Elevating Board Form Concrete to a Marketable Aesthetic
If the Great Recession has taught us anything as a company, it is that a concrete construction company can be extremely resilient when everything is on the line.
In order to be resilient, our company had to be creative and apply ourselves to finding work and finding uniqueness any way possible. Out here in the West, we noticed an architectural trend in housing toward what was being referred to as a “contemporary aesthetic”. This challenged us to see our ability as not just a concrete contractor but to apply our craftsmanship and generate a marketable product.
Now, whether or not a concrete contractor really knew what contemporary aesthetic meant was somewhat beside the point. What we saw changing in architecture was that contemporary was a trend to save cost. The designs were simple, straight lines and crisp, clean forms. Gone were the high pitch roofs, eyebrows and extensive elevating forms. Roof lines had become flat and simple. It seemed the architectural change offered ways of achieving structures with less cost because land prices recovered quickly. Builders and developers condensed forms and simplified designs to make housing affordable in our market.
As the architecture changed to the contemporary or more modern style, it was natural that concrete would participate and in some ways return to being featured. While concrete would be more expensive, it had important value among three timeless, organic and natural elements (wood, stone and concrete) that elevated the sturdiness of housing or grounded it when combined with steel and glass. We found owners began developing an interest in a combination of concrete and wood in a “rough” look for their homes, desiring a board form concrete finish. We started with a few small board form jobs during the deepest parts of recession in 2008 to 2011. These jobs gave us some experience and opened our minds to the possibilities. Utah then recovered more quickly than some regions of the country and all of a sudden we saw a number of jobs proposed with a lot of above grade, board form concrete walls. Not all were full or even significant amounts of board form. More than a few of these projects were patio or retaining walls where the board form anchored the style of that specific space.
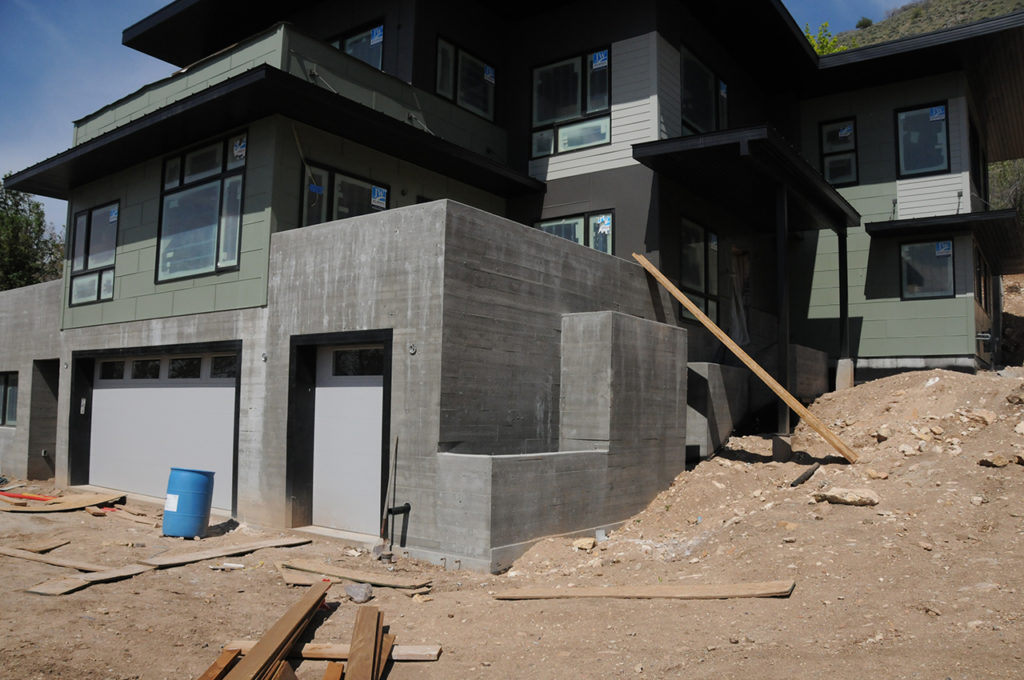
Our first big job was designed by an architect from Seattle, Washington with considerable experience designing uninsulated, above-grade concrete having an exposed architectural finish. This look can be a real challenge and after several mock-ups, which we have come to realize are extremely important on every architectural wall, we decided to go with a liner of 6 in. wide ruff-cut cedar.
We looked into information from ACI and talked with local consultants before deciding to pretreat the cedar with a cementitious covering to draw out the sugar in the wood. Our research identified that natural sugars in the softer parts of the wood grain act as retarders to the hydration process. The cementitious covering was intended to pull those sugars out and leave the wood neutralized for our casting operation.
Once the project started, however, we realized the size and scope of what we were dealing with and underestimated the amount of cedar we would need. This project had board form in the site work, three fire places each thirty-five feet tall, retaining walls and enclosure walls. Needing additional wood, we didn’t have the time to pretreat cedar so we went forward with untreated wood. The resulting finish between the treated and untreated cedar showed zero difference. We saw nice horizontal lines and a crisp look with both. We didn’t get a lot of wood grain but we did see clear expression of the knots. This remained confusing to us with all the warnings of retardation due to sugaring. I deduction was it may have been due to the form release we use. We strongly suggest mocking up your finish before attempting it without pretreatment or some other precaution against the sugaring potential.
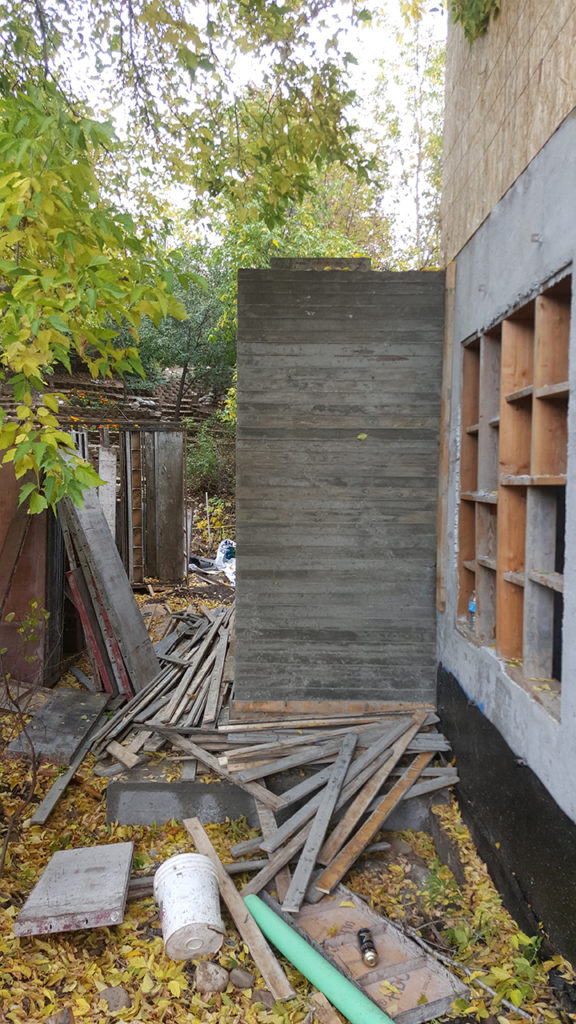
Designing the Mix
The mix we developed through the mock-up process to minimize bug holes consists of a 7-bag mix with 30% fly ash replacement. We added a mid-range water reducing admixture to increase flowability and lower the w/ cm. This permits us to place concrete at a 6 in. slump (+/- 1 in.), which we test out of the truck. The mix does tend to get a little hot so when the ambient temperatures are above 60 ̊F we add a delay-setting admixture. Over the last four years this mix as proven consistent and has yet to disappoint us in its workability or durability…other than the heat it generates. There is an extra cost of this design mix but the trade- off to performance in the architectural finish and placement consistency is worth the premium.
