in any fashion? If you have not had your policy reviewed recently, now’s a good time to bring it up to date.
NINTH, even if you do not have an employee handbook, consider putting in place an arbitration provision that prevents employment related disputes from being resolved in court. As you are probably aware, the litigation process is time-consuming and expensive. Arbitration, however, provides a less expensive, faster, and often more sympathetic forum for resolving employee complaints. These are state specific agreements and are easier to enforce in some states rather than others. If you cannot impose an arbitration agreement, consider at least a jury waiver provision so that if you wind up in court, the matter is tried before the judge only. This helps avoid the runaway jury verdict.
FINALLY, be aware that there are other things happening out there: OSHA is issuing new regulations making life more difficult for concrete industry employers. . . Immigration reform remains an uncertainty while enforcement continues. . . Restrictive covenants can still help you. . .
You still don’t want to hire LUZIRS (Lazy, Undisciplined, Zer0-interest, Irresponsible, Rude, Slackers) . . . and above all – Stay Alert. Why? Because Lerts live longer!!!
MOVING UP, MOVING FORWARD
NEW MEMBERS | NEW BENEFITS | STRONG FOUNDATIONS
This is an exciting time for the Concrete Foundations Association. Many of you are part of that energy and excitement and many of you are benefitting from it. At no time in the last decade has membership been growing as fast as it is right now and this is a result of old acquaintances returning as well as new relationships being made.
If you are part of our receiving list of notifications, you’ve no doubt seen the recent stream of announcements that provide evidence to a part of this energy. These announcements not only proclaim the energy of new involvement, they are opportunities for networking. Each company that is identified through this effort is a networking partner potential for you.
As a contractor, these companies can be someone you consider pulling along side of and mentoring, introducing them to your company and CFA membership through your communication. We’ve heard time and time again that the best and most dramatic influence on your own company is starting the conversation with another and learning as much (or more) from them as you perhaps intended to provide. Therefore, we continue to produce these announcements as a way of spurring each of you into this conversation and letting you take it where it leads.
As companies begin to investigate the decision to join the CFA, one of the first questions is often “what do we get for joining,” or in essence, “what’s in it for me?” This is a very important question.
Never before has our industry endured such hardships as the recession you are climbing out of. Never before have finances been stretched so far or scrutiny on spending been so great. This has honed the skills of company management at maximizing the effectiveness and efficiency for every dollar spent so as to garner every possible dollar earned. The equation is not simple, nor is it easy. This is where the CFA has been specifically focused of recent months. We’re pleased to be introducing to the market and to each of your organizations that join or renew, a new start to membership in our Member Resources Welcome Kit.
The Welcome Kit, while containing just a start of the concepts and programs that make the CFA such a strong network and opportunity for you, does provide tangible and immediate information you can implement as a difference maker. While extensive in its diverse application to your business, we do believe that strategically and over time, this information will challenge you and your company to think of process and procedure, program and performance as you begin to consider how this professional association can and should impact your business. It is for this reason that you’ve been encouraged to join.
The Welcome Kit is broken into major sections to relate to your business modules. Some of these sections represent major programming the CFA has developed or is in the process of developing. Other sections represent key information and relevant resources specific to your business and industry. Each kit currently contains:
• CFA Certification Program • CFA Fall Protection Program • CFA Technical Notes • CFA Management Moves Business Tools • CFA Convenient Networking Engagement • Insurance Captive for CFA Members • Concrete Facts MagazineFound throughout these pieces of information are the broadest range of member benefits that have ever been issued from the CFA to the membership and are a direct result of the countless hours of service already volunteered by leaders from companies like yours. They are a collection of assets that cannot be overlooked in the value of participation and membership in an organization such as this.
The Welcome Kit has also been upgraded to help you make a more professional statement of your membership to customers and visitors entering your office. The new and strong CFA branding is presented in a modern and attractive way for you to set on a counter or hang on the wall. We encourage you to place the CFA among the leading icons you hold up to the industry, as it becomes a centerpiece of support and growth for your company. The display of this membership acknowledgement can and should coincide with establishing the CFA brand as part of your digital presence.
