2021 PROJECTS OF THE YEAR
For more than twenty years, contractors have been given a platform to show off their accomplishments, feats, and the solutions to headaches encountered day in and day out across North America. This platform was first instituted as the “Basement From Hell,” which later became the “Basement of the Year,” where the goal was to identify a single top project. In its current form, known as the “Projects of the Year,” the platform has expanded to offer great variety for project recognitions.
Today, contractors continue to vie for elite recognition, as the program has become a cornerstone for them to advance the industry’s culture and elevate their marketing. Companies have discovered that submitting each year has been a key team-building component and has boosted morale by showing appreciation for and pride in jobs well done. Others have noted the impact on customer relationships when they hand a key account holder a plaque showing national recognition, which fosters stronger client retention and repeat business. Whether contractors are submitting for the first time or committing to annual participation, the process of recording, reflecting, and describing a project gives a company space to express why they are a leader in the marketplace, and that comes regardless of whether or not the competition elevates that effort to national recognition.
Here they are, the best of the best for 2021, the CFA Projects of the Year, recognized during #CFACON21 in Charleston, South Carolina, this past July. Though there is a near sweep from the state of Utah, submittals were received from coast to coast, once again demonstrating the diverse landscape of project types, sizes, complexity, and experiences.
___________________________________________________________________________________________________
ABOVE-GRADE CONCRETE HOME AWARD
Above-Grade There Are Leaders and Then There Are… | Elan by Burton
TCB WALLS INC.
West Melbourne, FL
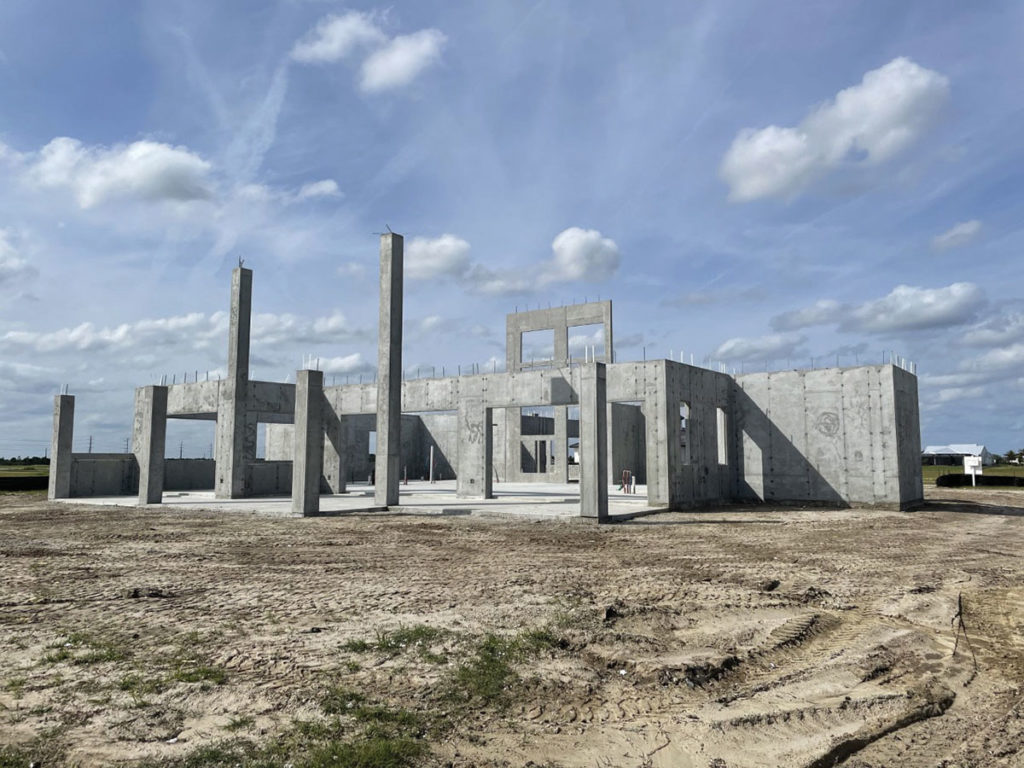
Marketed as “The Cure for Block,” the residential concrete shells being constructed by TCB Walls Inc. of West Melbourne, Florida, are quickly becoming a recognized standard for an acute section of the housing industry. Ironically, it is the performance of these all-concrete shells that should become the new standard across the much larger cross-section of the country, which is storm-ravaged, fire-scorched, and flood-weary. These (and many other labels that the disposable-housing trends in the U.S. continue to attempt to justify) speak to how the current housing market is holding on to outdated methods and delivering what some would describe as over-priced, disposable solutions.
