OSHA New Confined Space Rule
OSHA CLAIMS NEW CONFINED SPACE RULE WILL PREVENT 780 INJURIES A YEAR
The Occupational Safety and Health Administration issued a final rule to increase protections for construction workers in confined spaces. Confined spaces are described by OSHA as spaces not designed for people yet large enough for workers to enter and perform certain jobs. They have limited or restricted means of entry or exit and are not designed for continuous occupancy. Those contractors working in the concrete foundation industry may see this as a developing change to the configuration of safety measures between the outer erected wall of formwork and the edge of an excavation. Presently, OSHA defines the minimum requirement for this distance as three (3) feet in Subpart P.
The final ruling states that “an estimated 6 fatalities and 812 injuries occur annually among employees involved in construction work in confined spaces addressed by the provisions of this rulemaking. Based on a review and analysis of the incident reports associated with the reported injuries and fatalities, OSHA expects full compliance with the final rule to prevent 96 percent of the relevant injuries and fatalities. Thus, OSHA estimates that the final rule will prevent approximately 5.2 fatalities and 780 additional injuries annually.”
“In the construction industry, entering confined spaces is often necessary, but fatalities like these don’t have to happen,” said Secretary of Labor Thomas E. Perez. “This new rule will significantly improve the safety of construction workers who enter confined spaces. In fact, we estimate that it will prevent about 780 serious injuries every year.”
The rule will provide construction workers with protections similar to those manufacturing and general industry workers have had for more than two decades, with some differences tailored to the construction industry. These include requirements to ensure that multiple employers share vital safety information and to continuously monitor hazards — a safety option made possible by technological advances after the manufacturing and general industry standards were created.
“This rule will save lives of construction workers,” said Assistant Secretary of Labor for Occupational Safety and Health Dr. David Michaels. “Unlike most general industry worksites, construction sites are continually evolving, with the number and characteristics of confined spaces changing as work progresses. This rule emphasizes training, continuous worksite evaluation and communication requirements to further protect workers’ safety and health.”
Any time OSHA issues a final rule that impacts the construction industry, the cost of construction begins to escalate and employers are both at risk for non-compliance as well as lower productivity due to changes in training, education or certification. Therefore, it is important to understand the implications and applications of such specific final rulings. In the case of this final ruling for confined space, OSHA has determined that it is not directly applicable to any excavation or trench that falls under subpart P of 1926. The final ruling on confined space states, “OSHA agrees that subpart P, and not this confined space standard, would apply to the construction of most house foundations in an excavated area until the contractor backfills the area adjacent to the foundation or otherwise covers the foundation or the other areas. “
Subpart P defines the regulations for construction work in excavations. A list of the requirements for confined space and excavation safety includes:
- When forms or other structures are installed or constructed in an excavation so as to reduce the dimension measured from the forms or structure to the side of the excavation to 15 feet or less (measured at the bottom of the excavation), the excavation is considered to be a trench.
- The bottom of the excavation, from the excavation face to the formwork or wall, must not be less than 2 feet wide.
- A stairway, ladder, ramp or other safe means of egress shall be located in trench excavations that are 4 feet or more in depth so as to require no more than 25 feet of lateral travel for employees.
- No employee shall be permitted underneath loads handled by lifting or digging equipment. Employees shall be required to stand away from any vehicle being loaded or unloaded to avoid being struck by any spillage or falling materials. Operators may remain in the cabs of vehicles being loaded or unloaded when the vehicles are equipped, in accordance with 1926.601(b)(6), to provide adequate protection for the operator during loading and unloading operations.
- Employees shall be protected from excavated or other materials or equipment that could pose a hazard by falling or rolling into excavations. Protection shall be provided by placing and keeping such materials or equipment at least 2 feet from the edge of excavations, or by the use of retaining devices that are sufficient to prevent materials or equipment from falling or rolling into excavations, or by a combination of both if necessary.
- Each employee in an excavation shall be protected from cave-ins by an adequate protective system designed in accordance with paragraph (b) or (c) of this section except when made entirely in rock; are less than 5 feet in depth and examined by a competent person to have no indication of a potential cave-in; or have a protective system present with capacity to resist all reasonably expected loads.
- All simple slope excavations 20 feet or less in depth shall have a minimum allowable slope of 3⁄4:1 for Type A soil and 1:1 in Type B soil.
- All benched excavations 20 feet or less in depth shall conform to maximum bench dimensions of 5 feet heights and 4 feet runs for Type A soil and 4 feet heights and 4 feet runs for Type B soil when cohesive.
More direction on confined space and excavations are made available in the complete 1926 subpart P online at www.osha.gov.
The final ruling on confined space does leave room for interpretation for house foundations stating, “however, depending on the particular circumstances at the worksite, once the backfill or other covering occurs, the area inside the foundation space could be a confined space subject to this final rule if it meets all of the criteria in the definition of a confined space in 1926.1201.” Therefore, the concrete foundation industry is still advised to understand the implications of this new confined space final ruling and the accompanying standard.
Compliance assistance material and additional information is also available on OSHA’s Confined Spaces.
