2017 Projects of the Year | Single-Family Residence Under 2000 SF
Blue Willow Ridge Nest #3
Single-Family Residence Under 2,000 sq.ft.
SCW Footings & Foundations
Salt Lake City, Utah
The intrigue of the residential foundation that is under 2,000 sq.ft. is often overlooked in today’s construction economy, where bigger is spectacular and ostentatious is attractive. Some of the most challenging projects, however, come in small packages. That is the case for this year’s winner set in the “mountainscape” near Eden, Utah.
The main challenge for this project was the steep hillside of the lot. In a small footprint of only 1,076 sq.ft., the walls stepped thirteen times to cover a vertical descent of 15 feet. Steps are labor intensive, and when the project is small, they become dominant in the project costs. In addition to the significant number of wall steps, the small footprint incorporated 26 corners and three separate rebar schedules.
“This project was a long distance from our base of operations,” states John Graber of SCW Footings & Foundations. “Given its size, we could not afford to mobilize each crew for just this project, so we found a creative way to integrate it with trips to larger projects in and around the same area.”
Project Statistics:
194 lin. ft. of wall, 1,076 sq.ft. footprint
74 yd3 of concrete, 5,005 lin. ft. of steel
13 wall heights from 2 to 11 ft., all 8 in. thick
2017 Projects of the Year Overall Grand Project: Going Out On A Limb Is Easier Than Building On A Cliff…
The 2017 Projects of the Year Awards… continued excellence in the field of cast-in-place concrete.
OVERALL GRAND PROJECT OF THE YEAR
Single Family Residence Over 5,000 sq.ft.
Aerie Residence by Ekedal Concrete, Inc.,
Newport Beach, California
Corona Del Mar, California
15,000 sq.ft. Single Family Residence
Canadian novelist David Bergen once quipped, “I think a construction project for me is like writing a novel. I can’t do the project unless I can envision sort of the whole structure and see what the end result might be.” Lost in the completion of any project is the appreciation for the vision the contractor must have—the vision Bergen spoke of—to complete the seemingly impossible and the certainly incomprehensible.
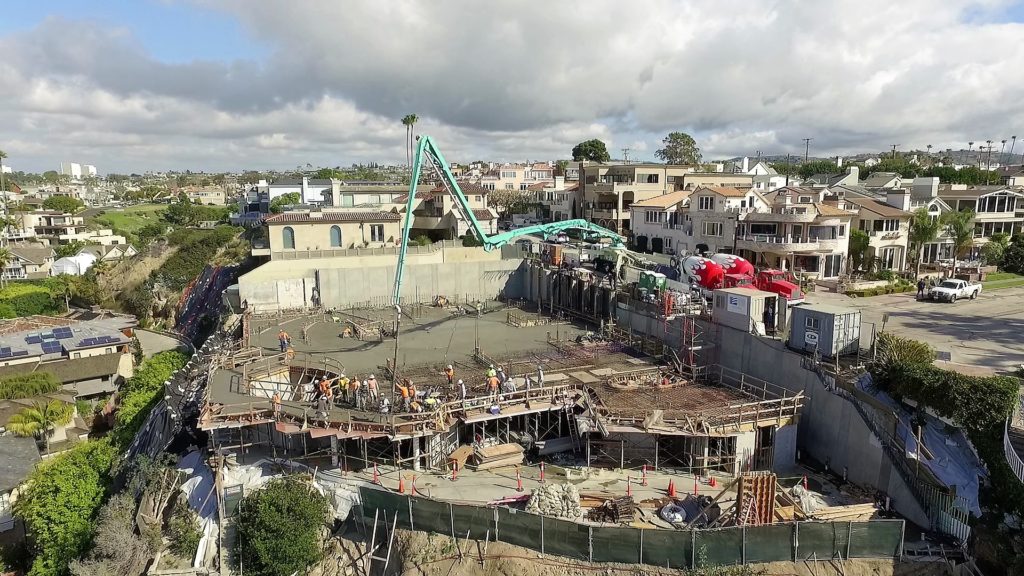
Drone photo of the Aerie elevated deck pour underway in Corona Del Mar, photo courtesy of Ekedal Concrete, Inc
Among the projects submitted for the 2017 CFA Projects of the Year was a project weighing in at 15,000 sq.ft. (1,393.5 sq.m.). The project, a private residence in Corona Del Mar, California was constructed on a cliff overlooking the coastal bay. Submitted by Ekedal Concrete, Inc. of Newport Beach, CA, this entry added to their already impressive collection of strikingly large concrete works with massive challenges. As a company, Ekedal has made a commitment to the mega-foundation residential market in taking on any and all challenges. Their results evidence the success of combining vision for the project sequence with the skill they have developed as a concrete contractor to deliver a foundation second to none and another award-winning project.
