CFA Member Obituary: John ‘Jack’ Easton
John Thomas “Jack” – Age 93, of Linden, died Tuesday, July 28, 2015. Funeral services will be held 11:00 AM Saturday, August 1, 2015 at Sharp Funeral Homes, Fenton Chapel, 1000 Silver Lake Road, Fenton. Chaplain Hank Messing officiating. Burial in Fairview Cemetery, Linden. Visitation will be held at the funeral home Thursday from 6-9 PM, Friday from 1-4 and 6-9 PM, and Saturday from 10:00 AM until the time of service. Those desiring may make contribution to the Wounded Warriors Project, Michigan Humane Society, Adopt-A-Pet, or Reverence Hospice.
Jack was born May 22, 1922 in Port Huron the son of George and Gertrude (Tebo) Easton. He was a veteran of WWII serving in the U.S. Navy. He married Audrey Behlow May 4, 1946 in Detroit and she preceded him in death February 29, 2000, he then married Georgine M. Felthaus February 10, 2001 in Livonia. He had resided in the Fenton area for the past 55 years. Jack had owned and operated Durand Equipment and Durand Forms with long time friend and business partner, Harry Harden and Jack’s latest business venture at the age of 80 was Easton Enterprises.
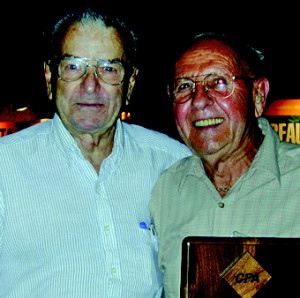
Jack Easton receiving the prestigious Robert D. Sawyer Lifetime Achievement Award during CFA Convention 2001 in Niagara Falls, ONT, Canada pictured here with Bob Sawyer.
He is survived by his wife, Georgine; daughters, Patricia (James) Okerstrom and Vivian Price; grandchildren, Amanda, Justin, Cortney (Shawn), Brandon, and Yvonne; great grandchildren, Shelby, Joey, and Kelli (Dan); great-great granddaughter, Madelynn; brother, Marshall Price; and several nieces and nephews. He was also preceded in death by his daughter, Margine Price; son, Leroy Harden; grandson, Kevin Harden; great grandson, Adam Harden; and brothers, Louis Price and Marshall Tebo. Online tributes may be made to the Jack Easton Obituary and Message Page.
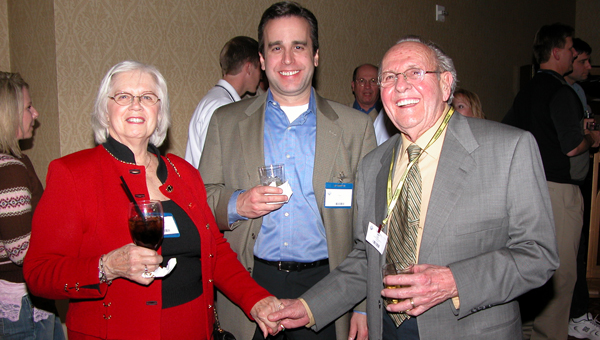
Jack and his wife, Georgine enjoying CFA friends during the Winter Meeting celebration at World of Concrete 2006.
OSHA Was Off. Way Off.
OSHA was off, way off!
That’s according to a new report by the Construction Industry Safety Coalition (CISC), which found that the Occupational Safety and Health Administration’s (OSHA) proposed silica standards for U.S. construction industry will cost the industry $5 billion per year—roughly $4.5 billion per year more than OSHA’s estimates. The coalition cautioned that the flawed cost estimates reflect deeper flaws in the rule and urged the federal agency to reconsider its approach.
OSHA’s proposed rule, intended to drastically reduce the permissible exposure limit (PEL) of crystalline silica for the construction industry, was underestimated by the agency to cost the construction industry about $511 million a year.
“The cost and impact analysis from OSHA reflects a fundamental misunderstanding of the construction industry,” a CISC statement reads. “The OSHA analysis included major errors and omissions that account for the large discrepancies with the CISC report.”
