Projects of the Year: Customer Challenges Deliver Award-Winning Results
CFA PROJECTS OF THE YEAR 2018:
Customer Challenges Deliver Award-Winning Results
This article features the Concrete Foundation Association’s Projects of the Year, the expanding industry recognition program that features high-quality concrete work that is all too soon, never seen again. Projects are submitted by member organizations in a variety of project categories and are reviewed by a panel of professionals from diverse backgrounds. The judges score projects based on established criteria, and from these scores they select categorical winners and honorable mentions. The program again evinces a growth of complexity, pride and interest with a record number of entries contributed. Each year, one project is labeled the Grand Project of the Year and is featured in Concrete Contractor magazine. Here, we present all winners across the broad spectrum of categories, demonstrating the breadth of work. Beginning as the “Basement from Hell,” the competition has grown in size and popularity with a new record number of entries for each of the past six years in a row. The key is getting started while you are building… After all, a picture is worth a thousand words.
A customer service and experience expert, Shep Hyken gave impactful advice about dealing with customers:
“The key is when a customer walks away, thinking ‘Wow, I love doing business with them, and I want to tell others about the experience.’”
When you think about a chance to interact on a project, to turn lines on paper into a three-dimensional reality – and even more importantly, to build a foundation that will serve as a framing of life – what is first and foremost in your mind? Is it profit; is it completion? Perhaps it is a volume-influenced reaction with little critical thinking. There is also a chance it could be related to keeping people busy, the headache of finding people to work, the additional stress or load on equipment and resources, and so on. However, find the company that considers each project as an opportunity to engage customers in a way that makes them their very best , and you will find the source of energy that is described time and time again by these successful projects.
Year after year, contractors respond to challenges by their customers (headaches to many, nightmares to some), and produce works of concrete superiority that become foundations for success. These are the companies that participate in the Projects of the Year; these are the entries that define the current trend of the industry; these are the leaders that challenge the status quo.
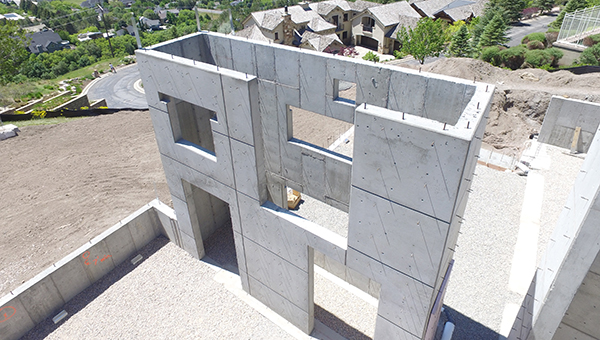
The Levy Residence, 2018 CFA Overall Grand Project of the Year by SCW Footings & Foundations, Inc., Salt Lake City, Utah.
Collecting the 2018 Grand Project of the Year
In the Spring of 2017, SCW Footings & Foundations of Salt Lake City, Utah completed construction on a project presenting quite unusual qualities when compared to traditional foundations seen across the landscape of both the CFA’s award programs and the traditional projects noted as single-family residential foundations. Where most concrete foundations simply establish a base for architecture, this project pulled the team of SCW into delivering architectural concrete that, in addition to providing the structure for the home, was made to be part of the visual aesthetic, with the skin and nuances many home owners today want from their home.
The project itself is not the ostentatious presentation of sheer size, volume and extreme contracting conditions that has been the moniker of this award program in years past. At just over 4,500 square feet (420 sq m) the project was sized among the more benign projects typically undertaken in the mountains and valleys of the lower Rockies. Yet, one is quick to take notice of this project after looking past the basic statistics. It features concrete walls that exceed 20 feet (6 m) with only a third of the total wall length less than 11 feet (3.4 m). These tall walls display a decorative concrete feature down the center of the floor plan, anchoring the foundation and the house itself into the landscape.
Submitting the project for the program, Dave Sheppard, project manager and estimator for SCW had this to say: “There aren’t many homes under 5,000 square feet that have these types of walls. Most noticeably, the feature that is a decorative concrete wall system down the middle of the home poured 20 feet and 6 inches (6.25 m) at its tallest point and spanned over 70 feet (21.3 m) from front to back.”
