Innovator MAX USA Corp. Introduces a New Large Jaw Cordless Rebar Tying Tool
New York, NY, April 28, 2020- MAX USA Corp. launched its new large jaw cordless rebar tying tool, the TwinTier RB611T. This exciting new rebar tying tool is the world’s only battery powered rebar tying tool with the ability to tie #9 x #10 rebar. Powered by MAX proprietary TwinTier technology, the RB611T is faster and delivers even greater efficiency and labor saving than previous rebar tying tool models.
TwinTier technology includes special attributes including its faster tying speed, which further increases productivity, a reduction in wire consumption, which further increases cost savings for end-users, and a wire tie that is shorter in height requiring less concrete to fully cover it.
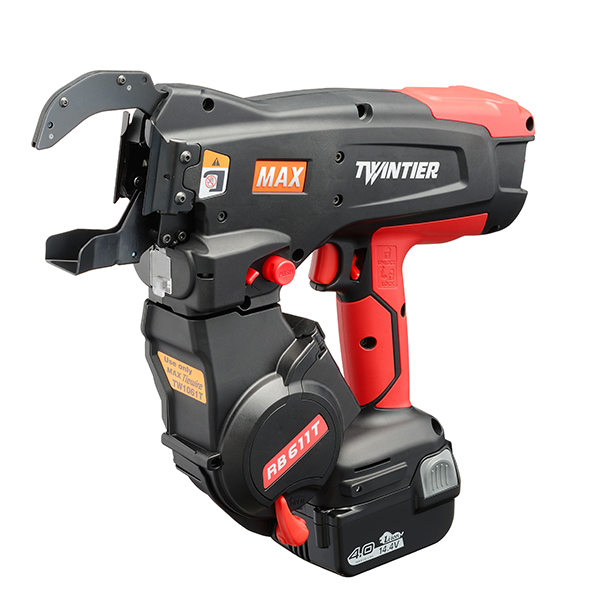
The TwinTier simultaneously shoots two 19ga. wires around rebar intersections wrapping once to form a tie equivalent to the strength of a hand snap tie. The TwinTier uses TW1061T series tie wire which is available in black, poly coated, electro. galvanized, stainless and Buy America steel options. The 4.0 amp li-ion battery, which powers the tool, will complete approximately 4,000 ties before needing to be recharged.
The TwinTier RB611T’s large jaw allows users to tie #5 x #5 up to #9 x #10 rebar (varying by rebar manufacturer). Its enclosed design offers greater protection against debris and moisture entering the tool. Like other MAX rebar tying tools, the simple operation of the TwinTier helps reduce muscular skeletal injuries, when compared to hand tying. Published NIOSH report (HEATA #2003-0146-2976) and the Canadian Safety Association of Ontario Final Report (WSIB Grant #01023) both support these statements.
MAX created the world’s first cordless rebar tying tool and the release of the RB611T marks a 27-year history of manufacturing and innovating cordless rebar tying tools. The MAX TwinTier is available through concrete and rental dealers in North and South America.
MAX USA CORP. is headquartered in Plainview, NY, and is owned by MAX CO., LTD., which is headquartered in Tokyo, Japan. MAX is recognized as a market leader in the quality manufacturing of tools for over 75 years. MAX has several divisions employing more than 2,000 people worldwide, including 200 R&D engineers.
To learn more about the MAX TwinTier you can call MAX at (800) 223-4293 or visit us on the web at www.maxusacorp.com.
CFA Members Urged to ‘Stand Down’ for Coronavirus Safety
CFA, in partnership with the NAHB, is urging our members, and all residential construction companies, to halt work for at least 10 minutes on Thursday, April 16, for a COVID-19 Job Site Safety Stand Down to educate workers on what they should do to keep themselves safe from coronavirus and to help “flatten the curve” for everyone.
NAHB has developed detailed blueprints and offered them to the industry — in English and Spanish — for contractors to conduct their COVID-19 safety stand downs, including guidance on sharing the resources digitally.
The Department of Homeland Security recently designated construction of single-family and multifamily housing as an “Essential Infrastructure Business,” allowing construction to continue in places under stay-at-home orders. Although this designation is not binding on state and local governments, it does mean that there could be more workers on construction sites in the coming weeks.
“We are already concerned for what the return to work and fuller operations might mean for our systems,” said CFA member Jeff Barnett, a foundation contractor and and long time member from Scottville, MI.
“We know it will be critical for our employees to understand their roles along with everyone on a construction site to alter normal behavior and strictly follow public health guidelines while at work,” stated CFA Board member Sean Smith, a foundation contractor from Wellington, OH.
As part of the safety stand down, members are being asked to pause all work for at least 10 minutes to relay coronavirus safety precautions, such as maintaining a distance of no less than six feet with others at all times, cleaning and sanitizing frequently used tools, equipment, and frequently touched surfaces on a regular basis and ensuring the proper sanitation of common surfaces and equipment. The safety information can also be distributed digitally (through email and/or text).
NAHB, and other construction industry partners have also developed a comprehensive Coronavirus Preparedness and Response Plan for Construction that outlines the steps every employer and employee should take to reduce the risk of exposure to and transmission of COVID-19. It describes how to prevent worker exposure to coronavirus, protective measures to be taken on the job site, personal protective equipment and work practice controls to be used, cleaning and disinfecting procedures and what to do if a worker becomes sick.
NAHB and industry partners also have created a quick-reference job site checklist for employers and employees and a job site safety poster — available in English and Spanish — that can be distributed throughout the workplace. These and other resources for members can be found at nahb.org/coronavirus.
Contact James Baty, CFA Executive Director or Rob Matuga, AVP, Labor, Safety & Health at the NAHB with any questions about the stand down.
Contact the CFA for additional COVID-19 policies and resources, including a recorded members webinars on OSHA regulations for reportable illnesses and Crisis Communication best practices.
U.S. Department of Labor Announces OSHA Interim Enforcement Response Plan to Protect Workers during the Coronavirus Pandemic
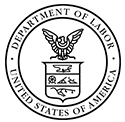
WASHINGTON, DC – The U.S. Department of Labor’s Occupational Safety and Health Administration (OSHA) today announced an interim enforcement response plan for the coronavirus pandemic. The response plan provides instructions and guidance to OSHA Area Offices and compliance safety and health officers (CSHOs) for handling coronavirus-related complaints, referrals, and severe illness reports.
During the coronavirus outbreak, OSHA Area Offices will utilize their inspection resources to fulfill mission essential functions and protect workers exposed to the disease. The response plan contains interim procedures that allow flexibility and discretion for field offices to maximize OSHA’s impact in securing safe workplaces in this evolving environment.
“OSHA is committed to protecting the health and safety of America’s workers during this challenging time in our nation’s history,” Principal Deputy Assistant Secretary Loren Sweatt said. “Today’s guidance outlines commonsense procedures for investigating complaints related to the coronavirus, while also ensuring the safety of workers, employers, and inspectors.”
The response plan outlines procedures for addressing reports of workplace hazards related to the coronavirus. Fatalities and imminent danger exposures related to the coronavirus will be prioritized for on-site inspections. The response plan contains procedures and sample documentation for CSHOs to use during coronavirus-related inspections. Workers requesting inspections, complaining of coronavirus exposure, or reporting illnesses may be protected under one or more whistleblower statutes and will be informed of their protections from retaliation.
This memorandum will take effect immediately and remain in effect until further notice. It is intended to be time-limited to the current public health crisis. Check OSHA’s webpage at www.osha.gov/coronavirusfrequently for updates.