SOURCE: OCCUPATIONAL
SAFETY & HEALTH
ADMINISTRATION MAY 4, 2015
MARKETING SPOTLIGHT: E-Marketing To Your Market
AN INTERVIEW WITH JASON ELLS ABOUT CUSTOM CONCRETE’S “THE CONCRETE POST”
By James Baty
CFA Executive Director
Perhaps one of the biggest challenges today is finding the right combination of message and vehicles to reach your customers and elevate your company above the competition. There is no doubt you’ve thought of Facebook, Twitter, Pinterest, LinkedIn, Google and many other popular social media outlets to test the water in your ability to market. How about your website? What look and message does it convey to a generation of owners quickly moving toward the label of “seekers?” These persons will use every bit of information at their disposal…from the Internet…to make their decision. Then, to most of us in today’s business world there is the never-ending barrage of email. While it might be suggested that email is overused and over-burdening to business today, it remains one of the most effective ways to achieve a wide variety of goals in one well-organized and strategic move.
I was able to connect recently with Jason Ells, Executive Director of Operations for Custom Concrete in Westfield, Indiana and garner a few minutes from his busy schedule to find out more about their e-marketing or electronic newsletter. It is titled ‘The Concrete Post’ and offers a wide variety of interests and topics conveyed to their market. A sample of their most recent edition is shown to the right.
James: Jason, that was a great-looking e-marketing piece distributed by your company recently. How long have you been producing and distributing an e-marketing piece like ‘The Concrete Post’?
Jason: We launched it in 2014, in conjunction with an updated website.
James: Rolling out a new website and a new communication vehicle at the same time had to be challenging. Did you look at the e-marketing as being purposed to drive people to the new site?
Jason: The email marketing is a small part of our overall strategy that integrates our website and social media efforts as well. The email efforts push people to our website to read our blog etc. and we have noticed a significant uptick in contacts and queries (via Google Analytic) through our website as a result.
James: It does have a great look and organized feel to it. I’m curious about your focus. Do you specifically target markets or demographics with your e-marketing content or do you produce single content to all that are subscribed to your distribution?
Jason: At this point, we are sending this e-marketing piece to both our external and internal audiences, across all verticals/industries.
James: I suspect that is challenging enough in the frenetic pace of today’s concrete industry to get one well-done piece out much less consider varying a message to the type of customer or subscriber. I’m always curious about the response that these pieces receive. How often would you say a customer or a potential customer mentions an e-marketing piece that they’ve seen from you recently?
Jason: We receive comments regularly; more importantly, we utilize a very cost effective e-marketing platform (www.MailChimp.com) that allows us to track open and click rates. The last email blast we sent out had a 38.5% open rate, well above the 22% industry standard.
James: That is certainly impressive and I would imagine it is largely related to finding the right content, the right trigger initially to get someone to interact with the piece. Personally, I found the photo contest a very creative interaction with your audience. Do you get many submittals from it?
Jason: Yes! It’s really created some engagement and friendly competition among staff.
James: Competition among staff can be very beneficial. It is easy for us to become complacent in the business roles we have. I certainly see that sort of impactful competition in the growing submittals to the CFA Projects of the Year competition (See article here). What would you say is the number one thing you’ve learned about your company in the undertaking of an e-marketing campaign?
Jason: We discovered that you have to find something that really engages them, not just pushes out information that you believe they need to know. Learning how to uncover that or really step outside of ourselves to determine what information will do that has been our biggest learning curve.
James: Ah yes, the learning curve. I believe this is the one thing that most keeps companies from getting involved in some of the technology that defines best business practices today; the reason why there are so few current or updated websites, social media engagements and even e-marketing efforts like this. Attacking the learning curve then might be suggested the biggest factor in differentiating yourself from competitors. What might be a word of advice you’d offer to companies considering e-marketing or perhaps even those opposed to spending the time implementing a campaign?
Jason: The bottom line is … well, the bottom line. We are ultimately using e-marketing as a means to generate leads and sales. A website should really act as one of your best sales people … when you think of it that way … a $5 – $10K investment and another $10K annually to maintain, update, and manage social media … versus another sales person, the ROI is exceedingly reasonable for the reach you are receiving. That said, you need to have a solid foundation of a strong website with regularly updated content.
James: This is all very impressive and I very much enjoy the content that your company brings out in each issue of ‘The Concrete Post.’ I also found the name to have a great feel. Excellent job and I look forward to future editions and seeing how this generates even greater leadership for your team.
While e-marketing can be a scary proposition, even some of the concepts that Jason describes about learning your customers and finding the right messages, it continues to be seen as a powerful tool for business today. You have to be different, you have to be branded with consistency and maintain your integrity. All of these vehicles permit ways to demonstrate the consistency in your message and integrity. The balance found in the ROI of comparing an additional personality on your sales team to vehicles that all existing sales and operation team members can participate and multiply themselves is a difficult task to undertake.
Let me encourage your company leadership to be consider what the network of the Concrete Foundations Association can do to move that forward. Professional peers like Jason find great energy in sharing strategies and conveying both success and failure to make your progress more efficient and effective. They are confident in finding the same from you in other areas. Attend CFA Convention 2015 and get to know this powerful business tool for today and tomorrow that is the Concrete Foundations Association.
CFA PROJECTS OF THE YEAR
THE CFA PROJECTS OF THE YEAR AS DETERMINED BY YOU….