Set in the sunny landscape of Viera, Florida, this year’s winner of the Above-Grade Project of the Year is a 6,040-square-foot example of high-quality concrete and intricate steel reinforcement detailing. Although primarily a single-story structural shell with just over 400 linear feet of wall, this project challenged the contractor to deliver a two-story, free-standing entrance wall along with several stately columns on the back of the project to support the veranda decking.

“We have been working for this contractor for over a decade, and cast-in-place concrete is available as an upgrade to any home they build,” said company president, Tim Ball. “Their clients are introduced to this option if they want the strongest, most durable home available to them. Over the last few years, this type of modern look has been gaining popularity in our area. The GC now has an entire line of homes dedicated to it as homeowners look to build security amidst the hurricane-level forces. The clean lines and square looks are very conducive to the cast-in-place wall system.”
The shell weighs in with 83 cubic yards of concrete and 7,700 pounds of steel reinforcement bars and another 1,120 pounds of Helix® Micro Rebar®. The majority of the walls are between 11 feet and 13 feet 4 inches in height, while two walls are 25 feet and 21 feet 8 inches. Wall thicknesses are predominantly 6 and 12 inches in thickness with the taller walls increased to 14 and 16 inches.
“While this project isn’t much different than all the custom homes we regularly produced, it does demonstrate the high quality of what we do every day,” Ball said.
Constructed in one continuous pour, TCB Walls had to use hydraulic lifts and two concrete pumps. “It was imperative for this client that the concrete not have pour lines or construction joints. Therefore, once concrete placement started, the entire project needed to be delivered with seamless integration,” Ball said.
Among the project’s most challenging aspects, namely, those aspects that required elevating crewmembers off the ground in the lifts during forming and placement, were the free-standing two-story columns and the two two-story sections of wall. These wall sections contained stacked windows and large beams, making the steel detailing intricate and the concrete consolidation challenging. The steel reinforcement was designed with #3, #4, #5, #7, and #8 rebar, and heavy doses of Helix were incorporated to achieve a design suitable to withstanding strong winds while maintaining an economical shell.
When asked about the most impressive aspect of this project, Ball said: “I think what we are most proud of for this project was that we set and placed concrete for the entire structure in just eight days. We then removed forms from this one and moved on to the next shell of 8,200 square feet followed by a two-story, 20,500-square-foot townhome. We don’t get much time to stop and appreciate our accomplishments these days, so it is great to have this program to help us focus on our successes.”
___________________________________________________________________________________________________
MULTI-FAMILY COMPLEX AWARD
Strung Together—Multi-Family Complex in the Mountains | Sterling at Capitol Hill Lots 105 and 106
SCW FOOTINGS & FOUNDATIONS
Salt Lake City, Utah

This year’s Multi-Family Apartment or Townhome Award goes to a project consisting of a series of efficient duplex foundation structures arrayed across a hillside in the mountains above Salt Lake City, Utah. While the project’s area as a whole is over 4,000 square feet, each duplex is only 800 square feet.
“Don’t let these little guys fool you,” states CEO and owner at SCW, Kirby Justesen. “While the area of each foundation is nothing striking, they are carved into the hillside along this drive. The foundation walls we had to create were between 19 feet 6 inches and 21 feet 6 inches in height across the backs, stepping down several times to sidewalls that were 1 foot 4 inches. In such a small footprint, these were very challenging to form and get the concrete placed.”

The total project weighs in with 127 cubic yards of concrete and over 14,000 pounds of steel reinforcement. Wall thicknesses range from 6 inches for the shorter sections to 8, 10, 12, and 16 inches for the tallest back walls.
“These are really retaining walls, considering the small plan size and the lack of much intersecting them for buttressing or stabilizing them,” the project manager, Raul Hernandez, said. “In all but one, each back wall has an offset near the midpoint to provide additional stability. These short offsets at such tall heights are real challenges to both the forming and the concrete placement processes.”
Seven separate footing steps of 11 feet 6 inches in total vertical grade change were required for these foundations. Due to the region’s soft soils and seismic conditions, the footings were 20 inches wide along the exterior sides with 18-inch interior footings. “By far the most striking part of this project is the 110-inch-wide footings supporting the tall rear walls on each of these structures,” Justesen said. “They are a result of the retaining wall design and the stability necessary to support such tall walls against the hillside. The steel detailing from these wide footings into the walls was very intricate and time consuming.”
When asked whether there was any unique aspect of their approach to this project, Hernandez said, “Every contractor knows that any project starts with the bidding process. We strive to ensure accuracy and profitability for both our company and the GC. To achieve this, scheduling plays a big role in providing the attention needed for such a project. As project manager, I study the plans alongside our CAD operator and find ways to simplify the project details to relay them more easily to the crews on site. We find that this allows them to refine our process, tackling each project at hand and providing excellence every time.”
