UNDERSTANDING PYRRHOTITE IN CONCRETE
by James Baty, Gary Ehrlich, Jamie Farny, Don Penepent, and Dennis Purinton
Concrete, the most widely used construction material in the world, is a complex matrix of materials that transforms into a reliable structural product. With so many variables—different ingredients, different performance requirements, varying exposures—specifiers are faced with many choices when designing durable concrete mixtures for the long term. Occasionally, concrete durability issues can arise when the structure is put into use.
One such issue has been making headlines since at least 2010 in the state of Connecticut, pertaining to an expansive reaction of a specific, identifiable aggregate. A decade earlier, similar issues were identified in Quebec, and documented cases have occurred in many European countries. This article presents information surrounding the expansive reaction related to an iron-sulfide-containing aggregate called pyrrhotite.
Pyrrhotite is the suspected cause of concrete durability issues found in the northeast U.S. (Conn.), primarily used for residential foundations. The foundations of interest are experiencing a slow crack development, resulting in the eventual loss of concrete strength. The problems, sometimes exhibiting themselves within the first 10 years, often begin to show after 15 to 20 years or longer. Presently, the only known repair for the damaged foundations is removal and replacement of the affected concrete.
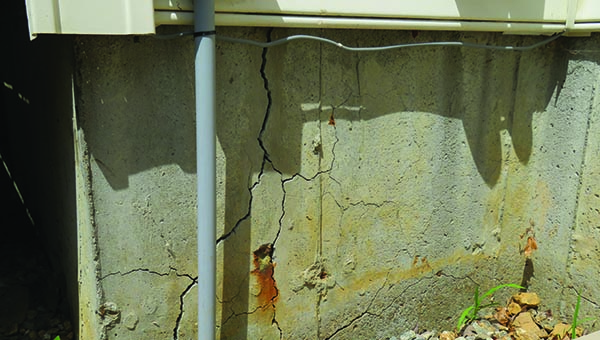
Figure 1. Typical cracking of pyrrhotite aggregate-affected concrete of a house foundation in Connecticut. Image courtesy of Michael Thomas.
For many reasons, the number of homes affected is unclear, but the problem has only been identified in four of the eight counties in Connecticut and in the Trois Rivieres area of Quebec, Canada. Homeowners in these areas are concerned and looking for assistance. Several concrete industry professionals are studying the issue to develop appropriate guidance. Meeting during conventions of the American Concrete Institute (ACI), participants from several committees impacted by the issue and research organizations offer their extensive knowledge of concrete and background in production and construction of these systems. Together they are well suited to adding some understanding to this issue.
As of spring 2017, two ACI committees—201, Durability of Concrete and 332, Residential Concrete Work—have agreed to look at the pyrrhotite issue in concrete. Not only is it important to make the industry aware of the issue, but it is also necessary to keep misinformation in check. ACI 201 has established a task group to study the issue and has been approved by the Institute to write a tech note, but that is expected to take some time to work its way through the committee process. In the meantime, this article is offered by representatives of the Portland Cement Association, the Concrete Foundations Association, the National Ready Mix Concrete Association, and the National Association of Home Builders, as these are some of the industry groups affected by this phenomenon. The article is intended to raise awareness of this durability issue by describing materials, exposure conditions, deterioration, and other countries’ experience with the problem, and by presenting the current best practices that can help prevent future occurrences of such pyrrhotite aggregate reaction.
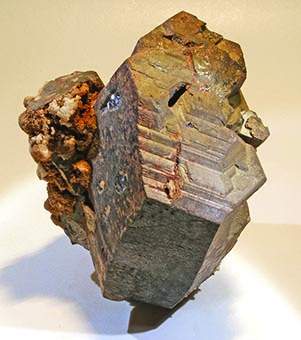
Figure 2. Pyrrhotite aggregate.
What Is the Pyrrhotite Aggregate?
The deteriorating foundations are associated with a quarried rock that contains a mineral called pyrrhotite (Figure 2). Pyrrhotite is the second most common iron sulfide in nature, and it is found associated with pyrite, marcasite, magnetite, and chalcopyrite (CSA 2014). Even so, aggregate that contains pyrrhotite, an unstable form of iron sulfide (Fe[1-x]S), in quantities that are able to be disruptive to concrete does not appear to be very common.