The report estimates that about 80 percent of the cost ($3.9 billion/year) will be direct compliance expenditures by the industry such as additional equipment, labor and record-keeping costs. The remaining 20 percent of the cost ($1.05 billion/year) will come in the form of increased prices that the industry will have to pay for construction materials and building products such as concrete block, glass, roofing shingles and more. OSHA’s estimates failed to take into account these additional costs to the construction industry that will result from the proposed standard.
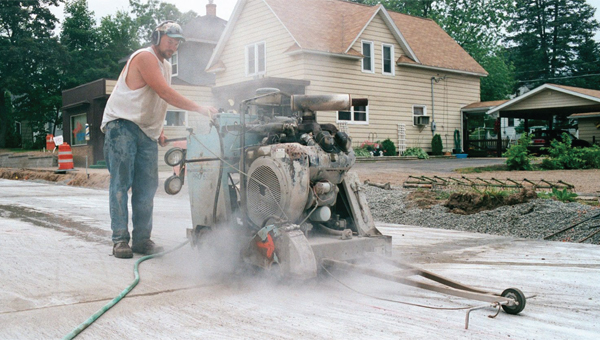
Dry cut saw methods produce substantial air-born particles. Methods to control silica dust with water are among the project requirements. (Photo courtesy of the Portland Cement Association, www.cement.org, Concrete Construction Image Library, Volume 1.)
According to the CISC statement, this will then be passed down to customers in the form of higher prices and mean “significant” job losses for the construction industry and the broader economy.
The CISC estimates that the proposed regulation would reduce the number of jobs in the U.S. economy by more than 52,700 yearly. That figure includes construction industry jobs, jobs in related industries such as building material suppliers, equipment manufacturers and architects, as well as losses in non-construction sectors. Additionally, the losses are full-time employee positions. Factoring in the many part-time or seasonal jobs, that number could increase to close to 80,000 positions lost.
“This report clearly demonstrates OSHA’s lack of real world understanding of the construction industry and raises serious questions about their ability to responsibly craft industry standards,” says Associated Builders and Contractors (AGC) vice president of government affairs Geoff Burr. “We hope that this report will lead OSHA to withdraw its proposed rule and work more closely with the construction industry to emphasize compliance with the current standard.”
Stephen E. Sandherr, CEO of AGC, echoes Burr’s concerns. “These errors raise serious and significant questions about many of the other assumptions the agency relied upon in crafting its new rules,” he says. “We need measures in place that are going to allow all of us to continue the significant improvements in silica safety the industry has made, and the sad truth is that the agency’s rule is too riddled with errors to do that.”
The full CISC report, which was also submitted to OSHA, can be found at: www.nahb.org/silicareport.
Dr. David McDonald Retained as New President and Chief Executive Officer of the Concrete Reinforcing Steel Institute
(SCHAUMBURG, ILLINOIS — October 5, 2015) The Executive Committee of the Concrete Reinforcing Steel Institute (CRSI) has appointed David McDonald, Ph.D., PE, F.ACI as the 11th President and Chief Executive Officer of the Institute effective immediately. Dr. McDonald will continue to oversee daily operations as well as directing future progress of the Institute as he has for the past three months as interim president.
“All of the candidates we met were solid and well versed in the issues and challenges of steel reinforced concrete. The leadership and management skills demonstrated by Dr. McDonald while interim president were key elements in our choice of a new executive”, according to Chairman Scott Stevens.
Previously, David was Managing Director of the Epoxy Interest Group of CRSI where his efforts included steering technical and marketing efforts.
McDonald’s prior experience was a Senior Research Associate at a Fortune 500 organization where he had both personnel and financial responsibilities and as a Consulting Engineer specializing in construction materials. Dr. McDonald obtained both his bachelor’s and doctorate degrees in Civil Engineering at the University of Sydney Australia.
David has participated in many technical committees including those within CRSI, ACI, ASTM and NACE. He has published many peer reviewed documents on durability of construction materials and is well known in the concrete industry. He is a licensed Professional Engineer in Illinois and has participated in management classes from Kellogg Business School at Northwestern University and the American Management Association.
About the Concrete Reinforcing Steel Institute
Founded in 1924, the Concrete Reinforcing Steel Institute (CRSI) is a technical institute and Standards Developing Organization (SDO) that stands as the authoritative resource for information related to steel reinforced concrete construction.
