Concrete Reinforcement Changing
THIS ARTICLE RECOUNTS THE PROCESS CONDUCTED BY ABI CORPORATION, STARTING IN SEPTEMBER 2103, TO INTERNALLY VALIDATE THE MERITS OF USING HELIX MICRO REBAR IN PLACE OF REBAR IN BASEMENT FOUNDATIONS WITH THE GOAL OF REDUCING LABOR.
The requirements to pass the test were simple: the process must save labor and the quality of the finished product must be as good or better than a traditionally reinforced wall. The testing was not scientifically certified and the information in this report is simply a history of the evaluation of the product. It is important this information not be used as a guide or a substitute for the information provided by Helix or a qualified structural engineer.
SMALL SCALE TESTING
Small scale testing began by casting samples that would be representative of 8” nominal wall sections that measured 26” long by 14” high by 7.5” thick. A 3000lb compressive strength concrete mix was used. After 28 days of curing time, the samples were laid flat in a hydraulic press. Three inches on either side were supported and the rest of the sample spanned approximately 20 inches. Pressure was increasingly applied in the center of the samples until they failed.
SAMPLE A was plain concrete. The sample failed at 19,980 pounds of pressure.
SAMPLE B had one #4 rebar floated into approximately the center or the sample. The concrete failed at 16,218lbs of pressure and the rebar began to yield steadily until 22,018 lbs (~0.5 inch crack width). Then it dramatically lost its ability to carry load and the crack quickly opened ~2 inches.
SAMPLE C had two #4 rebar floated into approximately the center. An audible pop was noted at 13257lbs when the concrete failed on the tensile (bottom) side of the sample and a visible crack began to form.
Complete cross sectional failure of the concrete occurred at 21,939lbs and the rebar quickly began to yield to the pressure. The yielding #4 bars were able to maintain a load reading of about 14,000lbs until the crack width opened to approximately 0.05 inches.
At that point a metallic snapping sound was noted and the pressure gauge dropped to 4598lbs and the crack started to open must faster.
SAMPLE D had 9lbs/yard of Helix 5-25. No rebar was used. Under rapid loading the sample failed at 21,705 lbs of pressure.
SAMPLE E had 9lbs/yard of Helix 5-25. No rebar was used. The load was applied much slower than sample 3 to try and detect the yielding of the Helix.
The sample failed at 17,205 lbs of pressure.
Dan Bromely the President of ABI Corporation said, “This test convinced me to move forward with the wall.” The wall he was referring to was a full-scale basement foundation section he poured behind the corporate headquarters located in the South East suburbs of Kansas City, Missouri.
THE FULL SCALE TEST WALL
The materials for the test started as 3000 psi compressive strength mix with 9lbs per yard of Helix 5-25 added at the batch plant. Water was added on site to achieve a 9 inch slump resulting in an unknown, but certainly much lower compressive strength. Aluminum Forms were then used to cast an 8 inch nominal wall, 9 foot tall, 16 foot long with 90 degree turn sections at each end. Other than corner steel, no traditional rebar was used in the wall, only Helix twisted steel micro reinforcement.
The wall was poured and the formwork was removed after 18 hours. It was immediately evident that an 8” long vertical shrinkage crack formed starting at the embedment of an anchor bolt and running down the wall. ABI experts were certain the shrinkage crack was the result of the high ambient temperature and the water added to the concrete mix at the site. This type of crack would have formed in the plastic phase of the concrete no matter what reinforcement was used.
The wall was allowed to cure 7 days and then backfill was placed against the wall. The method of backfill is important because the 12,000-pound loader was run parallel and close to the wall to add additional dynamic and static compressive loads to the wall. Ultimately, 100% unbalanced backfill was achieved with no evidence of change in the wall (see image below).
A hose was placed on the backfill near the wall and water was allowed to saturate the backfill for 7 days. Not only did the backfill become saturated, the soil at any point within 15 feet of the test wall was saturated to a depth of about 8 inches. Again, there was no obvious indication of change in the wall.
The next phase of the test likely generated the most severe loading of the wall. After allowing the backfill to dry, a ready mix truck with 10 yards of water and gravel, weighing approximately 70,000 pounds was backed up to the wall to simulate the pouring of a basement floor. In addition to the weight of the truck, the rear tires of the ready mix truck were spun against a compressed layer of approximately 10 inches of backfill that was trapped between the tires and the wall. Once the truck was stopped, the drum was rotated at high speed and abruptly stopped and rotated in the opposite direction several times. The shifting material and changes in drum direction caused the truck to heave back and forth transferring unknown amounts of energy to the soil inches from the wall. Neither the heaving of the truck nor the simultaneously applied weight and the pushing force of the tires created a visible change in the wall (see image below).