SCW Footings & Foundations has established a reputation of efficiency coupled with overall quality throughout this market, making them the top choice for this contractor and the many others they serve. This Multi-Family Complex Award is only just the beginning of their achievements shown in the 2021 Projects of the Year.
___________________________________________________________________________________________________
2K–5K SINGLE-FAMILY RESIDENTIAL FOUNDATION AWARD
A Fortress By Any Other Name | Stapley Residence
SCW FOOTINGS & FOUNDATIONS
Salt Lake City, Utah
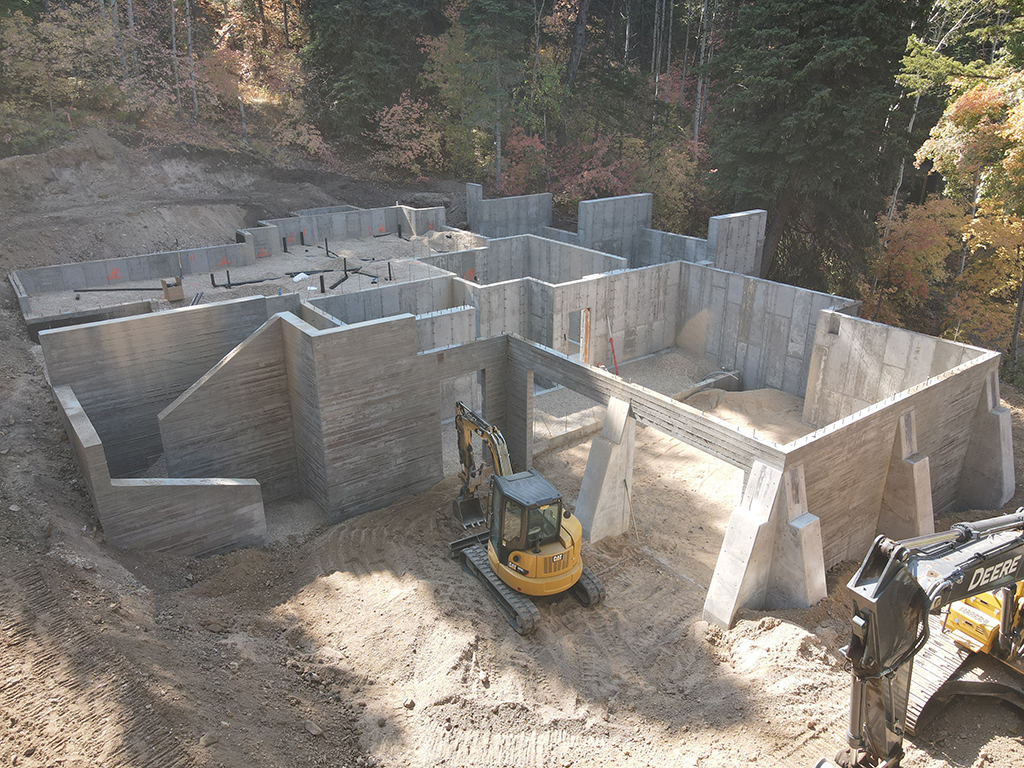
The concrete challenge of the Stapley Residence creates the effect of an epic setting for an impenetrable fortress. Battered walls, a labyrinth-like floor plan, and the rough texture of a board-form finish easily set this mid-size project apart with high marks.
This home is located in the timberline of Sundance, Utah, and its modest size of 4,365 square feet is overshadowed by the massive presence of form, texture, and amount of concrete. Over 570 linear feet of wall does little to evidence the complexity of buttresses that project outward from the attached garage. The foundation weighs in with nearly 380 cubic yards of concrete and more than 22,000 pounds of steel reinforcement, which speaks to the intense design requirements of the high-seismic region.
