OSHA Crane Operator Certification Compliance Dates Extended
Proposed rule issued to extend compliance date for crane operator certification requirements
OSHA has issued a proposed rule to extend the compliance date for the crane operator certification requirement by three years, to Nov. 10, 2017. The proposal would also extend the phase-in requirement for employers to ensure that their operators are qualified to operate the equipment. OSHA issued a final standard on requirements for cranes and derricks in construction work on Aug. 9, 2010. The standard requires crane operators on construction sites to meet one of four qualification/certification options by Nov. 10, 2014. After OSHA issued the standard, a number of parties raised concerns about the qualification/certification requirements. After conducting several public meetings, OSHA decided to extend the enforcement date so that the certification requirements do not take effect during potential rulemaking or cause disruption to the construction industry.
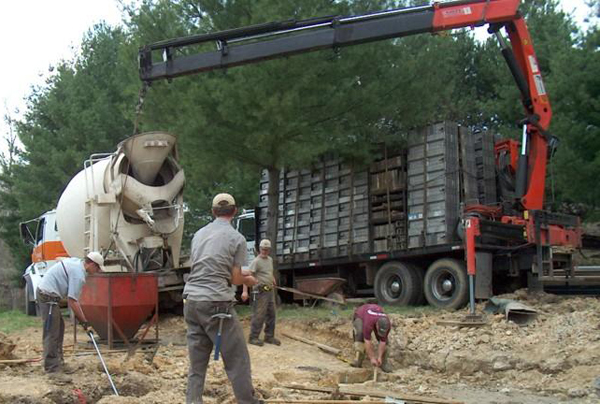
Truck cranes like this one are at the center of part of the debate. Delivering materials, operators may not require certification. Participating in construction, operators will require certification. Companies are at risk with such decisions.
Comments must be submitted by March 12, 2014 and may be submitted electronically at www.regulations.gov, the Federal e-Rulemaking Portal or by facsimile or mail. See the Federal Register notice for submission details and additional information about the proposed rule.
Project Entries for 2014 CFA Projects of the Year: Vote Now!
The 2014 CFA Projects of the Year Voting is now open.
Submitted by CFA members from diverse markets, this year’s crop of projects feature single family residences of monstrous proportion and insanely detailed modest footprints as well as challenging and imaginative multi-family. Never before has this level of detail and achievement been evidenced from submittals to this program.
Be sure to visit these great projects at http://www.cfawalls.org/awards/project/2014/index.php and take the short amount of time to let your opinions be known. Evaluate each project in a couple of easy steps.
Want to know more? Contact CFA headquarters at your convenience at 866-232-9255 or CFA Managing Director, Jim Baty at jbaty@cfawalls.org.
CFA Member Obituary: Gary Lee Bromley
Gary Lee Bromley, 75, of Lee’s Summit, MO passed away Wed. Jan. 15, 2014 at his home. Funeral service will be held on Sat. Jan. 18th at 11am at Woods Chapel UMC. Visitation will be held on Fri. Jan. 17th from 5-7pm at the church. Burial in Lee’s Summit cemetery. Memorial contributions may be made to Harvesters, Re-Discover, or Lee’s Summit Social Services.
Gary was born on Aug. 13th, 1938 in Independence, MO. He was a U.S. Marine Veteran, he attended the University of Missouri, Columbia, he was Captain of the Independence Fire Dept., and founder of ABI Corp., he was the past President of the Lee’s Summit Chamber of Commerce, the Concrete Foundations Association, and the Lee’s Summit Economic Development Council. Gary was a member of the Lee’s Summit United Methodist Church, the Lee’s Summit Rotary, and an 18 year member of the Lee’s Summit Hospital Board. Gary loved to hunt, fish, to be outdoors, and to travel. He was a loving husband, father, grandfather, and a man of great integrity.
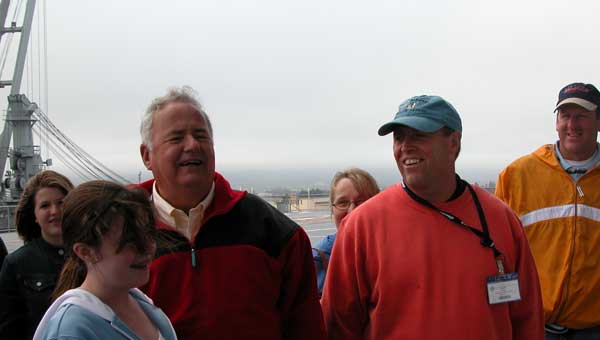
Gary Bromley and Scott Smith of MPW Construction Services enjoying a tour of the USS Nimitz during the 2005 CFA Summer Convention in San Francisco, CA
Gary is preceded in death by his father, Willis Bromley, and mother, Dona Bromley.