What work is your company proud of most when completed? How many foundations have you scrutinized during estimating, fought during construction and perfected through closeout? When the project is completed, does your crew and your company for that matter get a chance to pause a moment as the final trash is cleared and the last truck is ready to drive off the site to realize that it was truly another achievement? This is the primary reason why the Concrete Foundations Association (CFA) first created a competition for the industry in the late 90’s.
Submittals for the competition are due in to the Association each December or January. Projects can be submitted across the entire spectrum of work performed by the membership of the Association and categories are open for expansion to ensure proper representation and opportunity. Originally, the program recognized one project as the “Basement from Hell” projecting the complex challenge that can be faced. Today, the program is about achievement and quality no matter the project and many above-grade projects have been submitted as well as non-basement structures. The awards will be presented publicly during CFA Convention 2015, to be held in Williamsburg, Va. July 23- 25. Among the projects receiving recognition this year are three residential foundations, an above-grade concrete home and a college educational facility. “It is clear the markets across this country have been increasing as the number of entries to this program are increasing,” stated Jim Baty, executive director for the CFA. “What is even more impressive is the growth of types of projects submitted including apartment complexes, educational buildings and even a fire station along with another great year of challenging foundations”
This year, projects competed in categories for foundations for single-family residences split into three sizes (less than 2,000 square-feet, between 2,000 and 5,000 square-feet and greater than 5,000 square-feet), above-grade concrete homes, and commercial/multi-family structures. “Once again, this past year’s submittals represent both a broad cross-section of the continental U.S and the types of projects being designed and constructed by CFA members,” stated Baty.
OVERALL GRAND PROJECT— COMMERCIAL/MULTI-FAMILY
The project recognized by popular vote as this year’s overall grand project is the Science & Engineering Hall at George Washington University. Submitted by Ballinger AE, a professional member of the CFA, this project also demonstrates the growing network of design professionals within the membership of the association.
The George Washington University- Science and Engineering Hall is a new 700,000- square-foot building located in Washington. Of the total 700,000 square-feet, 300,000-square- feet encompass the 6-story subgrade structure.
There were many unique design and construction challenges that came with such a substantial and complex subgrade structure. The substructure extends to a maximum depth of occupied space of 74-feet below grade. The perimeter basement walls were designed to withstand the intense soil pressures caused at these depths. It is also located in close proximity to three existing dormitories, which remained occupied during construction. These dormitories required deep underpinning so as not to disturb the original foundations, and also imparted a surcharge onto the new substructure walls.
Rock elevation on the site varied from 74-feet below grade to 34-feet below grade, therefore significant rock excavation was required. This was accomplished with localized blasting, which again was done while the neighboring dormitories remained occupied.
Ed Zinski, associate principal and chief structural engineer for Ballinger AE was asked about the firm’s role in the project. “Ballinger has extensive experience with unique foundation and concrete design, as well as designing university lab spaces,” stated Zinski. “Working with our in-house design team and assisted by A&F Engineers local to Washington DC provided us with the ability to closely collaborate with the architectural and mechanical design of the building, in order to provide the most efficiently designed structure.”
Extensive computer modeling was used in all aspects of design including the deep basement walls with high soil and surcharge loads, the substructure slabs with open and sloping diaphragms translating extraordinary lateral soil loads, NIH caliber vibration resistant lab floors and high-bay post- tensioning design.
The high-bay testing lab featured a “strong-wall” and “strong-floor” designed and located 12-feet below grade level. Despite being located below grade, this lab was actually an elevated floor five stories above the building’s foundation. The elevated condition resulted in a unique design, as these types of intensely loaded labs are typically founded on grade. The design loads for the lab included more than one million pounds ultimate load applied laterally at the wall and vertically at the floor. The lab also houses a 20- ton crane and a drive-through truck receiving area to deliver specimens to the testing site. Again, extensive computer modeling was used to design this area. Ultimately it was determined that the strong-wall and strong-floor would be reinforced using solid post- tensioningrods.Thisisanotherarea that required close collaboration with Clark Construction, as well as with the civil engineering faculty of George Washington University during design and construction.
Also located within the building are several sloping columns, column transfers and a central core transfer with eccentric column loads of up to 5-million pounds. The slabs were designed to transfer the lateral load induced by the sloped columns. For three of the major column transfers over the main floor auditorium, it was determined that the best solution would be to utilize an exposed composite concrete and steel truss solution. Ballinger’s structural group worked closely with Clark Construction during the building of this unique truss to ensure all of the design requirements were met.
“We are thrilled that the CFA has honored our project, the George Washington University – Science and Engineering Hall, with this award,” stated Zinski. “I have long thought that something so critical as a structure’s foundation is often overlooked or taken for granted. That is why we joined the CFA and look forward to greater participation within the organization. This is also why we are so honored to be recognized by the CFA with this award.”
For more information on this foundation project, contact CFA Member Edward J. Zinski, PE of Ballinger at ezinski@ballinger-ae.com or (215) 446-0684.