Serving the needs of engineers, architects and construction professionals, CRSI offers many industry-trusted technical publications, standards documents, design aids, reference materials and educational opportunities. CRSI Members include manufacturers, fabricators, material suppliers and placers of steel reinforcing bars and related products as well as professionals who are involved in the research, design, and construction of steel reinforced concrete. CRSI also has a broad Region Manager network that supports both members and industry professionals. Serving the construction market in the United States, Canada, and Mexico, CRSI is headquartered in Schaumburg, Ill. with regional offices located across the United States.
Nox-Crete Hires Seasoned Sales Manager for Great Plains Region
This press release published on behalf of an active CFA National Associate member.
Nox-Crete Hires Seasoned Sales Manager for Great Plains Region
OMAHA, NEB.−Sept. 9, 2015—Todd Harris is bringing his 22 years of experience in the building and contractor supply industry to Nox-Crete Products Group as its Great Plains regional sales manager. He is located in the Omaha, Nebraska, headquarters office.
The Great Plains regional sales manager role is a technical sales position that is responsible for maintaining and nurturing relationships with new and existing customers in Iowa, Kansas, Minnesota, Missouri, Nebraska, North Dakota and South Dakota.
“We are excited to have Todd provide proactive service to existing customers in the Great Plains and to introduce Nox-Crete products to new distributors and contractors there,” said Mike Linn, president and owner. “We’re confident that with Todd’s experience and knowledge, we will be successful in expanding distribution and introducing new product lines in the region.”
Harris was most recently a territory sales representative with Contractors Siding, Windows & Roofing Supply in Omaha. He also spent 15 years with Tamko Building Products, also in Omaha.
Harris studied business administration at Dana College in Dana, Nebraska, where he also played football.
About Nox-Crete Products Group
Nox-Crete Products Group was established in 1956 after creating the world’s first chemically reactive form release agent. Since then, the industry-leading construction chemical company has expanded its product line to include tilt-up cure and bondbreakers, liquid floor hardeners, joint fillers, curing and sealing compounds, water repellents, a precast magnet system and more. Nox-Crete also manufactures a full line of Green Engineered™ products.
To learn more about Nox-Crete’s expansive product line, visit nox-crete.com or call 800-669-2738.
Out of Plumb May Not Mean Damaged and Unsafe
As published in Concrete Contractor Magazine.
Question: The foundation for my new home has one wall showing two vertical cracks and the top of the wall is not even with the base of the wall. I’m concerned the backfilling has pushed the wall in and the building inspector wants an engineer to certify the wall before the builder can proceed. What should I do? – Home Owner (Wisconsin).
Answer: The process of building a foundation for a home inevitably leads to the two most common issues that have been raised by this inquiry. First of all, any homeowner who begins inspecting the concrete work performed will have concerns when cracks present. While the two truths of concrete are quite well known in the construction industry; 1) concrete gets hard, and 2) concrete cracks, the owner is not prepared to consider this an acceptable explanation.
Cracking, by itself, should never be an immediate cause for concern. There are distinct characteristics of cracking that determine rather quickly whether the crack is problematic or simply a result of the drying and shrinkage process. More information on cracking can be obtained from our website in a free public download (http://bit.ly/aboutcracks).
However, in the case of this inquiry, another common concern that presents during the final stages of the foundation work, and unfortunately all to often before the beginning stages of the above-grade structure work, has been identified. That is, the wall is out of plumb and backfilling has been completed. It must first be noted that the primary code references for residential foundation walls both state limitations for the backfilling operation. For a practical interpretation of the backfill process, the CFA provides a tech note on backfilling, TN-0021. The International Residential Code (2015) states:
R404.1.7 Backfill placement. Backfill shall not be placed against the wall until the wall has sufficient strength and has been anchored to the floor above, or has been sufficiently braced to prevent damage by the backfill.2
Furthermore, ACI 332, which provides a broad set of minimum prescriptive code requirements and the performance based design for a majority of the residential foundations, echoes the position of the IRC by stating:
8.2.4 Lateral restraint—The equivalent fluid pressure of the backfill shall be determined, but in no case shall be taken as less than 30 psf/ft. The foundation walls shall be restrained top and bottom against lateral movement. The top and bottom restraint for the foundation wall shall be in place before the introduction of backfill against the foundation wall. Temporary lateral restraint shall be permitted.3
Both code references call attention to the same design assumption for foundation walls, a positive top and bottom connection exist so that the concrete wall performs like a beam and not a cantilever. The difference in performance or applied force can be quite substantial. While it is true there are likely hundreds of thousands of successful constructions where a top connection (the first floor framing) or bracing was not installed prior to backfill, there are enough cases where problems have been created from backfilling with no top connection to validate this code position.
