National Associates Take a Bow!!
The Concrete Foundations Association is made up primarily of contractor members, but one group of members who constantly step to the plate to add value to the Association are our National Associate members. Without them, all of our events would be more expensive and less informative; our magazine would be much smaller and black and white (remember what it looked like 10 years ago); and, life would be much harder for the CFA staff.
There has been a steady succession of associate members serving on the Board since I became involved in 1992 and each one of them takes their involvement seriously. They staff and chair committees; they serve as resources and referrals for questions and problems brought to our attention by members and non-members alike; and, they regularly contribute to our financial stability through advertisements in the newsletter, exhibiting, and sponsorships at our winter and summer meetings. They also provide expertise and content for stories, seminars, and a host of other needs of the membership.
This summer’s meeting is no exception. The Kalahari Resort in Wisconsin Dells is close to several of our national associate members and they are rolling out the welcome mat. We anticipate at least 35 of our national associates to exhibit this summer. If things come together, we will have not only outdoor exhibits but some outdoor demonstrations as well.
It could be argued that venues such as our summer meeting are weak when compared with the World of Concrete and other large trade shows, but the focus and intimacy of our summer meetings is something you can not get at the large trade shows.
There are benefits to our relatively small group for both the associates and the contractors. For the associates, they get feedback on new products from a select group of the best and most innovative contractors in the country. They also solidify and build on relationships that have been initiated on more formal terms.
The contractors, on the other hand, can get to know the company sales force and products without the distractions of Las Vegas or Orlando, competing seminars, or the need to see 250 other exhibitors before the end of the day. They can ask, and the sales people answer questions that simply take too much time at the larger venues.
There are also plenty of opportunities to interact with associates as well as other contractors at our social events. Some great deals have been “cemented” on the golf course. Of course, a few others have been brought into question after a Karaoke performance.
The summer meeting is built around families, which is appropriate given the number of our members who operate family businesses. If you haven’t made your reservations yet for this summer’s meeting, now is the time to do so. Otherwise you will miss a great opportunity.
Ed Sauter, Executive Director, CFA esauter@cfawalls.orgTech Talk: Footing Discontinuities According to Code
As Published by Concrete Homes Magazine (May-2006)
by James Baty, CFA
Editor’s Note: As part of our partnership with the Concrete Foundations Association (CFA), the following article is the second in a series on residential construction codes. For more information, visit cfawalls.org or call (319) 895-6940.
Codes are developed to provide assurance that structures are designed and constructed to withstand the test of time, not only for life safety but also for long-term durability. Yet codes can also be so complex that implementation causes struggles that delay, or worse yet, halt work. Residential construction is no different than any other construction market today. Recognizing this, the American Concrete Institute created a committee specific to the residential industry (332-Residential Concrete) to create guides and standards that help shape the quality and efficiency of this market. Nearly 20 years after the formation of this committee, the first ACI Residential Concrete Code has been published. Over the coming months, this article will digest some of the more substantive areas altering or improving the requirements for residential concrete as the industry prepares to shift from design and construction by ACI 318, chapter 22 to ACI 332.
The ACI 332 Standard, developed by this committee, provides the minimum cast-in-place design and construction requirements for one- and two-family dwellings and their accessory structures. The current version of the code (332-04) specifically addresses those requirements for concrete footings (wall, thickened slab and isolated), basement or foundation walls constructed only with removable forms and slabs-on-ground. Other elements and methods for residential construction do exist but are beyond the scope of this current document. Those not included remain under the provisions of ACI 318 and other code references.