Under the Occupational Safety and Health Act of 1970, employers are responsible for providing safe and healthful workplaces for their employees. OSHA’s role is to help ensure these conditions for America’s working men and women by setting and enforcing standards, and providing training, education and assistance. For more information, visit www.osha.gov.
The mission of the Department of Labor is to foster, promote, and develop the welfare of the wage earners, job seekers, and retirees of the United States; improve working conditions; advance opportunities for profitable employment; and assure work-related benefits and rights.
Release Number: 20-631-NAT
The Survey Says…
Reinforcement Trends Facing the Market
by James Baty, Executive Director
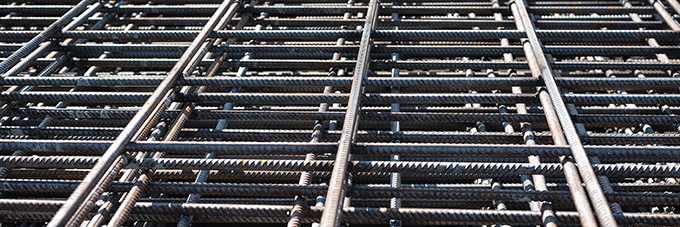
World of Concrete 2020 has come and gone. The Las Vegas Convention Center in Nevada serves as the annual home for WOC, a show that draws an average of 60,000 people each year. It continues to prove itself to be the global concrete industry’s most significant annual event.
Attendees at WOC this year were caught up in a wave of discussion and activities pertaining to labor savings. The most pervasive conversation topic among contractors in the cast-in-place industry had to have been, “What options can I pursue to offset the lack of skilled laborers I’m able to hire?” Not surprisingly, each of you reading this would likely agree — everyone is facing significant labor force challenges. What perhaps was surprising at this year’s event, however, was the subject that most contractors seemed to be testing. Concrete reinforcement — which is, for all intents and purposes, a requirement for all concrete projects — jumped to the forefront of discussions held in and around the booth for #CFAConcretePros, the home of the Concrete Foundations Association. The two most common questions about reinforcement were: 1) “What do you think of the glass-fiber rebar?” and 2) “Does anyone use rebar tying equipment?” In our search for answers, we found the products at WOC 2020 to be intriguing and engaging, but broader research of this market was conducted through surveys about experience and interest. In this article, I will summarize the premise of reinforcement as a requirement as well as the results of the survey our staff recently conducted. This article can also help prepare individuals seeking to become Certified Residential Foundation Technicians1 through the American Concrete Institute (ACI).
Concrete Basics
Any concrete basics course will tell you there are three truths to concrete: It is gray; it gets hard; it cracks. A fourth fact should be added: It can’t be stolen (compliments of a field manager for a Wisconsin-based contractor, quoted at a recent course). Most courses continue by explaining that concrete is often described or specified in terms of its compressive strength. For instance, in the International Residential Code2 and in ACI 332 – Code Requirements for Residential Concrete,3 the minimum compressive strength of concrete is set at 2,500 psi for a 28-day design strength. This is the standard for concrete, as it is relatively common to test the strength of concrete by crushing cylinders at different ages (7 days and 28 days being the most common times to test).
Concrete, while strong in resistance to compression (crushing) forces, is relatively weak in resisting forces in the opposite direction. When concrete cracks, it does so most often from the two forces we describe as tension and flexural. In fact, the engineering community knows that the tensile and flexural strength of concrete is only about 10% of its compressive strength. In order to control cracking in concrete, then, steel reinforcement has traditionally been added.
The first force, tensile, is most often an axial force created internally within the concrete due to shrinkage. Concrete is delivered into the forms as a near liquid. The chemical process of hydration consumes water in a reaction with the cementitious material, and water is evaporated from the concrete matrix by the climate. Between 7% and 18% of the concrete volume is water, with a residential code target ratio of 0.45 water to cementitious material (w/cm). The consumption and evaporation of water results in shrinkage that is generally assumed to be ¼ an inch for every 20 feet. Reinforcement is then prescribed to limit the cracks that occur naturally from this shrinkage and to control them from becoming problematic to the long-term behavior and performance of the concrete.
The second force, flexural, is best seen as the force created by backfill or wind pressure against a concrete wall or the load carried along an unsupported beam. As this load pushes or is applied against one face of a concrete member, bending results. In order for bending to occur, one side becomes shorter and the opposite side longer. The concrete face becoming shorter is called the “compression face,” as there is a force pushing inward from the ends. The face that becomes longer is called the “tension face,” and at a certain level of stress, like the crack produced from shrinkage, the face will crack. Reinforcement is prescribed to increase the amount of force the concrete can take once the cracking begins to occur from the anticipated force and to work with the concrete for long-term load behavior.
Survey Results
The science and engineering of concrete systems recommends reinforcement for virtually every type of concrete application. What does this have to do with labor, and why did it attract so much interest from contractors at the World of Concrete? This can be understood by looking at two elements of traditional steel reinforcement usage: weight and time. In a recent survey, the CFA studied the annual consumption of steel reinforcement. A sampling of 54 companies across the United States reported a total of 211,613 tons of steel reinforcement used annually, a surprisingly large number. Staggeringly, 200,000 tons of that was reported by one CFA member from California. If this contractor’s input is set aside, the industry average is 219 tons per year with 8 tons per year being the lowest reported weight and 1,000 tons the highest (aside from that residential contractor in California).
Where do you fit on this scale? Based on the current CFA contractor membership, we can project an estimated annual consumption of 240,000 tons of steel reinforcement. A former CFA board member and the contributor of the smallest quantity in the survey, Bill Mulready of C & B Foundations in Connecticut, said, “Years ago we maybe used less than a ton of rebar in a year with many more foundations. . . today, we are seeing a lot more than just rebar in footings and walls.”
With all of this weight inventoried, loaded on trucks, delivered to job sites and then unloaded stick by stick by your workforce, is it any surprise why so many companies were looking at the non-steel reinforcement bars found at WOC 2020? Owens Corning, the manufacturer of PINKBAR®, has recently joined the CFA as a National Associate member to begin promoting labor force improvement.
“PINKBAR™ has roughly 1/4 the weight of a comparable steel reinforcement bar, most traditionally #4 or #5 in the residential marketplace,” states Ashish Gandhi, Business Manager for PINKBAR™ Fiberglass Rebar. “We have already seen the response by concrete contractors to the significant stress reduction this product brings their workforce and are excited for the opportunity to partner with the CFA to rationalize this to a broader audience. Companies cannot overestimate the value of lowering the weight that has to be hauled and placed on these job sites within the most common bar sizes.”
Bearing in mind the two different elements of steel reinforcement described earlier, the product is used in the residential concrete industry in three major areas: slabs, footings and foundation walls. Each respondent affirmed that 100% of their steel reinforcement was distributed between these applications. Figure 1 shows the percentage of each application of steel presently being used. The weighting shows that the overwhelming majority of steel applications is in foundation walls. In fact, the aggregate totals show that 68.9% of all steel is placed in walls, 31.4% in footings, and only 16% in slabs-on-ground.