When a concern for movement in a foundation wall exists, however, caution should still be taken to not assume backfilling has cracked or pushed the wall inward. Some basic questions must still be asked.
The first is whether horizontal reinforcement was placed continuous in the wall and does it meet the minimum code requirements? The purpose of the required horizontal reinforcement is to reduce the number and width of cracks resulting from shrinkage.
The second question is whether the wall is bowed out of plane or leaning out of plane. This is an important condition to note. In order to determine the answer to this condition, a string line is the best method to test the position of the wall. A string should be drawn taught from bottom corner to bottom corner and from top corner to top corner. The string should be pulled taught as it approaches the wall so it can be determined if it touches a point near the center of the wall before getting to the corners. There are three potential outcomes from this test.
- String line is true at base of wall; string line at top of wall shows a bow. This is the case most likely to be of concern to an engineer and is the one to be sure to engage the parties on the project. With no bow at the base of the wall, the forms were set up true and it may be assumed that the top of the wall corresponded to the base, since forms are rigid. It should be noted that insulated concrete form walls may vary from this concern if they are plank or block style. The bow evidenced by the string is more likely to be a result of the backfill operation and stability of the wall is the next condition to investigate. An engineer should be involved at this stage.
- String line is bowed at base of wall; string line at top of wall shows a bow. This condition is a bit trickier and may still require an engineer’s assessment. Variation in the bow may still indicate influence in the wall structure by the backfilling operation. However, the bow in both the bottom and top of wall may also indicate a forming tolerance issue and forms that may not have be set completely straight. This I particular so given that the footing connection provides restraint against bowing or movement, further indicating that the wall was likely formed to that shape.
- String line is true at base of wall; string line is true at top of wall. A true string line should be the first indication that a forming tolerance is at hand. Walls that are loaded dynamically and moved from their cast position will evidence stress. Stress is not applied uniformly and movement does not result uniformly. The wall is confined at the corners where it has a much higher capacity and therefore movement results in a bowing along a longer section or cracking at or near the corners.
In the case of the project at hand, the contractor engaged the owner and demonstrated that a string line was true at both the top and bottom of the wall. The two cracks were spaced relatively evenly across the wall and were located on form joints, which further indicates a pattern of shrinkage cracking. Yet, the top of the wall was out of plumb inward by 1.5 inches, indicating an issue for tolerances.
It is proper to enter into any project with expectations of perfection and yet construction is a series of processes that require the allowance for tolerance of conditions that are less than perfect. The CFA Standard4 offers the following when considering tolerances:
8.3 Foundation Tolerances - The wall should be considered within tolerance if the following conditions are met:
-
The deviations did not cause the building to become structurally unstable.
-
The deviations did not encroach on areas reserved for other work.
-
The deviations did not severely impede other trades from doing their work.
-
The deviations did not put the building out of compliance from the governing building code.
-
The deviation or blemish did not contradict the specified class of architectural finish (unspecified class assumes “unfinished.”)
The project presents the case that the foundation wall was completed with a deviation along this particular wall. It was the only wall with such a remarked deviation. A dialog of acceptable tolerance is the next consideration. There are three references that influence this discussion as the jurisdictional codes do not address tolerances. Those references are 2010 CFA Standard, ACI 1175, and Residential Construction Performance Guidelines of the National Association of Homebuilders (NAHB). The particular tolerance in question for out of plumb of a vertical plane varies greatly across these three industry references. The NAHB reference is the most directly applicable reference specific to both residential construction and the nature of something being acceptable or not. This reference states:
2-13 – Concrete walls shall not be out of plumb by more than 1.5” in 8 feet when measured from the base to the top of the wall.6
Applying this reference and consideration of the full conditions for this project. The homeowner, builder and contractor should be having a conversation about how to complete the space for effective finishing of the basement. Concern for structural stability does not seem warranted, despite the builder proceeding with backfill ahead of top connection or temporary bracing.