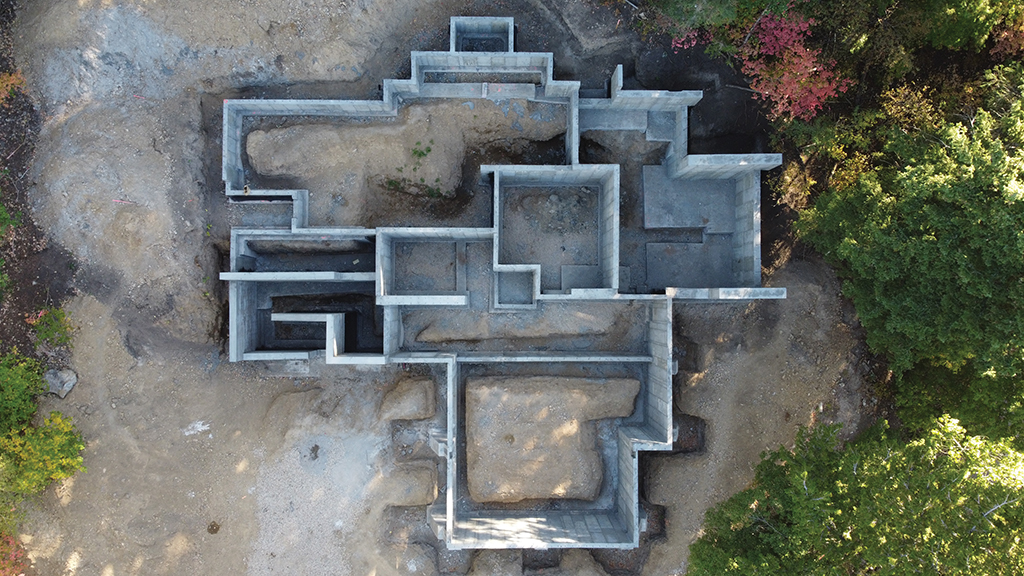
“The most impressive aspect of this project,” said CEO and owner of SCW, Kirby Justesen, “is the amount of above-grade exposed walls and the level of finish the client wanted from us. We have seen a strong preference over the last decade for architectural board-form finish, and this has taken us on quite a journey to perfect it. This project combined considerable surface area of board form with a smooth-ply architectural finish. The look is striking between the rough-hewn and the perfectly smooth.”
The foundation’s surface finish treatments are just the start of this project’s impressive features. Wall heights range from 1 foot high to 17 feet 6 inches. There are 68 linear feet of double-sided board-form-finished sloping walls that define a stair entry rising from the driveway. Seven different wall thickness measurements range from 6 to 24 inches. It is the thickest walls, however, that perhaps get the most attention. These walls function as buttresses or sloping counterforts around the garage, two of which the owners drive between as they enter through either of the single-car 10-foot openings and others framing around a 4-by-9-foot cast-in-place entry door.
Underneath the complexity of this half-and-half foundation is a footing complex with nineteen separate steps with a vertical grade change of more than 45 feet. Nearly all the footings are continuous-grade footings, with widths of 18 inches, 24 inches, 36 inches, 72 inches, and a whopping 114 inches.
“This has to be the most extreme project to date for us in terms of applying the architectural board-form finish,” Justesen said. “This was complex work, building the two-sided finish and then transitioning to such a smooth texture, particularly at the 24-inch-wide battered columns. We are very proud of the work our skilled crew was able to achieve and for the experienced leadership that was able to accomplish the great finished look.”
Historically, the CFA Projects of the Year competition’s top end is the “Over 5,000 Square Feet” category with large and small foundations competing. Along with the shear number of entries this year and the extremely close balloting, there was an especially large spread of foundation sizes. In order to better represent and honor projects in this top-level flight, judges segmented the entries and awarded a 5k–10k foundation, a 10k–25k foundation, and a first-ever over–25k foundation, while still including the Overall Grand Project of the Year.
___________________________________________________________________________________________________
5K–10K SINGLE-FAMILY RESIDENTIAL FOUNDATION AWARD
Cascading Down from a Mountaintop Experience | Lone Peak Lot 8
SCW FOOTINGS & FOUNDATIONS
Salt Lake City, Utah
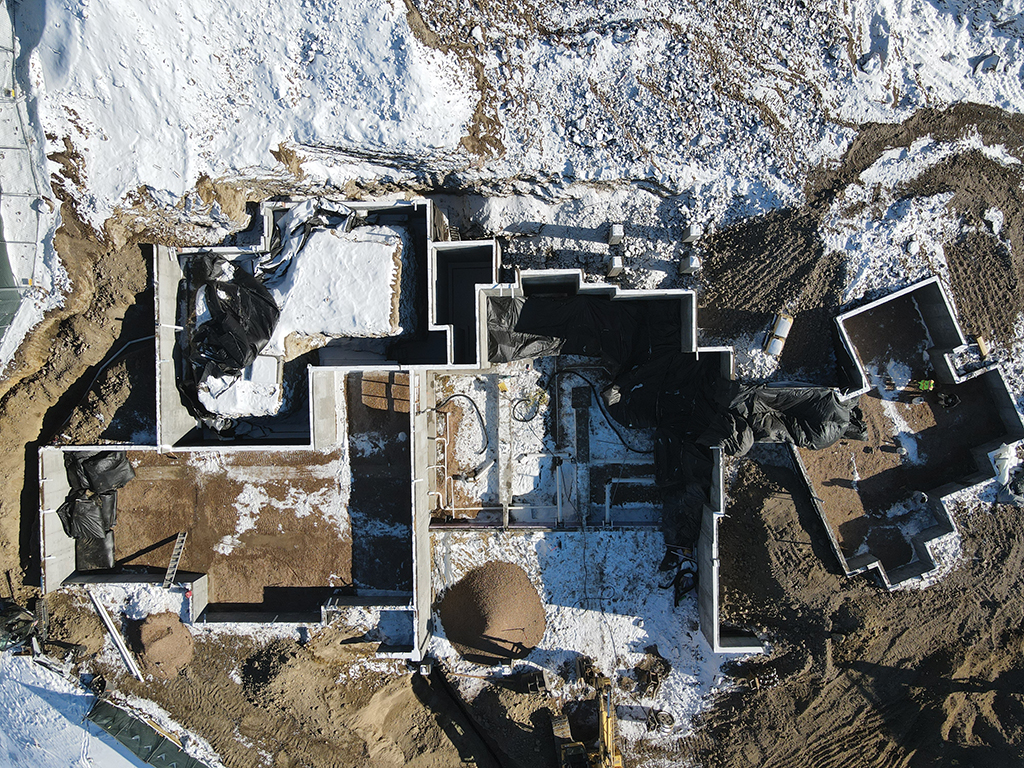
Keeping up their strong performance in this year’s submittals, SCW Footings & Foundations entered a staggering complex of footings and foundation walls for this modest 5,232-square-foot foundation in Wasatch County, Utah. This project was built near the top of a mountain range and was completed during the start of winter, so it was influenced by cold weather concrete protection decisions.