The final active phase of the test was backfilling gravel over the wall with the same 12,000 lb. loader used earlier in the test. The loader with full buckets of gravel was driven up to the wall such that the tracks pushed against and climbed on top of the wall (see image below)
The wall section is now 7 months old and has gone through the 2013-14 winter. The foundation on what would normally be the interior of the basement has been completely exposed since it was poured. There is no doubt the ground froze under the footing so an unknown amount of force was applied to the wall from frost heave. The original 8 inch long shrinkage crack has grown to a 48 inch long tight, but visible crack. During an inspection of the wall on March 18th, 2014 Dan Bromley commented,“That’s nothing” while observing the hairline crack indicating there it was nothing to be concerned about with regard to the integrity of the wall (see image below).
MARKETING STRATEGY
After seeing the results of the in-house testing, ABI was convinced they could offer better quality foundations by using Helix. The next step was to develop a marketing strategy and present the idea to their builders. Like most good marketing strategies, the ABI message is easy to understand and highlights the advantages of the product. Below are the ABI reasons to promote Helix:
- After extensive research and in-house testing we feel that it improves the quality of our foundations.
- It will help us be more productive. We can do more with less people and will help us mitigate the effects of the housing labor shortage as this market grows.
- Safer
- As a builder there may be a marketing opportunity to homebuyers; a chance to promote a better foundation product with the synergistic combination of waterproofing on a Helix reinforced wall.
DOSING HELIX
There are several important considerations when planning how to place Helix into the ready mix truck. Helix comes in 45lb boxes. To achieve a 9lb per yard concentration in a 10 yard truck two boxes (90 pounds) have to be added to the truck. Using the example of a basement that requires 60 yards of concrete, it would require six trucks of concrete and a dozen 45-pound boxes. In order to get the material into the truck, two important tasks have to be accomplished. The first is lifting the Helix to the level of the hopper and the second is a sifting the material so that no clumps are introduced into the truck.
ABI adds Helix at the concrete plant where the material can be lifted to an elevated platform with a forklift. Once the boxes are on the platform, one worker to stand safely with the hopper at waist level and sift the material into the trucks. As the number of projects using Helix increases they intend to look at automated dosing equipment.
Field dosing is an option as well, but can be physically challenging. To experience the worst-case scenario, Dan Bromley personally climbed the truck and sifted the material through a manual doser. Climbing a rear discharge truck without adequate truck mounted work platforms is the least desirable method. It is physically taxing and has a moderate safety risk for the worker. Front discharge trucks with safe working platforms provide for a better situation, but the material still has to be lifted to the level of the platform.
Methods of getting the helix into the truck are really only limited by ones imagination and mechanical ability as evidenced by the videos posted online. Do to an apparent lack of availability or unreasonably high cost, most dosing devices have been self- built by the companies that use Helix. Some are vibrating hoppers with blowers, some are vibrating table with chutes. One off-the-shelf solution may a fiber conveyor like the one available from Portable Conveyors (800) 456-7687. But the conveyor below still lacks a vibratory screen or tray to sift the material before it goes into the hopper and it is more expensive than a most of the homemade solutions.
PRODUCT ACCEPTANCE
In order to gain the support needed for technical acceptance in the Kansas City, Metropolitan Area, ABI thought is was important to have the involvement of well- known residential engineer. Therefore, they contracted Apex Engineering to prepare
drawings with Helix as an alternative to traditional rebar. Last fall, Luke Pinkerton, the President and Chief Technology officer for Helix was in town for a presentation at Kewitt and he was able to come to ABI and meet with Dan Bromley and Clayton Hess of Apex engineering. After that initial meeting, Apex did an extensive review of the science behind Helix.
Apex engineering was able to review a complete engineering report prepared by Helix based on a set of plans for a typical Kansas City foundation design. They were also able to review the documentation on the testing done to prove Helix’s ability to serve as a structural concrete reinforcement. The bulk of that information is now available in a single report named the ER-0279 Report.
Once satisfied, they prepared sealed drawings with notes for the use of Helix as an alternative. Unfortunately, the process took more than 2 months.