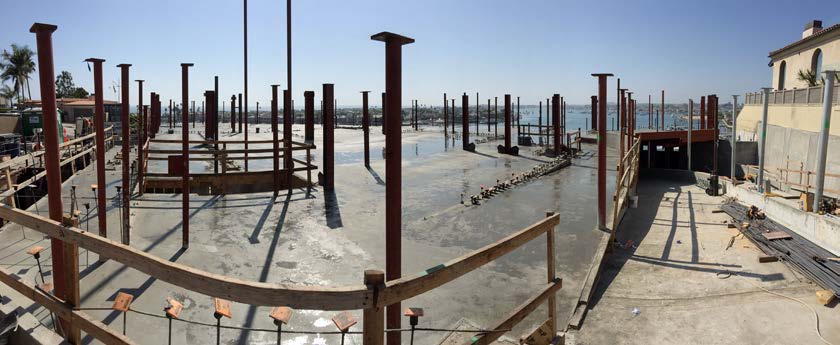
Garage access ramp and main level structural supports for Aerie project.
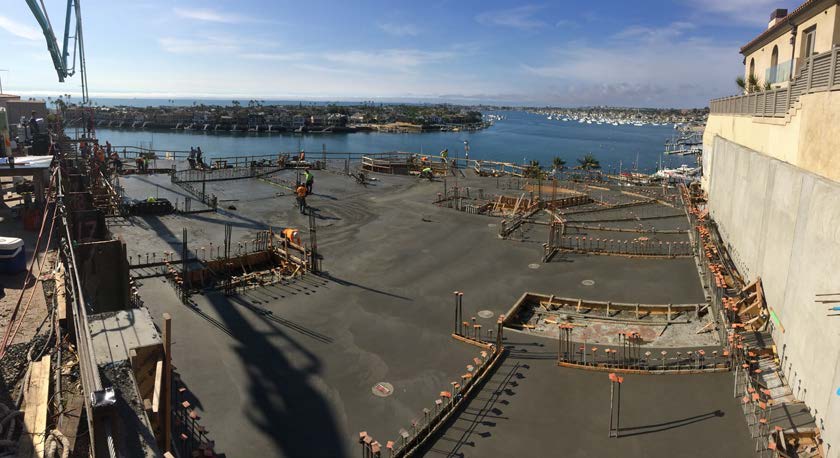
Finishing operations nearly complete on the elevated deck for the Aerie project. Photos courtesy of Ekedal Concrete, Inc.
One of the first questions often asked of a contractor working a project like this pertains to their selection. Ekedal Concrete had been involved with this project over a 10-year development timeline. Vice President for Ekedal Concrete, Ryan Ekedal, quickly describes the merits of this project and the selection for the concrete work as having stemmed from the investment they made: “This was a very complicated project in a very affluent part of the city next to multi-million dollar homes on both sides. All of the local governing agencies were involved, along with the coastal commission, so it was a very lengthy process to get the approvals. The entire design team came to Ekedal due to our reputation and the body of work we have to show over the span of 40 years. Ultimately, our selection is based on the immense amount of time on the front end of our projects, and a project like this very much needed that. Additionally, we bring experience in expediting approval processes and delivering an in-house shop drawing department with complex software solutions to make the pre-construction phase very smooth.” This company put a lot at stake early in the project, developing a relationship with the design team, the owner and the builder so that every aspect of the work could be controlled and delivered with confidence and precision.
