Casting Residential Foundation Walls in Cold Weather
By James R Baty II, F.ACI, Executive Director
During a recent CFA event, conversation took place regarding the research significance undertaken by the Association at the start of this new millennium – research that was, in most respects, the first of its kind. What plagued the industry at that time was scrutiny that concrete placed during conditions deemed as “cold weather” was in conflict with the then-current codes. As a current reader of Concrete Facts, it is probable that such research is new to you, considering this magazine has only been a free-subscription resource to the marketplace for about five years. And yet, this research is repeatedly lifted to our attention as having an instrumental role in regional progress for the acceptance of quality control measures for cold weather concrete. Therefore, we are revisiting this topic here, at the onset of the cold-weather season (though many have already been at it for a month), complete with updated references.
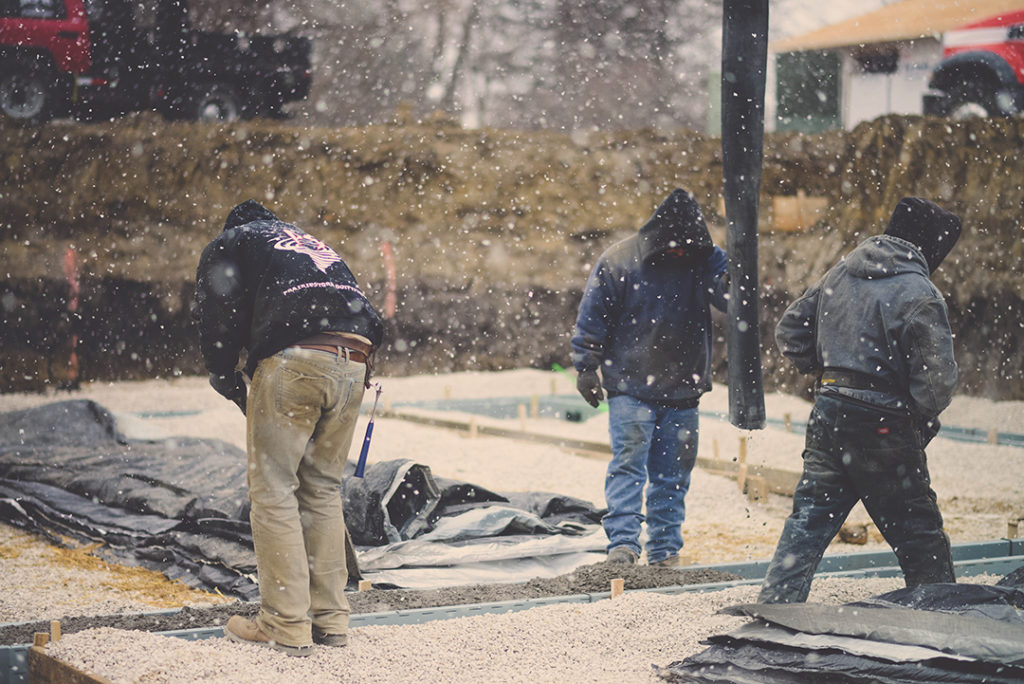
In 2004, a research task force developed by the Concrete Foundation Association (CFA) completed a three-year effort to better understand the performance of residential concrete foundation walls cast during extreme cold-weather conditions. This research began with moderate cold-weather impacts investigated in laboratory conditions and finished with actual extreme cold-weather job site conditions. The purpose of this research was to provide the industry with rationale practices to maintain concrete quality with budget sensitivity.
Before this research, concrete technology and, more importantly, cold-weather guidance and standards (as they related to cold weather) were largely founded on the premise that concrete freezes early on in temperature decline and ceases to gain strength once frozen. At that time, it was felt that nearly every contractor negatively impacted residential concrete by adding water. The purpose of adding water during cold weather was assumed to be solely to make it easier for contractors to work, or perhaps to improve the concrete flow throughout the formwork, weakening the concrete enough to be of structural concern. Some documented cases resulted in surface deficiencies and long-term durability impact to the aesthetics of the concrete surface. Residential concrete foundation walls, however, have always demonstrated higher-than-expected strength. While misuse of water was the primary concerning focus for cold-weather concreting, many other misconceptions and influences contributed to the larger diagnosis that there are definitely times that are “too cold to pour.” This began to come to a head as key industry guides and standards, such as ACI 306, evolved to be far too restrictive. This regulatory tightening happened despite significant empirical evidence and experienced construction practice that supported far less restrictive measures. As a result, prior to the completion of this research (and perhaps even still today), building officials and inspectors routinely shut down foundation projects, or practically shut them down by requiring heroic measures to cure in-place concrete. The judgments made by such officials are based on a narrow interpretation of theory versus practice and a lack of available information as to what is really important.