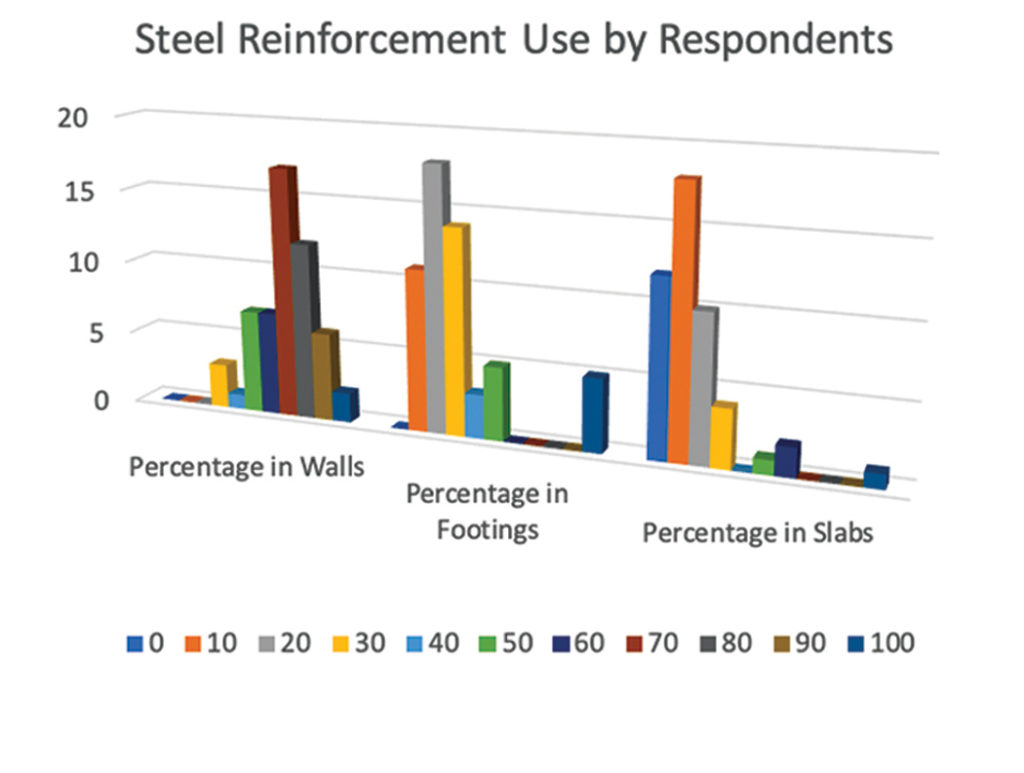
When selecting steel reinforcement for slabs-on-ground, there is a decision to be made between the principle types of rebar: welded-wire mats and rolled-wire. While the latter was a common product a couple of decades ago, construction quality has moved the industry further and further away from such a decision. Realizing that a contractor may use more than one type of product depending on the project design, specifications, and their own preference, the survey quantified the current market. 86% of respondents reported that they use steel rebar in slabs. 69% said welded-wire mats — a rigid, thick-gauge product that has a much higher load capacity before bending — was used on projects. Still, 20% of respondents reported continuing to use a rolled-wire fabric or mesh to reinforce slabs-on-ground. An indication of the need for continuing education in the industry, several contractors added comments related to the inability to ensure placement of steel when it is the rolled product. In total, 44.7% of the slabs-on-ground market appears to be using steel rebar while 48.4% is using a combination of the wire reinforcement options.
In addition to the steel reinforcement percentages noted above, a percentage that amounts to roughly 7% remains. Our survey inquired about the use of fibers in the marketplace. It is worth mentioning that many projects, particularly slabs-on-ground projects, may use a combination of fiber reinforcement (for durability and plastic surface shrinkage performance) and steel reinforcement (for load, shrinkage and temperature movement performance). There are also structural fibers in the marketplace, as has been represented during Concrete Foundations Convention, most recently with Helix™, presented in Denver in 2019. There will be further education offered in Charleston in 2020 (July 23–25) for a broad range of fiber products and application considerations. The survey sought to separate experience with traditional reinforcement products from that of experience with the increasing variety on the market for randomly mixed and steel alternatives. Figure 2 demonstrates that highest familiarity is with the synthetic, non-structural fibers, and there are varying lower levels of experience in structural products.
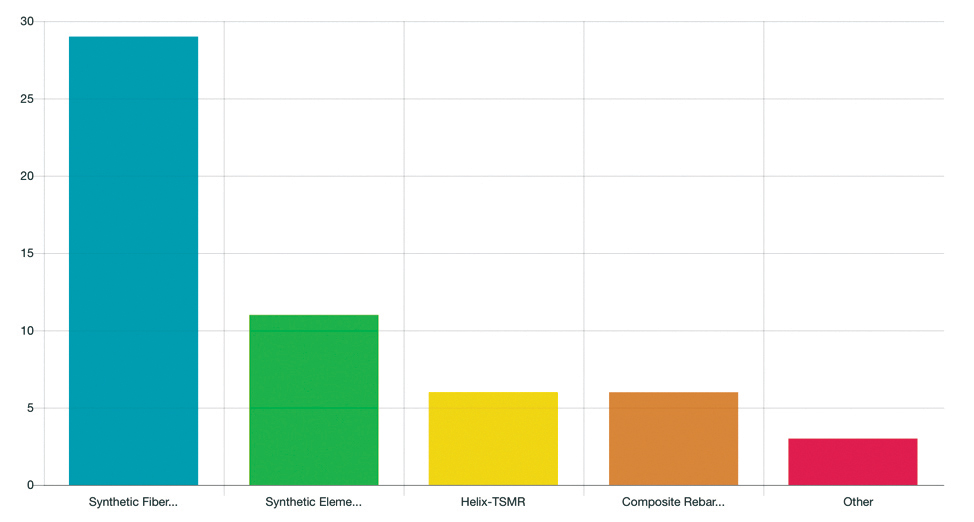
While these products, often described as reinforcement “replacement” products, are a strong source of interest for reducing the cost of labor and the pressures on limited workforce engagement, companies representing them are quick to point out their advantages in addressing the real reinforcement needs for concrete. Each has specific properties that, when properly applied, reinforce concrete more appropriately than the current steel reinforcement approach.
The survey’s final research goal was to determine the methods for securing reinforcement when using traditional steel. The residential concrete codes call for all steel reinforcement to be secured in place, which is often assumed to mean tied in place. There are traditional, or at least historical, methods for tying steel in place. One of these is the use of rolls of wire, cut and twisted around steel using pliers. Another is a tie known as the “loop tie,” which uses ends of pre-tied loops bent around steel at an intersection, then grabbed with a hook-end tool and spun or twisted until tight. There is also a new form of technology that has been increasing in popularity over the last decade, perhaps best described as a mechanical tie gun. Any intersection of steel is quickly grabbed by wire that shoots out of this gun and spins together tightly in a split second. A single crew member can secure an entire framework of steel reinforcement in half the time it takes three laborers hand-tying. Through the survey, it is evident that this growth of technology has had a significant impact on the labor market, as 48% of all respondents are already using mechanical tie systems. Max USA, a leading manufacturer of the tie gun technology, has recently joined the CFA as a National Associate.
“Being first to market with a battery powered rebar tying tool, MAX has witnessed the growth in the use of mechanical rebar tying technology; and for great reason,” states Denene Williams, National Marketing Manager for the company. “MAX battery powered rebar tying tools offer major benefits for reinforcing steel ironworkers and the businesses that employ them. Companies that have bought into the technology have seen an increase in production capacity, reduction in labor costs, and a decline in back and musculoskeletal injuries amongst their ironworkers. The latest model, the TwinTier, is a dual wire feeding rebar tier that significantly reduces the consumption of wire previously necessary to tie rebar intersections.”
The staff from Max USA will be on hand during Concrete Foundations Convention this year to begin reaching the 51% who are still tying by hand. Of this percentage of respondents, only 5% are still using rolls of wire hand cut and pieced together for each connection.