The SCW team describes a few unique and very intricate details that occur specifically in their notable wall. “The 4’ by 8’ (1.2m by 2.4m) smooth ply finish panels were showcased across all exposed faces of the wall,” states Sheppard. “These were outlined with chamfer strips and detailed with 18 faux cone tie holes in each panel. Overall, the finish covered nearly 1,600 square feet of wall.”
Companies that traditionally use manufactured handset forms for cast-in-place concrete foundations find a strong learning curve when they are given the challenge of producing a more contemporary, exposed concrete aesthetic like the snap-tie cone rhythm of a wall like this. When asked about their approach to this specialized aesthetic, Kirby Justesen, president of SCW Footings & Foundations, said, “Although we mostly form with aluminum panels, when we pour decorative concrete walls, whether that is board-form walls or traditional architectural walls with chamfer and cone ties, we use the Symon forming system. Symon forms allow us to more easily attach the boards or liners. Those boards can be wood planks, HDO plywood, or plastic/rubber liners. It just simply takes a lot more time to build and a lot more time to plan.”
SCW as a company has spent a lot of time experimenting with architectural concrete, as the Utah market has been trending toward a greater amount of the expressed concrete aesthetic in housing. “Over the years I developed an interest in decorative concrete and spent many years learning, discovering and trying new ways,” states Justesen. “This was mostly flatwork, counter tops, and vertical and horizontal overlays. It was during this time that I came to believe that the natural color of concrete is beautiful and gives the viewer a sense of strength and durable. About that time, we had architects drawing house plans with exposed concrete walls inside and out. The preferred choice was the board form look and to a lesser extent the traditional architectural walls with reveals and cone ties. I became very interested because it was a bit artsy and that appealed to me. We started learning how to pour the exposed walls with our regular production forms, Symon and Aluminum. We started with mockups that we poured in our yard so architects and owner could come and take a look. A bit to my surprise these exposed walls have really taken of in Utah. We now have two to four of these jobs going on continuously.”
SCW was recognized two years ago for another impressive feat of architectural concrete, involving the “board formed” appearance that has been very popular in the last ten years or so. The team at SCW is known throughout the region as the company contractors can turn to in order to mold concrete to fit the designer’s vision. Justesen believes it to be their attention to detail and craftsmanship that makes the difference. “This contractor was incredibly impressed with our portfolio found on our website (www.solidconcretewalls.com) and along with in-person site visits to other jobs, we were able to take them. We feel our architectural concrete is unmatched in the residential foundation industry in Utah, and we are fortunate with this opportunity that they agreed.”
But the challenge of a project like this, combining both size and complexity of the concrete work, does not come easy. Scheduling, Sheppard and Justesen believe, is an essential part of the success. Committing to such a project involves knowing it will require a crew that has perhaps the most experience and is larger than normal. While the standard residential foundation job is often characterized as a three-day project (given perfect conditions), the team at SCW know going into this type of a project that it will take weeks to complete. “Since projects like this can take weeks to complete, and we must be sure other jobs aren’t neglected because of them, we start by dedicating a project manager to the study of the project and pair him with a CAD draftsman in order to draw the details necessary to visualize the project from our perspective,” states Sheppard. “Architectural and even engineering plan sets just don’t deliver the detail we need,” says Justesen. “Therefore, our team redrafts the picture and details the wall heights, rebar schedules and step locations for our field crew so that they would not be hindered in any way.” This type of effort results in a completely new package of drawings that addresses each and every detail SCW will encounter on the project. All buck locations, panel sizes and locations, and every connection detail, are drawn fully to the satisfaction of the project manager before they get to the job site.
When asked how the company feels about the completion of this project and the recognition it now receives from the CFA Projects of the Year, Justesen offered, “These projects are fun to do and scary at the same time. We are always relieved when they turn out good. I love the look of durability and strength that exposed concrete walls have. When we have the chance to add a little artistry to our work it is enjoyable. When we receive industry recognition it is just icing on the cake.”