In Helix’s 12 years on the market it has been mostly confined to large commercial projects. Those projects are mostly engineered projects inspected by the engineers who designed them and the responsibility remains with the engineer. City inspectors however normally inspect residential construction and they rely on city codes that vary from city to city. The ER-0279 report doesn’t require an inspection to be conducted when using Helix. It only requires that the dosage be annotated on the batch ticket and that a written copy of the batching procedures to be on
hand when Helix is added to concrete. Since there isn’t anything to inspect other than the batch ticket annotation and the presence of written dosing procedures, it will likely present some city building departments with an unknown situation. The ER 279 report does however provide information about verification of dosage. Anyone who wants to make sure the correct amount of Helix is in the mix can take sample amounts of plastic concrete and wash away the cement, separate the Helix, from the aggregates and weigh it.
It’s A New Dawn, It’s A New Day…
Turning the calendar to 2015 has ushered in a great deal of excitement and anticipation here at CFA headquarters. First of all, I recognize that those of you reading this are in one of two camps; the many knowledgeable individuals working for CFA members that have relied on Ed Sauter for a great many years; or a far greater number of individuals working for companies that have yet to experience the powerful advantages that are found in the Concrete Foundations Association.
I am proud to now be serving those of you in that first camp as Executive Director. Since coming on staff in 2001, this Association has demonstrated incredible resilience, unparalleled passion and a hunger for the future that is hard to do justice with words. Your actions are often so much more telling. Ed Sauter has been a tremendous leader and mentor to this industry and this Association. Taking the reigns from the passionate and talented directors before him, Ed managed a period of growth for the CFA that has led to an enviable collection of research, support and prestige. This Association has now placed their trust and future in my hands, hands trained by Ed and prepared to lead the next generation of cast-in-place concrete greatness. I’m up for the challenge and prepared to give you everything I have… are you?
I remain proud of the opportunity to continue serving this industry, and therefore those of you in that much larger second camp. Whether you are an owner of a concrete contracting company or a key individual in a project management role, reading this message you have an opportunity right now to make the most convenient and timely investment in your future. In fact, this investment is one that won’t put your company at risk and it certainly isn’t a strong influence on your cash flow. It will, however, deliver a powerful network of potential and begin doing so the moment you commit your first year’s dues. Each and every one of you can and should have the opportunity to engage your peers and be supported by a powerful network that works every bit as hard as you do.
I possess an endless energy and passion for this Association and this industry that has partly come from the fourteen years of service I’ve already given you and partly for the genetic code found in my wiring. I have much to convey to you, together we have a long way to go and a lot of potential within our grasp. We haven’t even begun to dream our full potential yet. Michael Bublé is credited with that lyric, “It’s a new dawn, it’s a new day, and I’m feeling fine.” Well, unlike Michael, I’m not just feeling fine, I’m feeling charged up. Enjoy the pages of this magazine. They are built for you, each of you. I’d like to hear from you and be challenged to know your needs, your passions and your interests. That’s how I can best serve you, whether you are a member of this great Association or a member of the industry that is benefitting tremendously from the work we are doing. There is always room for you here.
James Baty
How Do We Stack Up?
If your company is like mine, right now you see everything turning up. The weather is turning and the forecast for Spring is starting to look real. We see jobs breaking and more pushing toward our involvement. Better yet, we know the struggles that have been faced over the last four months are all but gone and we can return to working at a straight pace with consistent product, conditions and contracts.
But is your company also like mine, with family members involved with you, even the next generation beginning to desire involvement? Can you foresee the problems coming in ramping up the labor force to handle the increased workload because the job market is saturated by unmotivated and “entitled” persons? Are you finding it a challenge to determine the best way to cycle out or recycle some of your overused equipment, the things you’ve been making due with and have held on to far to long? There is a pretty good chance that involved in this industry you can say yes to most of these questions in some way or another. What I know is there isn’t that much different between our companies, except perhaps one big one. We’re a member of this Association.
Having missed out on World of Concrete this year, I’m really looking forward to what this summer brings. Our convention will take place in a spot I know my family is looking forward to visiting and I’ve seen that some of the answers to my questions above are planned in the education that will be offered. As owner of this company, I draw a lot of my strength from the conversations and the network access I have found here. It isn’t always easy and there are some tough decisions that have to be made in order to achieve consistency when it comes to knowledge and experience. But that is on me, the peers I’ve met and continue to meet new each and every month through the CFA have become some of my most valuable assets.