Jim Baty is the Executive Director for the Concrete Foundations Association after having served as Technical Director since 2001. He is currently chair of ACI 332 and a voting member for ACI 306 with priorities of establishing better guidance and structure for residential concrete construction. For more information on this topic, contact Jim Baty at jbaty@cfawalls.org. Find out more at www.cfawalls.org.
References:
1 Backfilling Foundation Walls (TN-002) published by the Concrete Foundations Association, 113 1st Street NW, Mount Vernon, IA 52314 | Phone: 319-895-6940 | www.cfawalls.org
2 2015 International Residential Code® For One- and Two-Family Dwellings published by the International Code Council, Inc., 4051 West Flossmoor Road, Country Club Hills, IL 60478-5795 | Phone: 888-422-7233 | www.iccsafe.org
3 Residential Code Requirements for Structural Concrete (ACI 332-14) and Commentary published by the American Concrete Institute, 38800 Country Club Drive, Farmington Hills, MI 48331 | Phone: 248-848-3700 | www.concrete.org
4 2010 CFA Standard published by the Concrete Foundations Association, 113 1st Street NW, Mount Vernon, IA 52314 | Phone: 319-895-6940 | www.cfawalls.org
5 Specification for Tolerances for Concrete Construction and Materials (ACI 117-10) and Commentary published by the American Concrete Institute, 38800 Country Club Drive, Farmington Hills, MI 48331 | Phone: 248-848-3700 | www.concrete.org
6 Residential Construction Performance Guidelines for Professional Builders & Remodelers published by the National Association of Home Builders, National Housing Center, 1201 15th Street NW, Washington, DC 20005 | 800-368-5242 | www.nahb.org
2015 Projects of the Year: Private Residence Foundation (>5000 sq.ft.)
Private Residence Foundation >5000 sq.ft.
Acworth Home
Herbert Construction of Marietta, GA.
Acworth, Ga
The largest residential project to receive recognition this year represents the large-scale single-family residences over 5,000-square-feet category. Herbert Construction of Marietta, Ga. maintains their presence in the annual awards program with a private residence entry from Acworth, Ga.
“We estimated this project three separate times,” stated Doug Herbert, president of Herbert Construction. “The first estimate was submitted before the site was cut. Then, once the site was cleared and we could talk with the general contractor about the schedule we re-estimated. Next, we were asked to do one final estimate once the site was dug to the proper grade so that all variances in wall heights could be established.”
In all, 14 different wall heights were required varying from 3-feet to 18-feet and a cumulative total of 27-feet of vertical jumps (footing steps) were required. The walls themselves were configured with four different thicknesses ranging from 8-14-inches.
There were many additional outstanding features selected by popular vote for this project as award-worthy. The project included two sub wall areas that required six different details to accommodate the change in elevation. A curved retaining wall 70- feet long by 16-feet tall and 18-inches thick was designed to have brick ledge on both sides. The client asked for a safe-room under one of the porches with an internal concrete wall and integral door opening.
“The contractor viewed this as a very complicated project,” stated Herbert, “and we had to agree. However, we have grown accustomed to such challenges and using a combination of our CAD system, robotic layout and planning experience, we were able to decipher the challenges, plan an effective schedule and approach and deliver a very high quality foundation for this repeat customer.”
For more information on this foundation project, contact CFA Member Amanda Morris, Herbert Construction, at amandam@herbertconstruction.com or (770) 765-0103.
Project Specifications:
- Size
- Walls: 296 yds
- Footings: 118 yds
- Steel Used (wall & footings)
- #4: 20,669 lbs
- #5: 2,259
- Wall Heights: 14 different wall heights varying from 3′ to 18′
- Wall Thickness: 4 different wall widths varying from 8″ to 14″
2015 Projects of the Year: Private Residence Foundation 2000-5000 sq.ft.
Private Residence Foundation (2000-5000 sq.ft.)