Known simply as the Levy Residence, this project was submitted in the category of single-family residence, 2,000 to 5,000 square feet. It was selected to be the signature project this year over 22 other projects, including nine projects weighing in at over 5,000 square feet.
Decorative Structural Concrete to Honor Heritage
Not every project seeking recognition needs to be a foundation. Every year, CFA seeks to celebrate the achievements of cast-in-place concrete from the breadth of the industry. Very near the site of the Concrete Foundations Convention 2017 stands the Demonbreun (pronounced “demon brun”) Street Bridge. It was designed to honor Nashville’s Railroad Heritage. While it opened in late October 2006, linking downtown Nashville with the midtown area, the project has only recently been uncovered by members of this Association as an example of the incredible artistry, ingenuity and craftsmanship that goes into modern cast-in-place concrete.
Located about 10 blocks from the Sheraton Downtown Grand where CFA hosted last year’s Convention, the bridge stretches nearly 774 feet across the gulch and CSX Railroad between 10th and 12th Avenue. It provides three lanes of traffic along with walkways for bikes and pedestrians. After spanning Nashville’s historic railroad gulch for nearly 75 years, the original structure was deteriorating and had to be closed in July 2004. The new $8.3 million viaduct includes unique architectural features that pay tribute to the city’s historic ties to the railroad and music industries. Scott System, a national associate member of the CFA, worked with Hawkins Partners landscape architects in Nashville, Tennessee to complete their vision of piers that resembled a locomotive engine. Other railroad motifs were also blended into the barrier walls and abutments. According to the landscape architect, Chris Whitis, “The ‘Context Sensitive Design’ factor of this project required the structure to incorporate elements of the immediate surroundings.” This translated into an artistic component inspired by the area’s railroad heritage. “The addition of the artistic piece that included custom form liners did not inflate the cost of the overall project,” Whitis said.
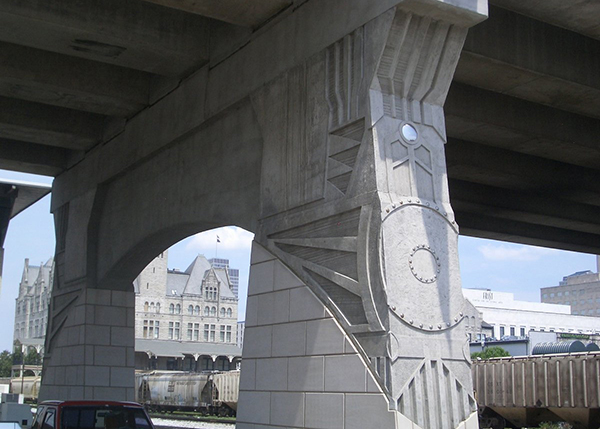
Demonbreun St. Viaduct, Nashville, TN. 2018 CFA Project of the Year for Non-Wall Structural Projects. Photo courtesy of Hawkins Partners Inc.
Scott Systems answered the Association-wide call for submittals to the 2018 competition once again after having received honorable mentions for a couple of years for work they had participated in. “In thinking about the awards program,” states Buck Scott, founder of Scott Systems, “I wanted to try and show something being done in concrete that has perhaps never been seen in old poured concrete.”
The tagline for Scott Systems is “The Art of Concrete Textures.” They have been involved in thousands of projects where patterning expressions in vertical concrete is desired and required. “We thought about the challenge from the architect and thought, ‘why not,’” said Scott. “So we produced an elastomeric liner to attach into the formwork. The result is stunning.” From the architects’ designs, employees at Scott System went to work developing the custom form liners made from urethane elastomer. They blocked the design using form shapes and incorporated various surface textures into their designs before producing the reverse image liner, a common approach to the complicated artistry they face regularly.
The art deco bridge serves as the major link between Nashville’s midtown and the new 2.1 million-square-foot Music City Center in downtown Nashville. The 300-foot-long bridge spans over the CSX railroad tracks. The project was completed five months ahead of schedule and was constructed under the project management of Bell & Associates of Brentwood, Tenn. The public works director, Billy Lynch, was quoted regarding the fast turn-around as saying it was, “a result of an unprecedented partnership between local and state governments and the fine work of TDOT’s contractor, Bell & Associates.” Add in the creative artistry produced by the liners produced by Scott Systems, and the result is clearly defining for the concrete industry and the 2018 Projects of the Year in the category of non-wall structural feature.