The 640 linear feet of cast-in-place foundation walls are comprised of 322 cubic yards of concrete and nearly 26,500 pounds of steel reinforcement; the walls step downward considerably as the project cascades from the upper elevation. Wall heights range from 4 feet up to 17 feet 4 inches and, for a change, have basic thicknesses of 8 and 10 inches.

“The basic statistics on this foundation should not be taken lightly,” said Raul Hernandez, project manager for SCW. “The lot required fourteen separate footing steps with a staggering 54 feet in vertical grade change. We had a long way to go from the top. The footing widths were 24 inches, 30 inches, 36 inches, and one of our widest ever at 122 inches. We also had several pad footings that ranged from 36 inches by 36 inches up to 96 inches by 96 inches.”
The complexity did not stop at the footings. The foundation walls step nineteen times, and from the tallest anchor bolt location to the lowest, there was 78 feet of vertical grade change, nearly six stories. Within this challenging changing wall height, 58 percent of the walls ranged from 10 feet to 17 feet 4 inches in height. As the walls near the lowest grade, retaining walls transition at the rear walkout area with tops sloping 4 inches along the lengths.
“We had a lot of embedded items in this project that further challenged the schedule,” Hernandez said. “We had twelve separate base plates, six embedded plates, and two door bucks that were cast-in-place, something we don’t experience all that often. The rocky landscape and the different finished floor elevations were our biggest challenges, as this project stepped downward with such a massive vertical grade change. Every footing step required additional bracing to avoid concrete blowouts during forming and much more extensive steel reinforcement detailing than even we are used to.”
“A project with this much technical challenge can only be met successfully with a combination of skill, attention to detail, and seasoned experience in understanding and applying forming and in knowledge about the concrete itself,” said Justesen. “We continue to be very proud of the extreme work our top crews are able to accomplish and take very seriously the reputation we have built in this market for this measure of excellence.”
___________________________________________________________________________________________________
10K–25K SINGLE-FAMILY RESIDENTIAL FOUNDATION AWARD
Taking Residential Concreting to the Extreme | 2201 and 2209 Bayside
EKEDAL CONCRETE INC.
Irvine, CA

Anyone who follows the Projects of the Year Awards for multiple years will begin to recognize the name and reputation of this winning entry. Breaking the monopoly on foundation awards this year is a monstrous foundation that is so large it is comprised of two former home sites located in Corona Del Mar, California.
The uniqueness of this lot overlooking the marina is a striking setting for an extreme level of concrete proficiency, which is the primary reason Patterson Custom Homes selected Ekedal Concrete. The project sits right on the bay front in Newport Beach, and consists of a 10,000-square-foot basement foundation along with a 12-inch cast-in-place podium deck sitting over it.