Attaching Board Form to Aluminum
One of the biggest questions that came up was the best way to attach the cedar boards to our forming system. Most of the concrete contractors we know use aluminum forms, like we do. Having access to conversations with others was important for our research and this network helped us come up with two plausible options.
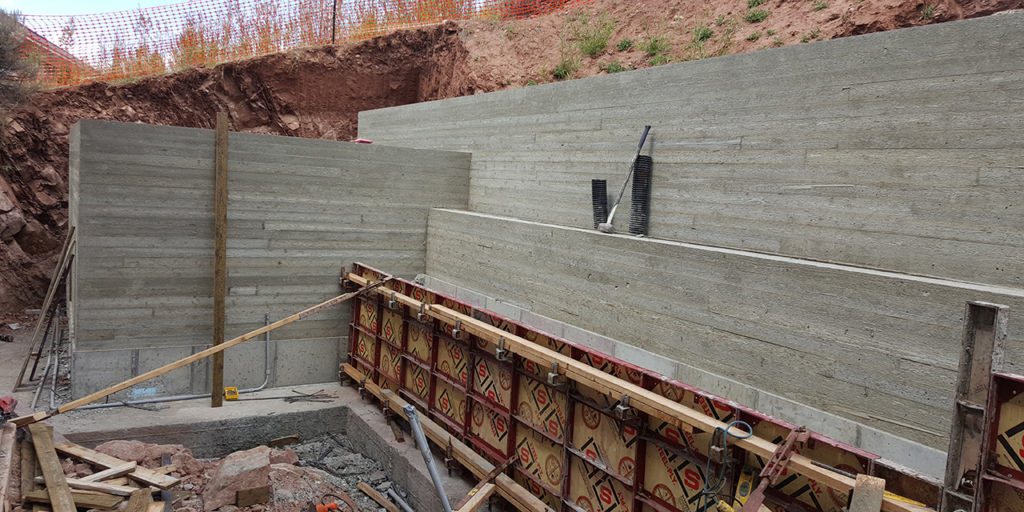
At first we tried using self-tapping black screws. These are your common, inexpensive drywall screws and they worked well enough. However, we found that the screws were very difficult to locate when it came time to remove them and the liners.
We received a suggestion then to try a very sturdy steel screw called “Remove Right”. This screw as a 1/4-in. hex headed end that is painted orange, making it easier to install as the head is less likely to strip and doesn’t snap off from torque. This screw was far easier to find, remove and then reuse.
We also discovered through our challenges that you need to consider the form tie. With our aluminum forms, we needed a tie that has a 1 in. break-back notch. We talked with the manufacturers and found we could order them. We use a multi-tool to cut a slot in the boards to accommodate the tie and keep the concrete crisp around this penetration.
Moving Forward
One of the challenges we faced with the acceptance of our board form finish was the lack of wood grain. We knew we would encounter owners that would want to see more grain expressed in the finished concrete surface. We started by distressing the grain using a wire wheel brush to remove the softer wood from the grain. The harder wood was left as raised areas and the grain had almost a burnished surface. It worked well enough, but in the end we decided that it took considerable time and still didn’t give us the consistency. Depending on the attention we gave the wood, we would end up with additional unnatural lines or wearing.
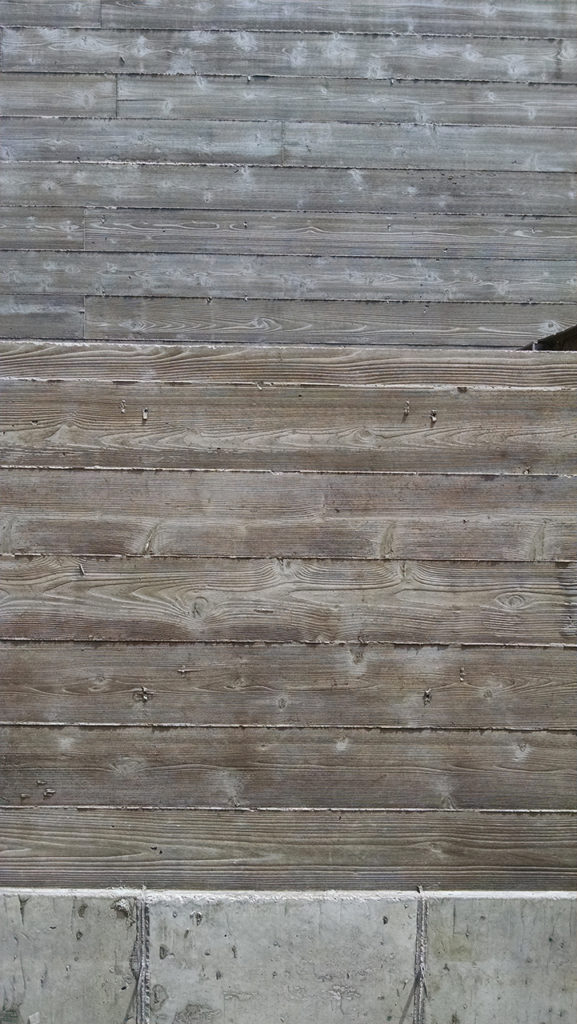
Our current solution is to use a weed burner over the entire board surface. We then use the wire wheel to take off the charring. This method has proven to produce the most beautiful wood grains with highs and lows. We then seal the burnt cedar with a standard wood sealer. This has provided us the actual control of the sugars in the wood and eliminated the expensive and time- consuming step of pre-treating the wood with a slurry mix. The sealer has also helped us more consistently reclaim the wood liners for multiple uses.