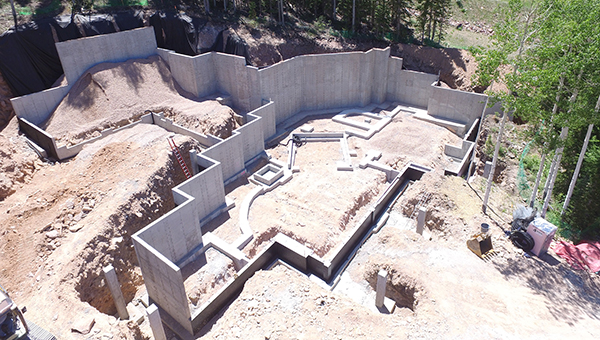
The Perrault Residence by SCW Footings & Foundations, Inc. of Salt Lake City, Utah. 2018 Project of the Year winner in the Over 5,000 sq.ft. project category.
The ‘Massive’ Foundation Still Impresses
Collecting a second award this year, SCW Footings & Foundations from Salt Lake City, Utah submitted the foundation known simply as the Perrault Residence with a footprint over13,000 square feet. Certainly, no stranger to large foundations (The Nowak Residence – 2016), the staff at SCW manages these projects knowing they have been involved because of their reputation.
“Many years ago, CFA brought in George Hadley as a guest speaker during the annual meeting we used to have during World of Concrete in Las Vegas,” states Justesen. “I learned that night probably the most important principle in subcontracting. It was this—you have three things to sell and they are; price, quality and timeliness. You can only ever deliver two…well, maybe in a recession you have to deliver three. My goal has always been to deliver quality and timeliness and to be the most progressive company willing to do the most difficult jobs, for a price. Many years of following this one principal is why I think we get a crack at biding all the largest residential homes found throughout these ski resorts along the Wasatch front.”
Reviewing the project photography, judges commented on how this job was filled with complexity. The team at SCW described how t was staged and poured in multiple phases, starting with the tallest, 28-foot retaining wall portion and ending with the shorter front 4-foot-tall walls. To achieve the strength and stability required for such tall walls, twelve separate 6-foot-long by nearly 25-foot-tall “deadmen” walls were added to the outside face to keep the wall plumb and true after backfilling. There were 70 corners throughout this job, adding complexity and time to the building process.
Concrete placement is not the only thing that makes these projects complex. The engineer identified over 20 base/embed plates throughout the job that were required to be cast into the footings and walls. “This is a very tedious task,” stated Shepherd. “We can’t have those misplaced or the future steel won’t fit properly.” In other words, what is cast in concrete is literally cast in stone, and the trades that followed them were relying on their accuracy to establish the success for the rest of the project.
The project location only further complicated the approach to the work. The Perrault Residence sits at the top of a mountain and has a beautiful view. SCW surveyed the approaches to the site using drones in order to have the best plan in place for getting concrete and pump trucks up there. Even with planning, however, getting the project set up properly was difficult.
All in all, they were successful. They began with 250 linear feet of 14-foot-wide by 24-inch-thick footings – that is 260 yards in one footing alone. “The terrain and changes in the footings were crazy on this project,” states Justesen. “They ranged from that thick all the way down to a typical 24-inch-wide continuous 12-foot footing. Perhaps the biggest elevation change we’ve faced, though. There was a total of 29 vertical feet between only five footing steps throughout this project.”
A Foundation Prepared for the Big Move
Not to be outdone by project scopes like that of “Big Dig,” Oklahoma is now the site of a massive cotton gin that was moved earlier this year from North Carolina. A machine of this magnitude requires a massive and complex foundation, and Basement Contractors of Oklahoma can fully describe the intricate details of matching a new foundation to an existing and functioning structure.
“The most complex part of this job was placing more than 1,000 anchors for the steel building and equipment,” states Mike Hancock, president for Basement Contractors. “The accuracy was stringent for the equipment to be re-used exactly as it was used in North Carolina, from where the cotton gin was being moved and had to be ready to go when it finally arrived.”