Survivors include wife, RoseAnn Bromely, of the home; 5 children, Daniel (Chris), David (Ginger), Jennifer Nye (Todd), Michael (Leah), and Anna Poole; 10 grandchildren, Katie, Matt, Nicholas, Lauren, Raegan, Madison, Coby, Gracie, Shepard,b and Courtney; 2 great- grandchildren, Mckinnley and Delaney, and 1 sister, Carolyn Shuttleworth.
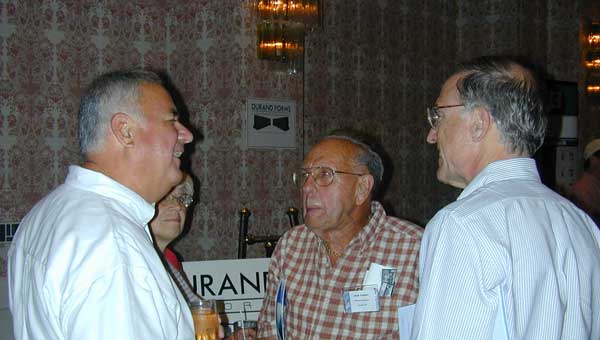
Gary and RoseAnn enjoying the company of Jack Easton during the 2001 CFA Summer Convention in Niagarra Falls, ONT
Online condolences may be left for the family at langsfordfuneralhome.com
Arrangements by:
Langsford Funeral Home
115 sw 3rd St.
Lee’s Summit, MO 64063
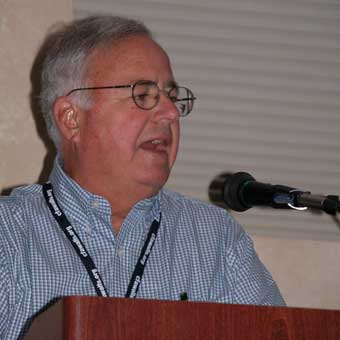
Gary speaks to the gathered attendees at the 2000 CFA Summer Convention in Lake of the Ozarks, Missouri
North American Specialty Products Debuts New Website, Offering Easy Access to Product and Application Information
CFA National Associate Member Debuts New Website
(Wayne, Pa.) – North American Specialty Products LLC (NASP), formerly CertainTeed Pipe and Foundation Group, a leading provider of specialty PVC pipe and residential and commercial building products, has launched a new website — offering easy access to information on its complete line of products and their benefits in a wide variety of projects. The website – www.naspecialtyproducts.com — is organized into sections on PVC pipe products and foundations building products, making it easy to quickly find relevant information.
“Our diverse family of products offer time and labor savings in a number of industries, from municipal sewer and water infrastructure management to energy-efficient residential and commercial construction,” said Mark DaSilva, manager of product development and marketing for North American Specialty Products. “The new website enables our customers to quickly find the information they need when they need it and in doing so helps elevate the North American Specialty Products brand in the diverse markets it serves.”
For NASP’s family of Certa-Lok® restrained-joint PVC pipe, the new website offers specific information on product uses in a wide array of applications, including potable and reclaimed water, gravity and force main sewer, electrical and communication conduit, agricultural irrigation, mining and fluid transfer, and residential and commercial water wells. For each application, the site offers useful information and content in the form of digital product brochures, engineering specification sheets and detailed product information.
To help builders and architects design homes and buildings with superior thermal performance and moisture protection, NASP offers basement waterproofing and remediation solutions such as Platon® waterproofing membrane, Form-A-Drain® concrete footing and drainage system, and above- and below-grade concrete wall insulation products such as T-Roc™ and ThermaEZE™. In addition to detailed information on each product, the new website offers illustrations, photos, installation guides and technical specifications.
For more information, visit http://naspecialtyproducts.com.
About North American Specialty Products LLC
North American Specialty Products LLC, a wholly owned subsidiary of North American Pipe Corporation, is a leading provider of specialty PVC pipe solutions serving the municipal water & sewer, water well, mining & energy and agricultural irrigation markets as well as residential and commercial building products. The company has one of the strongest portfolios of trusted product brands including Certa-Lok®, Yelomine™, Certa-Set®, StraightShot™, Certa-Com™, CertaFlo™, Form-A-Drain® and CertaForm®. For more information, visit http://naspecialtyproducts.com.
