2024 PROJECTS OF THE YEAR
The Rest of the Best
The last issue of Concrete Facts presented the top-voted project and each of the respective category winners from the 25th annual competition for the Concrete Foundations Association. Two ways to revisit these project awards are available in the toolbox accompanying this article. The feature image from each project can be found at the end of this article in a film-strip view as well. We now turn our attention to the remaining winners across the broad spectrum of submitions and categories as we present the rest of the best.
Projects of the Year is a showcase for many great works submitted by Association members who represent some of the top concrete professionals across the country. These projects demonstrate craftsmanship and creativity, setting standards for the cast-in-place concrete industry. Longtime member and past Board member, Kirby Justesen, president of SCW Footings & Foundations, knows how beneficial the program is. His company holds the record for the most CFA project awards received in a single year as well as holding the record for the most CFA project awards over all. Justesen said, “I think it’s a fun program that builds pride and unity for the company. The general contractor or owner of the project loves it when we hand deliver a winning plaque to them.”
Every award-winning project, whether a category winner or a named recipient, receives a plaque commemorating the win, as shown here.
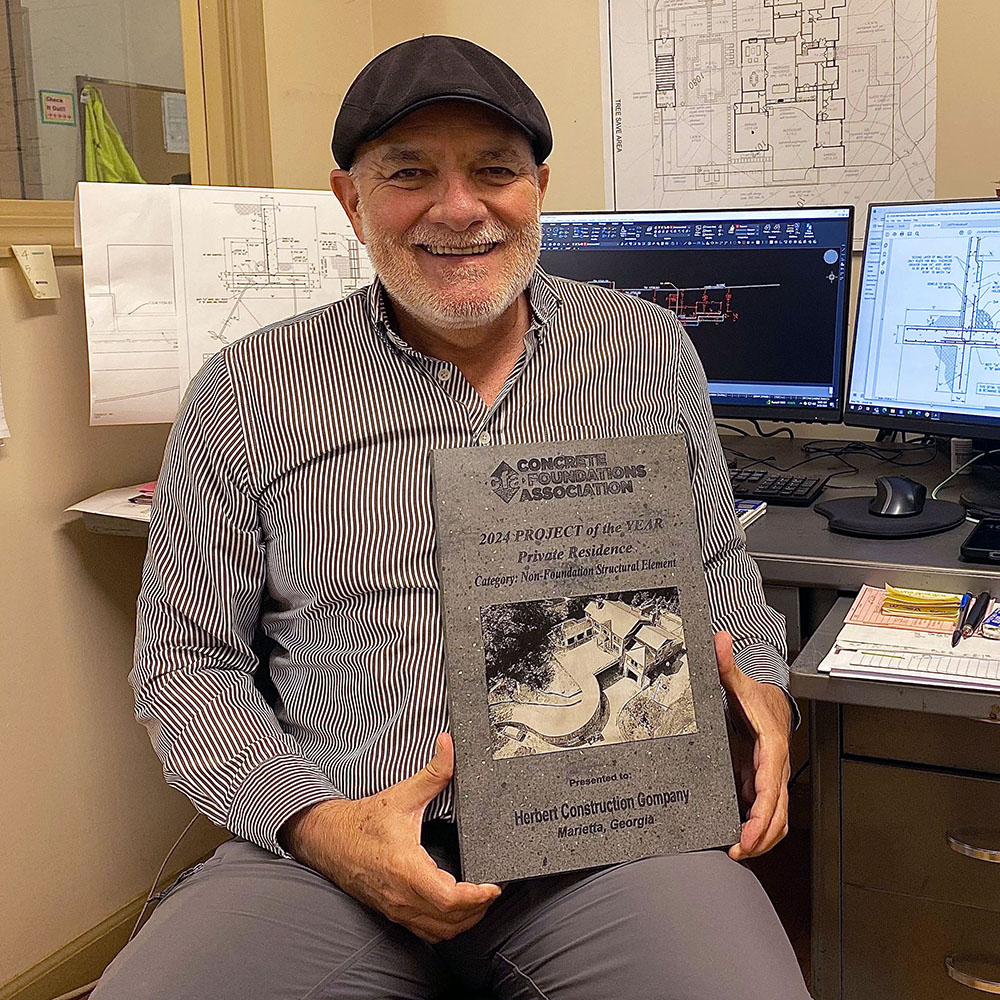
Francisco Hoyos, a CAD Operator for Herbert Construction Company, was heavily involved in the construction of the elevated slab for this CFA award-winning project.