As if the anchors for all the equipment were not exacting enough, over the 38,500 square feet of concrete floor, the elevations needed to be perfect, so the equipment would fit together correctly. The main floor of the gin was raised three feet above the receiving floor, so the entire area was graded three feet up. The exterior was then cut down to place the footings and three-foot stem walls. “On a project of this size you cannot afford to be off fractions of an inch in elevations, as the result becomes inches of deviation at those heights and distances,” states Hancock. “Matching a grade in Oklahoma from a location halfway across the country to within one-fourth of an inch while matching each piece of equipment’s anchor bolt locations without the original plans was more than challenging.”
The footings stepped down at critical equipment locations for the cotton gin process. The equipment coming from North Carolina dictated the elevations that needed to be established in Oklahoma, with five separate elevations across the building pad. Mike Hancock added, “We just had to make sure and make the new construction match what the used equipment required.”
Entered in the category of agricultural projects, the Cotton Gin adds recognition for the broader spectrum of cast-in-place concrete projects by contractor members of the CFA. This project was massive and prescribed a tedious level of quality control to an industry that few might regard as having such attention detail. Flatwork and foundations alike challenged the extent of the experience this contractor had developed in building high-quality residential foundations and above-grade concrete homes.
The Challenge of Repetition
Although CFA contractors are traditionally known for their work on single-family residential foundations, an increasing trend seen throughout the Association is the delivery of high-quality foundations for a wide variety of multi-family and townhome structures. Commercial foundations in both scope and approach, these projects challenge the coordination and mobilization of the standard residential foundation contractor. Along with being challenging, these can be among the most profitable.
This year, chosen from an impressive amount of submissions (the most ever received in any one year), Purinton Builders (East Granby, Conn.) receives the Project of the Year award for Multi-Family Residential. “Ridge Road,” a project previously covered in Concrete Facts (Winter 2018), features a collaborative effort between Purinton and fellow CFA member, Bartley Corp (Silver Springs, Md.), to accommodate the exceptionally large project.
The 23,000-square-foot project required a schedule where one half of the footings, foundation walls and slabs were installed first, to permit the carpenters to begin. Then, the concrete work for the remaining half was completed while above-grade work proceeded. Having multiple trades on site added complications to the workflow; it was a project characteristic not often encountered by most cast-in-place concrete contractors on foundation projects.
“This project was extremely tedious and complex,” states Dennis Purinton, company president. “There were more than 1,300 anchor bolts on this project and we wet set only 600 of them. It was necessary to post-install many anchor bolts to ensure accuracy. It is a dedicated profit opportunity and we were able to do this using the dustless drilling system we have come to rely on. OSHA’s Silica Regulation has not been difficult for us to adapt to since moving to this system several years ago.”
Purinton Builders was suited for this project due to their quality control measures and their familiarity with a variety of added products. This foundation required 2,300 square feet of slab insulation, 560 linear feet of slab-edge thermal break and 23,000 square feet of Stego® vapor retarder. Also, in addition to the considerable number of anchor bolts, the team installed more than 400 linear feet of threaded rod for shear-wall hold-downs with 600 two-and-a-half-inch square washers for shear panels. The foundation schedule included 26 columns and pilasters, 2,500 linear feet of footings with haunches, and 8-foot by 14-foot by 24-inch interior pads with double-mat #9 rebar spaced at 12 inches on center in both directions.
Most recognizable on the Ridge Road project, however, was the 47-foot-tall cast-in-place elevator shaft. The requirements were that we could be no more than ½-inch out of square or no more than 1-inch out of plumb or the elevator would not fit. We complied with a 50% safety factor. The walls were eight inches thick with a double mat of #4 and #5 rebar spaced at 12 inches on center both horizontally and vertically. We used traditional aluminum formwork with an OSHA-compliant staging and guardrail system.
“Coordination, organization and collaboration, along with high-quality equipment,” states Purinton, “make jobs like this go very efficiently. The Ridge Road multi-family Project of the Year winner is yet another example of the breadth of concrete expertise and challenge-accepting confidence CFA contractors put forth.
