Twisted Steel Micro-Rebar in Load-Carrying Concrete Walls
by Samhar Hoz, Jeff Novak, Luke Pinkerton
Concrete walls are widely used in building construction. Concrete is strong in compression; however, its tensile strength is only 8 to 15 percent of the compressive strength. Thus, plain concrete does not have good tensile properties. Cracks can develop due to loads, restrained shrinkage, or temperature changes that give rise to tensile stresses in excess of the concrete tensile strength.
Historically, many walls have been constructed of plain concrete. Modern codes, however, only allow plain concrete walls to be used in limited circumstances, where the walls are inherently stable. Design provisions for plain concrete are found in ACI 318-14 (1) and ACI 332-14 (2).
Reinforced walls are designed according to ACI 332-14 using rebar to increase their structural capacity. The minimum wall reinforcement required by ACI 332 is provided primarily for control of cracking and temperature stresses. Also, the minimum vertical wall reinforcement required by ACI 332 increases the strength of a wall. However, most wall designs provide standard diameter bars that are widely distributed and only carry load effectively after the concrete has cracked.
An alternative way to reinforce concrete walls is by using twisted steel micro-rebar (TSMR). TSMR reinforced concrete refers to concrete reinforced with short, randomly oriented twisted steel filaments. TSMR is fully anchored in concrete using continuous twisted rib deformations along the length of the shaft, similar to rebar. Because this type of reinforcement is distributed throughout the matrix and is fully anchored, it carries load both before and after the concrete develops cracks. In addition to its load-carrying capacity, TSMR provides redistribution of loads, potential reduction in crack widths, and increased durability of the finished structure. The degree to which these benefits are realized depends on the amount of TSMR added to the concrete mix. The mechanisms of how TSMR provides these benefits and how TSMR reinforced concrete can be used in practices is the subject of this paper.
The International Residential Code (IRC) governs the construction of walls used in residential structures (2). This building code basically references ACI 332 or ACI 318 (3) for the design of concrete structures. Although TSMR is not referenced in the IRC, the code does allow the use of alternative products as long as they undergo a detailed review process. The alternate means of code compliance (AMC) provision is in Section 104.11 of the 2015 IRC.
R104.11 Alternative materials, design and methods of construction and equipment. The provisions of this code are not intended to prevent the installation of any material or to prohibit any design or method of construction not specifically prescribed by this code, provided that any such alternative has been approved. An alternative material, design or method of construction shall be approved where the building official finds that the proposed design is satisfactory and complies with the intent of the provisions of this code, and that the material, method or work offered is, for the purpose intended, not less than the equivalent of that prescribed in this code. Compliance with the specific performance-based provisions of the International Codes shall be an alternative to the specific requirements of this code. Where the alternative material, design or method of construction is not approved, the building official shall respond in writing, stating the reasons why the alternative was not approved.
Evaluation reports (ERs), sometimes called code reports, are based on acceptance criteria (AC) or evaluation criteria (EC) and have been used by the construction industry for many decades. They are used to help assess a product’s code compliance through the code’s specified AMC provision and are typically used for products or systems not addressed in the code. They are also provided to help the building official and design professional determine if products or systems meet the prescriptive requirements and/or intent of the code. ERs have facilitated the use of new, innovative products through an evolving review and implementation process. They have also been used for products that are covered by the code as well as for times when there is some ambiguity in the code provisions. ERs have become a tool to facilitate, expedite and, in some cases, improve the design, building permit, construction, inspection and quality confirmation processes.
Helix TSMR received a Uniform-ES code approved evaluation report ER-0279 (4) in 2013, which states that Helix TSMR can be used as primary concrete reinforcement for structural applications.