The research premise put forth by the CFA recognized the great number of variables that affect the performance of concrete in cold temperatures. These variables include mass-to-surface-area ratio, protection from evaporation, limited exposure to wind effects (below grade), forming system and admixtures. This more complex picture gives evidence that regulations governing concrete pours in cold weather should be performance-based with the ability to predict, respond and monitor the achievable concrete quality as more than a function of the weather forecast.
Even today, in some regions, residential foundation contractors find either local codes or mindsets so restrictive during winter months that the residential market’s economy is significantly jeopardized. Restrictive requirements included tenting and heating, full blanketing, curing protection until achieving full design strength, and prohibiting or altering placements in temperatures as high as 50 F. While there are preparation and equipment limitations in some markets for the production and delivery of higher-target concrete temperatures, cold-weather concrete is a broad topic that needs to be more fully understood and embraced.
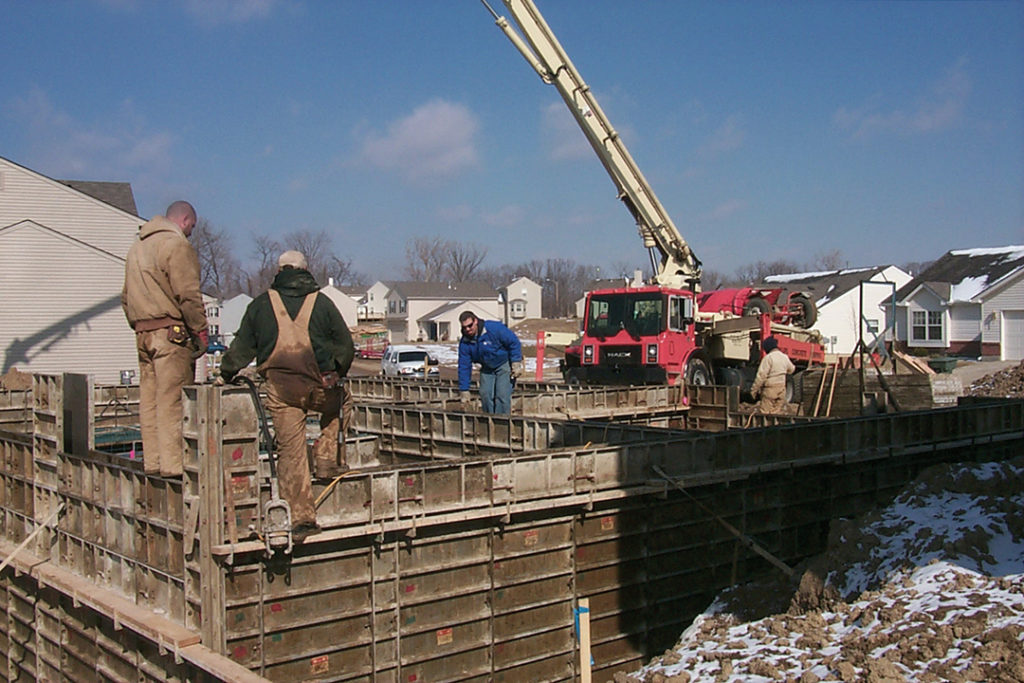
An encouraging fact to know as a contractor in the industry is that reliable research has changed many mindsets and code requirements. Not only do contractors continue to report much greater ease of cold-weather foundation efforts, but they also report greater concrete durability and many self-imposed practices that are improving both the concrete work and the concrete quality. While the information the rest of this article presents is largely from the completion of the 2004 research, it remains important for each contractor active in the residential industry to be mindful of entering a new season of cold weather and knowing where to go for support and third-party assurance.