It is also now March Madness and before you let the madness of the construction season grab a hold of you, let me just encourage you to set two calendar dates now. One date needs to be set immediately to join the CFA. It is the best $600 investment you will every make in your company. The other date is July 23-25. CFA Convention is the largest annual and dedicated gathering of the cast-in-place concrete contractor industry. I’d like to meet you, introduce my family and my fellow members, my friends to you and most importantly learn from you.
David Martinson – Martinson Construction
“Damp Rising”
As published in Concrete Contractor Magazine.
Question: I have a homeowner that wants me to put a poly sheet over the footing before I begin forming the foundation wall. He has read that water can migrate up through the footing into the wall and create mold problems for his home. Is this accurate? I’m concerned about the connection of the wall to the footing.
Answer: One of the current en vogue issues in the residential concrete industry by owners and designers is that of a phenomenon known as “rising damp.” This condition, described as the transportation of sub-grade moisture surrounding a house foundation through the footing and concrete wall and into the living space, has become a frequent technical inquiry at CFA headquarters.
“Rising damp is a European phenomenon produced from stone and block foundations rendered with stucco or plaster,” states Brent Anderson, P.E. of BDA Associates in Minneapolis, Minn. “Those foundations are tremendously hydrophobic, and permit large volumes of moisture to enter from the surrounding soils. They naturally move toward the warmer, dryer condition of the living space and then affect the adhesion of the plaster to the structural wall. Owners then have to remove the failing plaster and reapply, only to see the same thing happen in a few short years.”
Anderson, a long time champion for the quality of residential concrete, presented the subject of waterproofed concrete during the ACI 332 – Residential Concrete full committee meeting in Washington DC last fall. In attendance were many CFA contractors volunteering their time to help direct intentional transition of smarter codes and standards for residential concrete.
“It would take approximately 4,000 years for water to move through six inches of properly designed and delivered concrete,” notes Anderson. “Therefore, where is the concern for rising damp in today’s U.S. residential market? The best things that ever happened to residential concrete are the concrete pumps and conveyors. The design of concrete to take advantage of their efficiencies delivers an exceptional mix design to your footings and walls. It then becomes an issue of ensuring the natural cracks that happen in concrete are controlled (proper reinforcement) and/or the water prevented from reaching those cracks (effective waterproofing system).”
You should take caution when considering placing a poly sheet as a barrier between the footing and wall. This sheet can place the foundation wall at risk for movement during backfill, if it is not properly braced. ACI 332 requires all foundation walls to be connected to the footing either by a dowel at 24-in. on-center or a keyway. If the wall is doweled to the footing, the moisture barrier theory cannot be 100 percent effective due to the perforations, assuming it wouldn’t tear during forming and removal in the first place. Instead, a better recommendation is to work with your customers to help them see the complete system that actually controls moisture infiltration beginning with the quality of your concrete. If the concern remains, a spray-applied membrane that contains an aggregate for surface roughness would be a far better suggestion, although this would be a suspender to an already strong belt.
Jim Baty is the Executive Director for the Concrete Foundations Association after having served as Technical Director since 2001. He is currently chair of ACI 332 and a voting member for ACI 306 with priorities of establishing better guidance and structure for residential concrete construction. For more information on this topic, contact Jim Baty at jbaty@cfawalls.org. Find out more at www.cfawalls.org.
For Sale: Used 9-ft Western Flagship Elite
This equipment is being offered for sale by a CFA member in Ohio.
For sale is a used set of 9-foot, Western Flagship Elite forms. This is a complete set with many fillers, baskets, pinlocks, hinges and more. Review the complete inventory list for more details.
Contact Matt at (419) 286-2086 for more information, condition and pricing interest.
Monarch Materials Group Names New President
January 19, 2015
ADEL, IOWA – Monarch Materials Group names new president.
Monarch Materials Group, Inc. (Monarch) named Dan Higgins as its new president today. Monarch manufactures residential, basement window egress systems in Adel, IA and Englewood, CO and distributes them throughout the United States.
Dan joins Monarch having extensive experience in the concrete construction industry. His industry experience began as a regional sales manager with ConSpec Marketing and Manufacturing in Kansas City, KS. He also served in multiple roles for Dayton Superior Corporation, a manufacturer of a broad range of concrete construction products and services. Most recently, Dan was with a Pella Window & Door distributor as general manager and director of sales. Prior to this experience, Dan was with Pella Corporation helping lead business development.