The North American Specialty Product logo, Certa-Lok®, Yelomine™, Certa-Set®, StraightShot™, Certa-Com™, CertaFlo™, Platon®, T-Roc™, ThermaEZE™, Form-A-Drain® and CertaForm® are trademarks of North American Specialty Products. All sales of NASP products are subject to NASP’s standard terms and conditions of sale. Except for the warranties made in those terms and conditions, NASP makes no other warranty, whether express or implied, including but not limited to any warranty of merchantability or fitness for particular purpose.
###
For more information contact:
Investors:
Mr. Steve Bender
(713) 960-9111
investorrelations@westlake.com
Media:
Mr. David Hansen
(713) 960-9111
The Time Has Come
Letter from the Executive Director
Those who regularly receive this magazine know I have written several times about the formation of an insurance captive for CFA members. Over the past months the insurance market, as well as efforts to start this captive, have taken significant turns – one for the worse, one for the better. The worse one is that you are currently in a hard insurance market. It is getting more difficult to renew; coverage is being cancelled; and when renewals come, they are likely at significantly higher rates. While this is bad news for the market, it is positive news from the captive perspective. We have your solution!
The better news is that the insurance captive under development for CFA members has reached a point in the formation process that has never before been attained. Commitments from all insurance and underwriting layers have positioned this captive to move forward and set a start date!! The corporation for the entity has been formed and we are in the process of finalizing agreements with the management team and consultants. This has been a seven-year effort to this point and the current developments were essential to the process. There are still several steps to complete but the process is now in our hands. We expect all to be completed so the captive can commence operation by April 1, 2014
As one of our new readers, we want you to be aware of this opportunity. It will affect your insurance future and in a positive way. This is not a group-buying plan, a co-op or any other commercial market ploy.
This is an insurance company owned by the participating companies, companies that have a common scope, interest and composition. The key to this venture is the risk management aspect of the program. Losses from across your industry are collected, evaluated, and used to develop programs to reduce and control those risks. The net result will be lower insurance premiums over time and profitability that will be shared by the owners (insureds) instead of insurance companies. Companies participating will benefit from the company’s claims investigators who are answerable to YOU. Companies that do not participate can still benefit as this industry begins to receive specific risk management concepts that can be implemented through education provided by the CFA.
There is still an opportunity to participate in the start-up of this industry-changing program, but like so many infomercials, “you must act now.” Join with other industry leaders to truly change the way this industry operates from an insurance perspective. If you would like more information, please call us at 866-232-9255 and ask for Jim Baty or me, or email us at esauter@cfawalls.org or jbaty@cfawalls.org. We will connect you to one of the webinars planned in the coming weeks, to the program management team by phone or perhaps schedule a visit to your location as available.
Tired of Breaking Even?
Letter from your president, Jim Bartley
Dear Friends,
Our long, tough recession has had one of two effects on most concrete foundation contractors. Either we went broke, or mastered the art of breaking even. If you are reading this, my guess is you are a fine-tuned, break-even machine! I know I am.
Now that we have a better workload, I need to help my company break the habit of being a non-profit, but how? Raise prices? Good luck outpacing material increases. Increase productivity? What comes first—Productivity or production bonuses? Increase sales? Be careful of increased losses. Cut costs? That’s how we got to break-even. Reduce overhead? Not our talented people!
The answer is probably all of the above, but there is NO low-hanging fruit. Price increases may come easier if we share our results with our customers. We plan to tell them if we’re losing money! Increased productivity from our teams may happen if we share information, set goals, measure productivity, and reward success. Profits can bring wage increases and bonuses. Increase sales in a targeted way. Push products and services that bring profits. Good cost cutting may come by minimizing material increases. And finally, cut my management staff? That is where I draw the line! My people are too valuable! And furthermore, who has time for these changes anyway?!
I know. It is easy to lose money, and hard to earn it. We have to find ways to make the process easier. Start by developing a plan. In our company we call it the 5% plan (for 5% profit in 2014). Avoid reinventing the wheel—Consult your peers and gather ideas. Talk to CFA members on the phone, at World of Concrete, at “Live-before-5, or on Linked In. Avoid solving it alone—Involve your people in the process. Instead of cutting our management staff, we are asking them to help develop and implement the 5% plan.
