Elevating Board Form Concrete to a Marketable Aesthetic
If the Great Recession has taught us anything as a company, it is that a concrete construction company can be extremely resilient when everything is on the line.
In order to be resilient, our company had to be creative and apply ourselves to finding work and finding uniqueness any way possible. Out here in the West, we noticed an architectural trend in housing toward what was being referred to as a “contemporary aesthetic”. This challenged us to see our ability as not just a concrete contractor but to apply our craftsmanship and generate a marketable product.
Now, whether or not a concrete contractor really knew what contemporary aesthetic meant was somewhat beside the point. What we saw changing in architecture was that contemporary was a trend to save cost. The designs were simple, straight lines and crisp, clean forms. Gone were the high pitch roofs, eyebrows and extensive elevating forms. Roof lines had become flat and simple. It seemed the architectural change offered ways of achieving structures with less cost because land prices recovered quickly. Builders and developers condensed forms and simplified designs to make housing affordable in our market.
As the architecture changed to the contemporary or more modern style, it was natural that concrete would participate and in some ways return to being featured. While concrete would be more expensive, it had important value among three timeless, organic and natural elements (wood, stone and concrete) that elevated the sturdiness of housing or grounded it when combined with steel and glass. We found owners began developing an interest in a combination of concrete and wood in a “rough” look for their homes, desiring a board form concrete finish. We started with a few small board form jobs during the deepest parts of recession in 2008 to 2011. These jobs gave us some experience and opened our minds to the possibilities. Utah then recovered more quickly than some regions of the country and all of a sudden we saw a number of jobs proposed with a lot of above grade, board form concrete walls. Not all were full or even significant amounts of board form. More than a few of these projects were patio or retaining walls where the board form anchored the style of that specific space.
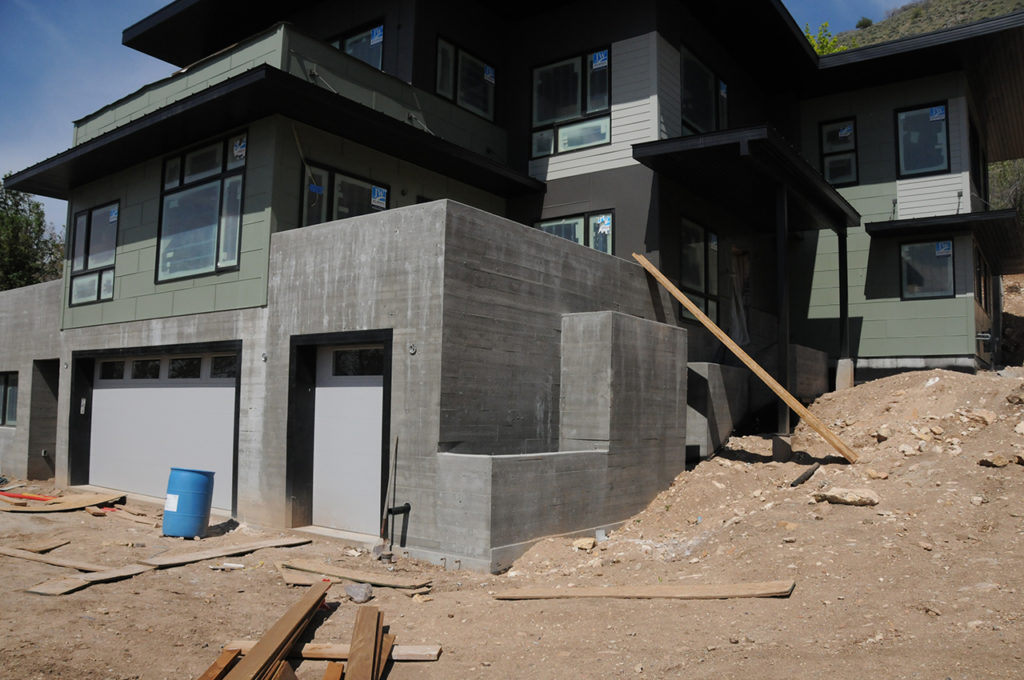
Our first big job was designed by an architect from Seattle, Washington with considerable experience designing uninsulated, above-grade concrete having an exposed architectural finish. This look can be a real challenge and after several mock-ups, which we have come to realize are extremely important on every architectural wall, we decided to go with a liner of 6 in. wide ruff-cut cedar.
We looked into information from ACI and talked with local consultants before deciding to pretreat the cedar with a cementitious covering to draw out the sugar in the wood. Our research identified that natural sugars in the softer parts of the wood grain act as retarders to the hydration process. The cementitious covering was intended to pull those sugars out and leave the wood neutralized for our casting operation.