Basic Costs
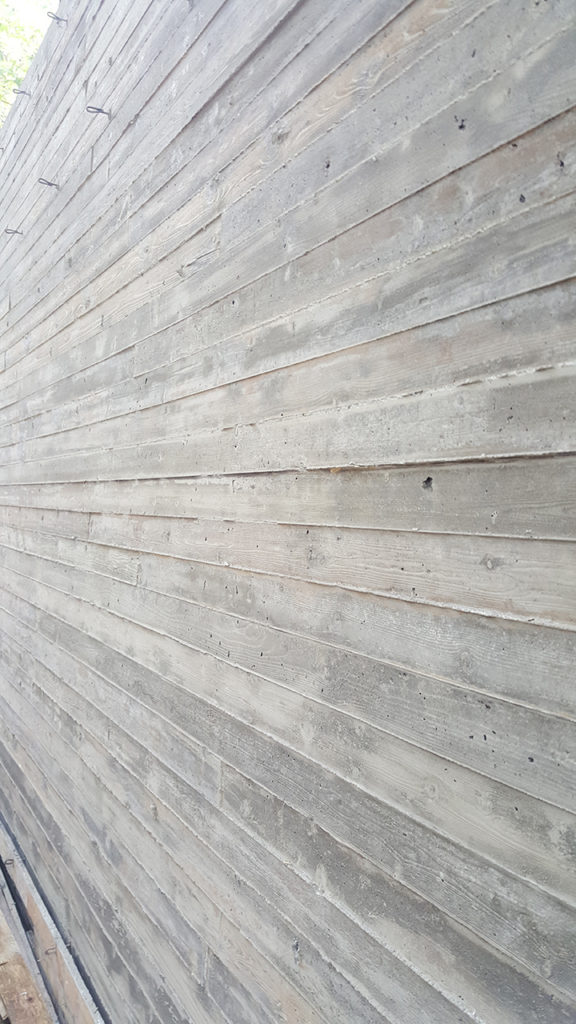
As a whole, the experience is our major investment. For materials we end up with about $2.50 per square foot for the cedar. We have mastered the reuse of the wood such that the cost to prepare the boards by burning, char removal and sealing is very minimal to the cost of the wall, although you would want to figure it in that first start-up, perhaps a $1.00 to $1.50 per square foot. This gives us a rough board liner cost of about $4.00 per square foot. Compare that to some of the labor costs for installing boards or for multi-use liners.
We believe the patterns and the results are speaking well for the time and energy we have invested in carving out this market niche or rather a response to the architectural trends of our market. For more information, give us a call, we’re proud to be part of the Concrete Foundations Association and have benefitted from talking through some of this development with several of our peers along the way.
ABOUT THE AUTHOR
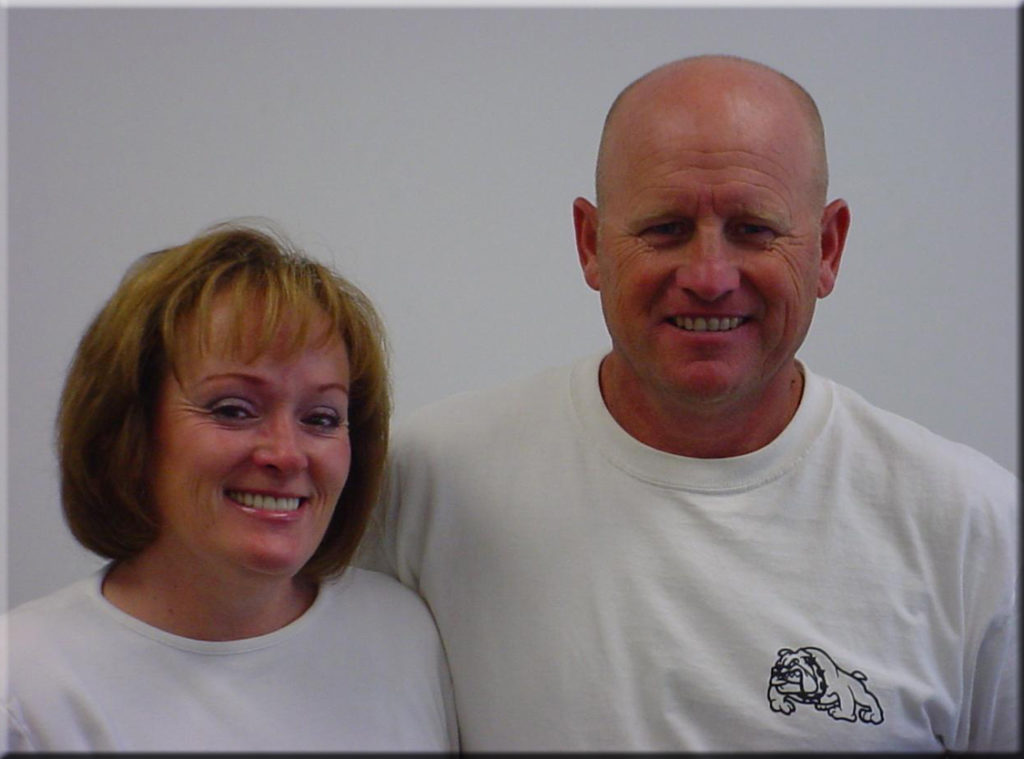
Kirby Justesen and his wife Pam reside in the Salt Lake City, Utah area where he is an owner at SCW Footings and Foundations. He is a leader in the concrete industry, now serving for his second time on the Board of Directors for the CFA and is a voting member of ACI 332, the residential concrete committee for ACI (www.concrete.org). Kirby has served as the chair of the CFA Technical Committee and has been part of the development of the three CFA Standards published to date.

Previewing CFA Convention 2016
Spring has sprung and no doubt your company is headed out the door in a frenetic pace. Most of the U.S. residential market is ramping up for a solid 2016 forecast as we have heard from so many of you. While PCA has tempered their projections from the Spring of 2015, all indicators are for a good and solid year for the residential construction industry. In fact, with so much at stake later this year for elections, many presume that there will be a strategic effort to increase the pace over the summer to fall.
Right in the midst of that is CFA Convention. Each year we answer the question by those that weren’t able to attend the previous year (but so much desired to), “why is it that CFA’s convention is held during the busiest time of the year for the foundation contractor?” After fifteen years on board with the CFA, I believe I have finally come to know the market well enough and the businesses each of you manage intimately enough to be able to see it. It isn’t easy, that’s for certain but there are several major variables that permit and even direct Convention to have its own place in the middle of the year.
Convention is a family-friendly environment – The values of business in this industry start with the family. It is important to maintain that feel and to celebrate it while the kids are able to take advantage of a great destination. Today’s kids become tomorrow’s management. They get a chance to grow up in the environment.
Convention is a strategic break – In the midst of a busy construction season, by the time July rolls around the schedule should be in good shape and company processes controlling the daily schedule. It is also at this point when the pressures are mounting and a break is needed to be best prepared to lead. Taking two to three days away can be the right refresher to renew passion, commitment and fine tune leadership through interacting with your peers and realizing you are not at this alone.