ABOVE-GRADE CONCRETE HOME
Since the start of the new millennia, the recognition of performance and aesthetic advantage for all concrete homes has been a focus for the CFA and many throughout the concrete industry. Over the years, many fine works of construction and design have been recognized in this award category. Certainly not less impressive is this year’s “Above-Grade Concrete Home Project of the Year,” Clifton Concrete Home by Bartley Corporation.
“We were selected for this project when several recommendations for this type of complex structure pointed our way,” stated Jim Bartley, president of Bartley Corporation. “The construction manager hired for the project desired to partner with us based on our previous experience in building a concrete home.”
Bartley was asked about what makes this type of a project such a challenge. “Working with owners, construction managers and architects as well as other trades that are new to concrete homes can be a major time commitment,” stated Bartley. “Meeting on site and collaborating with the entire team was the key to success. Having an architect that saw the project all the way through construction made everything go as planned.”
Prior to the kickoff meeting the homeowners wanted to see a sample of the normal cast-in-place wall finish, one delivered on any foundation project. Bartley built and poured the mockup and made sure it wasn’t “perfect.” To their surprise the owners loved the bug holes, imperfections, ties and form- lines. They are in the building industry and like the industrial construction look with natural imperfections. Therefore, extreme measures were taken to avoid using any patching materials on the walls. With the exception of one or two spots honeycombs were avoided. Surprisingly, a crew patched one of these honeycomb regions and when the homeowners saw the patching they asked that it be removed. This kept the project on track and consistent with the approved aesthetic negotiated early in the project.
Another unique characteristic of this design was the presence of two different insulation systems, Thermomass and ThermaEZE, both products that the company had prior experience but separately on projects. The standard wall section consisted of two reinforcement bar mats, Thermomass in the center with all the connectors, conduits, block outs and wall ties. However, where the weight of steel could not bear on insulation, the ThermaEZE system was brought in to provide an alternative support system. All walls were to be left exposed concrete as the final interior and exterior finish.
The most complex part of the project was the first and second floor walls. Gang forms were used to provide the large structural walls and Bartley engaged their commercial crew and a full time commercial superintendent to take the lead in these areas. Difficult block outs and forming along with many recesses for utilities, electronics and built-in features had to be as accurate as possible. Further complicating these walls was the flashing detail. The design called for flashing between the second floor and roof deck to cover the inside of the wall through to the Thermomass insulation sandwiched in the center of the wall. Although Bartley preferred to approach the design with a monolithic roof and second floor based on their experience, the design called for flashing to separate this interface into separate placements with flashing installation between.
Some of the other challenges faced on the project included unique window jambs and an elevator shaft. Many of the windows called for the sides of the window block out to be at 105-degrees rather than perpendicular to the face of the wall. The 3-story elevator shaft challenged the safety on the jobsite with openings that were constantly managed. The shaft was produced by first forming the outside of the elevator shaft and then, when the walls were ready to be closed, a crane carefully placed large interior panels on the inside of the wall.
For more information on this foundation project, contact CFA Member Jim Bartley, Bartley Corporation, at jim@bartleycorp.com or (301) 384-2700.
FOUNDATION FOR PRIVATE RESIDENCE: LESS THAN 2,000 SQ.FT.
This year’s award for a private residence foundation under 2,000-square-feet goes to Purinton Builders of East Granby, Conn. for the project known as Point of the Woods in Old Lyme, Conn. This extreme challenge included concrete piers excavated into and setting on rock at the waters edge. Craftsmanship was the primary goal and reason for the selection of this contractor for the project. Anything but a straightforward foundation, this project demonstrated how demanding and intense a small project could become, especially for the portions of the project that will go largely unnoticed as the completed work takes shape.
“The architect’s vision,” stated Dennis Purinton, president of Purinton Builders, “was to make the house appear to be growing out of the rock. When we visited the site and reviewed what they were trying to accomplish, we proposed options on different foundation designs.”
Ultimately, a tapered pier was chosen. On paper it looks like this very simple little job of a few piers and some slab work would be a quick turnaround. However, Purinton discovered that a low bridge protected access to the site. This required air to be let out of the tires of all ready mix trucks arriving and leaving. Additionally, the use of boom trucks, cranes or any large delivery trucks was prevented due to a combination of the bridge and the site location at the end of a half-mile long winding street with no turnaround.
From the start of this project, once the final design was set, challenge after challenge was uncovered and met. Tolerances for building location and elevations were set at a critical ± 1⁄4-inch. in order to comply with FEMA and local government regulations. Layout reference points were only given as centerlines, so the pier bases had to be set from those centers and then figured with the 5-degree tapers across the variable rocky surface to determine each individual pier configuration. Even the variable rocky surface presented the challenge of maintaining code required footings slopes of no more than 1:10, so cutting of individual pier bases for support was required.
If this wasn’t enough challenge for such a small site, the location proximity at water’s edge along with the steepness of the site necessitated safety awareness. Purinton Builders used caution throughout the project and during the layout and forming stages, safety harnesses made maneuvering at these early stages more difficult while holding such tight tolerances.
“Every tapered pier was different in either size or height and the largest challenge was anchoring them down to ensure that they did not rise up during concrete placement,” stated Purinton. “When it came time to form the slab, the form system was all designed and built on site, since it not only had to support the concrete work but generate a work platform on which to construct the house.”