Perhaps the most intriguing survey question asked respondents what they thought was the main cause of the lack of use of alternatives to steel reinforcement in their marketplace. In Figure 3, we see a diverse spread of the most common reasons, barriers or hurdles.
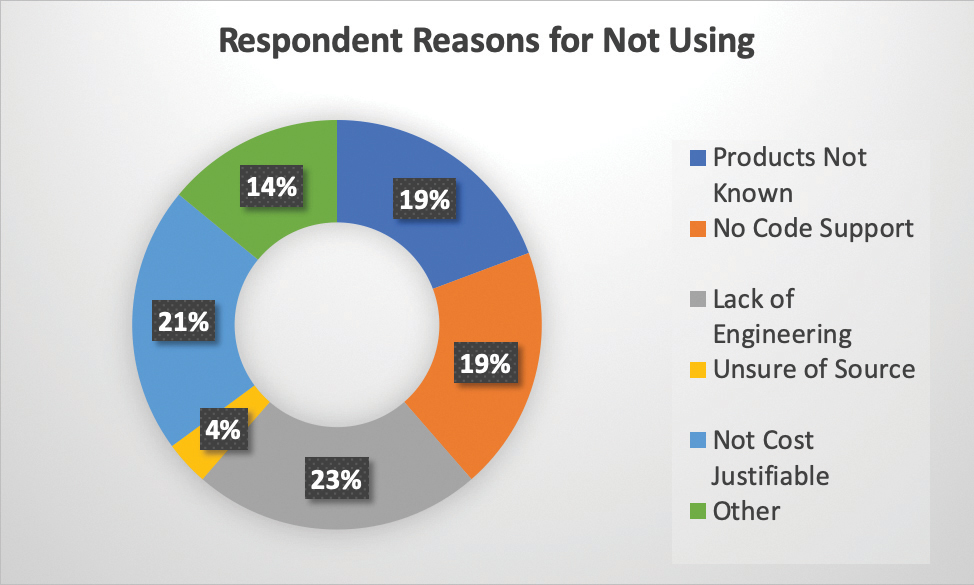
Lack of engineering (23%) was the most common reason respondents gave for a company(s) not using alternatives to steel reinforcement to date, although the reasons are similarly distributed.
“I think even though I know they conform to codes, the building inspectors here would not be accepting of them,” said one respondent. “Rebar they can see in place before the pour. Alternatives would require documentation or inspections outside of their scope.”
Another respondent said, “All foundations are structurally engineered and engineers require rebar reinforcing.” In truth, the residential concrete industry is both prescriptively directed and, when necessary, engineered with steel reinforcement. This is the standard building inspectors have been trained to use, and it is the standard they anticipate for inspections. However, building codes should create space for innovation and approval of systems not addressed by the code through alternative material submittal and approval. The IRC states:
R104.11 Alternative materials, design and methods of construction and equipment. The provisions of this code are not intended to prevent the installation of any material or to prohibit any design or method of construction not specifically prescribed by this code. The building official shall have the authority to approve an alternative material, design or method of construction upon application of the owner or the owner’s authorized agent. The building official shall first find that the proposed design is satisfactory and complies with the intent of the provisions of this code, and that the material method or work offered is, for the purpose intended, not less than the equivalent of that prescribed in this code in quality, strength, effectiveness, fire resistance, durability and safety. Compliance with the specific performance-based provisions of the International Codes shall be an alternative to the specific requirements of this code. Where the alternative material, design or method of construction is not approved, the building official shall respond in writing, stating the reasons why the alternative was not approved. [Emphasis added]
Any alternative to the prescribed methods must be submitted, evaluated and either approved or rejected with reasons for non-approval stated, which the interested party can work to remedy now or in the future. Remember, codes like the IRC (and thereby inspections) have specific intent:
The purpose of this code is to establish minimum requirements to safeguard the public safety, health and general welfare through affordability, structural strength, means of egress facilities, stability, sanitation, light and ventilation, energy conservation and safety to life and property from fire and other hazards attributed to the built environment, and to provide safety to fire fighters and emergency responders during emergency operations.
Innovative systems and products are a major reason why the Concrete Foundations Convention (Charleston, SC 2020) exists and why the advocacy of the CFA on behalf your business is such an important membership benefit. There are many more systems that contribute to this industry’s labor force reduction goals specifically related to reinforcement. For example, there are footing form brackets, like Accufooting Brace, and connectors that space, snap, and secure reinforcement for ICF and removable forms. At the Concrete Foundations Convention, so many of these systems and ideas are present, and there is plenty of time to discuss them (and it has less of a hectic pace than that of WOC).
Want to know more about this survey data or the goals and opportunities for labor force savings? Contact James Baty, the executive director for the Concrete Foundations Association.
1. Residential Concrete Foundation Technician certification program offered by the American Concrete Institute, 38800 Country Club Drive, Farmington Hills, MI 48331 | Phone: 248-848-3700 | www.concrete.org
2. 2018 International Residential Code® For One- and Two-Family Dwellings, International Code Council, Inc., 4051 West Flossmoor Road, Country Club Hills, IL 60478-5795 | Phone 1-888-422-7233 | www.iccsafe.org
3. ACI 332-14: Residential Code Requirements for Structural Concrete (ACI 332-14) and Commentary, American Concrete Institute, 38800 Country Club Drive, Farmington Hills, MI 48331 | Phone: 248-848-3700 | www.concrete.org
Evaluating Safety’s Return on Investment
by Julia Kunlo, CSP, Tim Neubauer, MSOSH, CSP
When discussing corporate safety, it is common to hear catchy taglines such as:
- “Safety is #1”
- “Safety is our top priority”
- “Safety above all else”
- “Safety first”
As an occupational safety consultant at Evolution Safety Resources, I am thrilled to hear that organizations are placing a high value on safety when considering their daily operations. The fact of the matter, unfortunately, is that the majority of these taglines are just not true. Businesses do not focus on safety first, because they must focus on profitability first. And while business owners should choose to only be profitable so long as they are safe, we understand that safety cannot realistically be seen as a line item without a budget. Considering the financial implications, how can companies protect their bottom line while also protecting their employees?
The information provided in this article should be used as a tool for deciding which components of a safety program to prioritize when all components cannot be reasonably afforded.
In 2017, the average cost per workplace injury was $39,000 — this figure includes wage losses, medical expenses, and administrative expenses (Work Injury Costs, n.d.). This statistic highlights the fact that companies, who must focus on profitability, cannot ignore the importance of a safety program. In fact, “various studies reflect correlations between proactively investing in occupational safety and health and experiencing lower incident rates and higher profit margins” (Druley, 2019).
Considering that safety has a budget (like all other components of business), companies must be strategic in how they spend their hard-earned dollars. So, what safety program elements will give you the biggest bang for your buck in terms of safety impact? To answer this question, we must consider each component of a safety program’s return on investment (ROI). In 2001, research was conducted to understand the benefit-to-cost ratio of various safety program components. This research measured the resources required to establish and maintain each program element as well as each element’s financial impact on the business (Jervis & Collins, 2001). When ranking highest return on investment to lowest return on investment, program elements were listed as followed:
1. Hazard prevention and control
- Assigned personnel/staff, access to and utilization of certified safety professionals, first aid/CPR personnel on all shifts, use of engineering and administrative controls, safety discipline system, etc.
2. Management leadership and employee involvement
- Integration of safety into business planning, written policies and programs, assigned safety responsibilities at all levels, readily available resources for safety efforts, annual safety program auditing, programs for continuous improvement, etc.