In Connecticut, this aggregate came from a specific quarry and was used in concrete supplied from one producer starting in the late 1980s and continuing until 2015. In Canada, the aggregate came from two quarries in Quebec. For various reasons, aggregate sources are not normally evaluated for pyrrhotite. Furthermore, as will be demonstrated in this article, identifying this aggregate may require that specialized testing be developed.
At this time, it is not yet known if testing all aggregate supplies for this sulfide mineral is necessary. Quarry owners, aggregate producers, ready mixed concrete producers, and others, whether in the affected areas or elsewhere, are rightly interested in making sure that any recommendations that are made about this issue be based on good science. Until it is understood exactly how much pyrrhotite causes problems, avoiding it entirely seems to be warranted. But identifying its occurrence in aggregate materials is itself fraught with difficulty. Some have said it is a bit like looking for a needle in a haystack. That places more of a burden on developing identification tests, because it is not possible to test every single piece of aggregate, so some representative portion of it must serve as a proxy for the entire source. Those researching this issue agree that if testing is to be done, the required tests must be practical as well as effective for industry and consumers to have confidence in them.
Production of Concrete – The Constituents
People familiar with concrete know that it contains a limited number of materials: fine and coarse aggregates, cementitious material(s), water, and, usually, admixtures. Most concrete is produced with potable water. Cementitious materials include portland cement, blended cement, hydraulic cement, and other supplementary cementitious materials, such as fly ash and slag, the two most common. Admixtures commonly used include air-entrainers, water reducers, set retarders, and set accelerators.
Fine and coarse aggregates comprise the largest portion of concrete, commonly 60 percent to 75 percent by volume. It is in the coarse aggregates that pyrrhotite is most concerning in regard to durability.
Reactive Aggregates in Concrete
Pyrrhotite expansion can be considered an aggregate durability issue (CSA 2014). The pyrrhotite particles in coarse aggregate are unstable in oxidizing conditions. Although the mechanism(s) of deterioration are not completely understood, the following summary appears to be supported: When exposed to water and oxygen, the sulfide minerals oxidize to form acidic-, iron-, and sulfate-rich by-products (CSA 2014). One of these products is sulfuric acid, which results in an acid attack on (primarily the portlandite in) the cement paste, weakening the paste, with sulfates as a by-product. These sulfates react with portlandite and hydrated aluminate phases in the paste, resulting in expansion, as happens in classical sulfate attack.
Deterioration typically consists of expansion, map cracking, popouts, white rims surrounding the aggregate particles, and yellowish discoloration near the cracks. In some cases, affected concrete can become so friable that it can almost be removed by hand (Rodrigues et al 2016). Although some of the basic deterioration mechanism seems to be known, this remains a relatively uncommon problem. Therefore, several aspects of this reaction need to be further observed in order to be better understood and be able to provide adequate guidance.
Canadian, European, and Other Countries’ Experience
The Canadian industry has been working on the pyrrhotite in concrete issue for many years, and CSA A23.1 provides some guidance. Annex P (non-mandatory) recommends that new and unproven sources of concrete aggregate be tested for sulfur content (CSA 2014). They note that many aggregates contain small amounts of sulfides, so it would be unrealistic to set a limit of 0.1 percent for sulfur content. That is why it may be more feasible to follow what the European standards recommend for aggregates—a recommendation developed over several decades, as reported by Rodrigues et al. (2016):
- France originally adopted a 1 percent sulfate (SO3) limit, with a max 0.4 percent sulfur (S).
- The broader European standards specify 1 percent S by mass for aggregates other than air-cooled blast furnace slag, or 2 percent S by mass of S for air-cooled blast furnace slag.
- 1 percent S limit for aggregates proven to contain pyrrhotite.
At present, there is no accelerated physical test method to assess the potential for expansion of concrete due to the oxidation of iron sulfides, but Canadian researchers have been working on a performance test that is based on an oxygen consumption test used to evaluate sulfide mineral content in mine tailings (Mbonimpa et al. 2011).