The Research Project
The interests of residential contractors and the economy of residential concrete during the winter months motivated the CFA to initiate a substantial research project designed to:
- Identify the actual performance of concrete at low temperatures.
- Provide information that would help differentiate between excessive measures and concerns outlined in building codes.
- Recommend intelligent or common-sense practices to be followed.
The goal of the research program was to provide “real world” data about mixes that contractors regularly use, the performance of those mixes at a variety of target temperatures, and what economical modifications should be made to achieve improved performances and results. Due to the realization that variability in concrete exists throughout the U.S. market, the research results were intended to allow contractors to adapt mix designs for regional differences. The complex research came in multiple phases that systematically addressed misconceptions and then showed the viability of the contractor and ready-mix producer working more closely together while contributing sound evidence to prove performance.
The Research Stages
Phase 1 – Following regional surveys, the research committee selected 36 representative mix designs to be tested under laboratory conditions. Concrete mixes were tested in a laboratory provided by Master Builders (now BASF) at 30 F and 50 F ambient conditions. These temperatures were implemented to more closely represent target temperatures being reported by the market as weather predictions when inspectors would begin targeting job sites for delays.
Phase 2 – Full-scale field research studies were then initiated under sub-freezing conditions using a selected sub-set of the original 36 mixes that represented the broadest economic array. All mixes were designed with 6 percent air-entrainment and a slump of 6-inches. All mix components were stored at 60 degrees Fahrenheit prior to batching. By the end of the project, more than 20 cubic yards of concrete had been batched and tested in more than 850 cylinders and 12 wall samples.