TSMR Mechanism
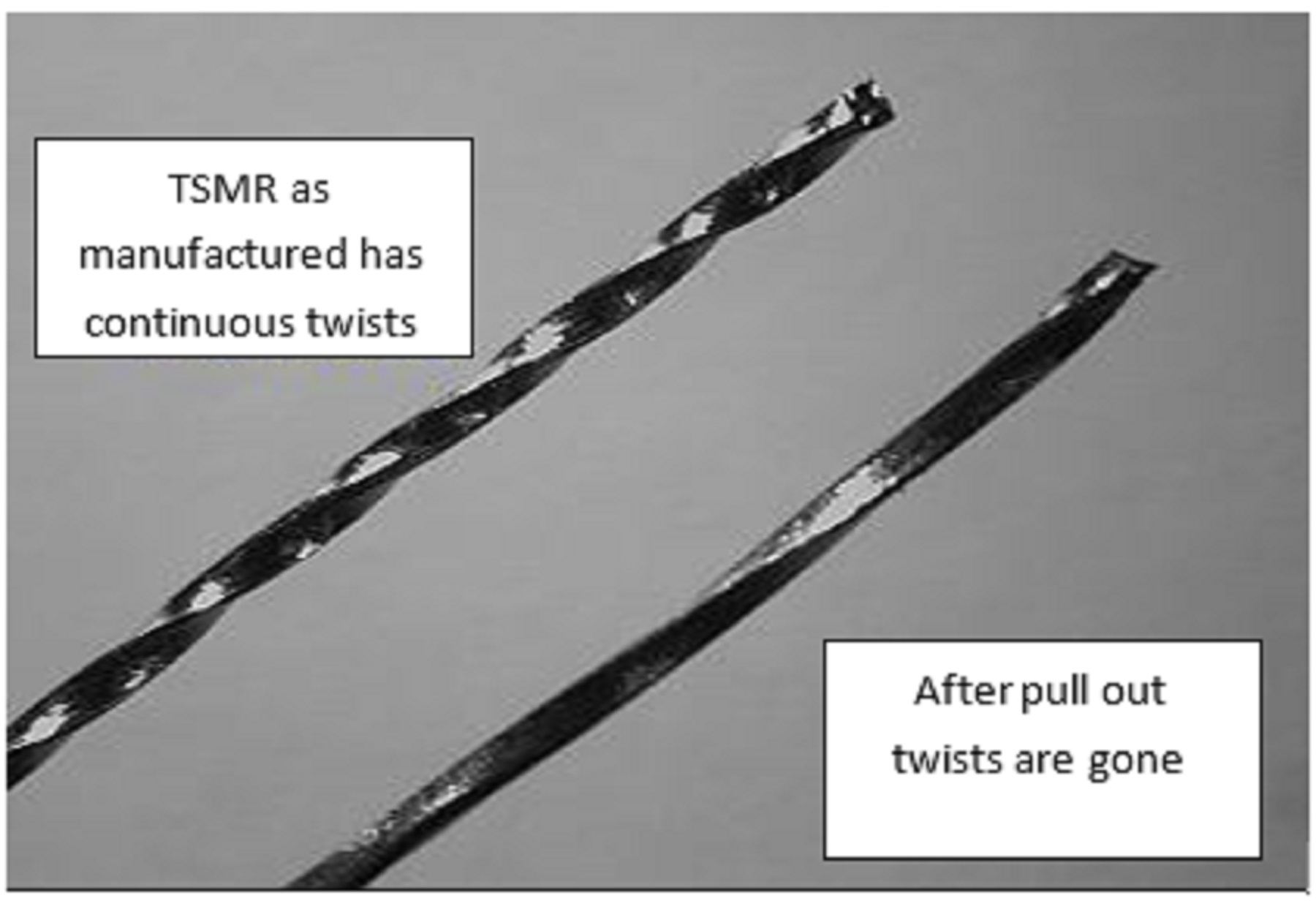
Figure 1: TSMR pullout behavior.
TSMR is an engineered product that substantially reduces the formation of cracks by increasing the tensile strain capacity of the concrete. This reduction or elimination of cracks optimizes the concrete’s durability. TSMR pieces are uniformly distributed, providing effective three-dimensional reinforcement.
As the concrete hardens and shrinks, microscopic cracks develop. TSMR intersects these micro-cracks, preventing them from developing into macro-cracks and potential problems. Today, the designer and contractor do not have to settle for the rebar or wire mesh method and gamble on it being in the right place. Technology has developed TSMR, a far superior system of engineered reinforcement that provides automatic high-tech crack protection in the concrete’s hardened state.