Members receiving such recognition then have the opportunity to purchase additional plaques to further share their achievement and notoriety with key customers and owners involved in the project. For more information, visit https://cfaconcretepros.org/cfa-projects-of-the-year/, where application forms for the 2025 program, due April 26, 2025, are already available.
Visit the Category Winners online at
concretefactsmagazine.com,
the flipbook version at
cfaconcretepros.aflip.in/ConcreteFactsVol32-1_2024-September.html,
or visit the award page listing at
cfaconcretepros.org/cfa-projects-of-the-year
And now,
the rest of the best for 2024.
_____________________________________________________________________________________________
NON-FOUNDATION STRUCTURAL ELEMENT
HERBERT CONSTRUCTION COMPANY
PRIVATE RESIDENCE – ATLANTA, GEORGIA
This project stands as an outstanding example of innovation and engineering excellence, earning accolades for its remarkable achievements in residential construction. Encompassing 5,221 square feet, this extensive build incorporated 1,375 cubic yards of concrete and an impressive 243,821 pounds of steel reinforcement, spanning 190,829 linear feet. Over a meticulous three-year period, the project was executed in 14 phases, showcasing unparalleled precision and craftsmanship.
One of its most noteworthy accomplishments is the construction of a massive 20-foot-tall basement with integrated RV parking, complemented by a sophisticated pool and site retaining walls to navigate substantial grade changes. The inclusion of a robust concrete safe room with a concrete roof further demonstrated a commitment to safety and durability.
The project’s crown jewel is the thick elevated structural slab, which is 55 feet by 55 feet by 14 inches and is positioned 14 feet above finished grade, supported by advanced rebar and post-tensioning cables to form an upper and lower motor court. This ambitious feature is a testament to advanced engineering and design ingenuity.
The team gave special attention to custom solutions, such as blockouts for RV plumbing, water, and electrical needs. The use of #9 rebar, rare in residential settings, highlighted the project’s emphasis on reinforcement and resilience. Additionally, the project included curved, sloped retaining walls designed with precision-engineered brick ledge boxes, brought to life through CAD and careful craftsmanship.
This achievement exemplifies how thoughtful design, strategic planning, and execution can push the boundaries of residential construction, setting a new standard for future projects.
_____________________________________________________________________________________________
NON-FOUNDATION STRUCTURAL ELEMENT
BEAVER CONCRETE CONSTRUCTION
ASHBURN COMMUNITY CHURCH WALL – ASHBURN, VIRGINIA
This project showcases a complex design of four converging retaining walls, each with a unique shape and curvature. The walls, averaging 11 feet in height and 8 inches in thickness, span a total of 415 linear feet, requiring 250 cubic yards of concrete. Each wall’s distinct height and radius presented significant design and construction challenges.
The construction included four series of radius footers, each set at different elevations and distances, converging at both ends. These footers, essential for structural stability, varied in depth to adapt to poor soil conditions near zoned wetland areas. The increased footer depth ensured the integrity of the structure while meeting aesthetic and design requirements.
Close collaboration was imperative to overcome site challenges. The principal design team, engineering team, excavation team, and contractor’s estimating and operations teams worked in unison to address soil conditions and maintain design integrity. Effective communication streamlined the project, ensuring that all aspects met the client’s expectations.