Once the project started, however, we realized the size and scope of what we were dealing with and underestimated the amount of cedar we would need. This project had board form in the site work, three fire places each thirty-five feet tall, retaining walls and enclosure walls. Needing additional wood, we didn’t have the time to pretreat cedar so we went forward with untreated wood. The resulting finish between the treated and untreated cedar showed zero difference. We saw nice horizontal lines and a crisp look with both. We didn’t get a lot of wood grain but we did see clear expression of the knots. This remained confusing to us with all the warnings of retardation due to sugaring. I deduction was it may have been due to the form release we use. We strongly suggest mocking up your finish before attempting it without pretreatment or some other precaution against the sugaring potential.
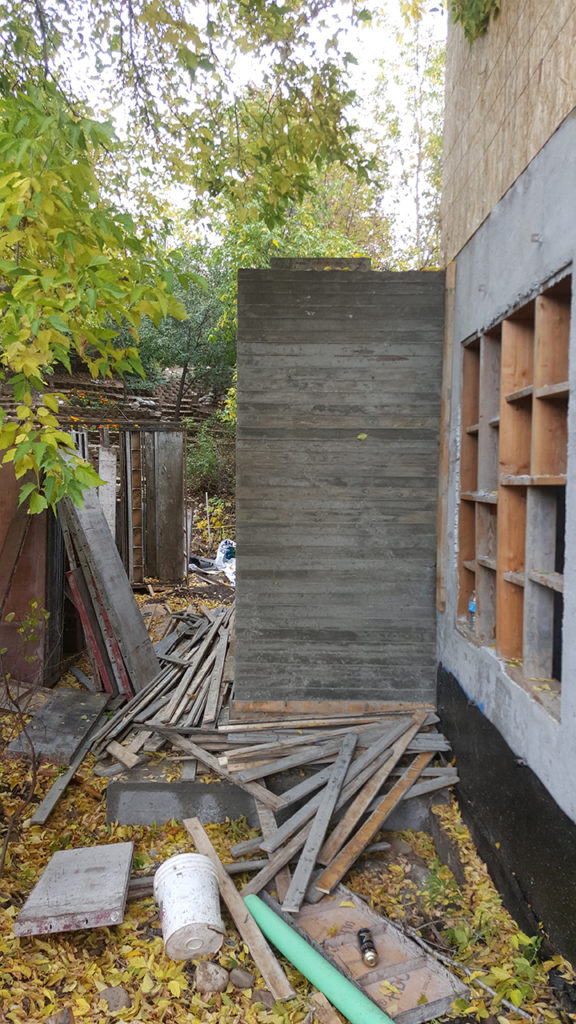
Designing the Mix
The mix we developed through the mock-up process to minimize bug holes consists of a 7-bag mix with 30% fly ash replacement. We added a mid-range water reducing admixture to increase flowability and lower the w/ cm. This permits us to place concrete at a 6 in. slump (+/- 1 in.), which we test out of the truck. The mix does tend to get a little hot so when the ambient temperatures are above 60 ̊F we add a delay-setting admixture. Over the last four years this mix as proven consistent and has yet to disappoint us in its workability or durability…other than the heat it generates. There is an extra cost of this design mix but the trade- off to performance in the architectural finish and placement consistency is worth the premium.
Attaching Board Form to Aluminum
One of the biggest questions that came up was the best way to attach the cedar boards to our forming system. Most of the concrete contractors we know use aluminum forms, like we do. Having access to conversations with others was important for our research and this network helped us come up with two plausible options.
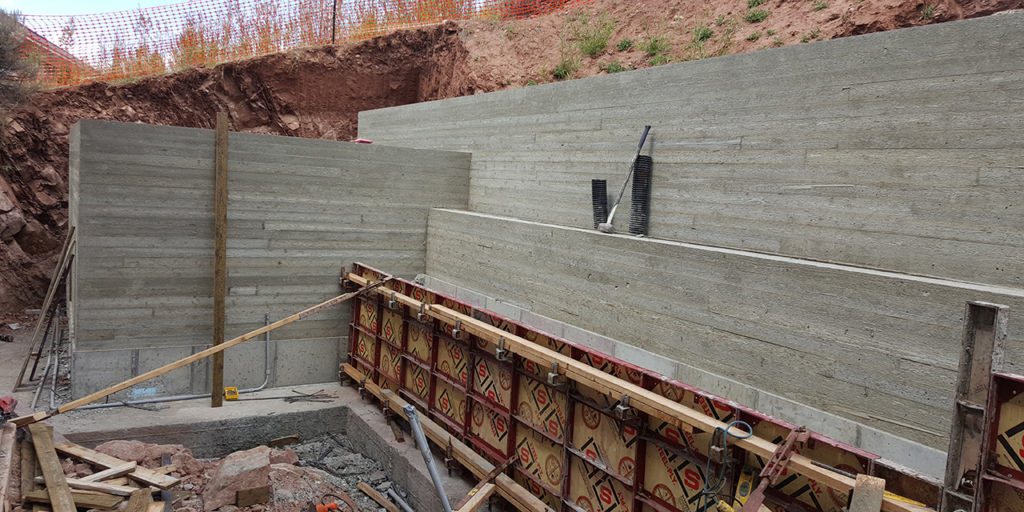
At first we tried using self-tapping black screws. These are your common, inexpensive drywall screws and they worked well enough. However, we found that the screws were very difficult to locate when it came time to remove them and the liners.