The Helix brand TSMR has a square cross section and is produced to have a twisted profile that allows each piece to bond to the matrix over its full length. Helix 5-25 TSMR is made from 1,700 MPa (246 ksi) minimum high tensile strength steel, which is similar to that used in pre-stressing cables. It is 25 mm (1.00 in.) long and 0.50 mm (0.02 in.) in diameter, and there are 25,307 fibers/kg (11,500 fibers/lb).
The untwisting of TSMR as it pulls out of concrete produces behavior that is significantly different than traditional steel fibers: pullout is governed by twisting resistance rather than friction. In addition, the twist anchorage allows for efficient tensile stress redistribution within the concrete prior to concrete cracking. The result is a significant increase in the concrete’s strain capacity and proactive pre-crack properties. After the formation of a crack, the tensile stress remains constant as untwisting occurs, providing reactive post-crack properties (4).
Figure 1 shows TSMR as manufactured (left) and after a pull-out test (right). The left or upper, unused piece shows a consistent helical twist along the full length. Those twists allow the entirety of each piece to bond with the concrete, bridge micro cracks and carry loads at a lower strain. The right or lower piece shows that in order to be pulled out of the concrete, TSMR must untwist, which produces a constant tensile strain resistance.
Tensile resistance is the primary engineering feature to pay attention to in the design of TSMR reinforced concrete. While beam tests have been the traditional way to evaluate fiber-reinforced concrete, flexural stress must be calculated using the section properties for the uncracked section. Because the stresses in a beam vary at different depths (both before and after cracking), the flexural test does not adequately measure the tensile performance of micro-reinforced concrete.