This project exemplifies innovative engineering and meticulous planning, resulting in a harmonious blend of form and function. The careful consideration of soil conditions, combined with the unique design elements, highlights the collaborative effort required to achieve this complex and aesthetically pleasing structure.
_____________________________________________________________________________________________
SINGLE-FAMILY FOUNDATION – 2,000 TO 5,000 SQ. FT.
CHAPIN CONCRETE CONTRACTORS INC.
COULTER ROAD – ST. MATTHEWS, SOUTH CAROLINA
This medium-sized residential concrete foundation project is a testament to meticulous planning, expert execution, and innovative design. Spanning 423 linear feet and covering 2,335 square feet, the foundation utilized a total of 195 cubic yards of concrete—43 cubic yards for the footings and 109 cubic yards for the foundation walls. An additional 43 cubic yards of concrete were required for the slabs, which featured microfiber reinforcement for enhanced durability.
The project included 7,200 pounds of steel reinforcement, distributed with 2,900 pounds in the footings and 4,300 pounds in the walls. The basement wall footings were constructed to a standard 24 inches wide by 12 inches thick, while the retaining wall footings varied in width from 3 to 8 feet, maintaining a consistent 12-inch thickness. Remarkably, only 3 vertical feet of change in footing elevation were required, reducing complexity in the overall process. The supporting walls, ranging from 8 to 12 inches thick and heights between 5 and 11 feet, provided solid structural support.
The true hallmark of this project is its 12 arched openings, carefully crafted into the walls to serve as windows and decorative elements. These arches added an artistic dimension to the construction, making it an exciting endeavor for the team. Each blockout was skillfully built off site at the contractor’s shop, where templates marked on the floor and high-end materials ensured smooth, precise finishes. Once transported to the site, setting and bracing the arches took just over two days before the concrete was poured, resulting in visually striking features such as arched windows, door openings, and a standalone porch structure supported by three arches and rebar grade beams.
This project exemplifies excellence in residential construction, merging structural precision with aesthetic finesse. The innovative use of handcrafted arches showcases a commitment to craftsmanship and an eye for detail, elevating the overall appeal of this medium-sized foundation.
_____________________________________________________________________________________________
SINGLE-FAMILY FOUNDATION – 2,000 TO 5,000 SQ. FT.
STEPHENS & SMITH CONSTRUCTION CO.
PRIVATE RESIDENCE – ELKHORN, NEBRASKA
This single-family residence foundation project is recognized as an exemplary achievement in concrete construction, earning distinction for its innovation and precise execution. With a 4,004-square-foot footprint and 971 linear feet of walls, the foundation required 438 cubic yards of concrete and 27,440 pounds of steel reinforcement.
The project team overcame notable challenges due to the need for non-standard, reinforced footings to support a precast hollow core plank main floor with a 4-inch topping. The intricate design included footings up to 32 inches wide and 12 inches thick, along with 17 interior pads, all precisely coordinated across eight distinct elevation steps. These adjustments allowed for seamless transitions between various foundation elements, including basement, crawl space, and grade beam footings.
A particular highlight was the construction of complex radius retaining and stair walls, requiring careful excavation to maintain structural integrity between closely placed footings. These radius walls, incorporating four different curves and stone ledges, ranged from 2 feet to 14 feet in height. The meticulous use of #5 and #4 rebar ensured stability and resilience.
The project’s success was underpinned by detailed collaboration with engineers and contractors, with 3D modeling playing a pivotal role in translating design complexities to on-site execution. The result was a durable, visually compelling foundation.
This project not only met but exceeded industry standards, highlighting the team’s commitment to superior craftsmanship and their ability to transform complex requirements into a beautifully executed residential foundation.
_____________________________________________________________________________________________
SINGLE-FAMILY FOUNDATION – 10,000 TO 15,000 SQ. FT.
SCW FOOTINGS & FOUNDATIONS INC.