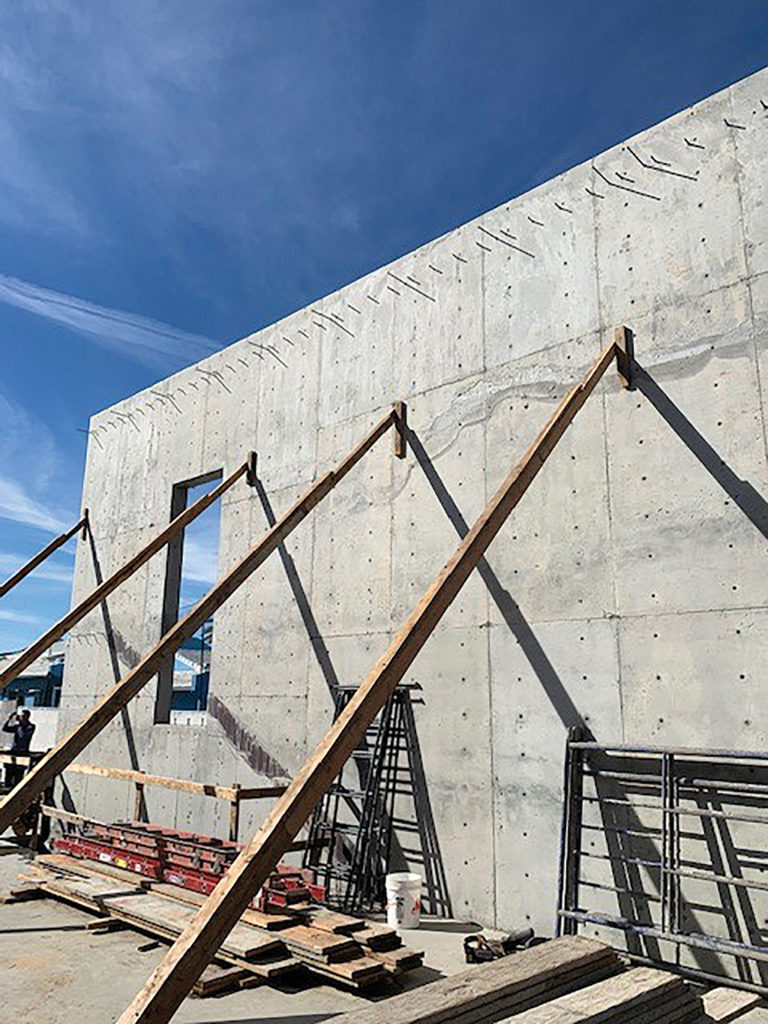
Projects along this stretch of the California coastline extend downward to great depths, which challenges the construction team. “This project sits below the sea level at its lowest,” said Ryan Ekedal, president for Ekedal Concrete. “Therefore, we were required to install a shoring and dewatering system. We ended up drilling forty-eight 30-inch caissons averaging 39.5 feet each with a total drilling depth of 1,900 feet. Following this, we set W24X130 soldier beams that were roughly 40 feet long. Once all shoring piles were drilled and concrete placed, nineteen 18-inch diameter dewatering well points were drilled to a depth of 20 feet. We then set up the dewatering system to bring the water table down to below the bottom of slab so we would have a dry working environment, even though it was below sea level. The Coastal Commission required a filtration system to treat for metallic impurities prior to any water being ejected back into the ocean. The system pumped out over 100 gallons a minute into the bay, 24/7 for six months until the basement walls were backfilled.
A project of this nature goes well beyond the norm when it comes to average residential foundations, regardless of size. Still, the project stats are impressive, including 4,550 cubic yards of concrete along with 750,000 pounds of steel reinforcement. Cast-in-place wall heights are 12 to 13 feet in height and both the shotcrete and CIP walls are 12 inches thick.
“The shoring wall was 20 feet tall and battered from 12 inches to 15 inches. For this reason it had to be placed with shotcrete,” Ekedal said. “We then had several walls which were cast in place. This project had far too much hardware along the tops of walls, so we needed to utilize traditional forms to locate and hang the hardware prior to concrete placement. Additionally, a 30-foot freestanding poured wall sat on top of the podium deck. This required bracing to remain in place until cured and engineering sign off was received.”
Even the casual reader would agree there are many challenging details worth noting from this project. “For our team, the most difficult portion was getting the mix designs dialed in so we would have proper movement of the aggregate during the placements,” Ekedal said. “The large rebar diameters and one-inch aggregate maximum could prove problematic with a design that would inhibit formation of rock pockets. This also held true for concrete placement for the caissons. The mix was custom formulated to take into consideration the water and soils, and to be able to insert or push the I-beam down into the poured concrete caisson. These caissons were tough, as they were drilled well into the water table, which we had to then use steel casings to keep the holes open, preventing cave in.”