Evaluation criteria EC-015 established a direct tension method to characterize TSMR (6). Direct tension tests are used to determine the load capacity of individual TSMRs using a cylindrical tensile test specimen. The design methodology uses this tension response data to compute a tensile resistance stress that is related to a particular dosage rate of TSMR in concrete.
TSMR Construction Advantages
The difference between a wall built with TSMR (B) and a wall built with rebar (A) is illustrated in Figure 2. The conventional approach with rebar reinforcement does not behave as a true composite since concrete must crack before the reinforcement becomes active (4).
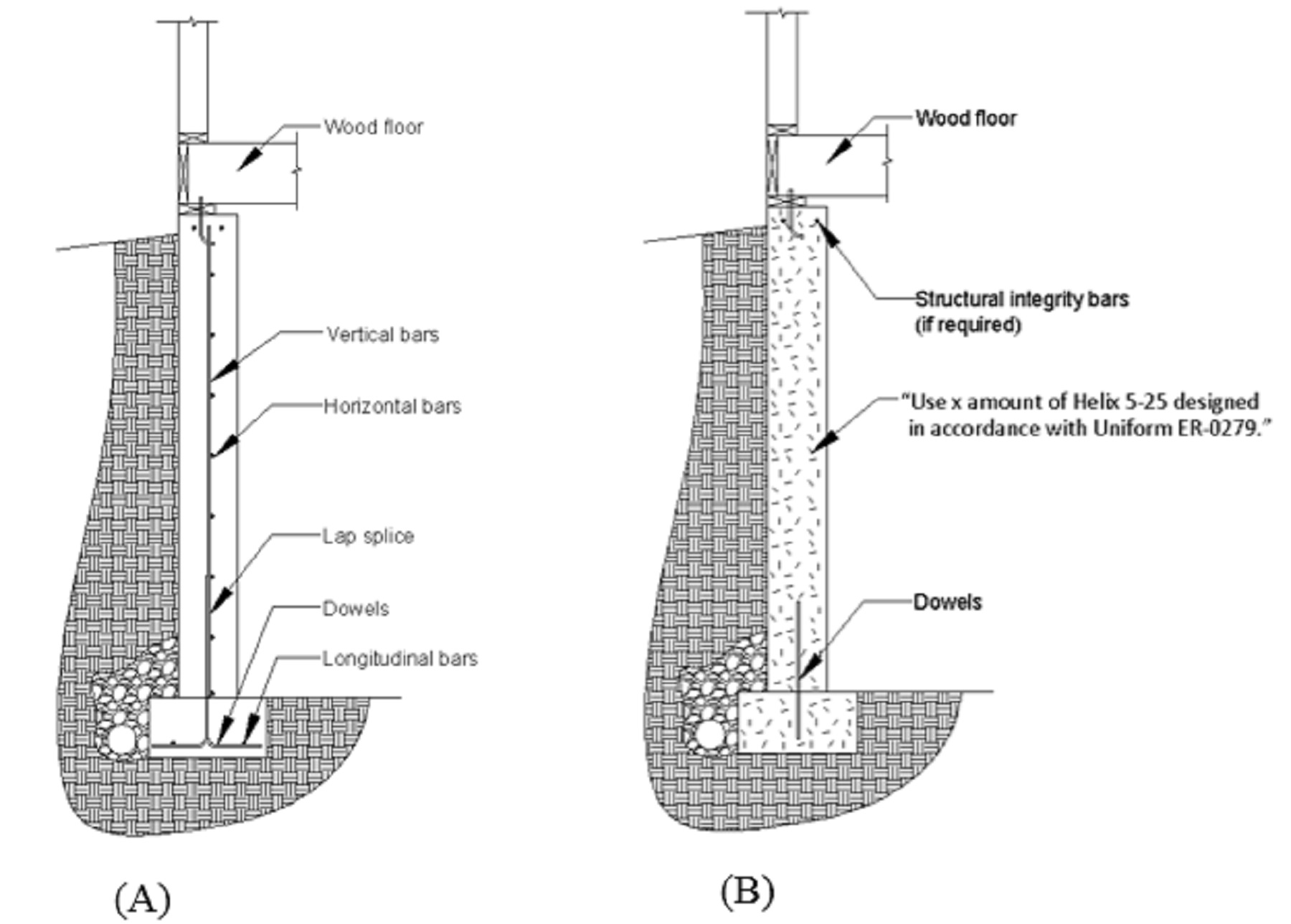
Figure 2. Concrete wall reinforcement with conventional rebar and TSMR
The purchase, delivery, cutting, bending and tying of rebar and mesh is time-consuming and costly. Placing the reinforcement at the specified depth is a critical step since the wall’s strength is decreased greatly when it is misplaced.
Building with TSMR eliminates placing errors since it is distributed throughout the concrete. Generally, TSMR is delivered to the job site already mixed in the concrete truck (Figure 3). The dosage of TSMR added to the mix should be noted on the batch ticket.
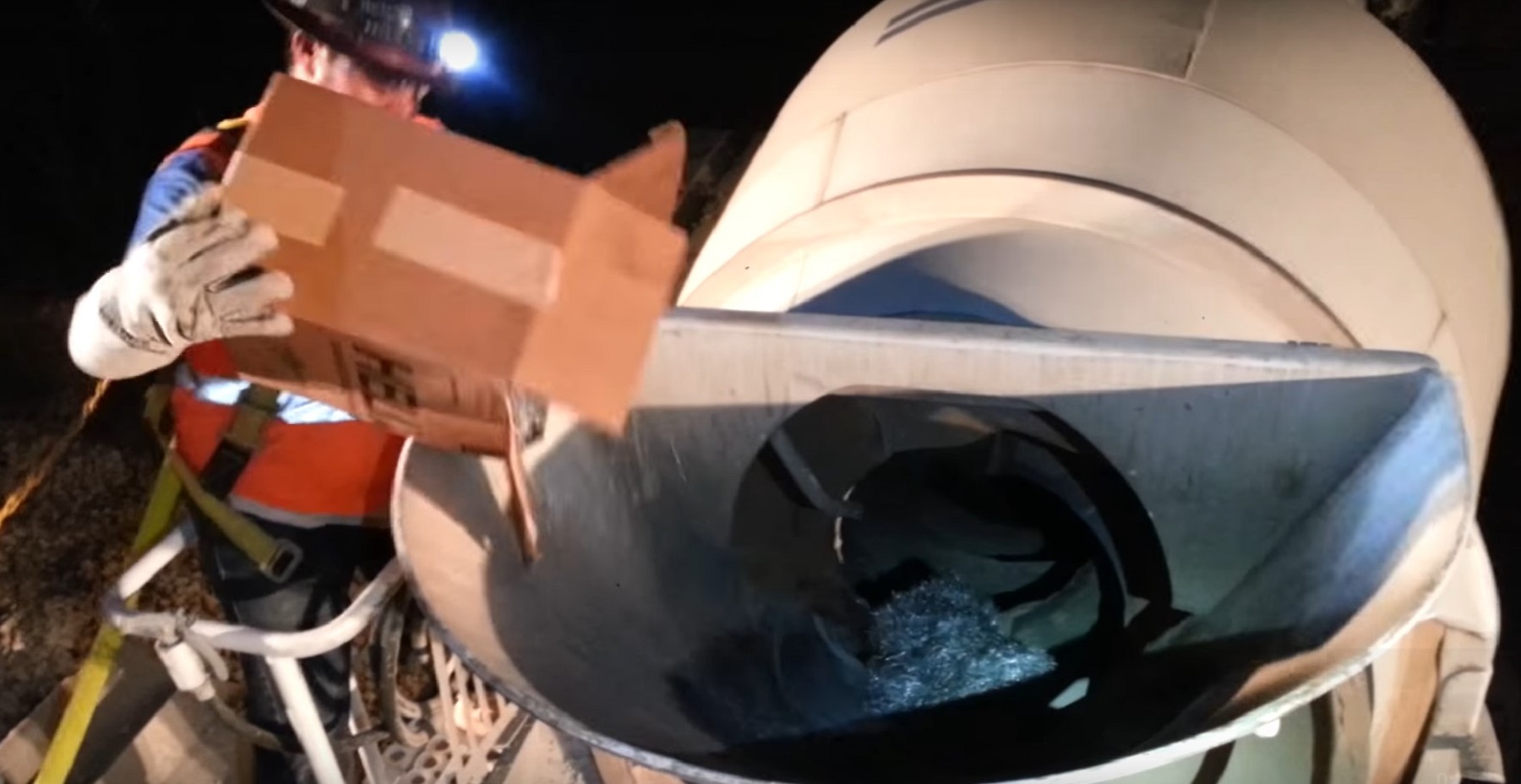
Figure 2. Mixing TSMR in concrete truck at job site.
Using TSMR reinforced concrete maximizes the speed and efficiency of construction. It also increases worksite safety by reducing injuries due to cuts (placing), strains (lifting), and tripping/falling (maneuvering on top of rebar) that are traditionally associated with rebar and mesh.
Wall Applications