Believe me… I don’t have all the answers. Our 5% plan is just getting started. Step one for us was continuing our CFA membership. Without the help and ideas from our CFA friends, we would be broke instead of break-even.
See you in Las Vegas! Hopefully, as we talk at breakfast, at the booth, and at the bar we can break through to 5% and beyond!
Happy Holidays!
What Should You Expect from 2014?
Codes, Standards, Rules, Regulations and Insurance…It is All Changing
It really doesn’t matter that your profession is the concrete industry. Were you in just about any industry, the rules for doing business and the parameters that shape your industry are likely to be changing such that business next year, perhaps even tomorrow, will most certainly be different than it is today.
Anthony Robbins is quoted as having said “If you’re not growing, you’re dying.” Perhaps a derivation of this might be “If you’re not changing, you’re being passed by.” Oddly enough, that seems to be the case as we all know that “Change is inevitable” – dd. In fact, perhaps the best way to prepare for 2014 and all of the changes that you will have to account for is best embodied by Albert Einstein who stated, “The world as we have created it is a process of our thinking. It cannot be changed without changing our thinking.” In essence, we must adapt to the changes we are given for they are nothing more than responses to the thinking continually occurring with change in mind for a changing world.
Although no one can deny that enough has changed in 2013, there are some very important characteristics of the construction environments in which you work as well as the business environments that you manage to be sure you have prepared for in the coming year. Here are a few we have been involved in or tracking and will most certainly be expanding for greater knowledge as more becomes available.
SILICA REGULATIONS – OSHA
While it seems every aspect of the construction site is already controlled for the minutia that might happen to replace common sense and responsibility? The impending regulations for control of air-borne silica are yet further example of the exhaustive measures contractors now must face.
The rule is based on the facts that inhalation of very fine particles of crystalline silica put workers at risk for silicosis, lunch cancer, COPD and even kidney disease (www.OSHA.gov). The Assistant Secretary of Labor for OSHA, Dr. David Michaels has been quoted saying, “Exposure to silica can be deadly, and limiting that exposure is essential.” The basis for regulation is the prediction that the proposed rule will save nearly 700 lives and prevent 1,600 new cases of these diseases per year.
A two-part rule, one for general industry and one for construction focuses on the processes that introduce these “respirable” particles of silica. OSHA has set up a website for information at https://www.osha.gov/silica/. Here you can gain access to the research, the proposed rule making and the remaining steps. However, the short and sweet of it for construction professionals as summarized by OSHA’s Fact Sheet for the proposed standard for construction. Under this rule, employers would have to:
- Measure the amount of silica that workers are exposed to if it may be at or above an action level of 25 μg/m3 (micrograms of silica per cubic meter of air), averaged over an 8-hour day;
- Protect workers from respirable crystalline silica exposures above the PEL of 50 μg/m3, averaged over an 8-hour day;
- Limit workers’ access to areas where they could be exposed above the PEL;
- Use dust controls to protect workers from silica exposures above the PEL;
- Provide respirators to workers when dust controls cannot limit exposures to the PEL;
- Offer medical exams-including chest X-rays and lung function tests-every three years for workers exposed above the PEL for 30 or more days per year;
- Train workers on work operations that result in silica exposure and ways to limit exposure; and
- Keep records of workers’ silica exposure and medical exams.
How does this impact the concrete foundations industry? How many concrete saws does your company own? How many foundations have your workers cutting out a notch, altering a wall profile, sanding a surface, cutting concrete blocks and a myriad of other processes that introduce the silica cut or abraded from the hardened concrete into the air.
In response to requests for an extension on the rulemaking, the deadline to submit written comments and testimony is being extended from Dec. 11, 2013, to Jan. 27, 2014, to allow stakeholders additional time to comment on the proposed rule and supporting analyses. Additional information on the proposed rule, including five fact sheets and procedures for submitting written comments and participating in public hearings, is available at https://www.osha.gov/silica/. Members of the public may comment on the proposal by visiting http://www.regulations.gov.
FALL PROTECTION – OSHA
Although it should not be a surprise to any concrete professional in the residential industry, there are still hundreds of questions being asked about the implications of the requirement for fall protection. What measures are implemented on your jobsites to provide active or passive fall protection for your workers? By the rule making completed in 2010, this industry suddenly became responsible for implementing any combination of six active fall protection measures during the construction of cast-in-place concrete foundations. These include scaffold brackets, personal fall arrest, guardrails, safety nets, ladders and aerial lifts. Under practical study and exposure to greater risk, many CFA members have generated evidence that these systems cannot provide worker safety due to technological or physical restrictions to their safety parameters or they induce greater worker stress and risk during their installation, if they can achieve protection at all.