As seen in the images, the project sits into the side of a large cliff overlooking the ocean. This meant considerable shoring was needed to hold the cliff. The construction sequence of drilling, pouring, shoring, re-shoring and continuing this process maintained the surrounding areas. Shoring walls were 20 ft. (6 m) tall and tapered from 8 in. (20 cm) to 20 in. (50 cm) consisting of shotcrete in separate sections due to the shoring piles needing to stay in place until the sections came to their desired strength. Read More
Defining Leadership
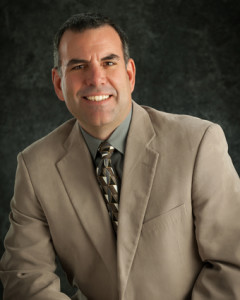
James Baty, CFA Executive Director, jbaty@cfaconcretepros.org
Here is the problem with being seen as a leader: leaders continue to give a lot of time, energy and often money as a way of contributing to the larger goal or to honor the position they have attained. This is increasingly hard on the organization and the individual as it regularly conflicts with the mission and vision of the company, whose work positioned the person to be seen or considered a leader. And yet, leadership is one of the most exciting, driving and beneficial opportunities that anyone can achieve.
The Merriam-Webster dictionary defines leadership in three ways. I often find it important to visit the dictionary when considering such terms, as life tends to place blinders on us, preventing us from taking in the fullness of our own definitions. In this resource, a leader is defined as “something that leads; a person who leads;” or, “a horse placed in advance of the other horses of a team” (www.meriam-webster.com). I would like to work backwards through these global definitions.
A horse placed in advance of a team. While there are always rogue or shooting stars, most hard-working persons recognize that “many hands make light work,” as my mother would say. While one is placed at the front, it is the concerted direction of all that makes for completion of the task at hand. A leader sets the pace and defines the direction in a way that makes it possible for the entire team to contribute.
A person who leads. We are confident because we are made to appear confident. We are naturally inclined to follow and to be organized into a cohesive effort. You want to get a task done, select the right individual to lead and allow them to organize those around them—inspiration combined with perspiration. I see that played out today with your association president and within our member companies, be it the CEO to the company, the division manager to the divisions or the crew leader to the forming crew.
Something that leads implies an object or a device (the dictionary offers a short length of stronger material between fishing line and the hook). In some ways, a tool, a device that serves the purpose of making sure energy and direction accomplish the task. Without the leader, the hook is severed and cannot deliver. Without the leader, the target cannot be attained accurately and efficiently. Without the leader, the door is left open with nothing coming in.
What are you struggling with in your company? If you are not taking the time to define it and label it, chances are you are not challenging your company enough. Without challenge, there is no inspiration, and perspiration is just energy wasted. Come to Concrete Foundations Convention 2017 in Nashville and become labeled as a leader in more ways than one.
Is Bigger Really Better?
Many years ago at a summer meeting the topic of one of the speakers was “How To Grow Your Business?” His opening statement was, “Why do you want to grow? Do you think that growth is going to substantially increase your bottom line?”
“If you are willing to do more than you are paid to do, eventually you will be paid to do more than you do.” (anonymous)
At the time, we chose the growth option and it took many years for us to realize growth did not increase our profit margins enough to justify the additional costs we incurred.
Three downturns in the economy taught us that diversity and being efficient at what we did was much more profitable than volume of business. That change in philosophy was truly the reason we survived the last downturn.
We have visited a number of CFA members over the years who have taught us many ways to operate more efficiently and what equipment it was wise to purchase to bring about some of that efficiency. On one of those visits a fellow CFA member commented, “Forms and equipment are cheap; it’s the labor that is expensive.” With the increasing shortage of qualified labor, we have found it even more important to research high-quality, versatile machinery. Equipment may be cheap, but cheap equipment may not always be the best answer. I consulted with a contractor recently on the purchase of a new piece of equipment. The conversation lead to the final decision of what to purchase, in this case, high quality with many options, not price. His last statement to me was that this purchase opened up a less competitive market and that in six months we would be purchasing a second one. A piece of equipment purchased for use in the less competitive markets pays for itself very quickly.