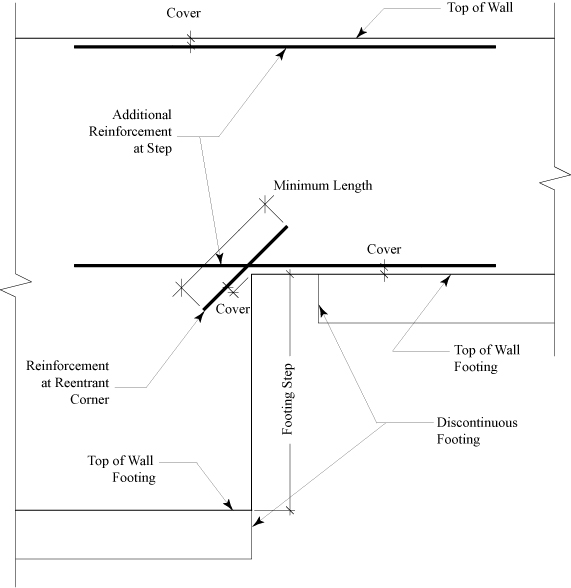
Figure 1 – Foundation wall spanning the horizontal discontinuity in the footing
There are many aspects of current construction that all too often are not easily supported or referenced in a general building code. One example is the design of footings and foundations at extreme changes in elevation, such as the step from a basement foundation to a garage wall. This design requirement also exists where a building lot falls rapidly from front to back, requiring the foundation wall to step at varying intervals. Still other conditions exist where the design must account for footings spanning trenches or poor soil conditions. ACI 332 has developed guidelines for these conditions, supporting the current practices that are followed in the field with sound design guidelines.
Designing for footing discontinuity
Fundamentally, the footings transition the load from the house and the foundation walls to the sub-grade. The foundation walls provide the vertical transfer and support the lateral pressure applied by the earth. However, where significant changes in elevation occur, an area exists in the excavation where a continuous footing is not practical or effective. This transition is considered a discontinuity in the footing design and the foundation wall must be engineered to perform as a beam spanning from the end of the footing above to the beginning of the footing below. ACI 332 states:
Where a wall footing is discontinuous due to an abrupt elevation change, the maximum horizontal discontinuity of the wall footing shall be 4 feet.
The code recognizes that there are areas requiring abrupt elevation changes in the foundation. Referred to as steps, these areas are typically experienced in walk-out basements, at significant changes in the grade, and in the transitions to garage foundations. An example of this condition is seen in Figure 1.
The condition created by a footing discontinuity is limited in ACI 332 to a maximum dimension for the discontinuity (distance between the footing ends) of 4 feet. This condition also requires the following:
At discontinuous wall footings, where wall footing elevation change is greater than twice the footing thickness, place a minimum of two No. 4 horizontal reinforcing bars, one at the top and the other at the bottom of the wall, in addition to other required wall reinforcement. These bars shall extend at each end at least 36 inches into the wall portion supported directly by the top and bottom wall footings. The bars shall be placed in the middle third of the wall thickness.
By providing the reinforcement as stated above, the foundation wall spanning the footing discontinuity transfers the vertical load within that span to the areas of the wall directly over the two footing sections as a structural beam. The footings then transfer the combined loads to the sub-grade.
Designing for unsupported footing conditions
There are also conditions encountered from time to time on jobsites where the footing must span a trench or a soil condition that is less stable than the rest of the sub-grade. ACI 332 addresses these conditions with a variety of requirements. An unsupported footing is considered any distance where the load transfer of the footing cannot be maintained at the same pressure condition of the assumed sub-grade. These are most commonly found around water or sanitary pipes, power trenches or areas where poor soil compaction settles below the surface of the surrounding sub-grade. In general, good practice suggests that any backfill should be compacted by tamping to the level of the bottom surface of the footings and the top level of the surrounding sub-grade. This will obtain adequate bearing and minimize the likelihood of detrimental settlement.
However, there are conditions where this is not appropriate or possible. For these conditions, the footing must be considered a structural beam and designed to span the sub-grade condition. ACI 332 requires that:
Where an unsupported wall footing section does not exceed a 3-foot span, a minimum of two No. 4 reinforcement bars shall be placed in the bottom of the footing and extend at least 18 inches into the supported sections on both sides. Reinforcement bars shall have a minimum cover of 3 inches from the sides and bottom of the footing.
In other words, reinforcement (or additional reinforcement) is added to the footing at this condition. It must extend a minimum of 18 inches beyond the edge of the points where the sub-grade is considered to be insufficient for continuous support equal to that of the prepared sub-grade. Also, it is important to note that this design can only be used for a maximum span of 3 feet. Beyond this distance, the affected sub-grade must be engineered to the condition surrounding it.
Finally, ACI 332 provides that for areas where the soil under the intended footing has been removed by trenching or other methods, the void must be backfilled. Although it may not have to be compacted as stated above, the backfilling is important to prevent the adjacent sides of the trench or opening from becoming more unstable, extending the distance of the unsupported condition.