Convention builds identity – The rest of the concrete industry is defined by off- season and late-season opportunities for learning. These are times when the cash is the hardest to come by or the pressure is the greatest trying to fit things in. Here in the middle of summer there are no other major concrete industries representing themselves or gathering. This gives way to CFA Convention being the right location to bring together all industry interests, contractor and technology alike to make true the identity of the ‘Largest Gathering of the Poured Wall Contractor.’
Conflicts come and they go. Some of them are unavoidable and some of them are value-driven. What you can’t mistake is the value of being in a space and time with others that have your responsibilities, your mindset and also that of your next generation of leadership.
A Tale of Two Events
Each year, one of the things my crew members look forward to is a chance at an annual trip to World of Concrete. This year was no different and we ended up taking a total of fourteen guys that did their very best in this past year. World of Concrete has continued to be an affordable and beneficial way for me to take guys from the field during the off-season and put them in a place where they can experience the indus- try at a grander scale, obtain some continuing education that helps them to expand their thinking about concrete and the work we do or how we manage … and yes, at the same time it gives them a place to go and let down their hair after a long year.
One of the requirements I have for them is attending a minimum of three classes during the week. With more than 75 courses to choose from, each guy has a chance to hit something of interest and bring it back to the company to improve themselves as well as those around us. I challenge them to share within that first week we’re back.
However great World of Concrete is for my guys, it isn’t the complete event for my professional needs. I find it really hard to concentrate and maintain more than a fifteen-minute conversation among all that is going on. While the gathering at the Hofbrauhaus is a great way to catch up with friends and my guys get the absolute most out of the evening, what I find energizing and most beneficial for my company is the CFA Convention, held each year during the latter part of the summer.
You’re asking right now how it is that I can take off from my business and head to some resort or enticing vacation spot with my family for a few days to a week. I’d have to ask back, how can I not? After experiencing my first Convention over a decade ago, I’ve only missed those that are in direct conflict with a family event that I have no control over. I’ll even make a point of flying in just for the opening and first day if I can, to reconnect and pick up something valuable for me to chew on and drive my company forward in the months ahead.
There are a lot of choices for your management attention. If you are like me, most of them come at you so fast that you either knee-jerk and make the wrong decision or you wait to long and the opportunity is gone. I’ve come to know that being able to absorb from my peers and from some very important speakers CFA lines up to hit just what it is we are facing in our businesses while being in a relaxed and open-minded state has made a direct impact on my business. I will be at CFA Convention 2016 in Myrtle Beach. I challenge you to make that commitment. You will not regret the investment it will be for your company.
David Martinson – Martinson Construction
Letter from the President: Why We Persevere
This issue’s letter from the CFA Board President:
Why We Persevere
David Martinson Martinson Construction davem@martinsonconstruction.comI read a history document not long after joining the Board that talked about the original ideas for forming this Association. I found it of great interest to see how we compared today with the ideas such strong industry leaders had back in 1974. The original goal was to build the industry and support individual markets. Back then, you see, a poured concrete wall was still considered a premium, an upgrade, a luxury for a foundation and concrete block was much more common.
I’ve had a chance over my years as a CFA member to be in conversations with some of those leaders and find the strategies and the desires they had so much like we still hold today. I think it comes down to change. Change is not fun, nor is it easy. Yet when change happens after through perseverance and deliberate effort, it is almost certain to prove beneficial and liberating.
As President, I am very pleased to be able to participate in the endorsement of an effort that has finally come to fruition after more than twenty years. This effort is the epitome of such perseverance and I believe is absolutely an example of the type of impact the founding leaders of this Association set out to create. In 1994, the Board of Directors set out to create a standard group plan for insurance. The goal, as I understand from those efforts, was to isolate poured concrete contractors from the general insurance industry in order to establish better risk management and safety guidelines.
After each attempt to identify a company that had both the appetite and the ability to work with such an isolated group, the Board experienced setbacks, failure and restarts…that is, until the winter of 2014. Members of the Concrete Foundations Association, you will soon be receiving an announcement from our staff for the endorsement of the CFA Member Standard Market Insurance Program brokered by Arthur J. Gallagher, a titan in the alternative insurance industry. With it, you have a bright option for your insurance future.
As a CFA contractor member, you should try and take advantage of this new benefit as soon as possible. Contact our staff and they will put you in touch with the team at Gallagher who can develop an insurance quote for you and work through the options for your to pursue. This can make a very large difference in your planning for 2016. They will work with you based on your renewal dates and your needs.
Those of you reading this letter that are not a CFA member, you should also take this time to celebrate. We’ve been encouraging your company to join the CFA for the countless opportunities and advantages. This one alone makes any price of membership seem insignificant. What are you waiting for?
Where We Are Headed
All indications at the moment support the concrete industry maintaining a steady climb through the winter, into the heart of 2016 and extending in that same way into the 2020 to 2021 neighborhood. That is five to six years of constant growth, pressure, advancement and yes, change. Is it possible? Is it realistic?
Let’s assume for a moment that it is realistic and not only possible, but that it is imminent. In order for you to be supported throughout this growth cycle, this Association has to make some changes. We have to grow and expand to be able to provide the response and the resources that will be required by you and by the entire market. So what does that look like in terms of our strategic development? We are two and a half years into a strategic plan that was aimed at this very condition. So, for the most part we are implementing that very framework that is anticipated to support a larger Association.
The CFA Board of Director’s Strategic Plan for 2013 included the following items generated as goals for the next three year period. Each of these has been completed and efforts are underway to further increase awareness.
- Standard Market Insurance Program for CFA Members – exclusive insurance pool for all property and casualty lines.
- ACI/CFA Residential Foundation Technician Certification – transitioned fully to ACI
- CFA Residential Foundation Company Certification – expanding to new markets
- Expanded Convention Programming
- More tangible member benefits from resources
- Increased number of CFA regional events
I encourage you to read the interview with the newest Board members of the CFA beginning on the next page. You’ll find all three describing value from their membership growing through a common aspect, CFA meetings. This validates one of the Board goals to return to and increase the number of regional opportunities to be engaged in this peer network and learn more about your potential role.
The CFA Board continues to travel each Spring and Fall to meet during ACI Convention and lend their experience to the development of better codes and guides for your industry. We are combining these events and adding further regional opportunities to participate and learn at the same time. A regional event will be held near you soon and perhaps with increasing frequency. These won’t be the end all type of meeting as only CFA Convention can provide that, but they will establish a stronger sense of participation in an industry rather than attending to business in isolation. You simply can’t afford to remain on an island in the months and years to come.
Ask questions, challenge resources and request opportunities to be part of this evolution of your industry.
James Baty
CFA Executive Director
jbaty@cfawalls.org
Engage Your Employees With Elevated Communication
In many ways, Adrian Aragon was a great CEO; hard-working and completely devoted to his staff and organization, but it was not until he analyzed his CEO performance review that he noticed the blind-spot in his leadership: the gap between how he saw his communication, and how his employees were interpreting it. Committed to becoming a better communicator and more effective leader, Adrian met with an old colleague Ivana Smith, one of the nest leaders and communicators he had ever met. After scrutinizing his report for what seemed like an eternity, Ivana asked Adrian: “Why do you think so many of your employees believe you have a negative mindset and don’t communicate effectively with them?”