Phase 3 – Finally, further results for field data were gathered from 180 core samples taken at varying intervals from the wall samples. These cores were subjected to both compression and petrographic tests to determine the impact of the extreme weather conditions on strength and durability.
Throughout the program, the research implemented maturity testing, which is the science of predicting concrete’s strength gain over time given the mixture’s components and the placement’s temperature profile. The research matrix (fig. 1) produced from Phase 1 shows 44 maturity curves derived from the 36 mix designs subjected to 30 F and 50 F temperatures. Throughout the research, probes monitored representative cylinders and all wall samples, tracking both internal concrete and ambient temperatures.
Phase I – Testing in the Laboratory
To develop a thorough understanding of the strength gain for the various mixtures, 6-by-12-inch cylinders were cast and placed into a refrigerated (50 F) or frozen (30 F) chamber. Cylinders cured at these temperatures were then tested for compressive strength at 1, 2, 3, 7, 14 and 28 days and compared to their maturity curves. This phase consisted of 660 cylinders (fig. 2). The cement for the mixes consisted of either Type I or Type III, with content as low as 5-sack (470 pounds) and as high as 6.5-sack (611 pounds). Because admixtures can contribute to strength gain, especially at lower temperatures, the addition of 1 percent and 2 percent calcium chloride, mid-range water reducers (MRWR), and a non-chloride accelerator (NCR) were also tested.
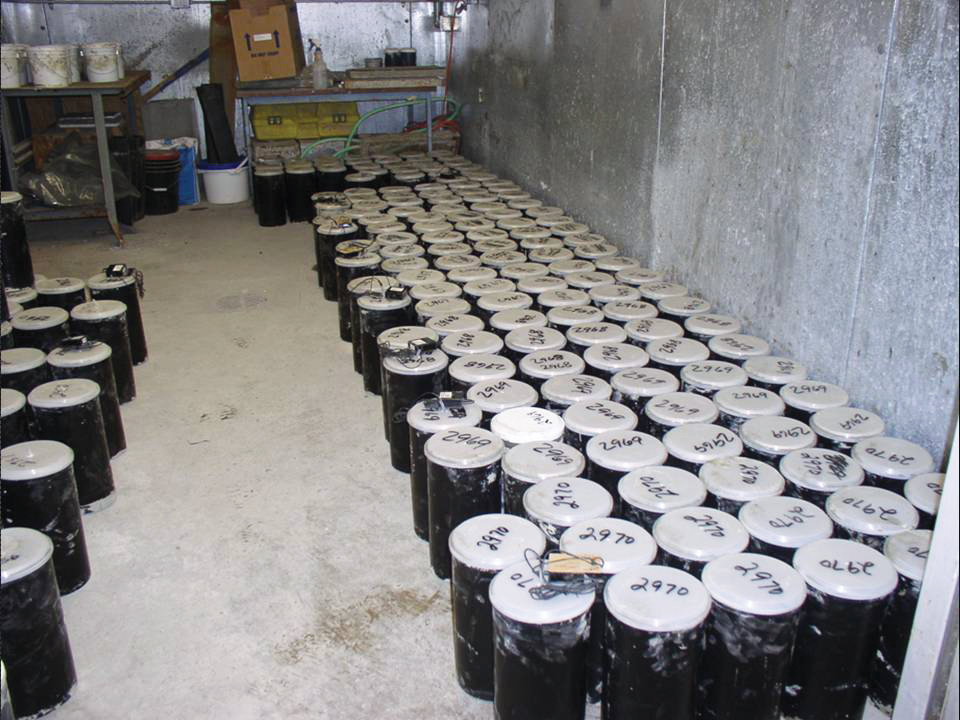
Phase II – Testing in the Field
Phase II brought about field research following closely upon the completion of the Phase I Laboratory research. In this phase, actual eight-inch walls were formed eight feet high in modified job site conditions. The walls were only six-foot-wide segments, and instead of being placed in an excavation, they were formed in a simulated excavation environment in Medina, Ohio, in the yard of Osborne-Medina Ready Mix. The concrete mixes selected from Phase I (fig. 3) represented the most favorable combination of performance and economy.
Figure 3 – Field Research: Phase I Mixes Selected for Phase II