Together in ACI 332, design professionals and industry experts have combined efforts to improve the rationalization and the construction of residential footings in response to the market growth and constant pursuit of the mantra “bigger, better, faster and more economy.”
Contact Jim Baty, Technical Director, (319) 895-6940 or jbaty@cfawalls.org
LET’S TALK ABOUT CHANGING YOUR BUSINESS CFA Spring Meeting Triumphs in Indy
There are many reasons why a foundation contracting company might look to the CFA for potential interest. On the surface, the Association has been providing access to some of the highest quality equipment and products for thirty years. However, time and time again, it is the individuals that make the commitment to get to an event that will express just how influential CFA meetings are to their business.
This year’s spring meeting has come and gone and certainly did not disappoint those making the trip. Since implementing an expanded regional meeting scope last year in Minneapolis, attendees taking a smaller block out of their schedule to attend have found an increasingly comprehensive approach to two important characteristics of today’s contracting company…the need for improved safety and the need to find ways of improving their bottom line. We were more than a little disappointed that area builders and building inspectors did not find an interest in seminars planned for Friday afternoon in Indy but when Saturday’s events opened, the outcome more than made up for it.
The CFA was fortunate to be on the doorstep of Custom Concrete who volunteered many from their company to bolster the new direction of CFA education which is “Building Better Businesses”.
Beginning bright and early Saturday morning, nearly 50 attendees that decided to attend the management tracks began to trek through concepts of “Managing Growth through Process and Technology”, “Optimizing Growth through Effective Delegation”, “Evaluating Your Business’ Facility Needs” and “Building an Invaluable Workforce”. The information at the root of these presentations demonstrated the significant lengths that we will now go to deliver a message that each can take away to potentially change their company strategies and decisions. Realizing the importance of effective processes and evaluations, quality facilities and ultimately educating and advancing employees is the target we have for these meetings. The efforts that Terry Blake, Jason Ellis, Jason Brown, Lee Truax and Ruthie Casner, all of Custom Concrete put forth to share ideas and generate discussion were nothing short of exemplary.
[Kathy, please contact Kevin Wernimont of Tri-State Concrete Construction, Inc. at 563-583-2307 and see if he can give you a quote to use on the impact this meeting had on him and then work it in here. They are a brand new member and committed to attending in Indy and The Dells right off the bat. I think this is a very important message, especially the distance they traveled.]
Management tracks or business concepts is a strong direction that will now be explored in many ways by the CFA as we continue to provide better opportunities for companies to grow through membership. The Board of Directors met during Friday morning of this event for their annual spring board meeting. Combined with a focus on ways to implement quality assurance in the CFA (see next issues’s survey summary on Certification) focusing on topics of how to help companies consider changes and implement business strategies has become a major direction the Board has given to your Association.
But let’s not forget about safety. Quality and effective safety strategies must be employed by foundation contractors no differently than any other business that involves such hazardous conditions as heavy equipment, open excavations and chemical exposure. However, through messages such as those delivered at this meeting to the nearly 40 in attendance, the atmosphere for safe work practices can be substantially improved clearing way for better education and company-wide commitments to change. The message seemed repetitive but coming from so many different angles including pumps, mixing trucks, truck cranes and excavation to name a few, “What Can You Do to Make Sure You Go Home Tonight” was certainly delivered with sound results. Once again, the commitment of speakers like Walt Tharp (IMI), Dan McGivern (V&H Trucks), Jerry Eisle (Cranes & Equipment), Dan Bromley (ABI Corp) and Gary Brown (R.L. McRary) to deliver a concise and convincing message of the importance of safety in and around foundation construction was beyond compare.
Though the opportunity to attend this level of education in a single day is something still relatively new around the CFA, it must be noted that this would not be possible without the incredible support of the many sponsors contributing time and money to make a difference in your businesses. Our commitment to education was echoed through the attendance of this spring’s sponsors:
• BigFoot Construction Equipment • Debco Crane & Machinery • Fine Line Footing Forms • HIAB Inc. • Irving Equipment • Irving Materials Inc. (IMI) • Monarch Foundations • Putzmeister • Schwing America, Inc. • The Bilco Company • V&H Inc. TrucksSo we close the books on the CFA Spring Regional Meeting 2006. The number of companies represented and the quantity of attendees was a great statement made by this section of the Midwest.
