OSHA Whistleblower Investigations
Employers need to make sure their policies and practices do not violate the law
by Jim Rogers, jimrogers@asu.edu
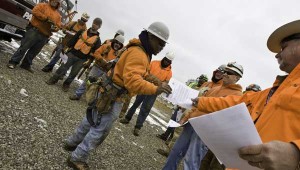
The job site safety meeting is one of the most important aspects of maintaining a program where both the company’s managed safety rules are kept active as well as the methods for reporting unsafe conditions or practices.
As contractors, we are all aware of OSHA and its role in protecting the health and safety of our workforce. Many contractors send their personnel to receive training related to record keeping requirements and job site regulations; however, one area that is often overlooked relates to the laws under OSHA’s jurisdiction that protect “whistleblowers”. People generally associate this term with an employee who “turns in” an employer for unsafe practices. While this is certainly an accurate association, there are much more subtle forms of whistleblower violations that an employer may engage in, some of which may not even be recognized within the company.
The OSH Act, signed into law in 1971, created the Occupational Safety and Health Administration within the U.S. Department of Labor. The OSH Act requires employers to provide a safe and healthful workplace for all employees. This general requirement is also known as the “General Duty Clause” and all of the published OSHA standards, such as the 29 CFR 1926 Construction Industry Standards, are basically extensions of this general requirement. The Act also gives employees the right to file an OSHA complaint, the right to take part in an inspection or speak to an OSHA Compliance Officer, and the right to raise a concern or complaint about a health or safety issue. Employees must also be given reasonable access to company records regarding accident and exposure rates. There are many laws under OSHA’s jurisdiction that protect employees from discrimination or retaliation when they exercise any of these rights. In fact, OSHA enforces the whistleblower provisions of 22 statutes protecting employees who report violations of various securities laws, trucking, airline, nuclear power, pipeline, environmental, rail, public transportation, workplace safety and health, and consumer protection laws.
FIVE EMPLOYER STEPS TO WHISTLEBLOWER COMPLIANCE
- Make sure superintendents know employees have the right to file OSHA complaints.
- Create an environment that encourages reporting unsafe conditions.
- Provide proper training throughout your company on the handling of complaints.
- Institute a reporting system that is effective to the chain of command.
- Review incentive programs to ensure they don’t discourage reporting of incidents.
Classic examples of retaliation against an employee include firing them or laying them off, “blacklisting” them within the industry, demoting them or denying them a promotion or other benefits. Threats, harassment and intimidation are also considered violations of the whistleblower protection laws. While these so called classic examples may be fairly straightforward, i.e. the employee files a complaint and the employer finds out and retaliates, there are also much more subtle forms of violations that employers need to be aware of. These more subtle forms of violations include intimidation or harassment by middle managers who may not be aware of the laws, creating an overall environment that discourages the reporting of hazards, and the use of any incentive program that disciplines or assigns any sort of demerits to individuals who report injuries.
OSHA has announced stepped up investigation and enforcement in this area, so it is important for employers to make sure none of their policies or practices violates the law. The first two issues, harassment by managers who may not be aware of the laws, and having an overall environment that discourages the reporting of safety issues, can be resolved through training and policy implementation. Make sure your superintendents, foremen and crew leaders understand that all employees have these rights and instruct them that they cannot take action against employees for exercising these rights. Creating an environment that encourages the reporting of unsafe conditions can boost employee morale and it shows them that you care about them. Used as a management tool, a system like this can also help an employer be proactive in identification and abatement of hazardous conditions. Injuries to employees result in lost time, reduced productivity, lower morale, higher employee turnover, and increased workers compensation insurance costs (just to name a few).
The construction industry depends on its workforce to deliver its products and services. Creating an environment that shows these employees that you care about their health and well-being can lead to increased morale on the job site, it helps to reduce employee turnover, and helps management to identify and abate hazards before they have a chance to cause injuries.
In addition to these “human” impacts, occupational injuries, deaths and illnesses continue to have an extreme economic impact on the industry. The number of fatal and nonfatal injuries in 2007 was estimated to be more than 5,600 and almost 8,559,000, respectively, at a cost of $6 billion and $186 billion. The number of fatal and nonfatal illnesses was estimated at more than 53,000 and nearly 427,000, respectively, with cost estimates of $46 billion and $12 billion. For injuries and diseases combined, medical cost estimates were $67 billion (27% of the total), and indirect costs were almost $183 billion (73%). Injuries comprised 77 percent of the total, and diseases accounted for 23 percent. The total estimated costs were approximately $250 billion.
The medical and indirect costs of occupational injuries and illnesses are sizable, at least as large as the cost of cancer. Workers’ compensation covers less than 25 percent of these costs.1 To help create an effective environment, an employer needs to provide proper training throughout the company to ensure that managers know how to properly handle complaints and suggestions, and to ensure that its trade’s people understand both their rights and their responsibilities. In any workplace, it is often most affective to have a system of reporting that results in issues being reviewed by people outside the reporting employee’s direct chain of command. In the construction industry, this can be especially helpful.