TSMR has been used in concrete projects globally, with approvals in 99 countries. It has been used to replace reinforcement in above- and below-grade commercial and residential walls. Table 1 shows representative commercial wall projects. These projects illustrate the breadth of applications. The projects range from single-story houses to 25-story buildings. Too numerous to list, TSMR has also been used in thousands of residential projects in above- and below-grade foundation walls.
Table 1. Representative TSMR Commercial & Residential Wall Projects |
||||
Year |
Project |
Building type |
Wall thickness |
TSMR wall design |
2006-2016 |
The Villages Development
|
Over 8,000 single-story houses |
6 inches |
Full replacement of rebar
|
2006 |
Fairmont Village
|
3-story townhomes |
6 inches |
Full replacement of rebar
|
2008 |
St. Margaret Mary CatholicChurch
|
6-story church |
6-8 inches |
Partial replacement of rebar
|
2009 |
Holliday Inn Express
|
4-story hotel |
6 inches |
Full replacement of rebar
|
2012 |
12th Avenue Apartments
|
5-story apartments |
4, 6 & 8 inches |
Full replacement of rebar
|
2012 |
Pensmore Estate
|
5-story residence |
8 & 10 inches |
Partial replacement of rebar
|
2015 |
University of Waterloo
|
25-story dormitory |
10 inches |
Replaced one layer of rebar
|
2016 |
Hilton Garden Inn
|
5-story hotel |
4 & 6 inches |
Replaced horizontal rebar
|
2016 |
Indigo Green Apartments
|
Multiple 3-story apartments |
6 & 7 inches |
Replaced horizontal and reduced vertical rebar
|
2017 |
Hilton Garden Inn
|
5-story hotel |
4 & 6 inches |
Replaced horizontal rebar
|
2016 |
Helio Apartment Melbourne, Victoria, Australia |
16-story apartments |
6 inches |
Partial replacement of rebar
|
Carew Residence, Appleton, Wisconsin
At 13,200 square feet, the Carew home is anything but typical. In addition to living areas, the residence has a 34-foot-long indoor swimming pool, a full-size basketball court, a theater, wine cellar, and oval office with spectacular views of nearby Appleton, Wisconsin.