We begin to look forward with an extreme amount of interest to the Summer Meeting in The Dells where we will continue our commitment to concepts of “Building Better Businesses” while maintaining our level of quality minded education on the product produced. After that, it is on to Hartford, Connecticut for our next chance to demonstrate the effectiveness of pulling together companies on a regional level to network and expand the potential to improve the business of foundation contracting.
Thanks Indy, thanks Custom, thank you sponsors and thank you attendees.
Jim Baty, Technical Director jbaty@cfawalls.orgSurveys- MVI or MIV?
The CFA Staff has recently sent out several surveys to its members; one to collect our thoughts on some of our competition, one to poll us about our historical experience of sill-plate connections and even one on the topic of certification. Is it worth your time to fill these questionnaires out and return them? Are the results of these surveys useful? Are they MVI, Most Valuable Information or just MIV, Minutiae in Volumes?
I remember sitting in a CFA Board meeting years ago when one of my all time favorite people and Past President, Ron Colvin, (this was well before his presidency) gave us his viewpoints. I think the acronym he used may have been PIA! Ron, never one to mince words, thought all surveys were a complete waste of time. He said that the few people who fill them out are probably lying! Ron may have been right, in fact he probably was right, about most surveys, but after years more experience with this group I am certain that he underestimated the members of the CFA!
Every time the CFA Staff sends a survey to our membership, the response is amazing. We get a much better return rate than we expect, along with invaluable additional comments, suggestions and a wealth of knowledge on the issues. The feedback we get helps us understand the issues, the problems, the future and the very basics of our business. With this information we can plan events, articles, and be better equipped to guide codes and standards.
In the following pages you will read the survey results from the sill-plate questionnaire conducted in February. I believe you will find these results very interesting as well as the information on how this knowledge is being used to shape our industry and the “rules” we must follow. This is just one more shining example of how willing our membership is to help our group and each other.
To those of you that responded to this survey, I thank you on behalf of the membership and the industry. To those of you that did not respond, I hope you see the benefits that are being derived from gathering this information and consider participating in future efforts. Based on the effectiveness generated by our initial three, there will be more, but we are committed to keeping them Valuable and brief.
What a group this is! I hope to see you all at Kalihari!
Terry Lavy, CFA President, Lavy Concrete Construction Inc. terry@lavyconcrete.comA Complete Residential Concrete Code
The first edition of the ACI 332 Code – Requirements for Residential Concrete Construction, has been published. Chapter 7 (Foundation Walls) is referenced in the 2006 Edition of the International Residential Code. But what comes next? The 332 Committee has begun working on the next version (’07) with a goal to make it a complete residential concrete code. It should be noted that this effort has the enthusiastic support of ACI.
Many compromises (i.e. deletions) were made in producing the inaugural version, ACI 332-04, in order to get the approval of ACI’s TAC (Technical Activities Committee) engineering staff, agreement of committee members, and to meet the deadline for inclusion in the 2006 IRC. The cycle starts anew as the committee begins work on the 332-07 version of the Residential Standard (Note: the document is a standard until adoption by a legal jurisdiction, at which time it becomes a code). The goals of the committee are inclusion of the provisions that were deleted during the development of the ’04 version of the Standard, and reference of the entire Standard in the 2009 version of the IRC. The 332 Standard must be published nearly 2 years ahead of the code in order for it to be considered.
Incorporation of a design section for foundation walls and footings is a primary goal for 2007. The design section will include plain structural concrete (no vertical steel), moderately reinforced concrete (less than minimum ACI 318 required steel but sufficient to carry the loads), and a full design section with the modified design parameters included in the ’04 version. The benefit of the inclusion of a moderately reinforced section will be a reduction in the amount of vertical steel currently required in the empirical tables of the 332-04 version once the maximum loading conditions for plain structural concrete have been exceeded. The design provisions were in one of the earlier drafts of 332-04 but were deleted at the request of ACI. ACI-318 will no longer be referenced for residential foundation applications.
Inclusion of provisions for seismic design will make the document applicable to all regions of the US residential construction market. The primary impact of this will be load calculations, connections and design provisions for structures in Seismic Zones D, E, and F. Most CFA members will not be impacted by this change.