Dan is a veteran who has served multiple combat tours in Afghanistan and Iraq. He has a Bachelor of Science Degree in Civil Engineering from the United States Military Academy at West Point, NY and a Master’s Degree in Business Administration from Rockhurst University in Kansas City, MO.
Dan and his family currently reside in Pleasant Hill, IA.
A Day in the Life of a Leader
CFA Professional Awards
CFA RECOGNIZES MARY WILSON OF MICHEL CONCRETE WITH M.V.P. AWARD
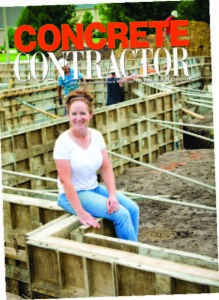
Cover from Concrete Contractor Magazine’s June/July 2011 issue featuring the diversification efforts of Mary Wilson and Michel Concrete.
Sonny Newman, president of contract manufacturer EE Technologies was quoted in Business News Daily in defining leadership as “influencing others by your character, humility, and example. It is recognizable when others follow in word and deed without obligation or coercion.” This quote is a perfect representation of the parameters considered when the CFA Board of Directors awarded Mary Wilson of Michel Concrete in Springfield, Illinois the Most Valuable Person award this past summer.
The CFA M.V.P. award was developed to recognize the significant contributions of specific individuals toward the advancement of the Association’s mission and purpose. This award was first presented in 2004 to Brad Barnes, P.E. for this leadership and authorship of the ‘CFA Cold Weather Research Study and Final Report’. Brad passed away this past year leaving behind a legacy of confidence in the performance of concrete walls during cold and freezing conditions. Current CFA President, David Martinson of Martinson Construction in Waterloo, IA states, “In short, this M.V.P. Award is presented to an individual who has given generously of their time and talent in helping the CFA become the successful organization that it is today.”
It is likely that Mary’s name is not unfamiliar to you. She has been extensively involved in much the CFA has been about over the past six years since joining in 2008. Nearly as soon as she brought her company into the CFA network, she began taking on the challenges presented to her. Much of this has come in the way of asking questions of interest and finding new ways to express or challenge both her answers and those of her peers. This has included becoming a Board member, a voting member of ACI Committee 332, chair of ACI 332-D for Footings and Foundations and much more.
Mary is perhaps most widely known and recognized for her work on the CFA’s interpretation for fall protection. At a time when OSHA was turning the entire residential construction industry toward one of six active fall protection systems (safety nets, lanyards, guardrails, ladders, aerial/mechanical lifts and scaffolds), she forged ahead with three months of extensive research recognizing the stress and risk these systems would place on her crew members, most notably scaffolding. Her efforts resulted in the CFA’s production of a draft alternate fall protection position, an educational program on how to determine the impact of fall protection systems and their feasibility and later sponsored the creation of an entire development program for contractors the CFA now offers to its members.
We congratulate and thank Mary Wilson for her unselfish, humble and dedicated leadership to carve a portion of a stronger future for this industry.
Mary can be reached at Mary@Michelconcrete.com.
The CFA Projects of the Year Competition
EACH YEAR, PROFESSIONALS IN THE CONCRETE INDUSTRY THAT ARE MEMBERS OF THE CFA SUBMIT PROJECTS OF VARYING SIZE, SCOPE AND CHALLENGE FOR CONSIDERATION BY THE GENERAL PUBLIC TO BE CONSIDERED AS A PROJECT OF THE YEAR. MULTIPLE CATEGORIES OFFER RECOGNITION FOR ACCOMPLISHMENTS OF ANY SIZE AS WELL AS TYPE OF PROJECT.
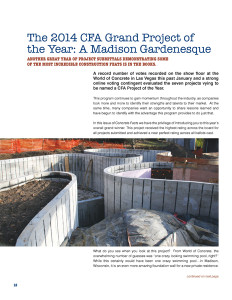
The 2014 Grand Project was selected by industry peers and popular vote to be the serpentine walls of the Gardenesque home built in Madison, WI by CFA member, Hottmann Construction.
This year, ten projects are presented on the pages that follow. Each page gives key statistics and a brief synopsis of the project from perspective of the submitting company, as well as some representative photos.
As a participant in this industry, you are encouraged to visit the CFA Projects of the Year at http://bit.ly/CFAAwards or by visiting the CFA website, www. cfawalls.org.