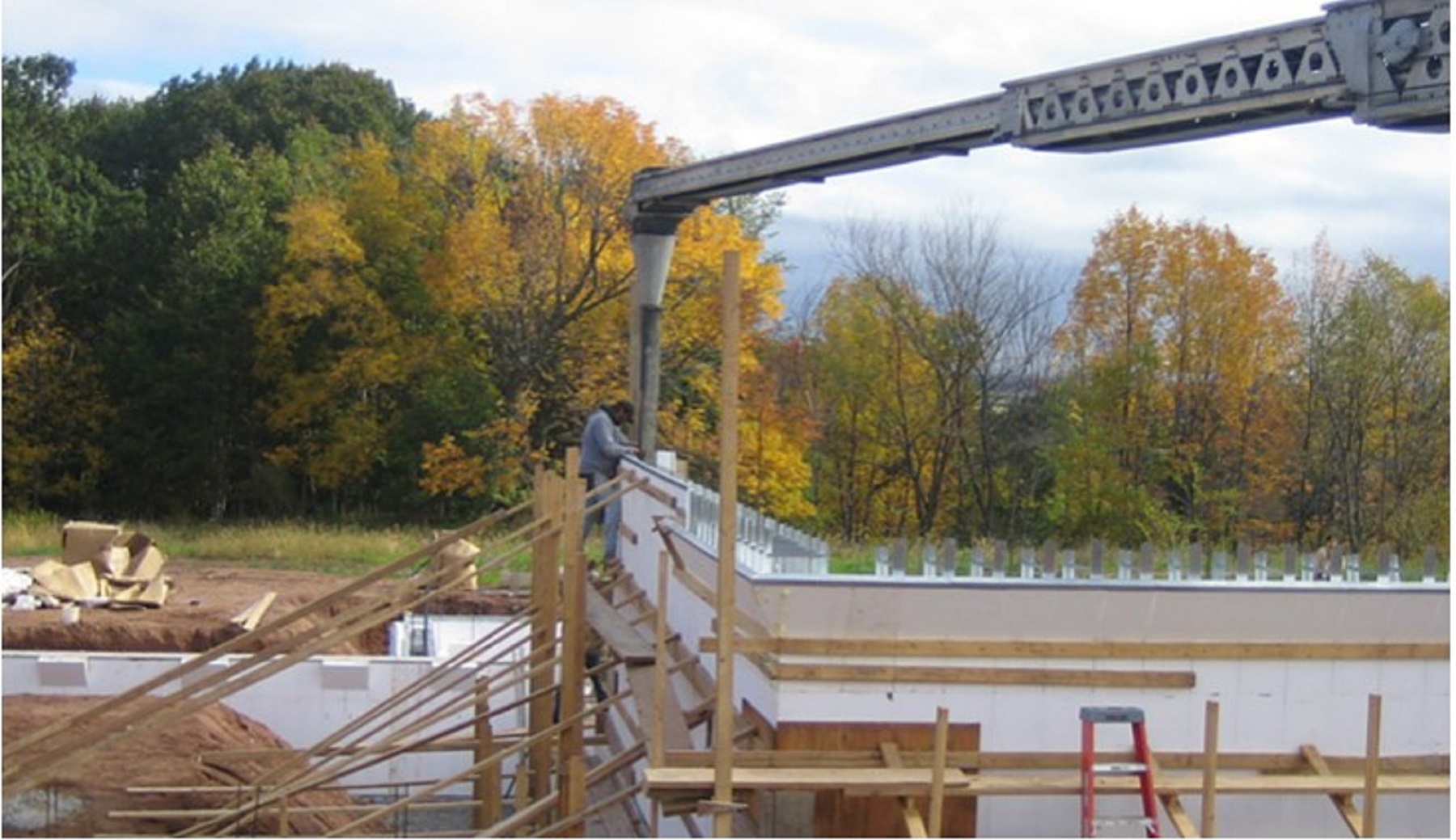
Figure 4. Carew Residence project.
The foundation walls, which used the TF Forming System’s vertically oriented ICF panel design, varied between 12 and 20 inches thick. Helix TSMR was added into the concrete ready-mix trucks and pumped into each wall segment, as seen in the picture below.