Finally, the inclusion of empirical design criteria for above grade residential concrete wall systems will be added. This is a very important step for continued growth of this market. Provisions for above-grade design of concrete systems are already in the IRC because of previous efforts of the PCA and ICF industries. However, the new provisions will reference all forms of above-grade walls regardless of the forming system used.
The 332-07 document with all new items must be developed, approved, balloted, and published within the next 18 months in order to be considered for the 2009 IRC. Once this edition is completed, the only exclusions will be cantilevered retaining walls and structural concrete decks and slabs. They will be on the agenda for the 2010 version of the 332 Standard. That doesn’t mean slabs and retaining walls can’t be constructed – but they will need to be designed in accordance with ACI 318, the current design method for these building elements.
A residential code, separate from the commercial code (ACI-318) has been a priority of the CFA for at least the past 10 years and it is great to see some progress toward this goal. I would like to welcome Kirby Justesen to the 332 Committee. He joins Buck Bartley, Barry Herbert, Brent Anderson, Jim Baty and myself to make certain the interests of the contractors who build these structures are represented. The 332 Committee has created sub-committees for each of the major residential concrete components (slabs, foundation walls, footings, above grade walls, materials, etc.) which provides opportunities for participation from a much broader cross-section of the industry. If you have an interest in working on this important document, contact Jim Baty, ACI 332 Secretary and CFA Technical Director at 866-232-9255 or jbaty@cfawalls.org.
Ed Sauter, Executive Director, CFA esauter@cfawalls.orgU.S. Ready to Increase Mexican Cement Imports
Yet to be finalized, an accord announced by the U.S. and Mexico last week to settle a 16-year dispute on anti-dumping duties on Mexican cement imports will help to alleviate shortages of the building material that have been reported in more than 30 states.
“With U.S. capacity running at full tilt, the nation still must import more than 20% of its cement supply in order to meet domestic needs,” said NAHB President David Pressly. “Once finalized, this agreement will provide additional supplies of Mexican cement to the U.S. market. The pact is vital to meet consumer demand, which is expected to increase in the coming year as the rebuilding efforts from Hurricanes Katrina and Wilma get into full swing.”
Under the proposed settlement, which could be finalized this spring, the U.S. will reduce duties on Mexican cement from $26 to $3 per ton, and Mexican imports will be permitted to grow to 3 million metric tons annually, up from last year’s level of approximately 2 million tons. After three years, the quotas and duties would be entirely eliminated.
During the past year, NAHB has held several discussions with Commerce Department officials — including Secretary Carlos Gutierrez — urging the Administration to overturn the costly tariffs and outlining how cement shortages have led to construction delays and harmed housing affordability by increasing the cost of building projects. Data was also provided on states and geographic areas that have been most affected by the shortages.
“We are pleased that Commerce Secretary Gutierrez heeded our concerns, and showed a willingness to work with our industry and consider the needs of American consumers,” said Pressly. The accord is structured so that Florida and the Gulf region, areas facing cement shortages, will be able to significantly increase their shipments of Mexican cement. The negotiated framework also provides the flexibility to allow the President to direct an additional 200,000 metric tons of cement to areas hit by natural disasters.
High anti-dumping tariffs that have been in place since 1990 have limited supply from Mexico, which has excess capacity. Because of its close proximity to the U.S., it takes only four days to import cement from Mexico, compared with 40 days from Asia.
“Throughout the process, builders have been pushing to resolve this dispute in a manner that leads to free trade, and we are pleased that this framework will ultimately lead to this favorable outcome,” said Pressly. “We urge both governments to quickly finalize the accord so that we can achieve this important objective as soon as possible.”
Under the agreement, the 3 million tons would be distributed in eight areas, as follows:
· Alabama/Mississippi — 55,000 tons · Arizona — 1.25 million tons · California — 150,000 tons · Florida — 200,000 tons (more than twice the state’s current allocation of 75,000 tons · New Mexico/El Paso — 725,000 tons · New Orleans — 280,000 tons · Texas — 215,000 tons · Rest of U.S. — 125,000 tonsFor more information, e-mail Jason Lynn at NAHB, or call him at 800-368-5242 x8307; or contact Michael Carliner, x8376.
www.theconcretesource.com
The world wide web continues to grow and serve as an ever-more-useful tool to all of us in the foundation industry. As one of the sponsors of The Concrete Source, CFA welcomes this new presence on the web as yet another great resource for us.