You will be presented by each project, with multiple photos and additional project information. Each project will be rated on a scale of 1 to 5 (not ranked) according to three categories of assessing its challenge and success.
All projects will be evaluated for top project in each category, honorable mention. One project will be selected across all categories as the Overall Grand Project.
Year after year, companies with entries receiving such recognition make this a part of their marketing presence. If you have projects that have presented challenge or offer a sense of pride for your company, you are encouraged to consider submitting them for next year’s competition.
Contact CFA Executive Director, Jim Baty, at jbaty@cfawalls.org or 866- 232-9255 to discuss the competition in detail.
Each project submitted for the 2015 competition can be visited at http://www.cfawalls.org/awards/project/index.html where a unique link to the voting will also be made available until midnight on February 28th, 2015. Winners will be presented during the Annual Convention in Williamsburg, Virginia this summer and throughout the CFA website.
CFA Members Exhibiting at WOC 2015
The Concrete Foundations Association is a co-sponsor for the World of Concrete. We are also an information and network hub for a vast amount of education and information available in seminars and throughout the show floor. Interested attendees can register at the lowest attendance rates for WOC through the CFA and our unique link of http://bit.ly/WOCwithCFA. Be sure to visit the CFA WOC2015 booth at #C4341.
See these CFA member companies and many more at World of Concrete 2015, Feb. 2-6 in Las Vegas, NV.
*New for this year, an exhibit-only pass will be available at a $20 fee (no free passes offered) Online registrations only. Valid for new registrants only. Some restrictions may apply. Contact CFA or Hanley Wood, show owner, for more details.
BIK Hydraulics……………………………………………C4709
Boman Kemp…………………………………………….N2244
Concrete Contractor Magazine……………………C4129c
Concrete Forms Services LLC……………………..O32019
Cosella-Dorken Products Inc……………………….O32125
Cranes & Equipment Corp………………………….C6425
Epro Services Inc……………………………………….S11254
GMX Inc…………………………………………………….S10752
Grip-Tite Manufacturing Co LLC…………………..S10847
Helix Steel…………………………………………………N312
Hiab USA Inc……………………………………………..C5921
Irving Equipment LLC…………………………………C5447
Leica Geosystems Inc…………………………………C5748
Mar-Flex Waterproofing & Building Products…C3649
North American Specialty Products……………..N2562
Nox-Crete Products Group………………………….S11219
PALFINGER North America…………………………C5803
Precise Forms Inc………………………………………C4519
Prinsco Inc………………………………………………..N1557
Putzmeister America Inc……………………………..C5727
Rockwell LLC…………………………………………….N2057
Schwing America……………………………………….C5126
SpecChem LLC………………………………………….C3245
Stego Industries…………………………………………S11650
The Bilco Company……………………………………N1051
Thermomass……………………………………………..C4148
Tremco Barrier Solutions Inc……………………….S10827
Wall-Ties & Forms Inc…………………………………C4611
Western Forms Inc……………………………………..C6127
Cold Weather Slab Testing
EARLIER THIS YEAR, A CONTRACTOR AND A TEAM OF MANUFACTURERS AND INDIVIDUALS, PERFORMED A SERIES OF COLD WEATHER TESTS ON 15 DIFFERENT PANELS TO REPLICATE 15 DIFFERENT FIELD CONDITIONS. HERE ARE THEIR PRELIMINARY FINDINGS.
As seen in
Earlier this year, a contractor and a team of manufacturers and individuals, performed a series of cold weather tests on 15 different panels to replicate 15 different field conditions. Here are their preliminary findings.
In the course of conducting cold weather testing on concrete slabs, Dennis Purinton, owner of Purinton Builders in East Granby, Conn. and his team, which included five ACI 306 Committee members, were seeking answers to the following questions:
• What effect does cold grade and cold ambient temperature have on slabs on grade?
• Does changing concrete temperature change its performance?
• Does concrete temperature affect the performance of accelerators?
• What effect do Supplemental Cementitious Materials (SCM’s) have on cold weather slabs?
“It was a great winter for field testing the performance of slabs on grade in cold temperatures,” says Dennis Purinton, owner of Purinton Builders in East Granby, Conn.
The team chose February 10, 2014 as the placement day and it was a beautiful, cold day in Suffield, Conn. Purinton says the morning started with single digit temperatures and a couple of inches of new snow from the night before. Meanwhile, the ambient temperature never got above the mid 20s.