This is the type of job that would put many companies out of business if they did not know what they were doing. The project had everything imaginable, including caissons/shoring, dewatering, water filtration, mat slab, battered shotcrete walls, waterproofing, radius cast-in-place walls, outrageous rebar details, podium decks, and radius driveway deck (above grade), to highlight the big items. The project also required all steel reinforcement for the mat slab to be epoxy coated, and all concrete was specified at 5,000 psi minimum with a Xypex waterproofing admixture.
“A very complex project due to its size and the location of a foundation below sea level,” Ekedal said. “You have to be very cognizant of the amount of water being drawn down by the dewatering system, because you need to be aware of how much water needs to be pulled. Too much water pulled brings with it fine sands and could create voids under neighboring properties. Our long history of working in these environments gave us the confidence to approach the project. By working directly with Patterson Custom Homes, the architect and engineer, we were able to get needed dimensions for points and intersections at critical locations. Our pre-construction team was critical in staying far ahead of the work in the field by addressing clashes.”
___________________________________________________________________________________________________
2021 OVERALL GRAND PROJECT OF THE YEAR
OVER-25K SINGLE-FAMILY RESIDENTIAL FOUNDATION AWARD
The Biggest, the Baddest, the Beast | Quail Hollow Estates
SCW FOOTINGS & FOUNDATIONS
Salt Lake City, Utah
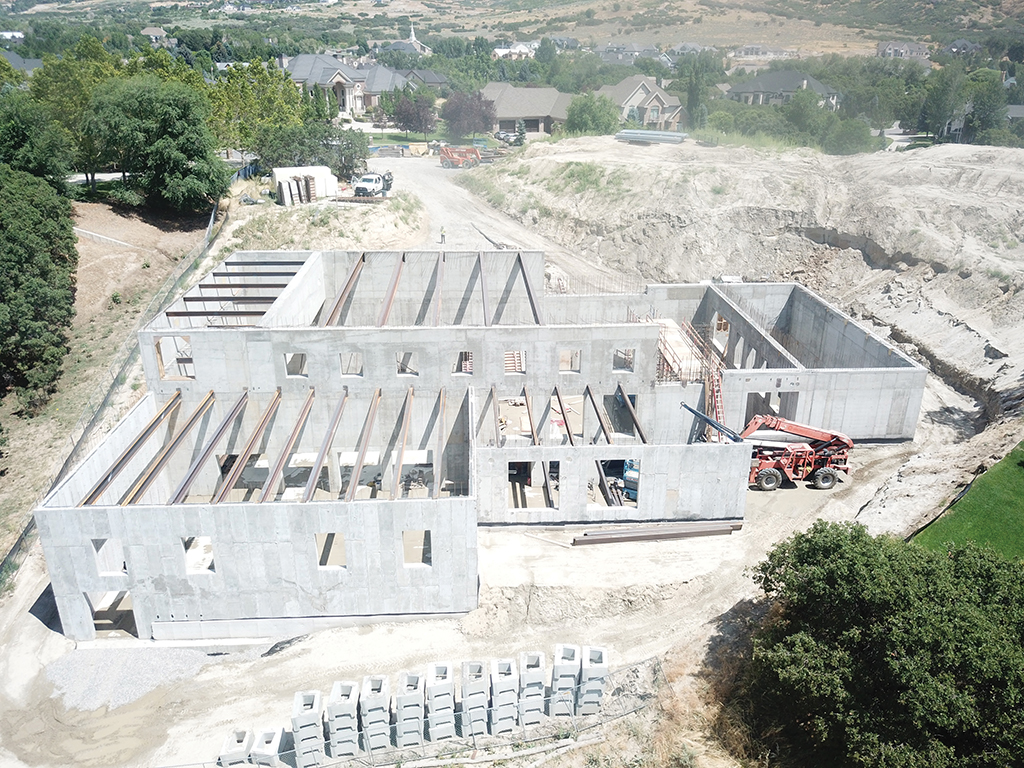
Laying claim to one of the most prolific years of unique and spell-binding projects, SCW Footing & Foundations finishes off the 2021 Projects of the Year with this Overall Grand Project Award for their project in Alpine, Utah, known as Quail Hollow Estates. At first glance, this project might resemble more of a commercial project or complex. As the details unfold, however, the complexity of the hidden foundation with connecting tunnels and the programmed space for a single residential customer make this one of the most staggering winners in the history of the Association.