This site is organized into contractors, manufacturers, and manufacturer catalogs, with additional links to industry news, web site sponsors, announcements and safety articles. Place a want ad, look for a job or post a job, submit your professional listing, or look to see what’s on the industry calendar are some of the other perks to this site.
Member News
MONARCH MFG. NEWS
WAUKEE, IA – Monarch Manufacturing has promoted Tony Oberman to general manager. Oberman had been senior operations director.
“We are delighted to promote Tony to the position of general manager,” said Larry R. Haberman, CEO of Monarch Holdings, Inc. “He brings a high level of experience, respect, wealth of knowledge and strong leadership to our company.”
Oberman also brings strong leadership to his community. “Not only has Tony proven himself within Monarch, he has been the Mayor of Waukee, IA, one of the fastest growing suburbs in the US,” says Haberman. “And, this past year, he was honored with the coveted Forty Under 40 award for Excellence in leadership in Greater Des Moines.” The award recognizes outstanding young professionals under the age of 40 who have demonstrated exceptional community and business leadership
“Monarch is a great company,” says Oberman. “I have had the chance to move up taking on several positions at Monarch; I am looking forward to my new role and the opportunity to take on more responsibility. We have put together an excellent management team and staff at Monarch, I am fortunate to be leading such a talented group. In 2006 we will be introducing several new products, as well as, begin other initiatives to grow our company; it’s going to be an exciting year. “
Oberman joined Monarch as plant supervisor in 1999. He was promoted to senior operations director in the summer of 2005. As general manager, Oberman’s responsibilities will include overseeing sales, marketing, product development, manufacturing and financial aspects of the company. A prime objective of promoting Tony as GM is to bring a focus to Monarch to achieve significant growth via new products, new markets, and acquisitions. Oberman holds a MBA and a BS degree in Industrial Technology from Iowa State University.
Monarch manufactures a complete line of windows, including Egress, window bucks, and area walls integrated as a flexible system. For more information visit www.MonarchManufacturing.com
CHANGES FOR CIFA
A flurry of activity is taking place at CIFA USA, a CFA National Associate, to help support their expanding role in the U.S. market for concrete pumps. This includes their brand new production facility and additions to their sales staff.
Just seven months after the groundbreaking ceremony in mid-July the state-of-the-art facility in Yorkville, Wisconsin, is completed and officially the new home of the CIFA USA headquarters. This 8-acre facility consists of 38,000 square feet of production area with state-of-the-art equipment; 85,000 square feet paved area, and 5,600 square feet of office space.
The new facility will allow CIFA USA to accommodate the growth in sales and increase in personnel required to sustain its success. Future plans include expansion to quadruple the size of the Wisconsin facility which will allow for more growth in the product line. A Grand Opening ceremony is planned for mid-July, 2006. Mr. Matteo Rolla, Executive Vice President of CIFA USA, Inc states, “This Grand Opening will mark a new phase for CIFA USA and will include the introduction of new products designed exclusively for the US market.”
***
Don’t be surprised if you find yourself talking with two new managers for CIFA USA in the coming months. The company has announced the appointment of Mr. Kim Kretchman as Southern Regional Sales Manager and Mr. Bob Miller as Regional Sales Manager for the Northeast Atlantic states. Mr. Rolla has this to say about the two newest members of CIFA’s team:
“Mr. Kretchman is an important asset to CIFA with his vast experience in the pumping industry. He worked for many years with Oshkosh Truck Division, owned his own pumping company for 10 years and then became operation manager for Loflin Concrete Pumping Division. Mr. Kretchman truly has hands-on experience in the pumping industry and is the kind of salesman every pumper would like to meet.”
“Mr. Miller’s appointment strongly reinforces our commitment to providing complete customer satisfaction with the highest quality concrete pumping equipment in the industry. We are proud to have him on board.”
Those located in North and South Carolina, southern Virginia, eastern Tennessee, Arizona, and New Mexico can contact Mr. Kretchman, based in South Carolina at (336) 345-4895 or email to kkretchman@cifausa.com. Those located in northern Virginia, West Virginia, Washington D.C., eastern Pennsylvania, Massachusetts, New Hampshire, Vermont, New Jersey, and Maine can contact Mr. Miller, based in Maryland at (410) 610-9401 or email to bmiller@cifausa.com. Both may also be contacted by calling the CIFA USA headquarters at (877) 243-2345.