Adrian took a moment then muttered, “With all the stress it’s hard to always maintain a positive and enthusiastic attitude.”
Ivana nodded in agreement. “That’s true, being positive when stressed is a real challenge, however doing so will help lower your stress, increase your energy and make you feel a lot better. It will also help set the tone for your entire company.”
“I guess you’re right. I should probably be more positive.”
“More positive yes, but the real key is to really listen to them. The most important part of communication is effective listening. Most of us are rather disengaged when we listen, but if you can really listen to what your employees are saying you will be able to build more trust and rapport with them, resolve more conflict and connect in a deeper way with them.”
Ivana is right. Effective listening does two things; it ensures that the sender’s communication has been received as intended, and it tells the sender that their communication has value. There’s an old saying, “Listening is love.” Great listeners are masters at making those they are listening to feel important, and perhaps on some deeper level, loved. To really connect with your staff and make them feel valued you’ll want to move towards empathetic listening.
Disengaged Listening
Have you ever had a conversation with someone you felt just didn’t get anything you said despite their involved contribution to the conversation? You probably sensed their minds were completely focused on what they wanted to say next, and not on absorbing and processing what you were saying. Well, that is disengaged listening, and most of the time although we might be hearing what’s being said, our minds are actually busy thinking about what to say next. Disengaged listening isn’t just responsible for corrupting the communication that’s being received; it leaves the speaker feeling unimportant.
To escape the disengaged listening trap, the next time you are having a conversation with someone begin to notice when your mind either starts to wander from the conversation or is thinking about what to say next. The simple act of bringing awareness to how you listen will make you a much better listener and leave those you communicate with feeling valued.
Engaged Listening
Engaged listening means listening
without judgment, opinions or preconceived notions. Engaged listening creates a space for others to really express what they are thinking without them feeling like they are being judged. It also ensures they are heard, and that their thoughts and feelings are important to you. You can become a more engaged listener by asking empowering questions; questions that probe, seek clarity, focus on solutions and put the power to solve a problem or challenge into the other person’s hands. For example, “How might you accomplish that?” or “What’s another way of seeing that?”
There is a direct link between employee engagement and how much those employees feel their company values them. Organizations that have created a culture that values its staff by listening to them in an engaged and nonjudgmental way will find its members reciprocating the value and respect they feel by raising their energy and level of engagement while at work. You can become a much more engaged listener by acknowledging and validating the feelings other people express to you the same way Ivana did with Adrian.
Empathetic Listening
This is the highest form of listening and will build strong ties with your employees if you master it. Empathetic listening is feeling what the other person is feeling through their communication. It includes deciphering body language, reading between the lines, listening for tonal discrepancies and looking for what’s not being said as much as what’s being said.
Listening at such a high level lets the person who is speaking know that you’ve captured their emotional experience. Although empathetic listening requires considerable focus, effort and concentration, with enough practice it can become routine.
Adrian worked hard at being a more positive and effective communicator. He became a lot less judgmental and shifted his focus from finding problems to finding solutions. Whenever his employees were upset about something he’d acknowledge and validate their feelings. And when they became stuck or frustrated, he’d ask them empowering questions to shift their perspective. He developed more rapport with them, and earned more of their trust, which left them feeling more valued, respected and connected to him. It didn’t take long after that for their own performance and engagement to increase as well.
ABOUT THE AUTHOR
Ascanio Pignatelli is an award winning speaker, seminar leader, coach and author of the forthcoming book Lead from Need. He is the founder of ApexCEO, an executive coaching and leadership development group that helps C-level executives develop the leadership and communication skills to create more engaging workplaces. To book Ascanio for your next speak- ing event or workshop, please call him at 310.913.2313 or visit www.apexceo.com.
WoundSeal Instantly Stops Bleeding
When Jobsite Accidents Occur, WoundSeal Instantly Stops The Bleeding To Safely Keep Workers On The Job.
Hook knives, box cutters, and saw blades all tools of the trade and three of the biggest reasons construction workers suffer wounds on the job. When accidents happen, injured workers can stop bleeding cuts instantly through WoundSeal, a breakthrough powders doctors have used for years in the hospital.
Now available through occupational first aid distributors and over the counter at national pharmacies, WoundSeal is a topical powder that stops external bleeding through the creation of an instant, protective and waterproof scab. Ideal for the jobsite, the easy-to-use powder enables injured workers to effectively treat their own wound in order to get back to work quickly.
In the home, treating a bleeding wound is typically very easy due to the availability of first aid supplies and the clean environment of the home. But out on a construction site, it s a different story.
“When accidents happen, especially in the construction industry where there are many contaminates such as dirt, grease and dust that can enter a wound, it is critically important to treat the wound immediately to avoid adverse health outcomes,” states Louis M. Guzzi, MD, a prominent Orlando critical care physician. “In the ER, I’ve treated the injured who couldn’t stop their bleeding wound and those who come to my office a day later because their ailing wound was treated with duct tape, glue or not at all.”
“In many cases, most of these trips to seek medical care could have been avoided if the injured worker could have stopped the bleeding quickly and protect it from the elements. That’s why I’m excited to see that WoundSeal, the same product I use in the hospital, is now available for purchase. I’m confident that this one first-aid product will help save both the worker and his/her employer money, time and aggravation.”
How WoundSeal Is Different & Works
While hemostatic agents, such as styptic pencils, have been on the market for minor shaving nicks and paper cuts, WoundSeal is the only product that can treat a broad range of external bleeding wounds.
Here is how it works once a cut occurs: The person tries to clean the bleeding wound if possible and lets the wound re-bleed. Blood is necessary for the powder to work.
With blood present, the person pours the topical powder – comprised of a hydrophilic polymer and potassium ferrate onto the wound and applies light pressure. Powder + Pressure = Instant Scab.
The powder interacts with the wound’s blood to form a protective scab in seconds. Note: the powder works independently of the body s blood- clotting cascade to stop bleeding without entering the blood stream.
The instant scab protects the wound and is waterproof. It falls off naturally as the wound heals.
Through WoundSeal s breakthrough technology, consumers treating a bleeding wound can now reduce the number of steps and products used to one easy-to-use application and reduce actual bleeding time from minutes, hours or even days (as with senior citizens) to just seconds. Unlike traditional gauze, tape and bandages, WoundSeal is guaranteed to stop external bleeding.
For construction workers who bleed easily and persistently because of a medical condition or prescribed medicine, “WoundSeal is one of the biggest revelations in occupational first aid since adhesive bandages were introduced more than 100 years ago,”states Dr. Guzzi. “The ability to go from many products to just one, and increase the effectiveness of stopping bleeding is a tremendous step forward in wound care.”