For more information on this foundation project, contact CFA Member Dennis Purinton, Purinton Builders, at purintonbuilders@yahoo.com or (860) 653-6664.
FOUNDATION FOR PRIVATE RESIDENCE: 2,000 TO 5,000 SQ.FT.
Following the recognition received for their “Overall Grand Project” award in 2014, Hottmann Construction Company receives the award for a private residence foundation between 2,000 and 5,000-square-feet with the Pappas Residence in Fox Lake, Wis.
“We submitted the Pappas Residence this year largely on the complexity of the sloping lot for this intermediate sized structure,” stated Mike Thole, project superintendent for Hottmann. “With a height difference from front to back of 14-feet, the footings on this job jumped or stepped four different times.”
The location for this home was on a mature lake but located within a stretch of relatively new and updated “lake houses”. Every other lot was filled with house while this lot remained filled with trees. After clearing and excavating, there was no room for convenient concrete delivery so placement challenges were met with conveyor and extra labor. Despite these challenges, including the multiple steps, the foundation was square and true and delivered according to schedule.
Prior to the start of the house framing, a precast concrete patio was installed immediately after backfilling the foundation. This further complicated the sequencing on the project and required care in the backfilling procedure to protect the unsupported foundation walls while erecting the patio.
The house design took advantage of several other techniques Hottmann has delivered for clients in the past. A wine cellar was created under the front stoop. While this is not necessarily a unique feature, their experience in curved walls delivered walls with an 8-foot-4 radius on the backside of this room with recesses for cabinets to be installed on the interior of the wall. This is complimented by a curved wall on the back patio. Finally, roof drains were internal to the structure and exit the foundation walls through block outs placed by Hottmann.
For more information on this foundation project, contact CFA Member Mike Thole, Hottmann Construction, at mthole@hottmannconstruction.com or (608) 849-1155.
FOUNDATION FOR PRIVATE RESIDENCE: GREATER THAN 5,000 SQ.FT.
The final project to receive recognition this year represents the large- scale single-family residences over 5,000-square-feet category. Herbert Construction of Marietta, Ga. maintains their presence in the annual awards program with a private residence entry from Acworth, Ga.
“We estimated this project three separate times,” stated Doug Herbert, president of Herbert Construction. “The first estimate was submitted before the site was cut. Then, once the site was cleared and we could talk with the general contractor about the schedule we re-estimated. Next, we were asked to do one final estimate once the site was dug to the proper grade so that all variances in wall heights could be established.”
In all, 14 different wall heights were required varying from 3-feet to 18- feet and a cumulative total of 27- feet of vertical jumps (footing steps) were required. The walls themselves were configured with four different thicknesses ranging from 8-14-inches.
There were many additional outstanding features selected by popular vote for this project as award-worthy. The project included two sub wall areas that required six different details to accommodate the change in elevation. A curved retaining wall 70-feet long by 16-feet tall and 18-inches thick was designed to have brick ledge on both sides. The client asked for a safe- room under one of the porches with an internal concrete wall and integral door opening.
“The contractor viewed this as a very complicated project,” stated Herbert, “and we had to agree. However, we have grown accustomed to such challenges and using a combination of our CAD system, robotic layout and planning experience, we were able to decipher the challenges, plan an effective schedule and approach and deliver a very high quality foundation for this repeat customer.”
For more information on this foundation project, contact CFA Member Amanda Morris, Herbert Construction, at amandam@herbertconstruction.com or (770) 765-0103.
MORE INFORMATION
Each year, the CFA “Projects of the Year” offers a challenging competition to the industry. This publicizes the craftsmanship and creativity of the cast-in-place concrete industry that largely goes unnoticed or unseen. It is free to CFA members and brings to light the quality and accomplishments that happen daily in the concrete industry, many which become quickly covered never to be recognizable or appreciated within the final product.
For more information on these projects, visit the “CFA Projects of the Year” at http://www.cfawalls.org/awards/project/index.html where you will find more images and facts for this year’s winners, the historical archives for the competition and information on the competition itself including voting basis and entry guidelines. If you would like more information, please contact Jim Baty at the CFA. Phone 866-232-9255 or jbaty@cfawalls.org.
A Year In The Life Of A Concrete Contractor
What is perhaps the most unique part of your company, your business, your professional life? While this question begs you to think of the accomplishments you have made or the challenges you have faced, what I believe it to really be is the isolation you have as a company.
The practice of concrete construction at the scale of residential, agricultural and light commercial is one of extreme focus. Your eyes must be on the local economy and market and due to the pressures these two alone create, you have every reason to exhibit the trait of working on an island at times, that is, an island inhabited by intense competition.
What is missing more than anything in your business is connectivity. A chance to participate with peers, other contractors that are nearly identical to your business and behavior, is one of the most vital resources most companies miss out on. It is also the very reason why CFA Convention was created decades ago and remains today, focused on growing as the largest gathering of the poured wall concrete contractor. There must be an opportunity for you to access the minds of your peers without the pressures of business and the challenges to your focus. There must be an annual meeting that collects the thoughts of your industry, from the collective minds of the professionals working hard at the daily implementation so as to generate a blueprint for improving conditions, information, strategies and codes.