Concrete Townhomes Sail to Completion
EH Building Group II, the new Southwest Division of the heralded EH Building Group headquartered in West Palm Beach, Fla., is sailing to completion of its first concrete townhome development. Mike Aranda Sr., CEO and founder of EH Building Group working with Architect Kevin Campbell, of International Innovation Design, Cape Coral, Fla. designed Sail Harbour, the Caribbean-styled village on 46 acres of prime real estate in Lee County, Fla. The development is the only private residential community in Lee Memorial Health Park and is situated in proximity to the popular beaches of Fort Myers and Sanibel.
Sail Harbour consists of 473 solid concrete homes priced in the mid $200,000s and is slated for completion by April 2007. The two-and three-bedroom townhomes—many offering lake or preserve views—will range from 1,747 to 1,895 square feet of living area and will have one- or two-car garages.
Most housing communities in the surrounding area sell at figures well above Sail Harbour’s asking prices. But with this project, EH Building Group II sought to offer prospective buyers attractive, energy efficient and safe homes at affordable prices. To ensure high quality and to remain within budget for this large residential project, EH Building Group II selected the Outinord tunnel forming system. Potential costsavings alone, however, did not drive developers to specify Outinord.
They chose Outinord’s construction method because it produces high-quality structures that are energy efficient as well as sound, fire and weather resistant, and it offers construction workers unparalleled safety. “We’re pleased that EH Building Group II chose our tunnel forming products for Sail Harbour,” says Robert Fallowfield, vice president, Outinord. “We’re involved with some exciting high-end residential and commercial developments in the region, and it’s equally rewarding to work on a neighborhood where people of all ages can find affordable, well constructed and safe homes in Florida.”
As fast-paced purchases have indicated, homebuyers have been enthusiastic about the homes’ solid concrete construction and amenities like a development-wide state-of- the-art fiber optic network, optional elevators and the community’s village cabana with pool and sundeck. EH Building Group II opened sales in October 2004 and within three months 2/3rds of the neighborhood of friendly streets was sold. As of May 2005 all 473 units were sold, with a large share of sales coming from overseas investors.
The buyer’s excitement comes as no surprise to Bruce Hershey, vice president of corporate sales and marketing EH Building Group’s Southeast and Southwest Divisions. “It is easy to bring your family home to the finest quality the construction industry has to offer—a beautiful place in this region that affordably offers the security of solid poured concrete walls and ceilings and hurricane windows and doors.”
Sail Harbour is making a big splash in the building industry as well. Parent company, EH Building Group and the Sail Harbour community were featured in the June 2005 Builder magazine. The development was touted as one of 10 best-selling communities in the nation’s top 75 housing markets, and the company was ranked as the seventh fastest growing builder in the country. The Builders Association of South Florida also honored Sail Harbour when it bestowed on the new townhome community four of the association’s “Florida’s Best” awards in 2005.
Based on Sail Harbour’s resounding success, EH Building Group II will soon develop its first gated golf community in Southwest Florida, Copperhead Golf and Country Club in Lehigh Acres. Copperhead will have 990 home sites situated around a par-72 Gordon Lewis-designed golf course. Select homes in the development will include tunnel form construction.
Sail Harbour is EH Building Group’s first community in Lee County. The award-winning company has more than 23 years’ experience delivering the most popular neighborhoods in the Palm Beach area, including East Lake Village, Wyndham Park, Country Club Village and Pennock Landing. EH Building Group and its subsidiary, EH Building Group II, are committed to continually improving its products with technological advancements and enhanced services that add value to the customer’s investment. A strong commitment to customer satisfaction and high ethical standards are the foundation of this effort. The company’s Southwest Florida division headquarters is located at 12751 Westlinks Drive, in Unit 1, just east of Southwest Florida International Airport, off SR-82.