Pappas Residence
Hottmann Construction Company
Fox Lake, Wisconsin
Following the recognition received for their “Overall Grand Project” award in 2014, Hottmann Construction Company receives the award for a private residence foundation between 2,000 and 5,000-square-feet with the Pappas Residence in Fox Lake, Wis.
“We submitted the Pappas Residence this year largely on the complexity of the sloping lot for this intermediate sized structure,” stated Mike Thole, project superintendent for Hottmann. “With a height difference from front to back of 14-feet, the footings on this job jumped or stepped four different times.”
The location for this home was on a mature lake but located within a stretch of relatively new and updated “lake houses”. Every other lot was filled with house while this lot remained filled with trees. After clearing and excavating, there was no room for convenient concrete delivery so placement challenges were met with conveyor and extra labor. Despite these challenges, including the multiple steps, the foundation was square and true and delivered according to schedule.
Prior to the start of the house framing, a precast concrete patio was installed immediately after backfilling the foundation. This further complicated the sequencing on the project and required care in the backfilling procedure to protect the unsupported foundation walls while erecting the patio.
The house design took advantage of several other techniques Hottmann has delivered for clients in the past. A wine cellar was created under the front stoop. While this is not necessarily a unique feature, their experience in curved walls delivered walls with an 8-foot-4 radius on the backside of this room with recesses for cabinets to be installed on the interior of the wall. This is complimented by a curved wall on the back patio. Finally, roof drains were internal to the structure and exit the foundation walls through block outs placed by Hottmann.
For more information on this foundation project, contact CFA Member Mike Thole, Hottmann Construction, at mthole@hottmannconstruction.com or (608) 849-1155.
Project Specifications:
- Size
- Total Lin. Ft: 780
- Walls: 97 yds
- Footings: 52 yds
- Steel Used
- Walls: 1 ton
- Wall Height: 8’9″
- Wall Thickness: 8″ and 10″ at the house, 12″ at the rear patio
2015 Projects of the Year: Private Residence Foundation<2000 sq.ft.
Private Residence Foundation <2000 sq.ft.
Point of the Woods
Purinton Builders
Lyme, Connecticut
This year’s award for a private residence foundation under 2,000-square-feet goes to Purinton Builders of East Granby, Conn. for the project known as Point of the Woods in Old Lyme, Conn. This extreme challenge included concrete piers excavated into and setting on rock at the waters edge. Craftsmanship was the primary goal and reason for the selection of this contractor for the project. Anything but a straightforward foundation, this project demonstrated how demanding and intense a small project could become, especially for the portions of the project that will go largely unnoticed as the completed work takes shape.
“The architect’s vision,” stated Dennis Purinton, president of Purinton Builders, “was to make the house appear to be growing out of the rock. When we visited the site and reviewed what they were trying to accomplish, we proposed options on different foundation designs.”
Ultimately, a tapered pier was chosen. On paper it looks like this very simple little job of a few piers and some slab work would be a quick turnaround. However, Purinton discovered that a low bridge protected access to the site. This required air to be let out of the tires of all ready mix trucks arriving and leaving. Additionally, the use of boom trucks, cranes or any large delivery trucks was prevented due to a combination of the bridge and the site location at the end of a half-mile long winding street with no turnaround.
From the start of this project, once the final design was set, challenge after challenge was uncovered and met. Tolerances for building location and elevations were set at a critical ± ¼-inch. in order to comply with FEMA and local government regulations. Layout reference points were only given as centerlines, so the pier bases had to be set from those centers and then figured with the 5-degree tapers across the variable rocky surface to determine each individual pier configuration. Even the variable rocky surface presented the challenge of maintaining code required footings slopes of no more than 1:10, so cutting of individual pier bases for support was required.
If this wasn’t enough challenge for such a small site, the location proximity at water’s edge along with the steepness of the site necessitated safety awareness. Purinton Builders used caution throughout the project and during the layout and forming stages, safety harnesses made maneuvering at these early stages more difficult while holding such tight tolerances.