We received a suggestion then to try a very sturdy steel screw called “Remove Right”. This screw as a 1/4-in. hex headed end that is painted orange, making it easier to install as the head is less likely to strip and doesn’t snap off from torque. This screw was far easier to find, remove and then reuse.
We also discovered through our challenges that you need to consider the form tie. With our aluminum forms, we needed a tie that has a 1 in. break-back notch. We talked with the manufacturers and found we could order them. We use a multi-tool to cut a slot in the boards to accommodate the tie and keep the concrete crisp around this penetration.
Moving Forward
One of the challenges we faced with the acceptance of our board form finish was the lack of wood grain. We knew we would encounter owners that would want to see more grain expressed in the finished concrete surface. We started by distressing the grain using a wire wheel brush to remove the softer wood from the grain. The harder wood was left as raised areas and the grain had almost a burnished surface. It worked well enough, but in the end we decided that it took considerable time and still didn’t give us the consistency. Depending on the attention we gave the wood, we would end up with additional unnatural lines or wearing.
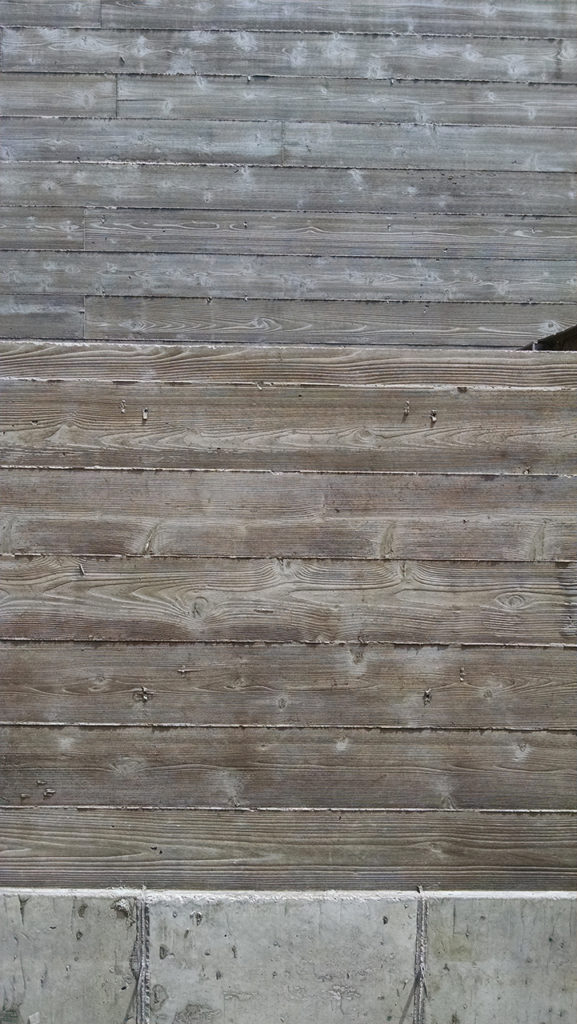
Our current solution is to use a weed burner over the entire board surface. We then use the wire wheel to take off the charring. This method has proven to produce the most beautiful wood grains with highs and lows. We then seal the burnt cedar with a standard wood sealer. This has provided us the actual control of the sugars in the wood and eliminated the expensive and time- consuming step of pre-treating the wood with a slurry mix. The sealer has also helped us more consistently reclaim the wood liners for multiple uses.