We have enough equipment available to allow us to be diverse, efficient, responsive on short notice, as well as be profitable, without a high volume of labor. We have worked hard at learning how to plan utilizing the resources available to us in a cost effective, efficient way. Part of that planning includes having a second option when things do not go as planned due to factors beyond our control.
We will have many equipment representatives available at this year’s CFA summer meeting in Nashville in July. I hope you will research equipment options that may be able to help you operate more efficiently. In addition, feel free to reach out and share experiences and expertise with fellow members—you never know what you may learn.
Remember: bigger may not always be better.
Summer Meeting (+) Networking = Additional Profit
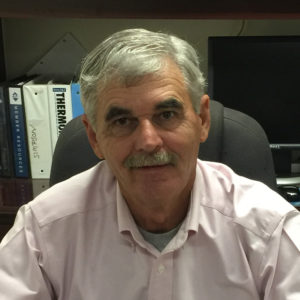
Dennis Purinton, Purinton Builders Inc., CFA President 2016-18, purintonbuilders@yahoo.com
Residential Building Down in May
Dodge Data & Analytics Report for June 2017
New Construction Starts in May Edge Up One Percent
Public Works Construction Strengthens, But Nonresidential Building and Housing Recede
NEW YORK – June 21, 2017 – At a seasonally adjusted annual rate of $651.2 billion, new construction starts in May increased a slight 1% from April, according to Dodge Data & Analytics. Public works construction bounced back 30% from its subdued April amount, helped by the May start of four large pipeline projects totaling a combined $3.0 billion. This enabled the nonbuilding construction sector (which also includes electric utilities and gas plants) to register a 23% gain in May, offsetting modest 4% declines for both nonresidential building and housing. Through the first five months of 2017, total construction starts on an unadjusted basis were $274.3 billion, down 5% from the same period a year ago. If the volatile manufacturing plant and electric utility/gas plant categories are excluded, total construction starts during the first five months of 2017 would be up 2% relative to last year.
The May statistics produced a reading of 138 for the Dodge Index (2000=100), slightly higher than the 137 reported for April. During this year’s first quarter, the Dodge Index averaged 152. “While May revealed slight improvement over April, the pace of expansion so far this spring has generally slowed following the elevated activity in the first quarter,” stated Robert A. Murray, chief economist for Dodge Data & Analytics.
“This is consistent with the up-and-down behavior that’s often been present in the current expansion, and a continuation of this pattern means that renewed strengthening can be expected in the months ahead,” Murray indicated. “On the plus side, long-term interest rates remain quite low, with the 10-year Treasury bill rate easing back to 2.2% even as the Federal Reserve raised the federal funds rate another quarter point last week. Numerous state and local bond measures passed in recent years are providing near term support for public works and institutional building. The expected benefits of a new federal infrastructure program, assuming one gets passed during the second half of 2017, would affect construction activity more in 2018. And, while vacancy rates for commercial building and multifamily housing are beginning to rise, the increases witnessed so far have been generally small.”
Nonbuilding construction in May was $146.9 billion (annual rate), up 23%. The public works categories as a group climbed 30%, rebounding from a 48% decline in April, as the “miscellaneous” public works category (which includes pipelines) soared 166%. The largest pipeline project entered as a construction start in May was the $1.5 billion Revolution Pipeline expansion in western Pennsylvania, which includes a 100-mile natural gas pipeline gathering system that will feed into a new cryogenic gas processing plant. Also entered as a May start were the $690 million Gulf South Coastal Bend Header project in Texas that will deliver natural gas to a liquefaction terminal in Freeport, the $500 million Atlantic Bridge natural gas pipeline expansion in the Northeast (New York, Connecticut, Massachusetts, Maine), and the $300 million Cameron Access natural gas pipeline expansion in Louisiana. Through the first five months of 2017, the dollar amount of new pipeline construction starts totaled $13.8 billion, already topping the full year 2016 amount of $11.6 billion. Highway and bridge construction in May grew 5%, helped by a $192 million highway project in San Antonio TX and a $125 million bridge improvement project in the Macon GA area. The top five states in terms of the dollar amount of new highway and bridge construction starts in May were Pennsylvania, Texas, California, Georgia, and Florida. The environmental public works categories retreated in May, with river/harbor development down 5%, water supply construction down 9%, and sewer construction down 11%. The electric utility/gas plant category dropped 3% in May after its 71% hike in April, with the largest May projects being a $500 million natural gas-fired power plant in Pennsylvania, a $259 million transmission line in California, and a $240 million wind power facility in Texas.