THE TEST
The testing consisted of 15 different 10 foot by 10 foot by 5 inch panels that replicated 15 different field conditions. “We placed three loads of concrete, provided by Tilcon, Conn. Two loads were a straight Portland cement design,” says Purinton. “The only variable was its batch temperature. The third load was a ternary blend of 45 percent SCM’s.”
Two of the 15 panels were constructed in a temporary building that had cold subgrades. A Wacker Neuson indirect fired heater was utilized here.
The balance of the slabs were placed outside in the open air; some with cold sub-grades, some utilizing hydronic ground heaters to heat the bases, and one with two inches of XPS directly under the slab.
All 15 panels were monitored with Con-Cure radio remote maturity meters. “There were four probes in every panel,” he says. “One was placed two inches below grade, one at the interface of the concrete and base, and two in the slab. We also monitored surface temperatures with a hollowed out block of insulation and a digital thermometer.”
The time of concrete placement and the surface temperature of the concrete were recorded at every step in the finishing process. In the slabs utilizing higher temperature concrete, the surface temperature dropped as much as 12 degrees Fahrenheit during the finishing process. In the slabs utilizing the lower temperature concrete, the surface temperature dropped as much as 15 degrees Fahrenheit. Even with surface temperatures dropping, no finishing issues occurred.
An ACI certified lab technician was also on site to record concrete temperature, test for air content, and make cylinders to be cured at the lab and tested for compressive strength.
After the finishing process was complete, all panels were covered with poly and blankets. “In addition, we added hydronic heat piping on top of the poly and under the blankets in three of the panels, to simulate moist, heated curing environment,” Purinton says.
CORING THE SLABS
During the seven days after placement, the average ambient daily high temperature was 29 degrees Fahrenheit. The nights averaged 13-degrees Fahrenheit with a low of zero degrees. Two days after placement, a 12 inch snow storm walloped the area of placement.
On the eighth day, the maturity meters were removed for reading, along with the blankets and poly on all panels. Water was present under the plastic on all panels, including the edges and corners. The surface temperature of all slabs was still above 32 degrees Fahrenheit despite only a few hours of temperatures above 32 degrees Fahrenheit over the previous seven days.
“We cored all 15 slabs at eight days and again at 28 days,” he explains. “The cores were taken to the Connecticut-based, Materials Testing, Inc. and tested for compressive strength.”
OBSERVATIONS
The following are just a few of the interesting facts that were observed in the testing process:
• There was minimal drop in the concrete temperature where the interface of the concrete and the 33 degree Fahrenheit sub-grade met.
• The 33 degree Fahrenheit sub-grade temperature had little or no effect on the concrete two inches above sub-grade.
• The sub-grade absorbed heat from the initial hydration that was slowly consumed by the slab in the curing process over some number of days.
• Two inches of XPS directly under the concrete accelerated set and finish times and reduced the compressive strengths in the cores.
• A warm sub-grade will shorten finish time, but higher concrete temperature will reduce finish time even further.
• Two trucks of the same mix design were ordered. The only difference between the two was the concrete on the first truck was 88 degrees Fahrenheit, while the concrete on the second truck was 54 degrees Fahrenheit. The 88 degrees Fahrenheit concrete compressive strength in lab cured cylinders was over 20 percent less than the 54 degrees Fahrenheit concrete cylinders. The cores in the field panels showed a similar reduction in compressive strengths.
• Finish times for the 45 percent ternary blend mix design showed a 10 percent increase in comprehensive strength over a 53 degrees Fahrenheit Portland cement mix design, and over 30 percent higher than the 88 degrees Fahrenheit Portland cement mix design. All were cured under the same conditions.
• Non-chloride accelerators are temperature sensitive in their effectiveness on finish time.
Purinton says the amount of data collected from this cold weather slab testing was daunting, resulting in hundreds of possible performance comparison combinations. “We have just begun in the effort to draw conclusions to many of these comparisons.”
Editor’s Note: None of this testing could have been carried out without the valuable help received from many companies and individuals. Thanks to Mike Barry; Gene Daniel; Euclid Chemical Company; Ron Kozilcowski; Lloyd Concrete; Bill Lyons; Materials Testing, Inc.; Mike Purinton; Smith Brothers Concrete; Tilcon, CT; Wacker Neuson; Con-Cure Corporation; JGW Concrete.