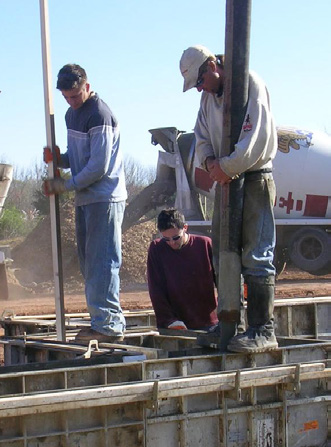
“Wall walkers” or “Wall shufflers” are an acceptable form of fall protection under 1926.502k provided a company has a formalized plan.
Work continues on the acceptance criteria and implementation of Alternate Fall Protection plans per section 1926.502(k) of OSHA’s rule. Here contractors implement a series of training, decision making, application and awareness measures to maintain the presence of fall protection on job sites under the responsibilities of trained, informed and even certified personnel.
If your company has not investigated your fall protection and determined the effective course of action, you should do so immediately and this winter is as perfect a time as any. CFA members have access to an Alternate Fall Protection Plan Kit developed to aid in the understanding and delivery of the essential components of a successful implementation. As this rule matures and as OSHA plans inspections more broadly, it will become more severe in its impact on employer responsibility. Additional work is underway to investigate a national plan or acceptance criteria for concrete foundation delivery and this may become a part of the current certification programs offered through the CFA and ACI.
CONCRETE DURABILITY REQUIREMENTS – ACI 332 STANDARD
Since its inception in 2004, the ACI 332 document Code Requirements for Residential Concrete, an acceptable alternative to the provisions of the International Residential Code, have applied concrete durability requirements similar to that of the IRC using weathering probability and a loosely-defined geographic map to set the minimum requirements.
With the pending release of ACI 332-13, the durability requirements for residential concrete will become more widely addressed to represent the breadth of exposure conditions. Concrete is prescribed by this new version of the code to be variable based on exposure to freeze/thaw cycling, sulfates and corrosive environments.
This is a similar approach to that taken by ACI 318 and offers the concrete professional and jurisdictions a more specific control of mix design for the anticipated exposure conditions. It also means that geographic reference based on maps is no longer the simple method of selecting the minimum strength requirements for concrete. Performance of concrete mix designs is largely the direction of this code and requiring greater knowledge of the conditions for delivery and service.
WORKPLACE INJURY AND ILLNESS TRACKING – OSHA
Underway is another OSHA proposed ruling that would require employers to keep a greater volume of records for workplace injuries and illness. Under this proposed rule, OSHA hopes to “improve both workplace safety and health through the collection of useful, accessible, establishment-specific injury and illness data to which OSHA currently does not have direct, timely and systematic access.” This will be accomplished by amending the workplace recordkeeping regulations and add requirements for electronic submission.
While this may be seen as only increasing the amount of clerical activity and record-keeping in an already paper laden environment, OSHA suggests that this will “not add to or change any employer’s obligation to complete and retain injury and illness records.” Their purpose is in increasing the transmission of these records to OSHA or OSHA’s designee.
The docket number for this proposed ruling is OSHA-2013-0023. It is advisable to communicate your concerns for this either electronically at www.regulations.gov or by fax to (202) 693-1648. You must include the docket reference in your response. It is likely that the CFA will only increase our recommendation for communication of concerns on this issue and we are also interested in learning your thoughts. Email me at jbaty@cfawalls.org to share your concerns privately with us. There will also be a discussion thread on this in our public “Concrete Foundations” group at LinkedIn.
COMPLIANCE SAFETY ACCOUNTABILITY (CSA)
Much information has been released by this Association on the potential impact CSA will have on your businesses. While it was instituted initially for large commercial carriers, as the efficiency of the Federal Motor Carrier Safety Administration (FMCSA) and Departments of Transportation has increased, their focus has begun to broaden. All companies that employ CDLs should expect to be impacted by this new carrier and driver rating system.
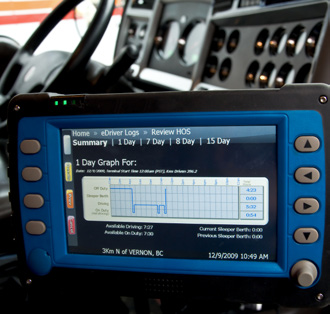
Typical electronic logging device currently pursued as a mandate by FMCSA for all commercial trucks.