Nonresidential building, at $219.3 billion (annual rate), slipped 4% in May. The commercial categories as a group fell 10%, with office construction dropping 40% following gains of 41% in March and 23% in April. The two largest office projects entered as May starts were the $300 million American Airlines Trinity Campus in Fort Worth TX and the $166 million General Electric Global Headquarters Building in Boston MA. The other commercial categories showed growth in May. Warehouse construction climbed 17%, lifted by the start of a $160 million Amazon fulfillment center in the Houston TX area and an $84 million Fed Ex distribution center in the Worcester MA area. Store construction advanced 16% with the help of a $200 million shopping center shell in Norwalk CT. Hotel construction increased 11%, reflecting the start of a $118 million Hilton hotel in Myrtle Beach SC and a $116 million hotel in Monticello NY. Also contributing was the commercial garage category, which rose 7% in May. Manufacturing plant construction jumped 22% in May, lifted by the start of a $975 million chemical plant expansion in Louisiana, a $385 million polyethylene plant in Texas, and a $120 million research lab upgrade in Colorado.
The institutional side of the nonresidential building market retreated 4% in May. Education facilities, the largest nonresidential building category by dollar volume, dropped 21% after registering a 12% gain in April. Even with the decline, there were several noteworthy educational facility projects that reached groundbreaking in May, including a $100 million science and engineering center at Union College in Schenectady NY, a $93 million engineering building at the University of Rhode Island in Kingston RI, a $76 million dentistry education facility at Texas A&M University in Dallas TX, and a $75 million high school in the Raleigh NC area. Declines were also reported for religious buildings, down 10%; and the amusement category, down 36%; although the latter did include the start of the $127 million Buddy Holly Hall of Performing Arts and Sciences in Lubbock TX. On the positive side, healthcare facilities climbed 38% in May with the help of five projects valued at $100 million or more, led by the $442 million Marcus Tower at Piedmont Hospital in Atlanta GA and a $265 million University of Colorado hospital in the Denver CO area. The public buildings category advanced 51% from a lackluster April, reflecting the start of $125 million detention facility in Phoenix AZ, while the transportation terminal category posted a 23% gain in May.
Residential building was $284.9 billion (annual rate) in May, down 4%. Multifamily housing retreated 10% following increases over the previous two months that saw activity rise 20%. There were seven multifamily projects valued at $100 million or more that reached groundbreaking in May, led by a $450 million multifamily high-rise in lower Manhattan NY, the $200 million multifamily portion of a $240 million multifamily/hotel mixed-use high-rise in Chicago IL, and a $200 million multifamily high-rise in Boston MA. In May, the top five metropolitan areas in terms of the dollar amount of multifamily starts were the following – New York NY, Los Angeles CA, Philadelphia PA, Chicago IL, and Boston MA. Through the first five months of 2017, the top five metropolitan areas were the following – New York NY, Los Angeles CA, Chicago IL, Washington DC, and San Francisco CA. The New York NY share of the national multifamily total so far in 2017 is 18%, up slightly from the 17% share reported for full year 2016, although down from the 25% share reported for full year 2015. Single family housing settled back 2% in May, with its upward track pausing for the third month in a row after showing steady growth during the fourth quarter of 2016 and the first two months of 2017. By major region, single family housing in May revealed this performance – the West, down 7%; the Midwest, down 5%; the South Atlantic, up 1%; the South Central, up 2%; and the Northeast, up 4%. One plus for single family housing going forward is the recent retreat in the cost of financing, with the 30-year fixed mortgage rate slipping to 3.9% in early June, after reaching 4.3% in late 2016.