Clinically Proven and Tested
While the topical powder is new on retail shelves, it is has been in use at leading hospitals for several years. Additionally, sports medicine professionals and trainers have also used the powder to stop bleeding at the collegiate and pro levels. Through WoundSeal Powder, people in industries that are likely to get frequent cuts or lacerations now have access to the same topical powder doctors use and what researchers have studied in the following:
The Science of a Seal for PICC Line Management: BioSeal CVC Powder: An Alternative Hemostatic Agent That Keeps Sites Dry and Intact. 2010. Florida
Hospital. (Editor’s Note: BioSeal and StatSeal are trade names of WoundSeal in the hospital).
Comparative Efficacy and Safety Results of Topical Hemostatic Powder and Sterile Compressed Foam Sponge in Second Intention Healing Following Mohs
Micrographic Surgery. 2010. University of Indiana.
Comparison of a Novel Hemostatic Agent to Currently Available Agents in a Swine Model of Lethal Arterial
Extremity Hemorrhage. 2007. Study sponsored by the US Department of Defense.
WoundSeal is nationally available through occupational health / first aid suppliers and at Walgreens, Rite Aid, CVS and other retailers. Visit www.woundseal.com for exact store locations and list of distributors.
Media Resources:
1. A multi-media release with downloadable photos and videos is available at www. stopbleedinginstantly.com.
2. The following sources are available upon request:
– Louis M. Guzzi, M.D., Orlando- Andrew McFall, vice president, Biolife
-Contact Scott Carpenter at (813) 210-0383 or scott@nextgreatbrand.com to coordinate.
3. WoundSeal product samples to test, for yourself, a friend or a senior you know who bleeds easily are available by contacting Scott Carpenter
4. WoundSeal product samples to test, for yourself, a friend or a senior you know who bleeds easily are available by contacting Scott Carpenter
About Biolife, LLC
Biolife, L.L.C. is a privately-owned company that manufactures and distributes a patented topical powder that stops bleeding and forms a seal over an external bleeding wound or an access site. Founded in 1999 and headquartered in Sarasota, Florida, Biolife’s powder products are sold to leading hospitals, occupational workplaces, profess
Editor’s Note: WoundSeal product samples to test for yourself, a friend who frequently bleeds or even your readers willing to try it (limited volume) for a short product story on its results are available by contacting Scott Carpenter at scott@nextgreatbrand.com.
RISK MANAGEMENT: Controlling Your Company’s Insurance Costs
Total Cost of Risk: A company’s soft and hard costs which contribute to the overall cost of their insurance program.
For too long insurance agents’ jobs has been oversimplified to just the placement of insurance and issuing certificates of insurance. The CFA and Arthur J. Gallagher have set a goal to be the best client service company in the industry and to do that, we will stand out from our competition by offering services typically
Controlling your company’s insurance costs is not something that happens overnight. It is a progression which requires continued vigilance and a balanced, measured approach. Regrettably there is no one stop solution to achieving and sustaining your company’s optimal Total Cost of Risk (TCOR). Every company is unique and no solution is going to be one size fits all. It is knowing these fundamental facts that led the CFA to partner with Arthur J. Gallagher to create a program for CFA members.
Soft Costs
So how are we going to do it differently than your current program? How are we going to get your company to optimal TCOR? Like any good building, first things first, we need to start at the foundation. Gallagher will conduct a thorough policy coverage review of your insurance coverages. We will also conduct an assessment of your operations to identify if your current insurance coverage has been customized for your company. This accomplishes several things. First, it allows us at Gallagher to get to know you, your company and your safety culture. Second, it identifies any potential gaps in coverage you may have which if left unchecked could cause an uncovered loss event. As you know, an uncovered loss would directly hit your bottom line. We are not looking to just place your insurance coverage, we want to partner with you to create a long term, practical and beneficial broker-client-carrier relationship. Additionally, we are analyzing CFA members risk management programs across the country to develop best practices. This will allow program members the option of implementing the best methods and will help members of all sizes stream- line this process. The idea is to save money on redundancies. Why should each member duplicate efforts on establishing their own best practices when the information may be out there already?
Hard Costs
The second step is taking a look at items which contribute to the hard costs of premium. Examples include analyzing your company’s Worker’s Compensation Modi cation Factor, loss history and identifying any loss trends. Doing this analysis will help us explain any irregularities in your loss history as well as current and future risk mitigation steps your company has or will take.
The more informed we are about all CFA members, the better we can address any areas of concern about your risk. We can then use these analytics to benchmark your company against your peers and provide informed guidance on what your peer group is purchasing to help you make more informed purchasing decisions. This is the most critical step of the process, and it is often where we lose the insured’s focus. Think about how much it impacts your overall business. An out of whack insurance program runs costly and may not be providing the benefits your company needs or worse, you’re buy- ing coverage you don’t actually need. This contributes to job costs which in the end could make your bid less competitive and ultimately hand that job opportunity over to a competitor.
After we package all of your information, including compiling your risk profile, company overview, loss trends and risk mitigation factors we will then set up a meeting with the underwriter to specifically discuss your company. As we said earlier, this is a tailored program to your industry, but it is also a tailored program to your company. It is during this meeting we will make sure the underwriter thoroughly understands all aspects of your company. Think of it this way, if you go into a store without a list, there is no direction, you may have a general idea of what you want but you’re bound to forget the eggs. We want to guide the underwriter as much as possible so we come out of the process with an insurance program that is not only competitive but addresses your company’s insurance needs.
The Approach
Enough about hard costs. Premium, this is where most brokers and insureds spend their time and this is where the CFA and Arthur J. Gallagher are going about it differently. We are taking enterprise risk management and utilizing those tools to bring your company the benefits, the same benefits large corporations have known about and have been taking advantage of for years. Remember the second step where we gathered your data? After further review, we will have identified your company’s risks and with the help of Gallagher Risk Services we will assist you in reducing, and where possible, eliminating that risk to your company. We have a vast amount of resources built into this program’s success. Gallagher Risk Services is developing CFA weekly toolbox talk topics, OSHA training, independent safety self-audit programs, online safety training and resources along with helping you to establish a sustainable return to work program. Proactively, Gallagher Risk Services has already completed a thorough review of several concrete foundation company’s safety manuals and created a best practices manual. We will continue to adapt this as we notice unique differences between company’s safety programs so as the CFA program continues to grow, those companies making it up will be the best risk in the industry. Over time, this will lead to CFA insurance program members winning more jobs due to a streamlined, optimized and cost effective insurance program. It’s all connected. We are also looking into ways to support companies in contract reviews and creating methods of pushback on some of the risk transfer the General Contractors are forcing down upon your company.
Have An Advocate
Inevitably, no matter how good we are and what we jointly do to manage your risks someone, someday will have a severe claim. When that does happen, we have dedicated claim advocates that specialize in Workers Compensation, General liability and Property assigned to the CFA Insurance Program. These individuals have backgrounds that range from an insurance carrier adjuster to the court room with legal experience in advocating on client’s behalf with the insurance carrier. Our risk advocate will work with you and the insurance company to resolve the claim in as mutually agreeable fashion as possible.
