Tight Market Conditions Briefing
May 2022 – Portland Cement Association
Introduction
Material specifiers frequently need to choose between concrete and alternative building materials. As concrete’s use has grown, cement shortages have begun to surface. Specifiers need accurate information about the shortage situation, and this briefing is an effort to provide the latest available information.
The Scope of Tight Market Conditions
Tight cement supply conditions vary by region but some evidence of tightness prevails in portions of 43 states according to PCA’s survey of cement manufacturers. In comparison, 28 states reported tightness in the spring of 2021. The tight cement supply conditions experienced during the past two years are a reflection of supply chain disruptions that have plagued the general economy. Where cement is in short supply, the reasons are typically threefold: strong cement demand, in some cases lingering disruptions associated with Covid-19, and logistics hinderances.
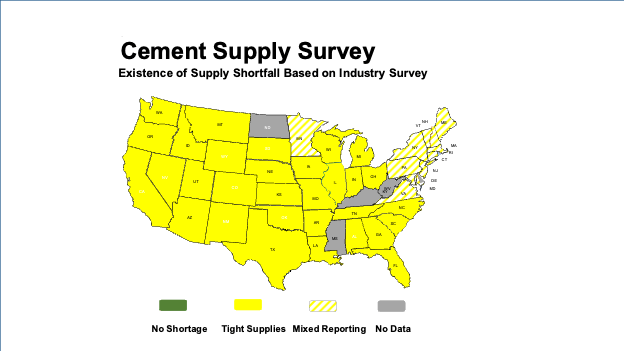
Strong Demand
Favorable winter weather last year resulted in strong consumption. On a seasonally adjusted basis, cement consumption in some of the winter months reached its highest levels since spring of 2007. Such strong consumption levels inhibit cement manufacturers’ ability to build inventories that are typically required to meet robust warm weather construction levels. Strong winter consumption conditions played a critical role in the emergence of tightness in 2021. These conditions repeated in 2022 – resulting in even stronger demand conditions than winter 2021.
Winter Inventory Build
Many cement companies build inventory during the winter months in preparation for peak summer construction season. Favorable weather conditions during the winter months generated stronger demand and hindered the ability to build inventories during typically slow cement consumption periods. According to PCA’s informal survey, spring order bookings remain strong and suggest the likelihood of strong near-term consumption levels.
Lingering Covid Disruptions
Furthermore, PCA surveys suggest some Covid-19 related production adjustments may have contributed to the lack of normal build-up of inventories that often materializes during the winter months. External contractor hours declined significantly in 2021. Some of these hours are accrued to specialized maintenance. Maintenance hinderances at cement manufacturing facilities can lead to unexpected temporary shutdowns which can aggravate shortages.
Import Disruptions
Port congestions and terminal disruptions have improved modestly since 2021. Despite this improvement, bottlenecks remain. Terminal disruptions, centered on the loading and unloading processes, have tied up ships, disrupting their normal flow. Port congestion has led to significant shipment delays. These delays can cause a ripple effect throughout the supply chain – including cement.
In addition to these difficulties, the war in the Ukraine has slowed exports to the United States from Turkey. Turkey imports one third of its coal from Russia. With the onset of hostilities, coal trade disruptions hindered Turkish cement production; such disruptions continue.
Turkey is the largest source of United States cement imports – accounting for more than 6.9 million metric tons in 2021 (more than even Canada’s 5.3 million metric tons). Turkish cement exports are concentrated on the U.S. east coast and states bordering the Gulf of Mexico. More than half of Turkey’s cement exports to the United States reach the Houston district ports; the Miami district accounts for 12%.
Logistic Hinderances
- The delivery of cement to the end consumer is heavily reliant on trucks and their drivers. Drivers are in short supply. This results in a slowing of cement deliveries.
- While only 17% of cement shipments to cement terminals travel via trucks, nearly all of the movement from terminals to final customers move via truck.
- Covid-related rail and barge disruptions also remain. These hinderances slow the cement products’ delivery to market and can account for transitory supply tightness. Even small temporary disruptions in shipments can cause turmoil in a geographic region. Notably, the Surface Transportation Board has recently taken action to assess and monitor wide-spread rail disruptions and service levels in an effort to facilitate improvements. The cement industry remains hopeful that over time the railroad supply chain will return to or even exceed previous “normal” operating conditions.
US Cement Supply Dynamics
The tight cement market conditions experienced during the past two years is a reflection of supply chain disruptions that have plagued the general economy. Some worry about the industry’s ability to meet upcoming demand associated with the infrastructure program. Many of the Covid-related supply chain disruptions will eventually fade – leading to improved supply capabilities.
PCA believes ample supply will be available to meet the demand associated with the infrastructure program. Consider the following:
- United States domestic cement capacity exceeds 106 million metric tons. In addition, more than 42 million metric tons of import capacity exists – bringing total cement capacity to 148 million metric tons.
- Supplementing this capacity, the United States cement industry continues to invest. Two U.S.-based plants are expanding capacity that by 2022 will add an additional 2.0 million metric tons of capacity. Permitting is underway for two greenfield sites that could add another 1.7 million metric tons of capacity. These investments come in the context of the industry’s ongoing investments to reduce its carbon footprint.
- In addition, several cement manufacturers have transitioned production, in whole or in part, from ordinary Portland cement to Portland limestone cement (Type 1L or PLC) as a key step to reduce the carbon intensity of cement and which, significantly, also leads to an increase in U.S. cement production capacity. These transitions to Type 1L and other blended cements are expected to continue as the U.S. cement industry supports future needs while also pursuing its roadmap to carbon neutrality.
- Aside from ample supply-side capabilities, it is likely that rising interest rates will result in some softening in residential and nonresidential demand for cement. This likelihood lowers the potential maximum cement consumption associated with the first few years of the recently passed infrastructure legislation. This potential demand side easing of consumption should contribute to the industry’s ability to meet infrastructure-related needs.