The Helix TSMR design for the foundation wall used 9 lb/yd3 to replace all of the vertical and horizontal rebar.
Richard Mortlock of TF Forming Systems said that “by incorporating Helix Steel in our design, we attained a higher level of structural reinforcement.”
Conclusion:
TSMR reinforced concrete refers to concrete reinforced with short, randomly oriented twisted steel filaments. TSMR is fully anchored in concrete using continuous twisted rib formations along the length of the shaft, similar to rebar. Because this type of reinforcement is distributed throughout the matrix and is fully anchored, it carries load both before and after the concrete develops cracks. In addition to its load-carrying capacity, TSMR provides redistribution of loads, potential reduction in crack widths, and increased durability of the finished structure. The degree to which these benefits are realized depends on the amount of TSMR added to the concrete mix. Although TSMR is not referenced in the IBC or IRC, the codes do allow the use of alternative products as long as they undergo a detailed review process (Section 104.11, 2015 IRC).
In order to successfully introduce any alternative product evaluation reports are used to help assess a product’s code compliance through the code specified AMC provision and are typically used for products or systems not addressed in the code. They are also provided to help the building official and design professional determine if products or systems meet the prescriptive requirements and/or intent of the code. Contractors, builders and engineers looking for such support have access to a Uniform-ES code approved evaluation report ER-0279 (5) completed by Helix in 2013. The ER-0279 states that Helix TSMR can be used in concrete reinforcement for walls and structural applications, which includes the residential concrete foundation wall. For more information, contact a Helix representative at 734-322-2114 or visit their website at www.helixsteel.com/residential.
About the Authors:
Samhar Hoz is a structural engineer at Helix Steel in Ann Arbor, Michigan. She has a master’s degree in engineering management from Eastern Michigan University. She has a Bachelor of Science in civil/structural engineering from Baghdad University. She has more than seven years’ experience in reinforced concrete structural design and construction for industrial and commercial projects. She is a secretary of two ACI 332 residential concrete work sub-committees.
Jeff Novak is vice president of engineering at Helix Steel in Ann Arbor, Michigan. He is responsible for the preparation of calculations for tunnel structures and building components using Helix concrete. He has more than 30 years’ experience in structural design of industrial and commercial projects. He earned a Bachelor of Science in civil engineering from the University of Maryland and an MBA from Kennesaw State University. He is subcommittee chairman of 506-b Fiber Reinforced Shotcrete and active on committees 506 Shotcrete, 360 Design of Slabs on Grade, and 544 Fiber Reinforced Concrete, and he is on American Society of Testing and Materials subcommittee C09.42 Fiber Reinforced Concrete.
Luke R. Pinkerton is president and chief technology officer at Helix Steel in Ann Arbor, Michigan. He has a Bachelor of Science in physics from Hope College and a Master of Science in civil/structural engineering from the University of Michigan, and he founded Helix Steel in 2002. He has 12 years of experience in reinforced concrete design, steel fiber design, non-linear finite element analysis, and blast and impact resistant design and testing. Luke is a member of ACI Committee 332, Residential Concrete Work and ASTM Concrete Pipe – C13.
Reference:
- American Concrete Institute. “Building code requirement for reinforced concrete.” (2014). ACI 318-14, Farmington Hills, Mich.
- American Concrete Institute. “Building code requirement for reinforced concrete.” (2014). ACI 332-14, Farmington Hills, Mich.
- International Code Council, 2015. Country Club Hills, Ill.
- Pinkerton, L.R. & Novak, J. (2014). Twisted steel micro-reinforcement – Advantages of microscopic composites. Concrete. 48. 36-37.
- Uniform Evaluation Service Evaluation report #297 (2013). Uniform Evaluation Service,. Ontario, Calif.
- Uniform Evaluation Service Evaluation Criteria #015 (2014). Uniform Evaluation Service, 5001 E. Philadelphia St. Ontario, CA 91761 – USA
Steel may be an expensive material, but its high strength makes it one of the most important parts of constructing a sizeable concrete structure today. Its useful strength in tension and compression makes it ten times stronger than the concrete itself, thus adding unmatchable strength to concrete structures.