In the end, our philosophy is this: If we manage the soft costs, which so many brokers and insured’s alike ignore, we can make your company a better risk and ultimately more competitive.
ABOUT THE AUTHOR
Christopher Mowery is a Client Service Supervisor for Arthur J. Gallagher & Company. He has over ten years of experience marketing and servicing Construction and Risk Management accounts. For more information about this article, Christopher can be reached at Christopher_Mowery@ajg.com. More information on Gallagher can be found at their website www.ajgrms.com.
Tennessee Concrete Association’s Net Zero Building
The Net Zero project began as an idea in 2010 and grew out of conversations from TCA’s participation in the local U.S. Green Building Council (USGBC) chapter
The Tennessee Concrete Association (TCA) is located in Nashville, TN and serves the concrete industry statewide. TCA represents 70% of the ready mix concrete production in the state and also represents concrete contractors, suppliers and other companies who work in the world of concrete construction.
In 2008 TCA purchased property near downtown Nashville and established a campus for TCA. An existing building on the site was renovated to provide of ce space for the association and a portion of the nearly 2 acre site was leased to another business. TCA took the remainder of the site and began to turn a plain industrial site into a unique concrete showplace.
Most of this extensive transformation took place during the “Great Recession” but in the true spirit of the Volunteer State, TCA’s members stepped up to donate nearly $250,000 worth of materials and services over a four-year period to fuel the remarkable transformation from industrial to amazing.
Much of the transformation involved concrete atwork. Pavement on the site includes conventional concrete, roller compacted concrete and previous concrete. Hardscaping for the exterior courtyard, outdoor kitchen and the pervious pavilion includes some outstanding decorative concrete work representing stamped, textured, and exposed finishes, along with several different ways to produce color in and on concrete surfaces. The site also includes concrete fencing, custom concrete benches, a concrete countertop, cast-in-place concrete cocktail tables and numerous concrete bin blocks.
Our transformation also included concrete walls and buildings. Two small buildings were constructed early on to showcase concrete safe rooms (using insulating concrete forms) and a panelized concrete wall system. But our most ambitious project utilizes cast-in- place concrete walls and has come to be known as The Net Zero Building.
The Net Zero project began as an idea in 2010 and grew out of conversations from TCA’s participation in the local U.S. Green Building Council (USGBC) chapter in Nashville. Those conversations grew into an actual project team with volunteers representing architecture, engineering, landscape architecture, academia and contractors. The team evolved over time, but the consistent team members were architect Mr. Paul Boulifard (BOULIFARD), mechanical engineer Mr. Kim Shinn (TLC Engineering for Architecture), Dr. Heather Brown (CIM-MTSU) and Alan Spark- man (Executive Director, TCA).
The team set out to design a structure that could be constructed quickly in response to natural disasters to provide immediate shelter but one that could be expanded later to become a more
permanent residence. In many ways we wanted to create a shelter that would be the antithesis of much-maligned mobile homes that were sent in to deal with the aftermath of Katrina. To that end, the structures needed to be resilient (resilient construction was not yet a hot topic in 2010) to protect against potential severe weather events during the recovery period and beyond, they needed to be built with common construction methods and materials, they needed to be energy efficient and they needed be simple as well as versatile.
TCA agreed to provide the site and construction materials, and to manage the construction process to build the structure once designed. The rest of the team agreed to contribute their time and expertise to the design process, and to provide any needed assistance during the permitting and construction process. The entire team was commit- ted to using the design and construction process to elevate the construction industry’s knowledge and acceptance of sustainable design and construction processes and techniques utilizing concrete as the primary material.
Once the core team was assembled, the design process began with a formal chartering process to generate feed-back and ideas about such a structure.
Early in our initial work, Nashville experienced the worst flooding that anyone could remember (May of 2010) and suddenly Nashville was struggling with the aftermath of an intense natural disaster. Our firsthand experience with the many problems that remained after the flood waters receded made us think carefully about the type of structure that could not only survive a flood event in terms of structural integrity, but could also be restored quickly to be suitable for human habitation after the event.
Several concrete systems were evaluated during our design process, but the impact of the 2010
floods really led us back to the use of cast-in-place concrete for our wall system. Not only would well-constructed concrete walls survive most any flood event, the concrete walls would be easy to clean and sanitize after a flood so the structure could be quickly re-occupied without extensive removal and replacement of spoiled building materials like drywall or wood.
With that question settled, we needed to find a way to make cast-in-place walls energy efficient and that search quickly led us to the Thermomass wall system. Thermomass signed on as a part of our team and agreed to provide their materials at no cost to TCA as their contribution to the project. We settled on a 12” overall wall thickness that was composed of a 4” exterior thickness of concrete, 2” of extruded polystyrene insulation, and a 6” interior thickness of concrete as the primary structural component of our wall system. We placed the thicker concrete wall section inside the insulation envelope to increase the thermal mass and temperature dampening capability of our structure.
Actual construction started in July, 2012. TCA installed a turndown foundation slab with the help of two sum- mer interns and some layout assistance from Dr. Marcus Knight and Jon Huddleston from the Concrete Industry Management (CIM) program at Middle Tennessee State University (MTSU).
A TCA contractor member with experience in poured wall construction (but no experience with Thermomass) was hired to complete the concrete shell of the building. The crew quickly picked up on the installation of the Thermomass system and construction of the foundation walls proceeded quickly. Next came the installation of a cast-in- place concrete floor that received a texture-skin finish and then the walls were continued up to the roof line. Care was taken to maintain the integrity of the insulation envelope such that the walls were insulated from the below-grade footing to the roof with no interruptions.
The main level walls were placed using Self-Consolidating Concrete, and then a 6” thick reinforced concrete roof slab was placed to complete the structural portion of the building. The insulation envelope was extended to cover the 6” roof slab (3” of extruded polystyrene was used on top of the at concrete roof) so the thermal mass of the concrete in the roof was also inside the insulation envelope.
From this point, a conventionally framed single slop metal roof system was installed with the roof angle optimized for solar exposure. A small solar (1500 watt PV) system was installed to provide lights and plugs for the build- ing. The upper portion of the ‘Solar Tower’ was completed using conventional masonry construction that was core-filled and the same roof system was used to cap off the tower.
The south-facing side of the Solar Tower was dedicated to glazing and vents. The glazing intentionally allows the top of the Tower to heat up and makes it the hottest portion of the entire structure. The hot air is then vented to the exterior through the vents that remain open year-round. The hot air that exits must be replaced so the design takes advantage of that natural ventilation to bring fresh air into the structure without any mechanical assistance.