3. Worksite analysis
- Activity hazard analysis (AHA), workplace safety inspections, written hazard reporting systems, incident investigations, trend analysis, etc.
4. Review of documentation
- Annual review of written safety program documentation
5. Safety and health training
- Training on safety responsibilities, job-specific hazards, PPE use/maintenance, and emergency drills
The highest-ranking program element, hazard prevention and control, is a broad term. What does that mean to an organization? According to the study, this category is mainly defined as having access to designated safety professionals. When analyzing the results, the authors proposed that “without core safety staff, the company will not have the resources needed to conduct hazard analyses, develop written safety rules, monitor regulatory compliance, and track corrective actions” (Jervis & Collins, 2001). When considering return on investment and safety efforts, the study finds that having a strong safety team and/or representative is the best financial decision a company can make. This is why Evolution Safety Resources is passionate about what we do — we bring value to our customers by providing expertise within the field of occupational safety and health. From procedure development and field inspections to long-term staffing and incident response and case management, we are ready to meet all of your workplace safety needs.
A commitment to workplace safety is something all companies should pledge for moral reasons. It is the right thing to do. Nevertheless, it is misguided to believe this commitment can be made without regard for a company’s financial future. A sound occupational safety and health program benefits the bottom line by reducing worker’s compensation claims, limiting litigation expenses, avoiding regulatory fines, lowering insurance premiums, qualifying for government contracts, and, ultimately, winning bids. Other program benefits are difficult to quantify, such as increased employee retention and improved overall morale. When considering the plethora of benefits related to a comprehensive safety program, companies with tight budgets should evaluate return on investment when budgeting their safety dollars.
Druley, K. (2019, January 4). The ROI of safety. Retrieved from https://www.safetyandhealthmagazine.com/articles/17819-the-roi-of-safety.
Jervis, S., & Collins, T. R. (2001). Measuring Safety’s RETURN ON INVESTMENT. (Cover story). Professional Safety, 46(9),
18. Retrieved from http://search.ebscohost.com.libraryresources.columbiasouthern.edu/login.aspx?direct=true&db=bsu&AN=5154027&site=eds-live&scope=site
Work Injury Costs. (n.d.). Retrieved from https://injuryfacts.nsc.org/work/costs/work-injury-costs/
Evolution Safety Resources is an occupational safety consultation firm based out of Raleigh, North Carolina. Visit our website (www.evolutionsafetyresources.com) to learn more about our services – we are proud of what we do and would love to be of assistance.
Walk-Out Foundation Frost-Free Design
Recently, a CFA contractor contacted Association headquarters for assistance in a difficult conversation taking place. A project under construction was flagged to not proceed until corrective action was made. After a series of steps from permit approval through inspections, despite having a registered engineer involved to provide the design and remediation steps, the inspections department was unwilling to finalize the foundation. This article shares the basis of the conditions and a review of the code perspective, as well as an assessment of the next conversation steps.

Q: A walk-out basement we are completing has fallen under scrutiny by the building department. As we started the excavation, poor soils were discovered at the rear of the footprint where the walk-out will occur. Our engineer designed a rock mat foundation with AB-3 in consecutive lifts of eight inches in thickness for a total of three feet in depth. The design did not call for a frost footing, and we planned to proceed with vertical insulation to protect the footing and the short wall of the walk-out, per the provisions for frost-protected, shallow foundations. The inspector is standing on the lack of frost-wall depth at this location and holding up the project. What are our options?
A: When dealing within the design and construction of structures with the enforced general building codes, there are several truths to fulfill. As I work with building inspection and code official departments across the country, it is always important to establish a common understanding of the nature of and purpose for decision-making, that which we hope both clarifies and upholds the intent and purpose of the provisions and the compliance.
In R101.3, the International Residential Code1 states:
R101.3 Intent. The purpose of this code is to establish minimum requirements to safeguard the public safety, health and general welfare through affordability, structural strength, means of egress facilities, stability, sanitation, light and ventilation, energy conservation and safety to life and property from fire and other hazards attributed to the built environment, and to provide safety to fire fighters and emergency responders during emergency operations.
Where the code’s intent intersects with design and review, often there is a tendency to drill much more deeply with interpretation and creative liberty for how to judge or assess compliance. General code provisions are not intended to resolve every custom situation or unique condition, rather they establish the conditions of absolute minimum standard from which designers and contractors proceed to resolve the individual project. The IRC further states in R104.1:
R104.1 General. The building official is hereby authorized and directed to enforce the provisions of this code. The building official shall have the authority to render interpretations of this code and to adopt policies and procedures in order to clarify the application of its provisions. Such interpretations, policies and procedures shall be in compliance with the intent and purpose of this code [see R101.3]. Such policies and procedures shall not have the effect of waiving requirements specifically provided for in this code. [Emphasis added]
An engineered design is supported by the integrity, professional credentials, and liability of the design professional that established it. The inspector has the responsibility and authority to review the design and to agree with compliance, and if the inspector has concerns or disagreements, they must provide evidence in accordance with the code’s intent and purpose, as found in IRC1 section R104.11:
R104.11 Alternative materials, design and methods of construction and equipment. The provisions of this code are not intended to prevent the installation of any material or to prohibit any design or method of construction not specifically prescribed by this code. The building official shall have the authority to approve an alternative material, design or method of construction upon application of the owner or the owner’s authorized agent. The building official shall first find that the proposed design is satisfactory and complies with the intent of the provisions of this code, and that the material, method or work offered is, for the purpose intended, not less than the equivalent of that prescribed in this code in quality, strength, effectiveness, fire resistance, durability and safety. Compliance with the specific performance-based provisions of the International Codes shall be an alternative to the specific requirements of this code. Where the alternative material, design or method of construction is not approved, the building official shall respond in writing, stating the reasons why the alternative was not approved. [Emphasis added]
If you have not received specific reasons in writing as to why your design proposal is rejected, it should be requested immediately. Documented reasoning is required when an official reviews and rejects the engineer’s approach to the project, and it is also a great way to openly present the terms for negotiation and further work — it can even help the inspector fully engage with the proposal. Of course, the design proposed must comply with the structural stability intent of the code, which is the purpose of sustaining the safety component addressed earlier, as seen in IRC1 R301.1:
R301.1 Application. Buildings and structures, and parts thereof, shall be constructed to safely support all loads, including dead loads, live loads, roof loads, flood loads, snow loads, wind loads and seismic loads as prescribed by this code. The construction of buildings and structures in accordance with the provisions of this code shall result in a system that provides a complete load path that meets the requirements for the transfer of loads from their point of origin through the load-resisting elements to the foundation. Buildings and structures constructed as prescribed by this code are deemed to comply with the requirements of this section. [Emphasis added]
Licensed engineers will not (likely) risk their professional status or their liability for intentionally designing a structure that does not comply with the parameters described in the code. Engineers are directed by the general provisions found in IRC section R301.1.3:
R301.1.3 Engineered design. Where a building of otherwise conventional construction contains structural elements exceeding the limits of Section R301 or otherwise not conforming to this code, these elements shall be designed in accordance with accepted engineering practice. The extent of such design need only demonstrate compliance of nonconventional elements with other applicable provisions and shall be compatible with the performance of the conventional framed system. Engineered design in accordance with the International Building Code is permitted for buildings and structures, and parts thereof, included in the scope of this code.