Contained in this magazine is the most important invitation you perhaps have been given. Many of you reading this letter realize it; some of you never miss and some of you have been waiting for the right condition to return. The majority of you, however, especially the thousands of concrete contractors that have not taken the step to membership, have not taken the opportunity to experience the power that comes from three days of immersion that can completely change the year that lies ahead. In essence, each CFA Convention features contractors sharing details of their past year while building relationships with impactful peers. A foundation develops from the shared details that will foster challenging growth opportunities for the year that lies ahead.
Let me introduce you to your professional peers. This one decision will very likely be the best one you’ll make this year and will be perhaps the best one you’ve made in the last decade when it comes to your business.
You Have A Very Important Decision To Make!
I’m composing this letter in my head during a recent relaxation trip to South Dakota. While in the midst of the great setting and the many casts mixed with the every attempt to stay out of business, I did find my mind fixated on CFA Convention 2015. You’ll read a lot about this event in the pages of this magazine but I want you to have my two cents on the event.
I’m very busy during the summer. It is the busy construction time, my kids are in a hundred activities and the weather in Iowa is nearly perfect. Why would I put my company at risk while being away for three or four days while I travel to an event featuring education and technology for a business that I’ve been in for decades? I was once where you stand but I did make the decision, one that has defined much of the success for my company. I’ll offer my thoughts to you in four main points.
1) Education initially attracted me to Convention. Each year I’ve returned, the CFA has continued to elevate the education and make it poignant to my business. This is largely because contractors like me weigh in on what the pressure points and hot topics are.
2) Friendships keep me coming back year after year. I do learn a lot from the education and the technology at Convention but I learn even more from the peers I’ve met, many of whom have become close friends. In this business, it is easy to put your nose down and never look up at those that have walked before you or that struggle on the same issues. Convention is a place where you make lasting friends for the remainder of your career. They will make you better.
3) Time Away is something I never realized as being important to my company. I am not gone long and rarely to far. At the same time, I am challenged and focused on ways to improve our business and that matters. What I also uncovered is that my employees and other leaders in our company grew during the time I needed to be away. I issued the challenge for them to be more responsible, do more and get better…they did and now we all look forward to this annual event.
4) Family Value is a price you can’t put on the experience. There are few times in your year when you have the real chance of focusing on your family while you expand your business, your mind or your potential. I’ve heard my kids plan their summer around Convention while not even to Christmas yet.
It’s not about where will you go next year? There is never a “good” time for you to leave your business but there is never a “better” time than making it happen right now. I’ll wager with you that your gain will far outweigh any realized pain.
David Martinson, Martinson Construction
Standing Water in Prepared Footings: A Problem or a Precaution?
by JAMES R. BATY II
Created: May 18, 2015 for Concrete Contractor Magazine
In this column, the Concrete Foundations Association explains frequent concerns lifted by homeowners as they are engaging a contractor or during the construction process. These issues are offered to you, the concrete contractor as a way of better understanding your customer and identifying the gap that exists between your message and their understanding.
This column deals with the concern for structural integrity of concrete footings due to water in the excavation.
Home owner Question: I visited the site of my new home and noticed a lot of water standing where the concrete walls will soon be poured. Won’t this be a problem for the quality of concrete in my footings? – Home Owner (Missouri).
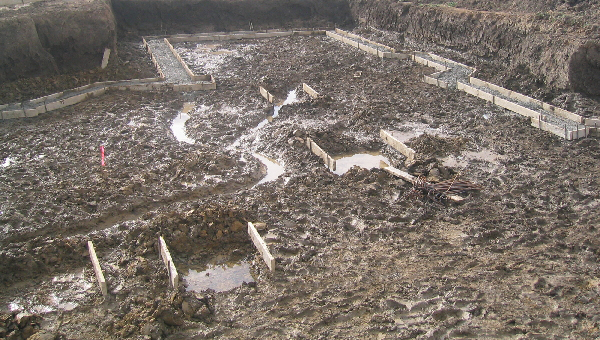
Spring rains left this foundation with standing water in the excavation. Concrete placements should take place promptly before saturation of the grade occurs.
This is a very common question, particularly during the predominantly rainy spring construction season. Concrete, as we know, is a basic mixture of water, cement, sand and large aggregate. There are also chemicals in virtually all of modern mixes for a variety of performance enhancements. One of the most critical parts of the mix design is the specified water-cementitious material ratio (w/cm). This specification will ultimately determine the effective strength properties of the mix as well as controlling the volumetric change during the hardening changes. This column has previously addressed the nature of increased water in mix designs.
At the very heart of this question is the basic idea that if a concrete mix is placed into water it will be harder for it to dry and therefore harden to be strong enough to support the structure. After all, most homeowners see concrete as a fluid that must first dry to get hard and if even more water is present, it must be like the glue their children use in school and weaken as the water mixes in. Although the homeowner may be justified with some concern for the presence of standing water, the strength of the concrete in the foundation is more than likely not part of it.
One of the duties of the contractor is to provide assurance for the performance of your construction. When it comes to a concrete mix, that assurance includes some basic facts:
- The strength of a concrete mix comes from the ratio of water to cement (or cementitious material) and is referred to as the w/cm.