Topping out at 31,605 square feet, the Quail Hollow Estate adds up nearly 2,800 linear feet of cast-in-place concrete wall with nearly 3,600 cubic yards of concrete and over 357,000 pounds of steel reinforcement ranging from #3 to #10 rebar. The wall heights range from 1 foot 6 inches up to 33 feet with thicknesses of 6 inches, 8 inches, 12 inches, 18 inches, and 24 inches.
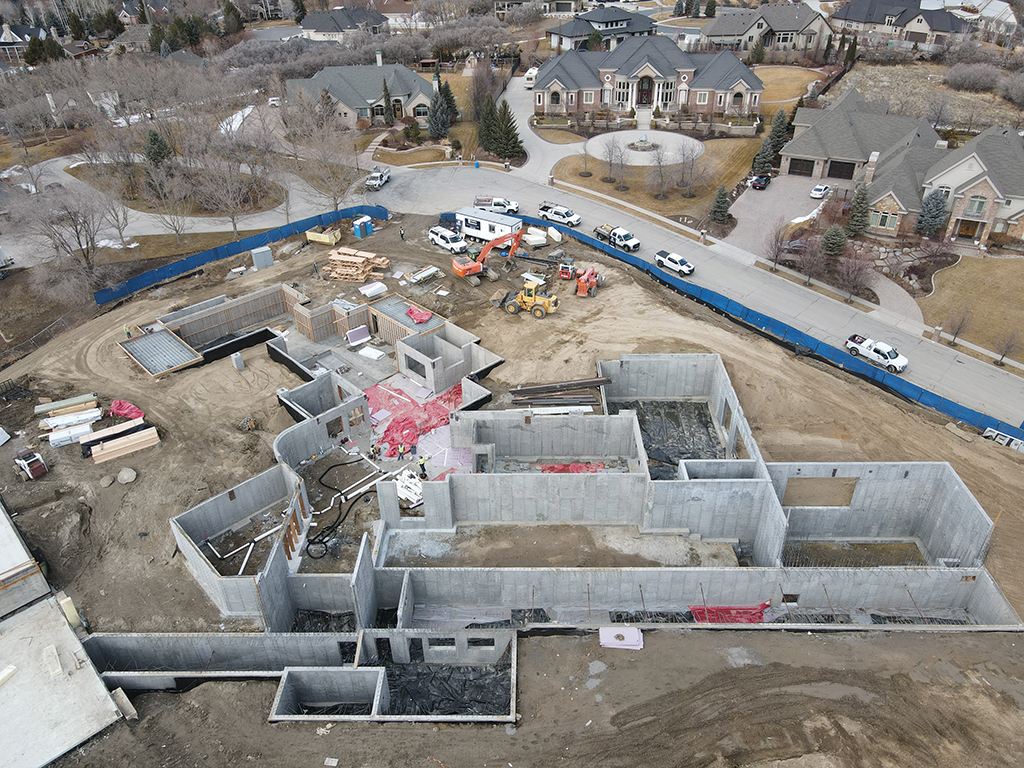
“This was a massive project,” said Raul Hernandez, project manager for SCW. “The layout to this estate extends 284 feet by 273 feet across the property lot. A lower storage level is underground and connects the residence to the sports complex.”
This project required twenty-nine footing steps with 83 feet of vertical grade change between the two major plan elements, one of which is a sports complex. The continuous footing complexity was joined by a massive, three-part footing pad of 151 feet by 68 feet by 24 inches deep; 63 feet by 37 feet by 24 inches deep; and 44 feet by 22 feet by 18 inches deep.
“One of the most unique project elements we have faced were the two concrete beams,” Hernandez said. “They were 60 feet in length, 12 feet in depth, and 2 feet thick, but they were also 21 feet above the finished floor. Forming was very challenging, concrete placement even more, and accommodating the time of curing for the beams in the schedule was very unusual.”
Scheduling for this massive project was the first challenge the SCW team had to address. The massive layout required twenty-two separate concrete pours, nine for the residence (including four footing pours), and five foundation pours. The sports complex needed four footing pours and nine foundation pours. The size of the sports complex required a crane on site for the entire foundation building process. “Due to the shoring for the concrete beams and the significant reinforcement sizes, particularly for the long rebar in the sports complex footing pads, we staged the crane in the center of the complex,” Hernandez said. “We had to build in a way we could drive the crane out of the project site when finished.”
When asked about the comparison of this project to others they have experienced, Hernandez said that being able to produce straight and plum walls with many vertical and horizontal cold joints was among the most difficult tasks of this project. Detailing the schedule and planning the use of additional bracing where pours would end overcame these constraints across the multiple pours and insured the continuation of pours to align properly. “This all couldn’t have been possible without the great teamwork and coordination from the project manager through to the crews on site,” said Kirby Justesen, SCW CEO and owner.