COLEMAN RESIDENCE – MORGAN COUNTY, UTAH
This single-family residence project, spanning an impressive 10,852 square feet, has earned recognition for excellence in concrete foundation construction. The project distinguished itself with its scale and complexity, involving 980 linear feet of concrete construction and a total of 539 cubic yards poured—247 cubic yards in the footings and 292 in the walls. Reinforcement reached an extraordinary 41,110 pounds, ensuring structural integrity, with over 10,200 pounds in the footings and nearly 30,900 pounds fortifying the walls.
The team demonstrated exceptional skill in managing the project’s challenges, including eleven wall heights from 3 to 16 feet and wall thicknesses ranging from 8 to 24 inches. Navigating the varied terrain required seven footing steps and twenty-one wall steps, totaling 48 and 101 feet in vertical grade changes, respectively. The project also incorporated 111 90-degree corners and 37 bay corners, showcasing meticulous planning and expertise.
Achieving such results required three separate concrete pours over a 237-foot-wide span. Each cold joint was precisely aligned to ensure seamless integration across the stages. The team’s attention to detail and ability to execute complex design elements set this project apart as a leader in residential concrete construction.
This project’s recognition as an award winner highlights an outstanding commitment to craftsmanship, precision, and innovation, making it a benchmark for excellence in structural engineering.
_____________________________________________________________________________________________
SINGLE-FAMILY FOUNDATION – 10,000 TO 15,000 SQ. FT.
EKEDAL CONCRETE
929 ZURICH CIRCLE – NEWPORT BEACH, CALIFORNIA
This concrete foundation project, encompassing 13,972 linear feet and 7,138 square feet, is a testament to engineering prowess and innovative construction techniques. The project features a 42-inch-thick mat slab with a 4-foot step down at the garage, and it includes car lifts, a sump tank ejection system, and a theater floor, all housed within a complex basement structure.
The project utilized 1,725 cubic yards of concrete, with 150 yards for walls and 852 yards for footings, reinforced by 28,000 pounds of steel in the walls and 89,000 pounds in the footings. The basement’s walls and slabs were constructed using epoxy-coated rebar to combat saltwater corrosion, a critical choice due to the site’s proximity to the ocean.
Notable features include an elevator shaft extending 40 feet below the water table and the use of shotcrete for basement walls, necessary due to the secant pile shoring system. The project was further complicated by the constant need for dewatering to manage ocean water intrusion, requiring around-the-clock pump monitoring to protect neighboring homes from subsidence.
Despite the tight site constraints, the project successfully integrated two floors of concrete decks with embedded I-beams and a concrete roof designed to support vehicular traffic. A robust elevator system, capable of accommodating a car, links the street level to the basement, as well as the second floor and roof.
Employing 5,000 psi concrete and ensuring waterproofing compatible with saltwater and hydrostatic conditions, this project exemplifies excellence in construction under challenging conditions, making it a worthy candidate for industry recognition.
_____________________________________________________________________________________________
ABOVE-GRADE CONCRETE HOME
BP WALLS INC. DBA TCB WALLS
BANANA RIVER DRIVE – MERRITT ISLAND, FLORIDA
This project is a rare feat in the residential industry, showcasing high-quality craftsmanship and durability in an all-concrete home. Spanning 6,262 square feet with 370 linear feet of walls, the construction consumed 117.5 cubic yards of concrete and 9,000 pounds of steel. Walls ranging from 12 to 15 feet tall, with a finished height of 24 feet, were built with varying thicknesses of 6, 12, and 16 inches, ensuring structural robustness.
Despite a challenging building site with limited access, the home was strategically positioned close to the road to optimize space. The use of hydraulic lifts and custom scaffold brackets facilitated construction on the confined site. The porch beams are a noteworthy feature; they were designed to shield truss ends from humid air, minimizing rot risk and enabling seamless stucco application. The front porch beam spans 34 feet without center support columns, offering unobstructed water views.