The intent should never be to “put the inspector in his or her place” or to disregard his or her concerns, but rather the goal should be to establish a common understanding of each person’s roles and responsibilities and to ensure the prudent advancement of the building process in light of these professional responsibilities. The building official is not to be held liable for any failure of an interpretation, but the IRC does provide for a board of appeals to review an illogical or unjust interpretation.
The issue at hand that you have described is a walk-out condition where the soils were poor. The engineer designed a solution where the offending soils were removed and replaced with graded and compacted gravel (AB-3) for a depth of three feet. The code establishes that the intent for footings is to provide safe load transfer of all building forces to the earth. As written in IRC section R403.1:

R403.1 General. All exterior walls shall be supported on continuous solid or fully grouted masonry or concrete footings, crushed stone footings, wood foundations, or other approved structural systems that shall be of sufficient design to accommodate all loads according to Section R301 and to transmit the resulting loads to the soil within the limitations as determined from the character of the soil. Footings shall be supported on undisturbed natural soils or engineered fill. Concrete footing shall be designed and constructed in accordance with the provisions of Section R403 or in accordance with ACI 332.2 [Emphasis added]
While concrete is the most common footing material seen today (since it is a quality forming platform for formed concrete foundation walls or laid masonry foundation walls), there are also two provisions for all-gravel footings, specifically for wood foundation and precast foundation systems. Both of these “acceptable” footings have characteristics that are less than those applied for concrete footings. These provisions can also be used to further interpret acceptance criteria for situations that fall between the specific or direct application of a code provision. IRC section R403.1.1:
R403.1.1 Minimum size. The minimum width, W, and thickness, T, for concrete footings shall be in accordance with Tables R403.1(1) through R403.1(3) and Figure R403.1(1) or R403.1.3, as applicable. The footing width shall be based on the load-bearing value of the soil in accordance with Table R401.4.1. Footing projections, P, shall be not less than 2 inches (51 mm) and shall not exceed the thickness of the footing. Footing thickness and projection for fireplaces shall be in accordance with Section R1001.2. The size of footings supporting piers and columns shall be based on the tributary load and allowable soil pressure in accordance with Table R401.4.1. Footings for wood foundations shall be in accordance with the details set forth in Section R403.2, and Figures R403.1(2) and R403.1(3). Footings for precast foundations shall be in accordance with the details set forth in Section R403.4, Table R403.4, and Figures R403.4(1) and R403.4(2). [Emphasis added]
These footing provisions for alternative foundation systems show required compacted gravel regions of 16 inches wide by 6 inches deep with gravel backfill up the outside of the foundation wall with protected film in full basement settings or just with gravel footing conditions for crawl spaces when there is not livable space inside. In IRC Table R403.4, which is found on page 110 of the 2018 edition, there are poor soil conditions that require as much as 44 inches of gravel footing below this type of foundation. Similarly, the engineered approach to your condition has a gravel “footing” that was created below your concrete footing to further augment the safe transfer of loads to the soils where lesser soils were insufficient. This depth is less than these high-load, poorer soil conditions. Furthermore, your engineered design proceeded in accordance with section R403.4.1 for the maximum eight-inch lifts to achieve the overall thickness the engineer required. Figure R403.4(2) shows the condition well, where a contained or prepared gravel footing of the required width and thickness is sufficient only for a precast concrete foundation wall, a condition you have essentially created with the replacement of the non-shrink grout layer with a concrete strip footing cast on top of the gravel footing.
The condition of this walk-out design appears from your description to be considered incompatible with the code’s frost protection requirements. This would (should) be delineated in the written statement for non-compliance, which is a required supplement to the review or inspection. If this is the case, the code is clear that a frost-protected foundation can eliminate the need for any footing/foundation element extending below the frost line. Section R403.3 of the IRC states:
R403.3 Frost-protected shallow foundations. For buildings where the monthly mean temperature of the building is maintained at not less than 64°F (18°C), footings are not required to extend below the frost line where protected from frost by insulation in accordance with Figure R403.3(1) and Table R403.3(1).
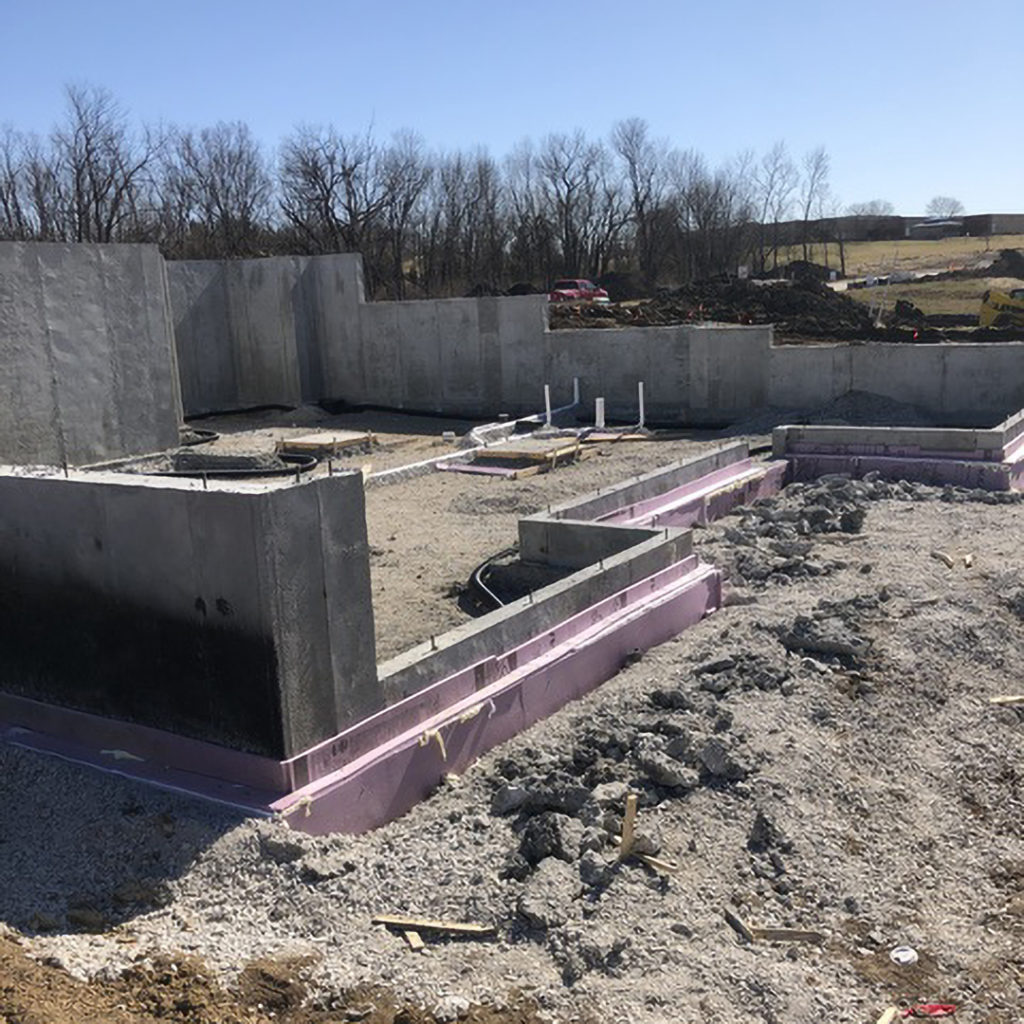
Using Table R403.3(1) as referenced and the accompanying Table R403.3(2) to determine the air-freezing index for your market, we can determine the design condition you would need to create. In the state of Missouri, the Air-Freezing Index for the Greater Kansas City market is 1,500 or less. Therefore, the requirement is for the footing to extend below the finished grade at a minimum of 12 inches and to have the equivalent of 1 inch of an expanded polystyrene insulation (R4.5 per inch) placed vertically through the top of the wall or top of the slab, whichever is greater. I would, however, strongly suggest (and have seen by your photos) the use of an extruded polystyrene insulation (R5 per inch). There is no requirement for horizontal insulation for this low of a freezing index. The design also calls for a minimum of 4 inches of gravel stone base under the footing, which you have achieved with the 3-foot engineered gravel fill that the engineer provided.