In our industry we go to work every day on multi-employer worksites, under constantly changing job site conditions and ever increasing pressures to get the job done. When a foreman is in the middle of trying to balance safety, productivity and quality, it can be easy to inadvertently overlook the significance of a single employee’s issue or concern. It is the employer’s challenge to create a system that seeks to remove causes of concern before they arise and to then effectively handle the unforeseen situations that arise everyday on our job sites.
The improper use of incentive programs has recently come into the public view in a case filed by OSHA earlier in 2013 against BNSF Railway Company. This is a large railroad company that has been in business for decades and probably has more resources at its disposal than many general contractors, and certainly more than most trade contractors, yet they still found themselves the subject of a very serious investigation into violations of whistleblower protection laws under OSHA’s jurisdiction.
This case highlights the potential subtleties of the law and illustrates how easy it could be for an incentive program to cross the line. OSHA has provided a great deal of information on this investigation and interested employers may find it helpful to read more on OSHA’s web site at www.osha.gov (search for BNSF Accord).
As an overview, BNSF had a program in place known as its Personal Performance Index. Under this plan, an employee would accrue points for reporting on-the-job injuries. The accrual of too many points was used as a criteria in the selection of employees who would be required to undergo additional reviews and possible disciplinary actions. This program resulted, according to BNSF employees, in an environment where the reporting of on-the-job injuries was discouraged. OSHA viewed this as a direct violation of the whistleblower protection laws. By assigning points to injured employees, regardless of the root cause of the incident, the company was not only in violation of the whistleblower protection laws, but they were also missing out on the opportunity to find and fix hazardous conditions.
Management reports that inaccurately show no on-the-job injuries are virtually useless as a tool for identifying areas that need to be addressed within a company’s operations.
The OSHA investigation into BNSF’s work practices resulted in a settlement with multiple employees and the signing of an agreement between BNSF and OSHA which included major changes to work place programs and continued monitoring of the programs by OSHA to ensure future compliance.
Any company could find themselves in this situation if they are not aware of the laws and how OSHA applies it to them. Any company incentive program that discourages the reporting of injuries is viewed by OSHA as flawed and has the potential to start a probe into violations of the whistleblower protection laws.
Consider something as seemingly innocent as a program that states “if no one gets hurt for the next 60 days, everyone on the crew gets a $250 bonus – but if one person gets hurt, then no one gets bonuses and we start the 60 day clock over.” On the surface, this might seem valid. The idea is to eliminate injuries and encourage the entire crew to look out for each other; however, this plan could easily be flawed and have the undesired effect of discouraging the reporting of any workplace injuries. For example, let’s say one member of the concrete placement crew is injured on some rebar, installed by others, that was not properly capped. The foreman takes the injured worker to the emergency room where he is stitched up. The company has good health insurance for its employees and the foreman suggests that the worker just have the bill paid by his health insurance. That way the injury doesn’t have to be reported to the company, and the crew doesn’t risk losing $250 each over an injury that they all feel is someone else’s fault anyway.
All of a sudden, what seemed like a simple plan to reduce accidents has turned into:
- A potential violation of OSHA whistleblower protection laws because the employee is being discouraged from reporting an injury
- A potential workers compensation insurance fraud case (depending on the laws of your state)
- A potential disgruntled employee due to the pressure being placed on them to keep the injury a secret
- A missed opportunity for the company to identify a hazardous condition on the job site, potentially leading to repeat incidents
Late in 2012, OSHA created the Whistleblower Protection Advisory Committee and Dr. David Michaels, Assistant U.S. Secretary of Labor in charge of OSHA, made the Whistleblower Protection Program a directorate, creating the Directorate of Whistleblower Protection Programs (DWPP) and adding over 35 positions for whistleblower field staff nationwide.
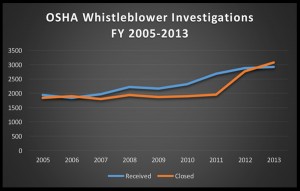
Fig. 1 – OSHA Whistleblower complaints for FY 2005-2013. Note the over 35% increase in annual cases closed in 2013 versus 2011.
The effects of these changes are illustrated in the chart in Figure 1 which shows a marked increase in the number of cases closed since the new Directorate was established. More recently, OSHA established an on-line portal that allows an individual to file a complaint over the Internet which is routed directly to the appropriate authority. With these significant changes and attention focused on enforcement, it is certainly prudent for all companies, large and small, to review their programs and policies for compliance. Make sure your incentive programs do not have unintended consequences. Educate your managers, superintendents and even foremen so they are aware of the laws. Work to create an environment that seeks to identify and eliminate potential hazards. Create a culture of safety that protects our human resources and encourages equal attention be paid to safety, productivity and quality.
ABOUT THE AUTHOR
Jim Rogers, is the Director of the OSHA Training Institute Education Center at Arizona State University, a part of the Del E. Webb School of Construction. He also teaches in the construction management program as an Associate Faculty member with courses including concrete, reinforcing, productivity and safety. Mr. Rogers has been involved in the construction industry for more than 25 years, specializing in concrete and post-tensioning. For additional information, visit http://osha.asu.edu.