Among the most recent mandates affected by this effort, the Electronic Log Mandate is certainly one you should be paying attention to. The FMCSA is attempting to complete work on a mandate in 2013 to require all truck drivers to use an electronic logging device.
Similar to the issues related to workplace recording, federal agencies are working to become as efficient as possible in the collection of data generated by the market. This particular mandate has four primary elements:
- Setting standards for the EOBR devices themselves,
- The requirement that drivers use them,
- Requirements for other hours-of-service support documents, and
- Measures to mitigate harassment of drivers by either carriers or enforcement officials.
Final ruling on these issues was expected in September but has yet to be confirmed to be in effect. CFA member, Foley Services (www. foleyservices.com), is a resource companies can contact to find out up to date information on rules and regulations affecting the transportation industry. Matt Wrobel, Vice President for Foley was present during the Annual Convention in New Mexico this past August to address the conference on the facts surrounding CSA. An update on these issues is being planned for the 2014 Annual Convention in Sandusky, Ohio (July 31 – Aug 2).
There will be more rules, regulations and changes to your business. As the authority for your industry, we are committed to keeping abreast of as many of these as possible and making sure you have access to the information that can make or break your success. If you are aware of additional pieces of legislation, code or rule making that should be made available to the industry, be sure to contact CFA Headquarters through any of our media outlets or contact points to start this discussion.
Bilco Introduces Redesigned Window Well System
Enhanced Design Allows System to Fit Wider Applications
NEW HAVEN, CT/December 3, 2013 – The stakWEL® Egress Window Well system consists of modular units that simply stack and mate together to accommodate virtually any foundation depth. The Bilco Company is pleased to announce that system has been redesigned to now accommodate window openings up to 54” in width.
Previously, the stakWEL system and optional cover were restricted to only openings up to 48″ in width. With this new design, the system will now easily install over windows wider than 48″ or poured-in-place windows that are 48” in width and have an additional perimeter frame. The wider module width allows installers to simply anchor stakWEL modules directly to the concrete foundation, eliminating the extra work that is typically required to anchor to a steel window frame or buck. The built-in mounting flanges feature key holes for fast and easy installation and an optional cover is available to ensure that the well opening is protected and free of snow, leaves and debris.
The stakWEL®Window Well System can be used with both utility and egress windows and offers a maintenance-free alternative to builders and homeowners. The product meets building code (IRC 2012) requirements for emergency egress in finished basement areas. Its innovative design features a built-in grip/step that facilitates safe egress and eliminates the need for a costly and unsightly fixed ladder.
Constructed of corrosion-resistant high-density polyethylene, stakWEL® is impervious to soil and moisture conditions and will not rust, rot, or discolor. It comes in a neutral driftwood color and features a pebbled interior finish that will compliment the interior of any home.
For more information on the stakWEL® Window Well system or any of the company’s code-compliant basement egress line of products, call (800) 854-9724 or visit www.bilco.com.
About Bilco
For over 85 years, The Bilco Company has been a building industry pioneer in the design and development of specialty access products. Over these years, the company has built a reputation among homeowners, builders, architects, and engineers for products that are unequaled in design and workmanship. Bilco – an ISO 9001 certified company – offers a line of egress window wells and Bilco basement doors that improve the look, function, and safety of basement areas, along with a complete line of commercial access products. For more information, visit www.bilco.com.
Keep up with the latest news from The Bilco Company by following their social media profiles: www.facebook.com/TheBilcoCompany and http://www.linkedin.com/Bilco.
###
Casting Foundation Concrete in Cold Weather
Expanded from Q&A Article seen in Concrete Contractor magazine.
by James R. Baty II, CFA Managing DirectorThe Concrete Foundations Association explains how commonly and effectively residential concrete foundations are constructed during the winter.
Question: Our foundations scheduled for installation these next few months will be affected by projected temperatures in the mid 30s to mid 40s. What advice is there to ensure my customers and our building inspectors that the walls will perform as designed? – Concrete Contractor (Wisconsin).
Answer: There is no denying that the vast majority of basement markets in the U.S. are turning colder, colder to the point of concern from customers, code officials and building inspectors as to what will happen to the concrete during these placements. A wealth of information has been generated in the past decade substantiating the recommended procedures necessary to produce quality foundation concrete during these conditions. Documents such as the CFA Cold Weather Research Report, ACI 332R-06 Guide to Residential Concrete, ACI 332-10 Residential Code Requirements for Structural Concrete, and ACI 306 Guide to Cold Weather Concrete, all establish consensus for the contractor to proceed with both caution and confidence under cold weather conditions.