Basic Costs
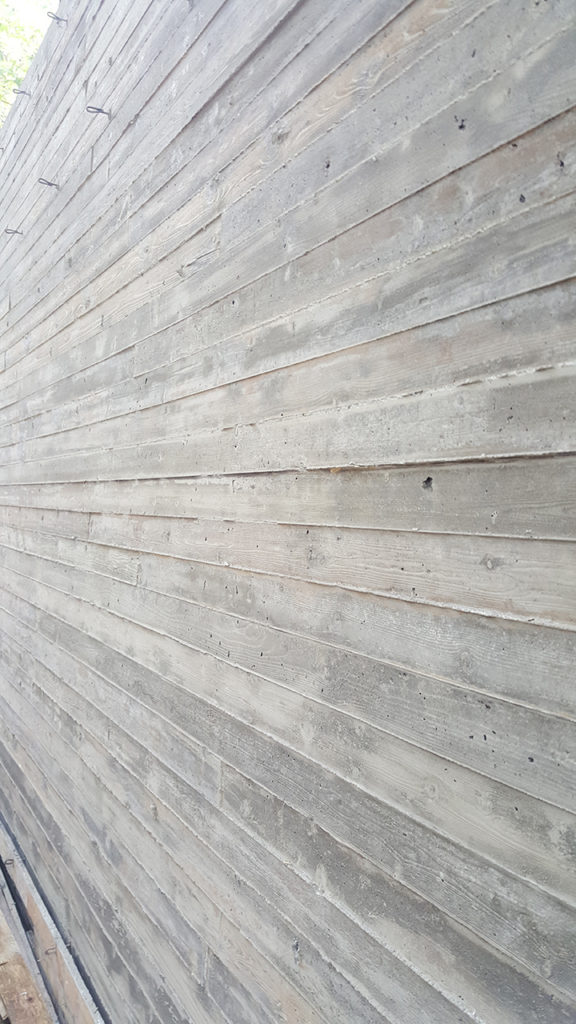
As a whole, the experience is our major investment. For materials we end up with about $2.50 per square foot for the cedar. We have mastered the reuse of the wood such that the cost to prepare the boards by burning, char removal and sealing is very minimal to the cost of the wall, although you would want to figure it in that first start-up, perhaps a $1.00 to $1.50 per square foot. This gives us a rough board liner cost of about $4.00 per square foot. Compare that to some of the labor costs for installing boards or for multi-use liners.
We believe the patterns and the results are speaking well for the time and energy we have invested in carving out this market niche or rather a response to the architectural trends of our market. For more information, give us a call, we’re proud to be part of the Concrete Foundations Association and have benefitted from talking through some of this development with several of our peers along the way.
ABOUT THE AUTHOR
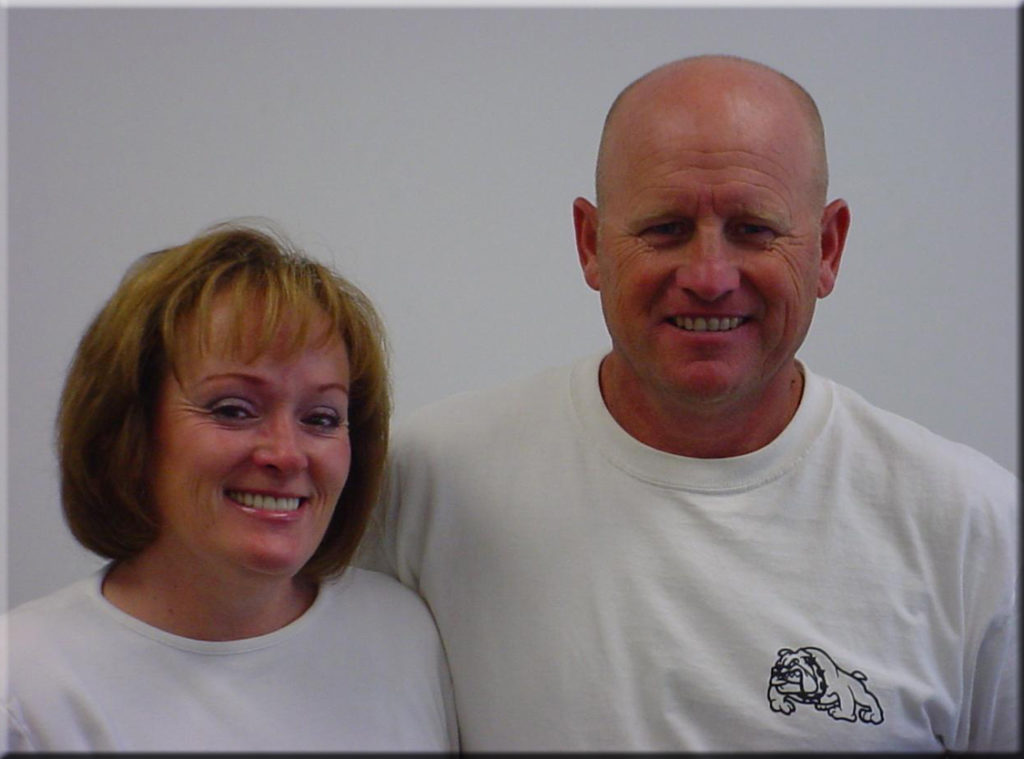
Kirby Justesen and his wife Pam reside in the Salt Lake City, Utah area where he is an owner at SCW Footings and Foundations. He is a leader in the concrete industry, now serving for his second time on the Board of Directors for the CFA and is a voting member of ACI 332, the residential concrete committee for ACI (www.concrete.org). Kirby has served as the chair of the CFA Technical Committee and has been part of the development of the three CFA Standards published to date.