Foundation Exposure
Walls for residential foundations may be partially or completely below ground. It is this type of exposure that provides adequate moisture and oxygen for this durability issue to be of concern when some (or a significant quantity of) pyrrhotite is present in the aggregate. It is the “safe” level that is still not known with certainty. Below-grade exposures are susceptible to damage because the ground moisture is regularly present below grade and residential concrete, when unregulated, can have a higher water-cementitious ratio than many other types of concrete construction. Concrete with a higher water-cementitious ratio, which is more permeable, allows for easier ingress of moisture and oxygen. This was confirmed by Canadian research in the 1970s by Berard et al., who found that concrete with a lower cement content deteriorated more quickly than concrete of higher cement content or lower water-cement ratio.
After prolonged exposure to oxygen and moisture, pyrrhotite reacts to create secondary minerals that can cause expansion. The aggregate basically rusts, and two expansive sulfate products are formed (gypsum and ettringite). Because concrete has a much lower tensile strength than compressive strength (about 10 percent), typical residential concrete of 2,500–4,000 psi (17–28 MPa) compressive strength would only have a tensile strength on the order of 250–400 psi (about 1.7–2.8 MPa). As such, it does not have a lot of capacity to resist tensile forces caused by the expansive mechanisms. The reaction also produces iron oxides, which may contribute to expansive stresses.
Another study on deterioration found that the type of aggregate and the permeability of the concrete play a role in the rate of oxidation of iron sulfides, and that the high pH of concrete increases the oxidation rate (Divet 1996, Divet and Davy 1996).
More needs to be learned about the deterioration mechanism before specific guidance can be provided. It is not yet clear if the concrete itself contains enough water for the reaction to proceed if good waterproofing materials are applied properly, but limiting the amount of ground moisture that can infiltrate the concrete is certainly good practice. Low permeability concrete can be achieved with lower w/cm and use of supplementary cementitious materials.
Long-Term Durability of Concrete
Damage occurs at a faster rate in lower quality concrete, but even better-quality concrete that contains pyrrhotite is likely to be susceptible to this deterioration, given enough time and the proper conditions. As noted earlier, the concrete may start to show signs of deterioration within a few years, or it may take more than 10 or 15 years to start exhibiting problems. For these reasons, avoiding the susceptible aggregate is the current recommended best practice to assure concrete durability.
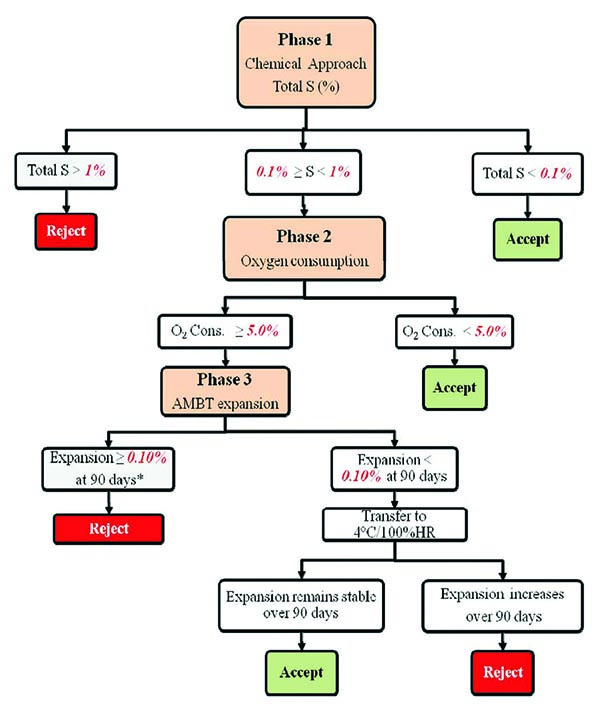
Fig. 3—Proposed protocol for determining potential reactivity of iron sulfide bearing aggregates. Numbers in italics represent limit values that still need to be validated through testing of wider range of aggregate materials. (*Cause of excessive expansion—that is, ASR and/or oxidation of sulfide minerals—should be addressed before rejecting aggregate.) (Rodrigues et al 2016)
Conclusions
Although this phenomenon appears to be geographically limited, there are potentially large numbers of homes already affected or at risk of developing this durability problem. Remediation of affected concrete does not seem to be an option, at least not for the most severe occurrences of pyrrhotite expansion. In those cases, the only solution to the problem is removal and replacement of the foundation with new concrete that does not contain pyrrhotite aggregate.