In order for cold weather foundation installations to be successful, there are some hard rules to recognize and follow. Most of these are related to the supporting soil condition, but some do affect the concrete and form preparation.
- The excavation must be not be frozen and must also be free of frost. A foundation is designed to transfer the building load to the ground. This most often involves a foundation wall and a footing, the latter contacting the soil condition. The foundation system is designed based on the strength or rather that bearing capacity of the supporting soil. When ground becomes frozen, its volume expands from the creation of ice particles and therefore changes its support condition. Once frozen ground has received a structure, that structure is falsely supported by the expanded grade and will experience settlement as the ground thaws. Similarly, ground with frost introduces both volume change and additional moisture to the grade condition for the concrete placement. While settlement may not be as likely here, the moisture present in the frost condition is moisture beyond what the mix design considers and may impact the water-cementitious material ratio that is rather important to strength development. This consideration is documented in ACI 306: 6.3—Subgrade conditionConcrete should not be placed on frozen subgrade. Remove all frost before placing the concrete and recompact thawed soil disturbed by frost. Placement of insulation over the subgrade, or provision of heat, is required to remove any frost in the soil and to raise the subgrade temperature above 32°F (0°C). An appropriate provision for heat should be selected based on the amount of frost depth and temperature difference with the air. Once thawed and recompacted, insulation should be placed directly over the subgrade to protect it from refreezing.
- Concrete must be protected from freezing until it has reached 500 psi. It must be protected from multiple freeze/thaw cycles until it has reached 1,500 psi. ACI 332-10 provides the following requirement for residential concrete:6.6.1 During anticipated ambient temperature conditions of 35°F or less, concrete temperature shall be maintained above a frozen state until a concrete compressive strength of 500 psi has been reached.The freezing point of concrete is in the neighborhood of 27°F, depending on the concrete mix. Both ACI 332 and ACI 306 establish a benchmark ambient or air temperature that contractors should consider targeting their monitoring or application of protection for freshly placed concrete. Concrete has remarkable strength gain characteristics due to the natural hydration process. Chemical processes result in a by-product and for hydration of cement the by-product produced is heat. This is a significant benefit to cold weather concrete, particularly for the construction of foundations. Foundation walls are most commonly created in vertical forms, set below the surrounding grade in an excavation…a protected environment. The forms are wood, steel, aluminum or in some cases insulation. All of these forming systems protect the concrete from air movement across the largest surface areas and therefore prevent convention from accelerating temperature and moisture loss. Significant research conducted on full-scale wall elements by the CFA has resulted in a more thorough understanding of this performance. So much so that with confidence, contractors have escalated the amount of cold weather foundations they install and have decreased the average cost of protection systems. The CFA Cold Weather Research Report offers:
Full analysis of the temperature histories of the wall segments and ambient conditions reveals that the mass of the curing concrete kept the concrete above ambient for at least the first 24 hours after placement, even in the leanest of mixtures. It is also observed that the cement content and type played a very large role in how long the concrete stayed above ambient temperatures.
During temperature periods beginning at 35°F and dropping significantly lower, concrete has the proven ability to self-sustain internal temperature permitting strength gain beyond the critical benchmark of 500 psi. This does not mean that concrete walls will not freeze, as they will and they may below the 500 psi benchmark. Contractors must also understand the behavior of even colder ambient temperatures that may flash freeze concrete or accelerate the temperature drop so that they can plan protection such as blankets and in the most severe cases, auxiliary heat sufficient to meet the strength gain goals.
- Mix design must be considered a top priority for successful cold weather concrete. Although the research statement above suggests that even lean concrete mixes perform well, it is important to realize that there are four important cold weather mix design decisions that set cold weather concrete up for success. The first is the water-cementitious material ratio. Water is required for the hydration process and is consumed by it. However, water is also the culprit for freezing. The higher the water content, the more susceptible the concrete is to early freezing. The CFA Cold Weather Report identifies:
There is a significant impact resulting from adding excessive water to concrete under cold weather conditions—the greater the water content, the greater the affect those freezing conditions will have on the concrete. A 6-inch slump may be acceptable, but a high water to cement ratio is not.