Brent Anderson, P.E. of BDA Associates, LLC said: “Frost-protected footings are fairly common in Minnesota, especially in northern Minn. I might suggest you use some spray foam at the joints of the insulation to get a continuous envelope. I generally use two sheets (layered) of insulation to create the required thickness and stagger the seams. In addition, I always recommend a drainpipe next to the foam. If you are in heavy clay soil and poor drainage exists near the foam, water can build up in the voids around the foam and start to saturate it over time. Saturation in the insulation reduces the effective R-value.”
Given the images supplied, non-compliance with the provisions of the code could not be corroborated. Therefore, the statement for non-compliance and rejection of the engineered design is important to obtain so that all parties can come together with a more complete understanding of intent, review and solution. If, however, an amicable solution cannot be established through further commentary and assistance in mediating this issue, the contractor would then be justified to seek a review by a board of appeals. However, it has been my experience that when they are requested to provide supporting documentation for such a position, building inspectors are often ready to find amicable solutions.
1 2018 International Residential Code® For One- and Two-Family Dwellings published by the International Code Council, Inc., 4051 West Flossmoor Road, Country Club Hills, IL 60478-5795 | Phone 1-888-422-7233 | www.iccsafe.org
2 Residential Code Requirements for Structural Concrete (ACI 332-14) and Commentary published by the American Concrete Institute, 38800 Country Club Drive, Farmington Hills, MI 48331 | Phone: 248-848-3700 | www.concrete.org
New Global Campaign Aims to Raise Awareness of the Importance of Concrete
GCCA kicks off year-long outreach programme with campaign to tell ‘Concrete Stories’
‘Concrete Stories’ a major new global communications campaign, which aims to increase awareness of the vital role concrete plays in everyday life, has been launched. The campaign, which is being directed by the Global Cement and Concrete Association (GCCA) and its member companies around the world, was launched at a meeting of Chief Executives from the cement and concrete industry globally at an event in Brussels, Belgium.
The campaign aims to engage members of the public by telling the ‘Story of Concrete’ through a number of different themes including how concrete contributes to everyday life, concrete as an enabler of change, and creative uses of concrete around the world. The GCCA will use digital content to engage members of the public directly via social media platforms. Additional themes will run throughout 2020 and will focus on the important role the cement and concrete industry will play in addressing the challenge of climate change.
Benjamin Sporton, GCCA Chief Executive said: “Concrete is an unsung hero. This is a material that is all around us and which we rarely consider. Throughout 2020 and starting with ‘Concrete Stories’, we want to show its versatility, its beauty as well as its numerous performance credentials. So many parts of our day-to-day lives are made possible by this amazing material.
”Cement and concrete are fundamental to our daily lives – the way we travel, our housing, our work and many other aspects. ‘Concrete Stories’ will bring the role that this ‘super’ material plays into the foreground. The campaign will also showcase the innovations that the cement and concrete industry is developing and show how it can be used in sometimes surprising and often beautiful ways,” he added.
The initial ‘Concrete Stories’ campaign will run for six weeks and will be featured primarily on GCCA’s social media channels. A hero video ‘our world is concrete’ kicks off the launch and will be featured across social media channels. It captures the versatility and key elements of concrete in our modern world – versions in English, Spanish and Chinese are available.
CEOs and Directors of GCCA’s global network of eighteen cement and concrete associations met in Brussels to discuss a range of key issues including innovation, sustainability and the industry’s climate ambition.
PCA Launches ‘Shaped by Concrete’ Educational Campaign
The Portland Cement Association (PCA) today announced Shaped by Concrete, a new educational campaign to increase awareness of the sustainability, resiliency and durability of concrete made with cement. The campaign will feature stories based on these themes, exploring how these construction materials shape the world around us to make our communities, cities and country better. With impacts from climate change, growing populations and accelerating urbanization creating demand for safe, affordable housing, there has never been a more important time to explain how and why concrete became – and continues to be – the material of choice for virtually every type of construction through its positive impacts on society.
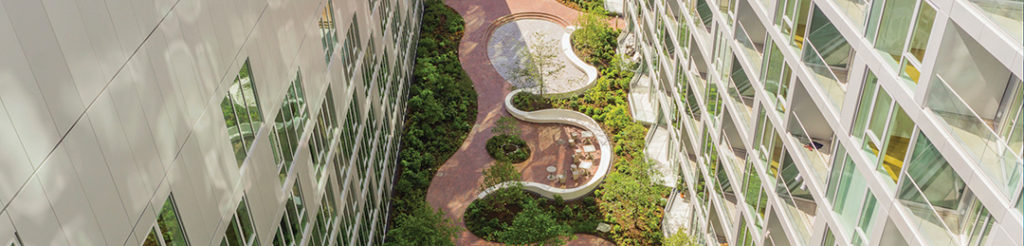
“As we prepare for the challenges future generations face, concrete will be even more critical to building a sustainable world for tomorrow,” said Mike Ireland, president and CEO of the Portland Cement Association. “Concrete is the most durable, resilient, available and affordable material in the built environment, supporting sustainable economic, social and environmental development priorities, and the Shaped by Concrete campaign is how we’ll tell that story to stakeholders and partners.”
Shaped by Concrete will focus on key themes often overlooked and underrepresented in conversations and media coverage of cement and concrete, including their ability to meet sustainable development goals, decrease costs from natural disasters, and assist with key societal challenges, such as our nation’s housing crisis.
A more sustainable material
Concrete, made with the key ingredient cement, is the most widely used man-made material in existence. It is second only to water as the most-consumed resource on Earth. Once mixed, it can be molded into nearly any shape or use. As a sustainable building material, concrete provides energy efficiency, lower life-cycle costs and resilience following natural and man-made disasters.
Compared to other building materials, concrete is a low-impact material, with the amount of energy consumed to extract, refine, process, transport and fabricate, as well as the amount of carbon to produce it being lower than other building materials.
However, because of its unmatched characteristics as a building material and the ability to readily use it, concrete is used in a significantly larger portion of construction – nearly all buildings – than other materials. Not satisfied with this already relatively lower impact, America’s cement manufacturers have undertaken significant efforts to aggressively address its impact on climate change. Cement producers have a strong culture of innovation that has led to a 35% reduction in the amount of energy used to produce a metric ton of cement over the last 47 years. Company-driven improvements have also led to the increased use of alternative fuels. Alternative fuels, such as industrial byproducts that otherwise would end up in landfills, now represent more than 15% of total cement plant energy consumption in the U.S.
Further, exposed concrete (such as roads, buildings, runways, sidewalks, etc.) continually absorbs carbon from the atmosphere and captures it forever, known as carbonation, offsetting emissions from its initial creation. Cement and concrete enable emissions reductions in other industries too. Concrete is an excellent insulator, keeping buildings warmer in the winter and cooler in the summer, thereby reducing building emissions. When used as a pavement, concrete has a much longer lifespan than other materials, requiring less maintenance and ensuring smooth, stiff roads, which improve vehicle fuel efficiency.