In addition, that fresh air supply was constructed so that the air enters the building at the bottom of the 4’ high foundation level and then must ow through a ‘conditioning maze” that is about 150 lineal feet. The floor of the maze is 4’ below grade and the floor temperature stays around 60 degrees year round. Exterior air is tempered from the exterior ambient temperature before it enters the living space above the foundation level. The combination of this air-tempering strategy with the large amount of thermal mass inside the insulation envelope maintain the interior temperature of the building between 50 and 80 degrees in all but the coldest winter temperatures. The structure has been able to maintain a 25 degree temperature differential (from ambient) even on the coldest winter days in January and February.
The Net Zero building is a showcase for resilient, sustainable, energy-efficient construction as well as a showcase for cast-in-place concrete walls and it is a fitting crown jewel for the TCA Campus.
ABOUT THE AUTHOR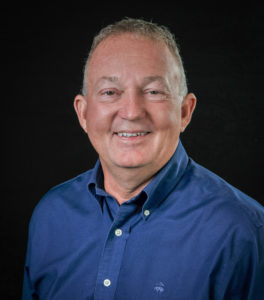
Alan Sparkman is the Executive Director for the Tennessee Concrete Association. He served The Aberdeen Group as Director of Industry Relations from 1995-98 before taking his position at TCA. He has been involved with the Construction Industry Management program since 2010 and maintains an active teaching and training schedule across the United States. For more information, contact him at asparkman@tnconcrete.org.
Three New Leaders Take Up The Challenge
Meet new CFA Directors Ken Kurszewski of Hottman Construction Company; Lindsay Castles of GMX, Inc.; and Mark Irving of Irving Equipment LLC.
The march toward CFA Convention held each year in late July or early August, includes an opportunity for changes to the leadership of the Association. Over more than forty years leading this industry, a wealth of energy, expertise, passion and balance has been brought to the collection of individuals tasked with steering the organization. This leadership has led in times of large and sustained growth through the years of feast as well as times of stability required during recession.
Author, Jim Rohn has said, “You must take personal responsibility. You cannot change the circumstances, the seasons, or the wind, but you can change yourself. That is something you have charge of.” The CFA Board is a reflection of this quote both in its pattern of influence and endurance as well as in the legacy that has been left behind. No different is this year than in years previous when the new Board members, taking over at their first meeting this past month in Denver, met with CFA staff to identify their goals, hopes and influences to reaching this point in their career. Jim Baty, Executive Director for the CFA welcomes Ken Kurszewski of Hottman Construction Company; Lindsay Castles of GMX, Inc.; and Mark Irving of Irving Equipment LLC during orientation as a way of helping you get to know each of them as well. Ken was elected at large by the membership for a 3-year term. Mark and Lindsay were elected to serve as representatives from the Associates’ Council with Mark receiving a 3-year term and Lindsay a 2-year term.
Jim: As we prepare to head toward your first meeting in Denver I’d like to know a few things about you that can help our members identify with your leadership. Each of you have considered participating at the Board level in the past, what would you say inspires you to volunteer your time and attention to the CFA at this moment?
Ken: Hottmann Construction has been a member of CFA since 2002 but I really wasn’t active until just a few years ago. I was overwhelmed with the members of the Association and their willingness to share information. This inspired me to become even more active and volunteer to serve on the Board.
Lindsay: That is an easy question. The CFA is a great organization that is ultimately driven by the people that are committed to its success. I am excited for the opportunity to spend more time around those great people for the common cause of advancing foundation walls in the residential building industry.
Mark: My inspiration to give time to the CFA is seeing all the generations before me that have given so much. I think it is “our” part to keep a legacy going.
Jim: There is a resounding consistency with your responses to what I’ve experienced from those directors that have come before you. I know you each have such leadership in mind when you think of the CFA Board. What is the very first thing that comes to your mind when you hear the phrase Concrete Foundations Association or think of the CFA?
Lindsay: Close Knit Group
Ken: The first thing that comes to my mind is the summer convention and how much I have learned at that event, both from the seminars and the other attendees.
Mark: What comes to mind is, when I heard long time CFA members say; “I can remember when we used to talk about pouring concrete at these meetings. Now we talk about Worker’s Comp., DOT compliance and sexual harassment. All good stuff. A company has to really keep up.” I think the CFA is doing an excellent job of “keeping up” and actually leading the cast in place industry with great technical articles and great real-life information a company can use and needs.
Jim: Ken, you mention Convention and its impact on you and Mark, you also mention the focus that has evolved over time within the rich heritage of this organization. What CFA event would each of you consider as the one that has meant the most to you or that you got the most from when it comes to investing in your company?
Mark: Honestly, I cannot think of one special event that stands out as it seems that each event gets more interesting and get more out of each one (because I put more into each one).
Ken: The 2013 summer convention in Albuquerque was the first event that I attended. This, as I mentioned above, was what made me realize I need to be active in the association to help me grow my business and my knowledge.
Lindsay: The summer meeting in my mind is the best opportunity to really experience the CFA. I enjoy it the most.
Jim: Membership in an organization seems like an easy thing but we know it challenges the average industry professional. Leadership is yet another step above and beyond that measure of commitment and comes at a definite price to both company and individual. I hear you each responding about the impact you’ve felt already from involvement that you are taking to a deeper level. Is there any specific area of your business that you believe the CFA has influenced, inspired or impacted?
Ken: We have made several changes over the last few years. I love coming back to Wisconsin and sharing ideas with the rest of the team. We have made changes in equipment, safety policies and organizational structure to name a few. Many of these changes and ideas have come from talking with other members.
Mark: Hands down—Safety. The CFA has created so much awareness for the safety of employees on the job from running better equipment to knowing what hazards are around the site and dealing with drug use.
Lindsay: We have had the opportunity to interact with many members of the CFA to advance the cause of the below grade waterproofing industry. It has been a great pleasure for GMX to be involved with the membership and develop lasting relationships that will endure many years to come.
Jim: So, now that you have found yourself to a seat on the Board, can you identify two or three things that you would like to see happen within the CFA during your first term as a Board member?
Lindsay: I would love to see the CFA participation grow with contractors placing a higher value on being associated with the CFA.
Mark: Some of the things I would like to see are: increased membership and getting more existing members to CFA events, maybe by personal invites from non-competitors.
Ken: The main thing for me is to continue and expand the collaboration between members, whether it is at the convention or outside of it. Another is to continue to build the membership and attendance at the conventions. Oh, and get golf back into the summer convention!
Jim: Gentlemen, the CFA is in for some great things through the addition of your leadership and your passion for this industry and this Association. I want to leave our readers with something tangible to make sure they don’t think this is written in a vacuum or that you’ve signed your name to a list of responses. So, I’m going to toss out a favorite subject or item and want you each to respond to the first thing that comes to you. Maybe this will strike up an extra conversation or two the first time you are with other members. Your responses are shown along with a quick bit of biographical information. Thanks for your time here in Denver and for the contributions you are already making on behalf of not just the hundreds of members of the Association but the thousands of contractors out there reading this and benefitting from the leadership of this Association.