Call (239) 275-0707 for more information or visit www.EHBuilding.com to learn more about the company’s first class communities.
by Wendy Shannon and Libbie Hough, Op5 Creative Wendy Shannon is President of Op5 Creative in Atlanta, Ga.K-WALL — from 3 years and 13 people to 13 years and 33 people
•Traverse City, MI 49684 Phone: (231) 943-4727 Fax: (231) 943-4679 •Petosky, MI 231-348-3449 www.K-Wall.comFounded by Rich Kubica in 1993, K-Wall Poured Walls, Inc. currently specializes in poured walls, E-Maxx Insulated Poured Walls, Concrete Flatwork and Concrete Homes. Today Patty and Rich Kubica co-own the company and have 33 employees.
Although the picture above (built by K-Wall) may give you the idea that K-Wall has moved their office to the Virgin Islands, Rich and Patty Kubica are solidly entrenched in Michigan. Founded by Rich Kubica in 1993, K-Wall Poured Wall, Inc. currently specializes in concrete poured walls, E-Maxx Insulated Poured Wall Systems, concrete flatwork and concrete homes.
Patty and Rich make a good team, leaving one partner to focus on the job site, and the other able to focus on marketing and sales. Patty first met Rich when she was serving as her own general contractor and hired him to pour the basement in a new house she was building. It was apparent to Rich that Patty knew her way around the job site. They became friends, then business associates, and finally, a couple. Patty joined K-Wall in 1997 and they were married in 1999.
At the time Rich had 12 employees and plenty of work to do – often burning the candle at both ends. He was named ‘Young Entrepreneur of Michigan’ in 1996, three years after he started K-Wall. He ran the business out of a small, rustic office, and had to rent a truck-mounted concrete boom pump for many jobs. Today K-Wall has 33 employees, a new 6,300 square foot building, and their own pump truck.
Patty self-appointed herself head of sales back in 1997. With her marketing background and construction knowledge industry, she has been able to focus on meeting potential clients – often with a bag of homemade muffins in hand (She is a certified chef too!), Rich and Patty have worked hard to build customer relationships for K-Wall. Patty says “The relationships and loyalty we have gained over the years with one-on-one communications with our customers are priceless.” They have a good team from the top down, and their other key players are Mark Steckley-Marketing, Wade Mariage-Project Coordinator/Scheduling, and Patty’s assistant, Nancy Hayes. Patty gladly says “And we’ve been successful. We’re a team. If you work hard, have a quality product, excellent service and good employees – and make smart business decisions – the rest follows naturally.”
Patty and Rich say one of the smartest things they’ve done is to invest in their own business. They have always believed in the worth of investing in things that will make their company more efficient and professional. With K-Wall, that means their modern facility, the best crews, top materials and equipment, and continuing education for them and their employees to keep up with the latest technology.
They say their investments have paid off many times over and they’ll continue to make them when they feel the time and reasons are right. In the end, it’s not about making money, but about making money work for you so that you can serve your customers better.
The K-Wall staff stays connected into their localHome Builders Association and Habitat For Humanity organizations, and nationally through CFA.
ABOUT THEIR PRODUCTS AND SERVICES…
K-Wall offers a variety of services, including:
•firm fill gymsum concrete floor underlayments •Gyp-span radiant for in-floor heating systems •E-Maxx Insulated Wall System •decorative concrete •flatwork •pools and whirlpools, and •waterproofing.Patty and Rich find that when they attend industry meetings, much of their time is spent talking to other contractors about the EMaxx Thermal Wall System — although manufactured and distributed by a Michigan manufacturer, they are the patented inventor of this product. In 1998 Rich came up with the idea after he had received several requests for a better insulated foundations and above grade housing.
The E-Maxx Thermal Wall System, based on an 8” thick wall can have an R-value of 11.5 to 26. There are EPS panels available for above grade use also. The E-Maxx system puts more concrete into the foundation, doubles the insulation value of precast, and offers more customization on the job site. These systems are particularly valuable in high wind areas such as the coast.
The E-Maxx Insulated Poured Walls have a total effective insulation value of up to R-46, accomplished through expanded polystyrene, zero air leakage and ‘heat absorbing’ thermal mass properties. K-Wall has been pouring walls in Northern Michigan since 1993 and upholds the highest standards by using the finest products and industry leading equipment. They attribute their solid reputation to being on-time and providing an outstanding finished product. KWall offers Rub-R-Wall® (Koncrete Armour) waterproofing with a 100-year warranty or WallShield Waterproofing with a 10-year warranty.
Editor’s Note: Thank you to the Grand Traverse Woman magazine for information about Patty included in this article, see 13-1.