“Every tapered pier was different in either size or height and the largest challenge was anchoring them down to ensure that they did not rise up during concrete placement,” stated Purinton. “When it came time to form the slab, the form system was all designed and built on site, since it not only had to support the concrete work but generate a work platform on which to construct the house.”
For more information on this foundation project, contact CFA Member Dennis Purinton, Purinton Builders, at purintonbuilders@yahoo.com or (860) 653-6664.
Project Specifications:
Not Provided
2015 Projects of the Year: Above-Grade Concrete Home
Above-Grade Concrete Home
Clifton Concrete Home
Bartley Corporation
Since the start of the new millennia, the recognition of performance and aesthetic advantage for all concrete homes has been a focus for the CFA and many throughout the concrete industry. Over the years, many fine works of construction and design have been recognized in this award category. Certainly no less impressive is this year’s “Above-Grade Concrete Home Project of the Year,” Clifton Concrete Home by Bartley Corporation.
“We were selected for this project when several recommendations for this type of complex structure pointed our way,” stated Jim Bartley, president of Bartley Corporation. “The construction manager hired for the project desired to partner with us based on our previous experience in building a concrete home.”
Bartley was asked about what makes this type of a project such a challenge. “Working with owners, construction managers and architects as well as other trades that are new to concrete homes can be a major time commitment,” stated Bartley. “Meeting on site and collaborating with the entire team was the key to success. Having an architect that saw the project all the way through construction made everything go as planned.”
Prior to the kickoff meeting the homeowners wanted to see a sample of the normal cast-in-place wall finish, one delivered on any foundation project. Bartley built and poured the mockup and made sure it wasn’t “perfect.” To their surprise the owners loved the bug holes, imperfections, ties and form-lines. They are in the building industry and like the industrial construction look with natural imperfections. Therefore, extreme measures were taken to avoid using any patching materials on the walls. With the exception of one or two spots honeycombs were avoided. Surprisingly, a crew patched one of these honeycomb regions and when the homeowners saw the patching they asked that it be removed. This kept the project on track and consistent with the approved aesthetic negotiated early in the project.
Another unique characteristic of this design was the presence of two different insulation systems, Thermomass and ThermaEZE, both products that the company had prior experience but separately on projects. The standard wall section consisted of two reinforcement bar mats, Thermomass in the center with all the connectors, conduits, block outs and wall ties. However, where the weight of steel could not bear on insulation, the ThermaEZE system was brought in to provide an alternative support system. All walls were to be left exposed concrete as the final interior and exterior finish.
The most complex part of the project was the first and second floor walls. Gang forms were used to provide the large structural walls and Bartley engaged their commercial crew and a full time commercial superintendent to take the lead in these areas. Difficult block outs and forming along with many recesses for utilities, electronics and built-in features had to be as accurate as possible. Further complicating these walls was the flashing detail. The design called for flashing between the second floor and roof deck to cover the inside of the wall through to the Thermomass insulation sandwiched in the center of the wall. Although Bartley preferred to approach the design with a monolithic roof and second floor based on their experience, the design called for flashing to separate this interface into separate placements with flashing installation between.
Some of the other challenges faced on the project included unique window jambs and an elevator shaft. Many of the windows called for the sides of the window block out to be at 105-degrees rather than perpendicular to the face of the wall. The 3-story elevator shaft challenged the safety on the jobsite with openings that were constantly managed. The shaft was produced by first forming the outside of the elevator shaft and then, when the walls were ready to be closed, a crane carefully placed large interior panels on the inside of the wall.
For more information on this foundation project, contact CFA Member Jim Bartley, Bartley Corporation, at jim@bartleycorp.com or (301) 384-2700.
- Size
- Total Lin ft.
- Basement: 285
- First floor: 92
- Total Sq Ft.
- Basement: 1548
- Garage: 1053
- Walls
- Basement: 106 yds
- First Floor: 102 yds
- Second Floor: 9 yds
- Footings
- Basement: 36 yds
- First floor: 16 yds
- Total Lin ft.