In addition to understanding how to remediate affected basements, it may also be necessary to institute appropriate aggregate testing procedures. It still is not known if testing will be recommended only in areas that are known to have this type of aggregate in their quarries or if it will include other areas.
Researchers continue to study the problem to understand it. As more is known about it, educating the concrete industry will become more important, from increasing awareness to explaining the preferred approaches for lessening the potential for future occurrences of the issue.
About the Authors
James R. Baty II, FACI, is executive director for the Concrete Foundations Association, representing a professional network of contractors, engineers, builders and ready mix suppliers engaged in the residential foundation industry across North America. He can be reached at 319-895-6940 or by email at jbaty@cfaconcretepros.org.
Gary Ehrlich is a director of codes and standards for the National Association of Home Builders, which strives to protect the American Dream of housing opportunities for all. He works to achieve professional success for members who build communities, create jobs and strengthen our economy. He can be reached at 202-266-8545 or by email at gehrlich@nahb.org.
Jamie Farny is the director of building marketing for the Portland Cement Association, which is dedicated to improving and extending the uses of portland cement and concrete in the United States through market development, engineering, research, education, and public affairs work. He can reached at 847-972-9172 or by email at jfarny@cement.org.
Don Penepent is the Ready Mix Division Manager for Tilcon Connecticut, Inc (an Oldcastle Company). He has been managing concrete operations and designing mixes for various applications for over 40 years. He can be reached at 860-612-5104 or by email at dpenepent@tilcon-inc.com.
Dennis Purinton is president of Purinton Builders of East Granby, Conn. and current president of the Concrete Foundations Association. His company has been installing residential and commercial foundations for 35 years. He is an active member of ACI 332, 306, and 655 committees. He can be reached at 860-670-1791 or by email at purintonbuilders@yahoo.com.
The authors would like to thank several individuals who reviewed this article:
Michael Thomas, professor of civil engineering at the University of New Brunswick, Fredericton, NB, Canada
Paul Tennis, director of product standards and technology at Portland Cement Association
Benoit Fournier, associate professor, Department of Geology and Geological Engineering at the University of Laval, Quebec City, QC, Canada
References
Berard, J., R. Roux and M. Durand. “Performance of concrete containing a variety of black shale.” Canadian Journal of Civil Engineering, vol. 2, 1975. pp. 58–65.
CSA 2014. Concrete materials and methods of concrete construction/Test methods and standard practices for concrete – Annex P Impact of sulphides in concrete aggregate on concrete behavior. CSA A23.1-14, CSA Group, Aug. 2014.
Divet, L. “Activité sulfatique dans les bétons consécutive à l’oxydation des pyrites continues dans les granulats: Synthèse bibliographique.” Bulletin des Laboratoires des Ponts et Chaussées, vol. 201, 1996. pp. 45–63.
Divet, L., J-P. Davy. “Étude des risques d’oxydation de la pyrite dans le milieu basique du béton.” Bulletin des Laboratoires des Ponts et Chaussées, vol. 204, 1996. pp. 97–107.
Mbonimpa, M., M. Aubertin, and B. Bussiere. “Oxygen consumption test to evaluate the diffusive flux into reactive tailings: interpretation and numerical assessment.” Canadian Geotechnical Journal, vol. 48, 2011. pp. 878–890.
Rodrigues, A., J. Duchesne, B. Fournier, B. Durand, M. H. Shehata, and P. Rivard. “Evaluation Protocol for Concrete Aggregates Containing Iron Sulfide Minerals.” ACI Materials Journal, vol. 113, no. 3, 2016.
With so many variables different ingredients, different performance requirements, specifiers are faced with many choices when designing durable concrete http://concrete.com/