Mix | Cement Qty. | Cement Type | Admixture |
3 | 5-sack | I | 2% Calcium* |
8 | 5.5-sack | I | 2% Calcium* |
13 | 6-sack | I | 2% Calcium* |
24 | 5-sack | III | 1% Calcium* |
29 | 5.5-sack | III | 1% Calcium* |
34 | 6-sack | III | 1% Calcium* |
*ACI 332-14 permits the use of up to two percent calcium chloride by cementitious weight (one percent by water-soluble chloride ion), provided steel reinforcement is not required for structural performance. Steel reinforcement intended for temperature and shrinkage crack control, such as horizontal or re-entrant corner steel, is not considered structural by definition.
Each mix was tested in an uncovered wall segment as well as in a segment covered with a six-foot blanket capping the top (fig. 4). Wall forms were removed from all segments after 24 hours, as were the blankets of the covered walls. Both internal and ambient temperatures were monitored for the walls, as was a full set of test cylinders from each mix. Once the wall forms were removed, cores were taken and tested along with cylinders at 1, 2, 3, 7, 14 and 28 days. Conditions at placement were 26 F, with snowfall. The temperature remained below freezing for 21 days, with an average temperature in the low teens and a low temperature recording of -19 F. The opportunity to record the strength gain of the full-scale walls at such favorable research temperatures was an added bonus.
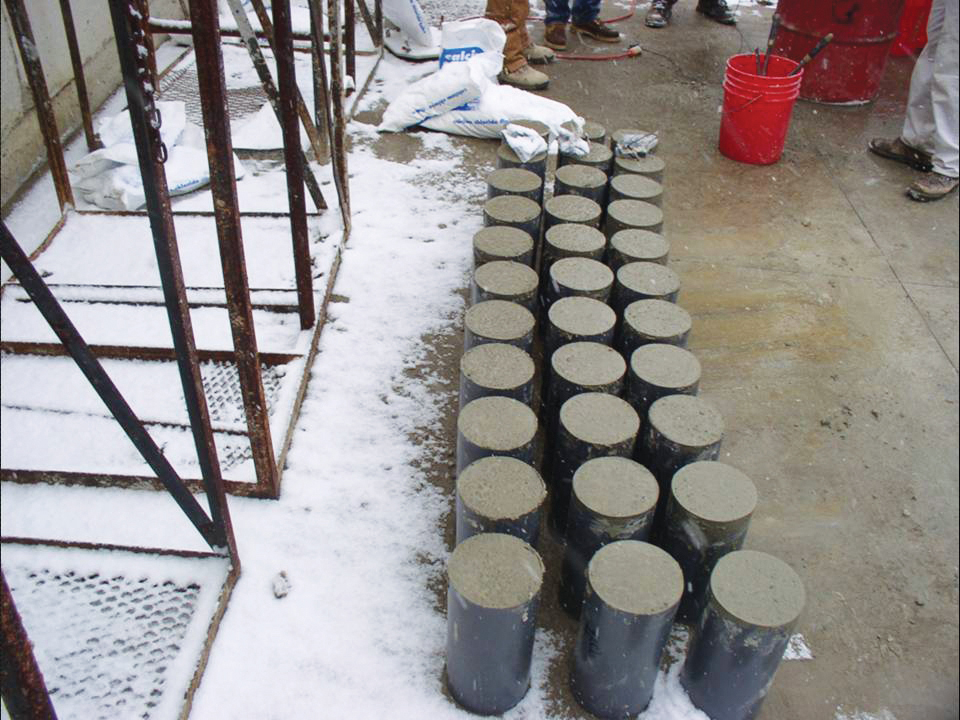
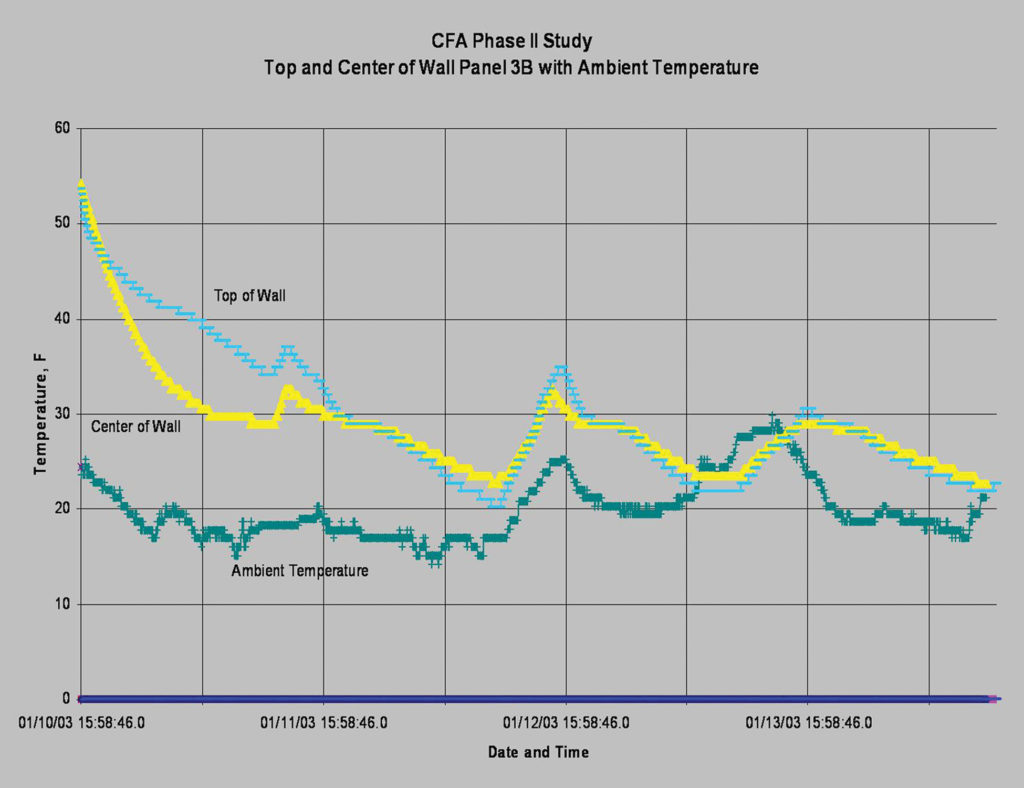
Phase III – Petrographic Testing
The final phase of the research project was petrographic examination of the cores taken from the field segments. Each mix type and location (covered versus uncovered for the first 24 hours) was subjected to petrography to determine the impact any freezing condition may have on the concrete. While there was definitive evidence that the range of mixes were affected by an initial set freezing, the typical freeze/thaw cycle that the samples were subjected to failed to produce continued deterioration. The behavior of all samples was such that the lab technician could not determine whether the samples were indicative of winter behavior or summer behavior.