- Steel Used
- Walls
- Basement: 6.4 tons
- First Floor: 4.2 tons
- Second Floor: .5 tons
- Footings:
- Basement: 1.6 tons
- First Floor: .4 tons
- Walls
- Wall Heights
- Basement: 11.2′
- First Floor: 9.2′-17′
- Second Floor: 9.2′
- Wall Thickness
- Basement: 12″-16″
- First Floor: 12″-16″
- Second Floor: 12″-16″
2015 Projects of the Year Overall Grand Project: Commercial/Multi Family
Commercial Structure
The George Washington University Science and Engineering Hall
Ballinger AE
Washington DC
The project recognized by popular vote as this year’s overall grand project is the Science & Engineering Hall at George Washington University. Submitted by Ballinger AE, a professional member of the CFA, this project also demonstrates the growing network of design professionals within the membership of the association.
The George Washington University- Science and Engineering Hall is a new 700,000- square-foot building located in Washington. Of the total 700,000 square-feet, 300,000-square-feet encompass the 6-story subgrade structure.
There were many unique design and construction challenges that came with such a substantial and complex subgrade structure. The substructure extends to a maximum depth of occupied space of 74-feet below grade. The perimeter basement walls were designed to withstand the intense soil pressures caused at these depths. It is also located in close proximity to three existing dormitories, which remained occupied during construction. These dormitories required deep underpinning so as not to disturb the original foundations, and also imparted a surcharge onto the new substructure walls.
Rock elevation on the site varied from 74-feet below grade to 34-feet below grade, therefore significant rock excavation was required. This was accomplished with localized blasting, which again was done while the neighboring dormitories remained occupied.
Ed Zinski, associate principal and chief structural engineer for Ballinger AE was asked about the firm’s role in the project. “Ballinger has extensive experience with unique foundation and concrete design, as well as designing university lab spaces,” stated Zinski. “Working with our in-house design team and assisted by A&F Engineers local to Washington DC provided us with the ability to closely collaborate with the architectural and mechanical design of the building, in order to provide the most efficiently designed structure.”
Extensive computer modeling was used in all aspects of design including the deep basement walls with high soil and surcharge loads, the substructure slabs with open and sloping diaphragms translating extraordinary lateral soil loads, NIH caliber vibration resistant lab floors and high-bay post-tensioning design.
The high-bay testing lab featured a “strong-wall” and “strong-floor” designed and located 12-feet below grade level. Despite being located below grade, this lab was actually an elevated floor five stories above the building’s foundation. The elevated condition resulted in a unique design, as these types of intensely loaded labs are typically founded on grade. The design loads for the lab included more than one million pounds ultimate load applied laterally at the wall and vertically at the floor. The lab also houses a 20-ton crane and a drive-through truck receiving area to deliver specimens to the testing site. Again, extensive computer modeling was used to design this area. Ultimately it was determined that the strong-wall and strong-floor would be reinforced using solid post-tensioning rods. This is another area that required close collaboration with Clark Construction, as well as with the civil engineering faculty of George Washington University during design and construction.
Also located within the building are several sloping columns, column transfers and a central core transfer with eccentric column loads of up to 5-million pounds. The slabs were designed to transfer the lateral load induced by the sloped columns. For three of the major column transfers over the main floor auditorium, it was determined that the best solution would be to utilize an exposed composite concrete and steel truss solution. Ballinger’s structural group worked closely with Clark Construction during the building of this unique truss to ensure all of the design requirements were met.
“We are thrilled that the CFA has honored our project, the George Washington University – Science and Engineering Hall, with this award,” stated Zinski. “I have long thought that something so critical as a structure’s foundation is often overlooked or taken for granted. That is why we joined the CFA and look forward to greater participation within the organization. This is also why we are so honored to be recognized by the CFA with this award.”
For more information on this foundation project, contact CFA Member Edward J. Zinski, PE of Ballinger at ezinski@ballinger-ae.com or (215) 446-0684.
Project Specifications:
- Size
- Total Lin. Ft. : 1200
- Total Sq. Ft. : 700,000
- Walls: 5100 cu.yds
- Footings: 1350 cu.yds
- Steel Used
- Walls: 190 tons
- Footings: 52 tons
- Wall Height: Total of 74′
- Wall Thickness: Varies between 20″ and 32″