The 5% decline for total construction starts on an unadjusted basis during the first five months of 2017 was due to a varied pattern by major sector. Nonbuilding construction fell 25% year-to-date, with electric utilities/gas plants down 67% while public works construction was down just 3%. Nonresidential building grew 5% year-to-date, with institutional building up 17%, commercial building down 5%, and manufacturing building down 9%. Residential building year-to-date was flat, with single family housing up 8% while multifamily housing decreased 17%. By geography, total construction starts in the January-May period of 2017 showed this behavior – the Midwest, down 18%; the South Central, down 14%; the Northeast, down 3%; the West, unchanged; and the South Atlantic, up 8%.
Additional perspective comes from looking at twelve-month moving totals, in this case the twelve months ending May 2017 versus the twelve months ending May 2016. On this basis, total construction starts were up 3%. By major sector, nonbuilding construction fell 12%, with electric utilities/gas plants down 41% while public works slipped 2%. Nonresidential building increased 14%, with manufacturing building up 20%, institutional building up 16%, and commercial building up 11%. Residential building grew 3%, with single family housing up 7% while multifamily housing fell 6%.
Hiring – CDL driver Class B/Laborer
We’re Hiring! – CDL driver class B/Laborer
Who: Peachey’s Poured Walls, Inc.
Where: 94 Long Lane – Belleville, Pa. 17004
Contact: peacheyspouredwalls@embarqmail.com
717-483-0109 – Barry
Starting wage: $18-$22 per hour
Join a great company and CFA member concrete contracting company and put your skills to work.
Nebraska’s Leading Concrete Construction Company Obtains New Resource
Lincoln, NE – Stephens & Smith Construction Co., (www.stephensandsmith.com) has announced that Jereme “Bird” Montgomery has
joined the S&S team as their Business Development Coordinator. His primary duties will focus on new and existing clients, sales, marketing, and social media. Mr. Montgomery has a wealth of experience within the concrete construction industry, having spent the past 11 years as the executive director for the Nebraska Concrete & Aggregates Association (NC&AA).
Jereme Montgomery obtained a Bachelor of Science degree in Construction Management from the University of Nebraska. He has nearly 20 years of experience in various aspects of the concrete industry. He started his concrete career working for the Nebraska Department of Roads in the Material and Testing Laboratory. Prior to joining Nebraska Concrete and Aggregates Association, Jereme worked as a concrete operations manager for a design and build firm, managing and constructing quality concrete flatwork. In 2015, Jereme was voted NRMCA State Affiliate Promoter of the Year. In 2016, he was recognized by Concrete Producer magazine as the industry’s Most Influential and also noted, Most Influential by Concrete Construction Magazine in 2017.
Jereme joins Stephens & Smith Construction Company to continue their success providing concrete construction services to many of the top General Contractors and other clients in Nebraska and surrounding areas. Jereme comments “I’m excited to start this new chapter in my career with S&S and look forward to working with an excellent team of concrete professionals to further develop their already extensive product and services. I am extremely blessed to be joining such a respected company that prides itself on top quality service.”
Steve Willis, CEO of Stephens & Smith states “We are excited to have Jereme join us, and are confident that his work and enthusiasm will help bring new opportunities and growth. We view his appointment as a sign of our commitment to being the leading company in our industry. New innovations and the increasing demand from our customers led us to look for an addition to our team who would fit the culture of our company, and it is fortunate that we were able to find someone of Jereme’s caliber to fulfill this role.”