Situated along the intercoastal waterway, the residence boasts panoramic vistas of the cruise terminal at Port Canaveral and the Indian River. Its location underscores the significance of storm-resistant homes, making it a beacon of resilience in coastal living. This project exemplifies the possibilities of cast-in-place concrete construction, demonstrating its capacity to withstand environmental challenges while providing enduring elegance and functionality.
_____________________________________________________________________________________________
SINGLE-FAMILY FOUNDATION – 5,000 TO 10,000 SQ. FT.
HERBERT CONSTRUCTION COMPANY
PENINSULA HOUSE – METRO ATLANTA, GEORGIA
This residential foundation has been recognized as a benchmark in construction excellence, showcasing technical achievement and innovation. Spanning 6,597 square feet, this extraordinary project required 574 cubic yards of concrete and nearly 39,000 linear feet of steel reinforcement, amounting to an impressive 27,440 pounds. Faced with difficult site conditions—a lakeside peninsula with steep elevations and poor soil—the construction team displayed exceptional skill and ingenuity.
This project had 17 distinct wall heights, stepping incrementally by one foot and incorporating four varied wall thicknesses: 8, 10, 12, and 16 inches. Such complexity was seamlessly managed, even as the project included a curved garage retaining wall with 10 vertical footing jumps over 67 feet and intricate footing pads for structural steel columns. The team’s adaptability was further tested when deep excavation unearthed old pipes and building remnants, yet they skillfully maintained progress.
The phased construction approach—beginning at the rear of the property and advancing toward the road—was a strategic response to seasonal rain and the challenging terrain. This effort included six separate footing and wall pours, executed with precision to meet high standards.
The standout achievement of this project was a 203-foot multi-radius retaining wall, boasting a 32-foot vertical elevation change and 16 footing jumps, complete with angled corners and a sloped top incorporating a brickledge. Additionally, the garage’s unique slab-ledged wall retained external dirt while supporting an internal slab, and two parallel stairway walls extended 3 feet above the basement to form a handrail, sloping from 18 feet 8 inches to 10 feet 8inches with door openings. The seamless integration of an elevator foundation further underscored the project’s technical mastery.
The Peninsula House exemplifies excellence in design and construction, overcoming natural obstacles with ingenuity and delivering a complex, multi-phased foundation worthy of industry acclaim.
_____________________________________________________________________________________________
EXISTING STRUCTURE ADDITION
TALPEY CONSTRUCTION LLC
Riverbank Lane – Old Lyme, Connecticut
This project showcases exceptional engineering and construction, integrating new porches, a garage, and a full basement with an existing house on a sloping riverfront lot. The addition required 35 stepped footings to manage the grade changes and involved 460 linear feet of concrete walls and 5,000 square feet of floor area. The construction utilized 518 cubic yards of concrete—260 yards for footings and 258 yards for foundation walls—and 36,000 pounds of steel reinforcement.
Wall heights ranged from 3 feet to 14 feet, with standard thicknesses of 8 and 12 inches. The addition’s front wall was 13 feet at its deepest, stepping up to frost wall areas. Walls diverged from the existing house at two angles, adding complexity.
The contractor began by establishing points and elevations on the existing house. Despite repeated rain causing washouts, footings were placed in a single pour. Wall forming started at the farthest point, progressing outward, and required three pours due to logistical constraints and varied form heights. Restricted access and limited crane reach necessitated a staged approach, avoiding the need to lift forms over several walls and over an occupied house.
The project was further complicated by the family living in the house during construction. The team faced challenges, including adverse weather, grade adjustments, shoreline proximity, varied angles, and intricate footing steps. Despite these hurdles, the project concluded with outstanding quality, exemplifying superior construction management and technical execution. This foundation addition stands as a testament to meticulous planning, skilled craftsmanship, and innovative problem-solving.