An Architectural Parking Structure Challenge
Bartley Corporation (Silver Springs, Md.) is the 2018 recipient of the Project of the Year category winner for Commercial Structure. The 1 East Pratt Street Plaza project incorporates an impressive variety of cast-in-place concrete delivered with high quality. The company has long held to their market commitment to both residential and commercial concrete projects, and yet they found themselves challenged by the technical nature of this project.
“The real challenge for us on this project,” states Jim Bartley, president of Bartley Corp, “was the fact we weren’t working with a traditional starting point for us. This project required us to work from an existing elevated parking deck in the center of the Baltimore inner harbor to create access to a plaza level converted into additional surface parking.”
The supporting ramp walls were continually sloped to maintain structural support for the angle of the ramp. They also extended above the ramp to the existing plaza level where the new parking deck was to be created.
This project consisted of 15,885 square feet of topping slab, a 954-square-foot ramp, and 220 linear feet of ramp walls that ranged in height from 1 to 8 feet and had thicknesses of 8, 12 and 22 inches. A total of 465 yards of concrete was placed with 224 yards located in the ramp walls. A total of 15,000 pounds of steel reinforcement was required in the relatively small project.
When asked about the most challenging features for the project, Bartley said it had to be the several new cast-in-place concrete beams that spanned the ramp opening being created. He said, “One of these beams was nearly 24 feet long and had an L-shape that was over 3 feet tall and 2 feet wide at the base, 18 inches wide at the top. We also cast two others that were of the same length but had cross sections of 12-by-12 inches and 18-by-12 inches.”
The project success was one of breaking the composition down into manageable quality-control steps. The walls supporting the ramp slab were built to the required slope, and then a special forming system was rented for the elevated ramp slab deck. Next, the walls were extended to their full height above the ramp slab and beams were added. The system used to control the pace and process of this project led to an impressive, completed work.
Small Yet Mighty…Mighty Complex
While the big projects often deliver the wow factor in the annual consideration for Projects of the Year, the fact remains that “the devil is in the details,” and the small projects demonstrate the nuances and challenges met in every day contracting. This can certainly be said for this year’s recipient in the “Single-Family Foundation: Under 2,000 Square Foot” category, delivered by Custom Concrete (Westfield, Ind.), referred to as “Indian Lake.”
“For a project of only 1,500 square feet, this offered us a real challenge,” states Darin Hackman, VP of Residential Construction for Custom. “We had 67 yards of concrete in the walls but had seven steps for eight different wall heights ranging from 2 feet to 10 feet. We were stepping these walls every 3 feet along both sides.”
At just over 1,500 square feet, the project contained 387 linear feet of 8- and 11 ½-inch concrete walls. Along the sides of the house, pilasters were installed to give additional stability to the stepping wall structure. Perhaps the most unique feature of this small house foundation, however, is the nine-foot wall built at the back of the house, just to support the basement floor slab. “The house sits on a very steep hillside,” states Hackman. “The design required an 8-inch-by-9-foot tall wall just to get to basement floor grade. Coincidingly [sic], the garage walls we normally see at three feet in height were sloped from three to nine feet.”
To further demonstrate the severity of the site’s condition: a house of this size would normally require approximately 270 tons of gravel for the pad and fill. This house, however, required more than 730 tons of gravel, largely due to the 9-foot-tall rear frost wall condition.
In addition to the quality projects featured here as category winners and the Overall Grand Project of the Year, six additional projects received Honorable Mention this year. These Honorable Mentions include Summit at Lost Mountain (Herbert Construction Company, Marietta, Ga.), Freshwater Lane (Doggett Concrete Inc., Charlotte, N.C.), Lake House (Basement Contractors, Edmond, Okla.) and DKM (Custom Concrete, Westfield, Ind.), all projects from the single family, over 5,000 square feet category as well as Doyle Residence (SCW Footings & Foundations, Salt Lake City, Utah) and Waterford (Michel Concrete, Springfield, Ill.) from the single-family residence, 2,000 – 5,000 square feet.
More photos of these projects can be seen under “Association Awards” through the “Recognition” section of the CFA’s website, www.cfaconcretepros.org, along with archives of the annual project award recipients.