About Stephens & Smith Construction Company\
Founded in 1971, Stephens & Smith Construction Company Inc. focuses on services in residential and commercial flatwork, foundations, decorative concrete, and specialty products. The company’s reputation and credibility speaks for itself. With over 45 years in business, they have grown exponentially over the years, due to their unique structure and approach to the company makeup. Their reputation has been the very foundation of their expansion, along with the valuable employees that have joined the team along the way. More information on the company’s notable achievements, services provided, and history can be seen on their website as well. www.stephensandsmith.com
For Sale: 2005 Western Star Crane Truck
For sale by a CFA member is a 2005 Western Star Crane Truck. Truck is in excellent running and working condition. My shop manager has thoroughly reviewed the equipment and verified no repair is required. Details of the equipment are as follows:
- Model: 4900SA
- Engine: Mercedes OM460LA, 450 HP
- Mileage: 174,574
- Hours: 10,381
- Vin: 5KKHALCVX5PU00833
- 2005 IMT Crane
- Model: 34-235
- Serial: 360446
- Price $135,000.00
For more information or interest, contact:
Darrell Colvard
Fleet Manager, Doggett Concrete, Inc.
p (704) 554-9200 | m (704) 634-0834
dcolvard@doggettconcrete.com
Photos of the truck are below.
FOR SALE: Trimble 5600 Geodimeter and Miscellaneous Equipment
CFA member looking to sell a used Robotic Layout machine. To go along with the machine, we have multiple data collectors with and without pole mounts, 360 prisms, and charging units. For more information contact Bob Nickoloff at 440 647 6661, or bnickoloff@mpwcs.com.
List of items can be seen pictured below and includes:
- Trimble 5600 Model 360 Target Prism
- Trimble CU Alpha Data Collectors with Pole Mount
- Trimble 560 2.4 ghz Robotic Total Station with Case
- Trimble Super Charger with Charging Cables and Power Supply
- Trimble Data Collectors, 1 TSCe and 2 Recon
Winter Walls – The Walls Are “Leaking”
As published in Concrete Contractor Magazine, April 10, 2017. This column presents a comparison issue between what is assumed to be faulty construction or installation and the natural hydration process combined with the change of seasons.
Question:
Last winter we installed several foundations for a builder in one development. He called this week asking us to provide inspection and support for a home owner claiming to have moisture along the foundation walls and slab perimeter. They see wall cracks and some shrinkage cracks in the slab and are challenging that the new concrete is leaking. This builder is asking us to provide a written explanation to give to their clients or an inspection report to determine if the walls are the problem. Can you help us identify the issue?
Answer:
The concrete foundation you installed this winter, like so many basements across northern climates, very likely achieved a frozen or near frozen state at some point, which is quite common. Cold weather requirements establish this cannot occur until after initial strength gain beyond 500 psi to prevent surface durability issues (ACI 332-14). When this happened, the hydration process slowed, and if truly frozen, stopped until the concrete temperature is returned to a level high enough for hydration to resume (+/- 30 degrees F).
Now spring, these walls contain significant moisture that will be consumed by this resuming hydration along with a considerable amount that will evaporate into the adjacent warming air of the confined basement spaces. Spring is also when the frost leaves the ground and rains begin to saturate the surrounding soils. The drainage systems properly installed will see an increase in water activity and sump pumps will not likely fully dry out. Here is where the problem begins.
Thousands of new foundations across a large portion of North America are constructed annually during the colder months of the year. Building demand does not slow for Old Man Winter and, in fact, builders must maintain aggressive construction schedules during these winter months to meet the growing demand of spring sales. Such aggressive schedules require foundation installation during cooler and even frozen temperature conditions. This can be ideal for developing stronger concrete as the impact of evaporation is lessened, maintaining moisture in the walls longer for the cement hydration process. However, when the concrete temperature drops low enough for the water molecules to freeze, this moisture is held at a constant, neither being consumed by hydration nor leaving the wall by evaporation.
ACI 332-14 specifies a maximum water to cementitious material ratio (w/cm) of 0.45 and as seen in Mix 3 of figure 1 (a common mix design for residential concrete walls), this means that around 20 percent of the concrete is water. We will not go through the math here but it is not uncommon for a yard of concrete to contain approximately 40 gallons of water. Each ready-mix truck carries between seven and ten yards of concrete…a lot of water.
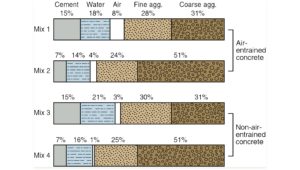
Figure 1: Examples of mix proportioning to alter the performance of concrete for strength, durability or other required performance consideration.