- Once created at the ready mix plant, the introduction of water “into” the mix will weaken the concrete and may upset the w/cm ratio more than the design calls for.
- Concrete weighs more than water and it will displace the water when introduced into any container or form rather than mixing with that water.
- Concrete hardens due to a chemical reaction and does not “dry” to harden. Water is required for the chemical reaction to occur with the cementitious material. Concrete piers for a bridge over a body of water is an excellent example of concrete hardening in water.
ACI 332-141 states in the commentary section R6.2.4:
…If the footing form permits water to exit, the hydraulic pressure of the concrete placement is sufficient to displace the water from the formed areas and prevent segregation.
This commentary builds on the minimum code requirement for not placing concrete in confined areas with water. This section provides recognition that concrete has a mass greater than that of water and during a placement operation, the concrete will displace or move the water due to a combination of this mass and the force of discharge creating a greater hydraulic pressure than the water can withstand. Moving ahead of the concrete placement, the water will exit the formed footing space at the first opportunity. If the footings are excavated into the undisturbed soil and there is no point at which the slope produces a natural exit, the concrete placement force and weight is still likely to force the water to exit over the top of the footing space. As long as the placement proceeds to fully displace the water, there should be no cause for concern. Only when the concrete does not fully displace the water will the partial volume of concrete and water result in segregation of the concrete mix where the large aggregate is separated from the cement paste.
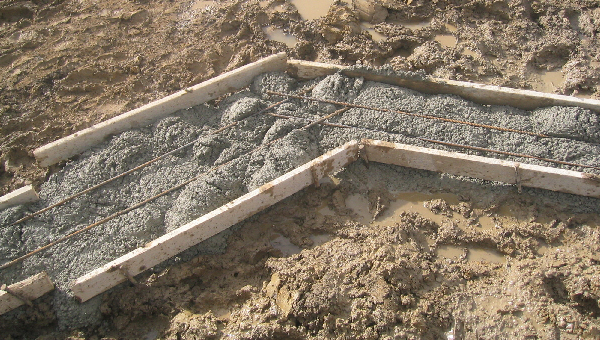
Contractors can plan exit strategies for water in the forming system for the hydraulic pressure of the concrete to push the water from the formed condition.
Some precautions to follow include:
- Prevent the water from segregating the mix or being incorporated in the mix by pushing the water with the flow of the concrete. A recommended practice for all concrete placement, this keeps the hydraulic pressure of the concrete flow influencing the water.
- Provide a way for water to escape during the placement at key junctures in the forms if possible.
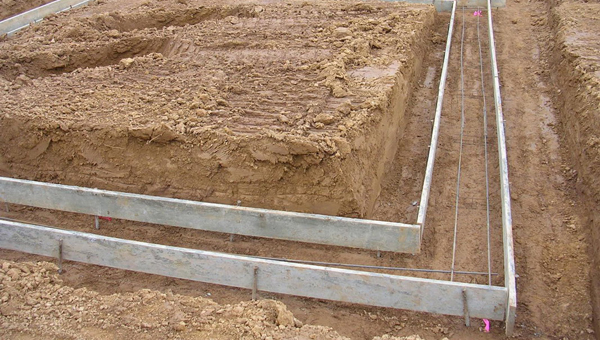
The overdig of this excavation combined with suspended footing forms provides protection from standing water in a confined space for this project.
The homeowner is likely also concerned with seeing mud, knowing that mud is softer than dry soil and thinking it is not ready to carry the load of the concrete foundation and therefore the house. There are some facts that can assure the homeowner for this concern as well:
- Footings and foundations are prepared on an excavation of “undisturbed” soil. This means the surface of the soil is cohesive or of a consistent strength.
- Standing water does not absorb quickly or easily into the surface of a cohesive soil.
- Water can be removed from an excavation without requiring compaction of the soil.
Water present on the top of soil does not immediately present a problem as saturation takes time. Depending on the type of soil and likely for most soils encountered for a foundation, that time can be considerable. However, the contractor must determine if the water presence has been sufficient to alter the surface of the prepared excavation. The IRC2 provides reference to this condition as follows in section R401.4.2:
Compressible or shifting soil. Instead of a complete geotechnical evaluation, when top or subsoils are compressible or shifting, they shall be removed to a depth and width sufficient to assure stable moisture content in each active zone and shall not be used as fill or stabilized within each active zone by chemical, dewatering or presaturation.
In other words, when the surface condition of the excavation is changing or no longer holds the condition of the designed soil capacity, remediation needs to occur. This is often a last resort that can be prevented with some common precautions including:
- Limit the time water stands in the excavation by moving forward with concrete placement or removing the water.
- Control the amount of traffic in the excavation. Foot traffic in areas of standing water will accelerate working the moisture into the soil, impacting the surface condition and the compaction of that top layer.
- Prior to concrete placement, all loose silty soils should be removed with a shovel along the bottom of the formwork, exposing the cohesive base.
Saturated soils do have a lower bearing capacity than the predicted or assumed condition. This is mainly due to expansion of the soils as the volume is increased with water. If concrete placement can be achieved soon enough, it is unlikely the water will have moved into the soil sufficient to disturb the compaction and bearing capacity will be maintained.