Results from the Testing
The data resulting from the three-phase project reinforces the more generally applied ability to predict strength gains in concrete exposed to cold weather conditions. Additionally, the data supports the idea that concrete’s foundation-wall environment is naturally protected from the detrimental impact of freezing. Most importantly, the research evidenced that maturity resumes for concrete when internal temperatures rise above freezing.
There are many more results and recommendations established by this research effort. The research continues to inform practical, effective and intelligent decisions for professional foundation contractors throughout North America. It has made a significant impact in the industry, now referenced by ACI 332 (and, by reference, the IRC) and by the ACI 306 Guide to Cold Weather Concrete. Since its publication, ACI 306 is now in its third revision and no longer presents cold weather as requiring protection below 40 F. The guide presents a conversation about protection and a decision-making process that encompasses many of the research results validated through this project.
CFA now offers two important resources relative to this research. The first is a 72-page research report with complete details on the mix designs, each phase test parameters and the recorded performance from each component. It is available from the CFA through online resources or by contacting our headquarters. This research report has also become part of the technical resources that form the basis of the ACI/CFA Residential Foundation Technician Certification. A condensed technical reference sheet is also available as a great communication tool for the principal findings is publicly available from the CFA website under Resources and can influence the conversation as well as confirm some of the more frequent practices influenced by the research.
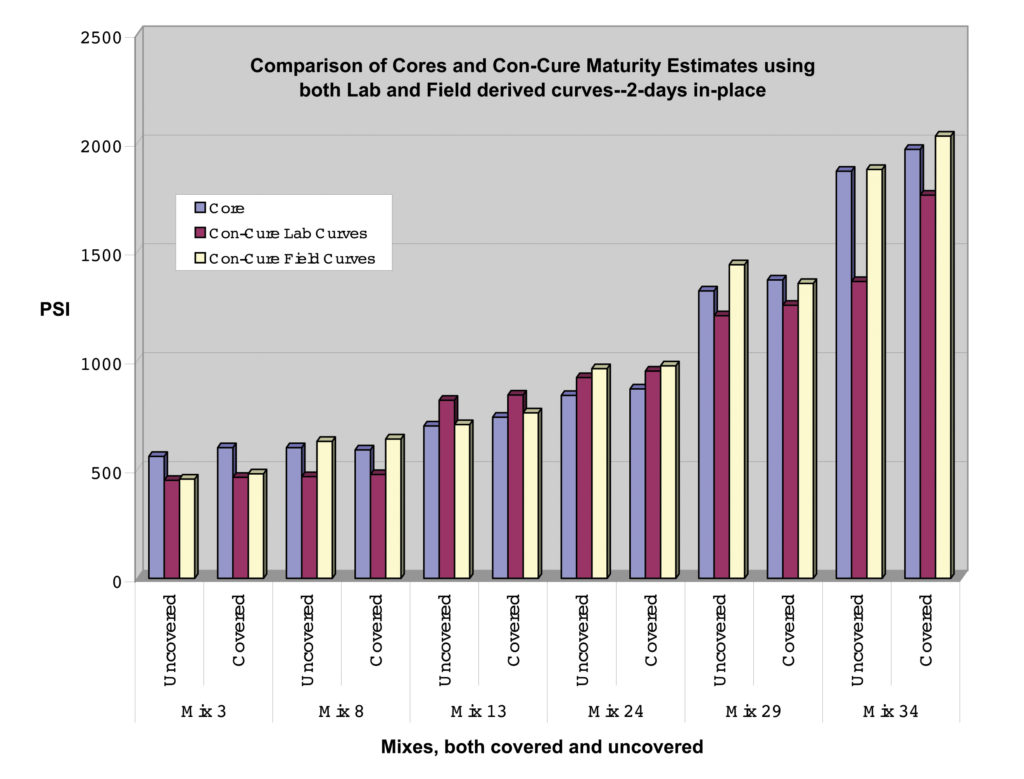
Determine What Is Next
Should you be interested in a more interactive discussion of these research findings, CFA members have access to a free online webinar held periodically throughout the year. Additionally, you can listen to a podcast that will soon be added to “Behind the Mic” – an audio-format discussion of great topics. Contact us for the details on the schedule, or visit our website for more information on registering for one of these.