Fast forward to the spring. Not only are the grasses and flowers waking up, the new foundation walls and the concrete can be said to be waking up as well. Even if the walls have reached full design strength, the amount of water that potentially remains within the concrete volume can be significant when considered in potential volume of gas. The waterproofed exterior of the foundation wall properly provides for long term performance and now this coating also prevents the moisture contained in the concrete from migrating into the soils and open exterior air. A fully-enclosed home has been built on top of the foundation wall, complete with floor deck sheathing or perhaps even finished flooring. The basement now exists as a super-chilled space of walls with considerable thermal mass at a relatively constant temperature along with confined air temperatures beginning to rise ever so slowly.
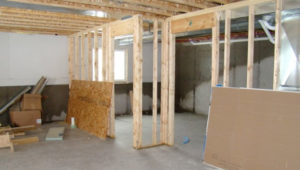
Figure 2: Condensation shown along the back walls of a foundation where air movement is negligible. A home owner may consider this a leaking wall if not properly informed.
Warming air achieves two known constants: 1) it begins to move and 2) it begins to absorb or take on an increasing amount of moisture (Figure 2). As the temperatures rise during the day, the air begins to move slowly along the concrete walls, still fresh from the winter construction. This movement picks up some of the water vapor that begins to evaporate from the concrete while it is also continues to hydrate. During the evening, air temperatures begin to cool again and the air can no longer hold the same amount of moisture (Figure 3). Since the basement is closed, air is no longer moving and the colder concrete walls become the ideal location for this moisture to condense back out of the air, resulting in darkening of the walls, condensation on slicker surfaces and along the base of the foundation walls. Cracks also present or are emphasized by this gathering moisture as there is greater surface area where natural shrinkage cracking has occurred in both slabs and walls. Cracks in concrete are part of a different discussion but for the application to this discussion, the cracks are not presenting moisture into the foundation, they are receiving the moisture from the air and the naturally-evaporating walls. This is a crucial conversation to have with the prospective home owner and builder so that proper preparation and maintenance of the space can be selected.
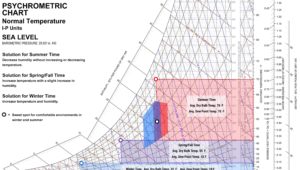
Figure 3: A common psychometric chart demonstrates the relationship between air temperature and moisture capacity, which produces relative humidity. Condensation occurs when air at a given temperature and moisture content meets a chilled surface forcing the air temperature to immediately change at the surface, dropping moisture in the form of condensation.
Is any of this a problem for the home owner? It is not very likely to ever be a problem provided that means of establishing a balance between air temperature and moisture exists. The easiest solution for the builder is a short-term dehumidifier to draw the excess moisture out of the concrete. The best solution for the home owner would be for the mechanical contractor to design a heat pump system that exchanges air in the basement with air in other parts of the home to take advantage of the natural heat-sink and more constant temperature of the basement, naturally removing the moisture as well. Eventually, the concrete will achieve an equilibrium in moisture content, generally within the first full year and moisture condensation due to the concrete is no longer noticed. However, moisture can still be an issue for those homes that never resolve the lack of air movement in the basement, a problem not attributed to the concrete foundation in any way.
Jim Baty is the Executive Director for the Concrete Foundations Association after having served as Technical Director since 2001. He is immediate past chair of ACI 332, currently chair of 332-D for Footing and Foundations and a voting member for ACI 306 and C-655 with priorities of establishing better guidance and structure for residential concrete construction as well as ACI 551 and C-650. For more information on this topic, contact Jim Baty at jbaty@cfaconcretepros.org. Find out more at www.cfaconcretepros.org.
References:
1 Residential Code Requirements for Structural Concrete (ACI 332-14) and Commentary published by the American Concrete Institute, www.concrete.org
2 How To Read A Psychometric Chart authored by Ryan Noble, published by QWare, June 2, 2016 | blog.qwarecmms.com