Through new members and new information, the CFA recognizes the growth and energy that is presently in the marketplace. More than ever before, companies want and need the partnership that comes from a solid and strong organization; one that offers solutions, resources, information and opportunities, as they are needed. It is therefore important to recognize that such firmness and strength comes only from legacy and consistency. The Concrete Foundations Association begins the celebration this summer of 40 years in existence. Consider what the past forty years means to you…where were you then, or were you then? I was just learning to run and broadening my vocabulary attending preschool. Leaders in your industry were taking time away from their businesses, for your business. They were thinking of you today as they gave of themselves then. From the minutes of the 2nd formation meeting on February 10, 1975 in Chicago, Illinois:
THE MEANINGFUL ASPECT OF THE CONVERSATION FOR REASONS FOR A POURED WALL ASSOCIATION TURNED OUT TO BE NOT SO MUCH AS THE REASONS FOR AN ASSOCIATION BUT THAT WHEN WE ARE ORGANIZED WE DO WHAT WE SAY WE ARE GOING TO DO! ALL IN ATTENDANCE AGREED ON THIS POINT SO THAT WE MAKE FUTURE MEETINGS PURPOSEFUL FOR THE MEMBERSHIP!
This statement in those minutes is written just as it was in the minutes, bold and all caps, while the rest was normal text. The founding members of this Association held firmly to one belief. The only reason an association, this Association, should exist was to provide for the needs of you, the industry and specifically the membership.
Twenty-one reasons were listed in those minutes, referred to in the quote above, as specific and individual industry needs or influences. Listing them below, see how many of them describe today’s CFA and what has been accomplished over the 40 years of purposed and diligent existence. An Association can:
1. prepare, print and distribute literature to all its members which points out the advantages of poured concrete walls over masonry block
2. contact testing laboratories for the purposes of securing actual test information comparing poured concrete walls with block as to strength, dampness, insulation, etc.
3. set up standards of performance regarding the quality of the work of its members…all with the idea of upgrading the industry
4. assist its membership in the exchange of ideas thru conversation at its meetings, newsletters, etc.
5. assist members in defining and/or changing local building codes
6. seek federal assistance in supporting apprenticeship training programs
7. send out periodic newsletter with such information as new ideas, interesting jobs, laws affecting the industry, new literature and products, OSHA information, union practices, etc.
8. prepare, publish and circulate its own magazine
9. investigate the availability and cost of hospitalization and pension programs
10. set up training programs for inexperienced field people…possibly having such people work for a time with experienced, efficient member operations
11. prepare training kits with manuals, slides, etc.
12. prepare training kits for office staff so as to acquaint them with what goes on in the field…all with the idea of making the entire company a more knowledgeable and closer coordinated work force
13. pursue the concept of collective buying power and its benefits
14. provide its members with aids and suggestions as to how to evaluate costs and investment in terms of profits
15. provide, thru its membership, an exchange of credit information on builders coming into a work area from the outside
16. provide and develop motivation ideas for the employees of a members’ company
17. provide its members with legal aid and assistance
18. approach other organizations such as OSHA, FHA, NRMCA, NAHB as a spokesman with power on matters pro and con affecting the poured wall contractor’s interests
19. help create a market by promoting “POURED CONCRETE WALLS MAKE THE BEST BASEMENTS!” with ads, mats available to members for local advertising, car/truck bumper stickers, etc.
20. prepare and distribute educational data to technical schools, universities, architects, etc. providing that poured walls are an economic factor and under what conditions are superior to masonry construction
21. produce a traveling exhibit for the purpose of promoting poured concrete walls at national and/or state level home builders, ready-mix, concrete shows, etc.
While there is certainly evidence of concepts and focal points that were plausible only forty years ago, there is tremendous evidence of the road map this generated list created for the Association that you have and own today.
So who were the pioneers that laid this path and established leadership that would persevere, even excel today? That question should be expanded to ask, who are the companies that have held strong the support for this industry and this Association since its inception. Together, they are the strong foundation for who the Concrete Foundation Association is and with great satisfaction, we are able to continue encouraging companies to join and benefit today.