“The industry has made major progress toward making concrete more sustainable, and it continues to push the boundaries of energy efficiency and emissions reductions through new research, technology and innovations,” said Jeremy Gregory, executive director, Concrete Sustainability Hub at the Massachusetts Institute of Technology. “Concrete will play a critical role in further decarbonization of the built environment, and I’m excited to see the stories of those advancements from ‘Shaped by Concrete’.”
Creating a resilient and prosperous nation
Concrete structures play a critical role in making communities stronger and safer. Of all construction materials for buildings and other infrastructure, concrete is by far the most disaster-resilient. Concrete improves durability of structures because it doesn’t burn, rust or rot, and is resistant to natural disasters including fire, wind, water and vibrations. This is especially important in the face of increasing numbers of catastrophic weather events, where safe shelter during and after disasters can mean the difference between life and death. That increased durability also provides economic benefits, especially in disaster-prone areas: every $1 spent on resilient building and construction can save $6 in recovery costs according to a recent study by the National Institute of Building Sciences. Considering that in 2017, the 16 largest weather events each caused over $1 billion in damage, savings from resilient concrete construction can quickly scale up.
Just as concrete plays a key role in the revitalization of the nation’s infrastructure, so too does the industry serve as a driver of economic growth and building block of the construction industry. Cement and concrete manufacturing directly or indirectly employs approximately 600,000 people in the U.S., and the collective industries contribute approximately $100 billion to our economy. Ultimately, durable, reliable infrastructure enables a productive, prosperous society and is a critical part of meeting civilization’s needs.
“From national security concerns to durability and safety in the face of natural and man-made disasters to enabling economic growth, cement and concrete make our communities more resilient,” said Tom Beck, PCA Chairman and President of Continental Cement. “‘Shaped by Concrete’ will help our industry show these important benefits and ensure cement and concrete continue to keep our nation safe, secure and prosperous.”
A solid foundation
Cement and concrete have been foundations in advancing society from the earliest of civilizations dating back to iconic structures that are nearly 2,000 years old, such as the Pantheon and Colosseum in Rome.
Today, our country’s most significant investments in infrastructure, transportation, culture and development were built with cement and concrete. Infrastructure projects like the Hoover Dam and the Los Angeles aqueduct helped shape the Western United States. World-class museums, such as the Guggenheim in New York are as stunning on the outside as the master works are on the inside. And our country’s transportation system, from the Metro system in our nation’s capital to the many airports that connect our world, show how cement and concrete are part of our lives every day.
“We are excited to share bold, compelling stories of how we can make the world a better place, shaped by concrete,” said Ireland.
For more information on cement and concrete, and to explore the new Shaped by Concrete campaign, visit www.shapedbyconcrete.com.
The Portland Cement Association (PCA), founded in 1916, is the premier policy research, education, and market intelligence organization serving America’s cement manufacturers. PCA members represents over 90 percent of U.S. cement production capacity and have facilities in all 50 states. The association promotes safety, sustainability, and innovation in all aspects of construction, fosters continuous improvement in cement manufacturing and distribution and generally promotes economic growth and sound infrastructure investment.
Mitch Mccaulley Named Nox-Crete VP of Business Development
Newest hire brings strong leadership, track record of growth to team
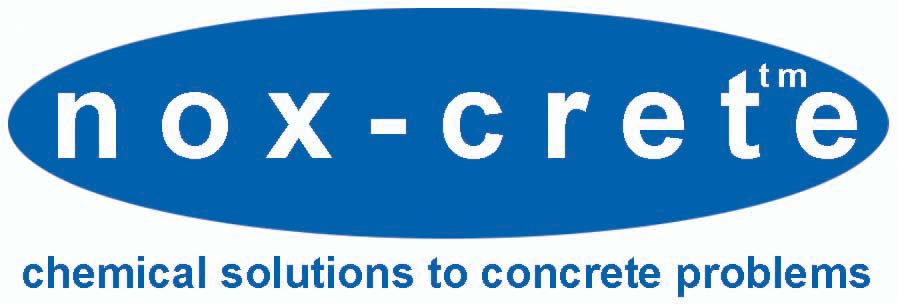
Nox-Crete, Inc. is pleased to announce the addition of Mitch McCaulley to their team. As Vice President of Business Development, Mitch will provide best in class leadership to the strong Nox-Crete sales team and will lend his considerable talents to guide the company in pursuing new opportunities and building strategic partnerships.
McCaulley joins Nox-Crete with a wealth of knowledge and experience within the concrete construction industry, where he has spent the bulk of his career. In addition to his extensive industry experience, Mitch has a strong leadership record, most recently as North American Sales Director for Thermomass/Oldcastle Construction Accessories, the leader in the concrete sandwich wall insulation systems.
Nox-Crete President Lori Reid says McCaulley is an excellent fit for the VP role, where he is sure to be a valuable asset that helps to shape Nox-Crete’s strategic vision.
“Mitch’s experience and growth mindset put he and Nox-Crete in an excellent position to continue a pattern of strategic growth,” Reid said. “We look forward to the positive impact his role will have on the company.”
McCaulley, in turn, is eager to be a part of the Nox-Crete team.
“I’ve long regarded Nox-Crete as an innovator in concrete chemicals and solutions throughout the field,” he said. “It’s exciting to be a part of a company known for such significant contributions, and I’m really looking forward to this role.”
Euclid Chemical Introduces Three Innovative New Products for the Concrete Industry
Product Launches Include EUCOWELD 2.0, LEVEL TOP PC-AGG and KUREZ DR VOX
The Euclid Chemical Company, a leading manufacturer of products for the concrete and masonry construction industry, announces the launch of three new products, Eucoweld 2.0, Level Top PC-AGG and new and improved Kurez DR VOX.
Each high-performance product was developed in response to the needs of construction professionals and was designed to meet a different challenge for new concrete construction, as well as the repair, protection and curing of existing concrete structures.
Euclid Chemical will introduce the new products at the upcoming World of Concrete, the annual international event dedicated to the commercial concrete and masonry construction industries, which will be held in Las Vegas, NV, Feb. 4-7, 2020.
EUCOWELD 2.0
Eucoweld 2.0 is a liquid latex bonding agent for concrete repairs and toppings. This bonding agent is ideal for repairing concrete with cement-based mortars and concrete overlays and toppings. It represents a new generation of easy-to-use latex, which can be applied directly to the surface from the container. Created with a long open-time, repair materials can be placed after Eucoweld 2.0 has dried or while it’s still wet. Drastically improving performance and stability, this unique non-EVA-based latex utilizes reactive chemistry for bonding, rather than depending on the moisture content of the repair material.
LEVEL TOP PC-AGG
Level Top PC-AGG is a polishable, self-leveling overlayment with natural aggregate, that’s easy to use and designed for new or worn concrete substrates. The high-early strength allows polishing within 24 hours of placement and provides excellent adhesion, toughness and long-term durability. It can also be used for countertops, tables, and other poured-in-place or precast applications. Plus, it can be ground, polished and dyed to achieve an appealing concrete appearance.
KUREZ DR VOX
Kurez DR VOX is a dissipating curing compound that provides an excellent initial cure for concrete. Applications include concrete that will later receive a covering or coating, or concrete surfaces where a long-term membrane film is not desired. The new improved version is easier than ever to spray and apply with even coverage. The simple removal process helps reduce labor costs associated with preparing the floor for subsequent treatments and coverings. It also dries leaving a clearer film for a more attractive appearance.