Cement type is another important decision. Most markets will offer Type III cement with characteristics of faster strength gain. While Type I cement is proven to be successful in cold weather conditions, Type III can give extra control and protection from the aspect of higher internal temperatures resulting in accelerated strength gain. Another aspect of the decision process for cold weather concrete is the use of admixtures. Calcium chloride has been the predominant cold-weather admixture for the residential concrete industry with decades of success. CaCl2, however, does increase the corrosion potential of reinforcement present in the foundation wall and therefore may not be the best solution. There are plenty of additional admixture options with non-chloride chemistry (NCAs) that research evidences as every bit as successful. The limits to amount of calcium chloride combined with the consideration for reinforcement compared to the cost of the non-chloride admixtures makes cost-effectiveness and control important to the contractor. The final, mix decision is temperature at production and delivery. This is a very important consideration for both producer and contractor. The higher the concrete temperature at delivery time, the more likely 500 psi will be attained in very cold conditions before freezing. The vast majority of residential foundations do not have enough mass present in reinforcement and forming systems to cause concern for a large difference between higher concrete delivery temperatures and the in-place low temperatures of those materials. While this can be a concern when such mass is high in that it may cause a portion of the concrete to drop in temperature more rapidly than other areas, residential concrete foundations do not pose this issue. These practice decisions are described in greater detail in the CFA Cold Weather Report such as:
Contractors should work with their local ready-mixed concrete producer to design concrete mixes that will perform well based on the expected variables for a placement. The mix designs used in this research provide a sound basis for your own mix development but should be used after localized testing.
CFA member, Dennis Purinton of Purinton Builders in East Granby, Conn. was asked about his thoughts on cold weather concrete foundations. “The four most important things to remember in cold weather concreting are 1) mix design, 2) concrete temperature, 3) CONCRETE TEMPERATURE and 4) the correct balance of accelerator to concrete temperature.” Dennis is a CFA Board member as well as a voting member on ACI 306 along with CFA Managing Director, Jim Baty. Dennis is also the head of a new task force CFA has formed to research cold weather performance of residential concrete slabs.
A wealth of recommendations is available in the resources this industry has at its disposal. ACI 332-10, ACI 332R-06 and ACI 306 are all available through the bookstore at www.concrete.org. The CFA Cold Weather Report is likewise available through the online order system at www.cfaconcretepros.org. CFA also offers its members annual free webinars on cold weather concrete preparation as well as a task force that members can access for discussion and experience. The most important aspect of cold weather concrete foundations is to understand that one solution does not fit every contractor, market or project condition and certainly all temperature ranges. There is great economy and performance that can be attained by identifying the variables that contractor and producer together can control. Most contractors develop a range of three to four mixes to use each season, dependent on the target ambient temperatures for their placements. Want to know more? Contact CFA Managing Director, Jim Baty at 319-895-6940 or by email at jbaty@cfaconcretepros.org.
Residential Construction Spending Hits Highest Level Since August 2008
Residential Construction Spending Hits Highest Level Since August 2008
Source: NATIONAL ASSOCIATION OF HOME BUILDERS
Created:
Total private residential construction spending rose 1.2% in August and is 18.7% higher than a year ago, with all segments showing growth
Total private residential construction spending is at its highest level since August 2008.
Private residential construction spending increased to a seasonally adjusted annual rate of $340.2 billion in August 2013 according to Census estimates. August data for construction put in place data was released today after a three-week delay due to the government shutdown.
The current reading is a 1.2% increase from the prior month and 18.7% higher than a year ago. After a tepid July, the pace of growth in construction spending improved in August.
Since market low points, total private residential construction spending is up 48.9% — single-family 88.5%; multifamily 146.6% — and improvement-related spending has grown 30.7%. Spending continues to improve for all categories, but remains well below their respective peaks.
Single-family spending registered an increase of 1.6% in August, while multifamily spending increased a healthy 3.2%. The home improvement category remained relatively flat with an increase of just 0.2% for the month.
For August, on a three-month moving average basis, all categories continued to experience significant improvements over the course of 2013. Remodeling related spending is up 8.4% for the year-to-date. Single-family spending has increased by 12.9% and multifamily spending has increased 15.8%.
The data show improvements in construction for all categories. However, the government shutdown had yet to occur and is not reflected in the August data.
A revised schedule posted by the Census indicates that September data for construction put in place will also be delayed one month. The September and October data are scheduled for release on the same date – December 2. This release should provide a better picture of construction spending moving forward.