When soils are determined to be saturated or when the placement could not be made quickly enough, the excavation should be cleared of the loosened soils, mud and water sufficient to re-establish the soil-bearing capacity assumed for the design.
Contractors should not be surprised to hear this concern from the homeowner. Knowing the facts, providing the reassurance and identifying the resources that can support your position are keys to a productive conversation on this issue. In fact, the contractor may very well have anticipated the inclement weather, and as stated previously, designed the forms for the movement of water. The contractor may also have experience in the remediation of the saturated soil condition, either removing the affected regions or drying out the excavation and ensuring compaction. Knowing the provisions of ACI 332-14, and the IRC, will help deliver a positive outcome to a natural part of the construction process.
Want to know more? Contact CFA Executive Director, Jim Baty at 866-232-9255 or by email at jbaty@cfawalls.org. The CFA is a national association with the mission to support the cast-in-place contractor as the voice and recognized authority for the residential concrete industry. ACI 332-14 can be obtained by contacting the CFA or by visiting the American Concrete Institute (www.concrete.org) and ordering from their bookstore.
References:
1 Residential Code Requirements for Structural Concrete (ACI 332-14) and Commentary published by the American Concrete Institute, 38800 Country Club Drive, Farmington Hills, MI 48331 | Phone: 248-848-3700 | www.concrete.org
2 2012 International Residential Code® For One- and Two-Family Dwellings published by the International Code Council, Inc., 4051 West Flossmoor Road, Country Club Hills, IL 60478-5795 | Phone 1-888-422-7233 | www.iccsafe.org
“RECRUITING KEEPERS” AND “KEEPING RECRUITS” TO BE PRESENTED AT CFA CONVENTION 2015
|
REPLACE BASEMENT DOOR TO INCREASE SAFETY, VALUE OF HOME
NEW HAVEN, CT/May 27, 2015 – Replacing a weathered or damaged basement door can have a great impact on the safety, appearance and value of a home. It’s in the spring and summer months, after basement doors have suffered through a long winter and have fallen victim to rotted wood, rusted metal or leakage, that homeowners may look to replace an old door with a high-quality and efficient one. Homeowners often select one of The Bilco Company’s several attractive options because they meet safety requirements, reduce or eliminate the need for regular maintenance and have superior design features.
Traditionally basement entrances are used to move large items like deck and patio furniture in to and out of storage areas or to relocate beds, large electronics and game tables to finished basement areas. To complete these often two-person tasks, a homeowner will benefit from an access solution that will securely remain in a wide, open position. Bilco doors come equipped with lift assistance for smooth, easy, one-hand operation and to prevent the door from slamming closed, allowing homeowners or workers to move quickly and safely through the entrance. In addition, Bilco’s basement doors satisfy the International Residential Code (IRC) 2012 building requirements, which require every basement used as living space to have an egress to the outside and every basement bedroom to have an additional egress window or door. These safety requirements are intended to allow occupants an alternate route to escape (and/or firefighters to enter) through the basement during a fire or other emergency.
Style preferences vary greatly from one homeowner to the next, so Bilco offers several customizable basement door options to fit functional requirements as well as individual taste. The Classic Series Steel Basement Doors are equipped with flanged construction and an improved header design to shed water and prevent binding due to ice and snow, permitting all-season use and lasting service. The Classic Series Sloped Wall Door features a versatile frame design and optional foundation plates to accommodate installation on virtually any areaway, including sidewalls of brick, stone, block or poured concrete.
Both steel models are available with an optional, factory-applied powder coat paint finish, which results in a tougher, more durable and weather- and chip-resistant coating. Homeowners will benefit from a lasting decorative and protective finish, which is offered in four standard colors (white, sandstone, light gray and brick) to complement the exterior of any home.
A third option, the Ultra Series basement door, is a maintenance-free basement access solution constructed from high-density polyethylene that provides safe and code-compliant basement access. Interchangeable side panel inserts allow homeowners to easily customize the door to add light or ventilation to a basement areaway.
All Bilco basement doors feature weather-tight performance, corrosion-resistant hardware and lift assistance for easy one-hand opening and closing. A standard slide-bolt lock is supplied for security and a keyed lock kit is available for added convenience and protection. Bilco basement doors can accommodate virtually any areaway due to a range of available sizes and extension panels.
Regardless of taste or preference, The Bilco Company can accommodate the needs of practically any customer with a variety of basement door models. The company’s low-or maintenance-free designs provide a stylish and attractive access way to any basement area that is safe, functional and code- compliant. To find a basement door dealer or a Bilco Independent Installer in your area, visit www.bilco.com or call (800) 854-9724.
About Bilco
For over 85 years, The Bilco Company has been a building industry pioneer in the design and development of specialty access products. Over these years, the company has built a reputation among homeowners, builders, architects, and engineers for products that are unequaled in design and workmanship. Bilco – an ISO 9001 certified company – offers a line of commercial and residential access products along with a complete line of Colt natural ventilation and smoke and fire containment products. For more information, visit www.bilco.com.
Keep up with the latest news from The Bilco Company by following it on Facebook and LinkedIn.
DON’T MISS THE CFA CONVENTION 2015 KICK-OFF BASH!
|
Join us for Construction Day at CFA Convention 2015
|