2020 PROJECTS OF THE YEAR
A Crop of Excellence During a Time of Pandemic
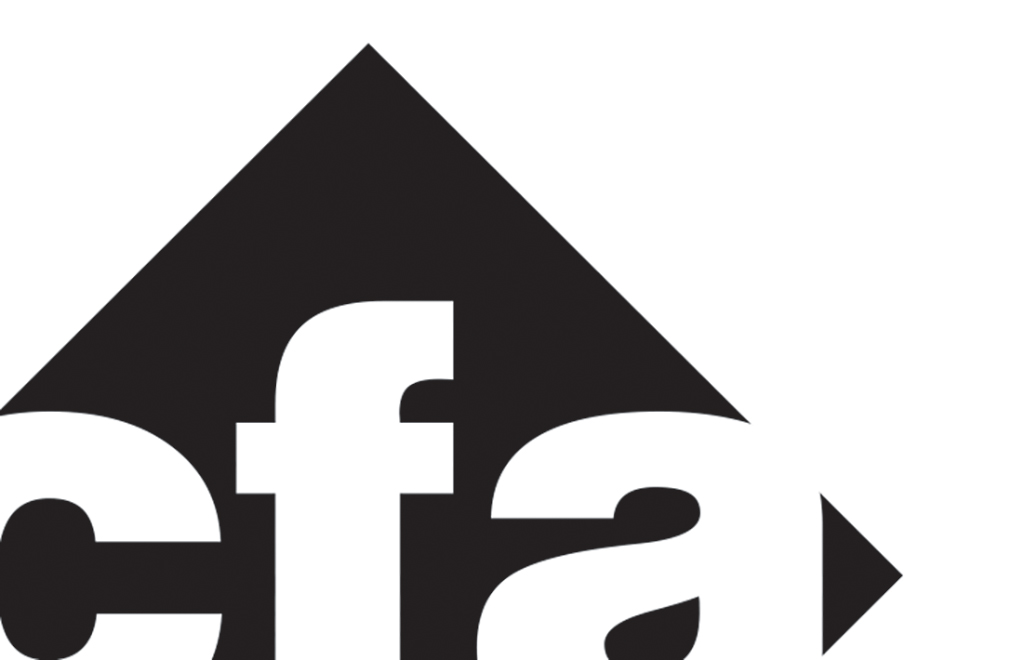
Each year, the Concrete Foundations Association offers to its members a chance to tout their accomplishments and reward their teams for jobs well done through the annual “Projects of the Year” awards. In addition to recognizing noteworthy projects, these awards expose people to the breadth of work completed by some of the industry’s top cast-in-place concrete companies.
Among the submittals every year are projects that can be described as massive and ones that are more representative of a modest size. Members are encouraged to keep track of projects that were complex challenges and projects that leave a team taking a breath to enjoy a job well done. Additionally, the categories are revisited each year to make sure there are openings appropriate for recognizing any new, diverse applications, which tend to showcase the creative growth of the cast-in-place concrete industry.
Formerly known as “The Basement From Hell,” the Association initiated this program under the direction of the long-time executive director, Ed Sauter. “Quite frankly, we initiated this program as a way of helping give annual marketing content to the Association,” Sauter said. “‘The Basement From Hell’ was coined to represent some truly remarkable, and at times monstrous, projects that challenged member companies the most.”
Each year, the top project was determined based on how challenging it was to estimate, build, and achieve some measure of profitability. This changed over time as project variety grew. “Today, contractor members of this Association are experts in residential and commercial foundations; they are taking on industrial slabs, tilt-up buildings, post-tensioned foundations, above-grade homes, and multi-family complexes,” said executive director for the CFA, James Baty. “As we have advanced the program, contractors have continued to ask us whether a project of one type or another would fit. This has resulted in broadening our categories to where, today, we have eight different categories and annually award at least half of them.”
The following pages represent this year’s awarded projects, selected for the first time in several years by popular vote by Association members. During #CFAAtTheEcho, participants had an opportunity to roam the Showcase Pavilion and watch three-minute videos about each project. After this, each project had a quick five-question survey with a point and click rating scale. This was an opportunity for the industry to come together to give contractors a chance to display their very best, and a chance to participate collaboratively in recognizing truly unique accomplishments.
______________________________________________________________________________
OVERALL GRAND PROJECT OF THE YEAR
Single-Family Residential Foundation Over 5,000 sq. ft.
SABO IN NEWPORT BEACH, CALIFORNIA
Member Since 2006

This project, nicknamed “Sabo,” is the type of job that would put many companies out of business if they did not know what they were doing. The project seems to have everything: caissons, shoring, mat slab, battered shotcrete walls, waterproofing, radius poured-in-place walls, outrageous rebar details, two pan decks with lightweight concrete, a radius driveway deck (above grade), waterproofing concrete additives, and epoxy-coated rebar.
The project’s footprint is 9,000 square feet, and its material details are incredible, with over 2,400 cubic yards of concrete, including over 1,100 yards each in the mat slab and caissons. There is 910,000 pounds of steel reinforcement, with 720,000 pounds in the caissons alone. Basement wall heights ranged from 11 to 26 feet and the wall thicknesses range from 12 to 18 inches.
“While gathering all of the data and information for this submission, I was left feeling very content with the amount of teamwork performed at Ekedal in a highly efficient manner,” stated Ryan Ekedal, president of Ekedal Concrete.
Rather than using traditional footings, this project has a 15,000-square-foot, 30-inch-thick mat slab. The slab features two layers of #6 reinforcement bars at 9-inch spacing each way, and all rebar was epoxy coated due to the proximity of the ocean below.
Since the project sits right on the bay front in Newport Beach and consists of a 9,000-square-foot basement foundation with the bottom of the slab sitting at 17 feet below sea level, we had to install a shoring and dewatering system. We drilled 109 30-inch caissons with a combined drilling depth of 6,000 feet. This was followed by the installation of a “secant” soldier pile system that used interlocked hard and soft piles, eliminating the need for the more common lagging technique used on shoring projects not in the water table. The reinforcing steel cages were over 48 feet long, each with eighteen #9 verticals with ties.
Once the caissons were drilled and poured, 17 “well points” with 18-inch diameters were drilled 50 feet deep, creating a dewatering system that brought the water table below the bottom elevation of the mat slab. This dewatering went on for six months.
The mat slab was used in lieu of footings, since the elevation is 17 feet below sea level. Once completed, the rest of the complex foundation, with curved walls and other architectural features, could progress.
“Receiving this award is such an honor, as it is voted on by my peers in the industry, which means a lot,” states Ekedal. “We try to deliver such an amazing experience to all of our clients, and to be acknowledged for this great work we are able to provide feels great! At Ekedal, we love concrete and the opportunities of building the impossible, so for other amazing people and companies in the industry to appreciate that is huge! This speaks volumes to the culture which is vital to the success and/or failures of a project or company. I try to always ensure the culture at Ekedal is one where all the employees know the mission and have the same goals and desire to be the best!”
______________________________________________________________________________
SINGLE-FAMILY RESIDENTIAL FOUNDATION 2-5k SQ. FT.
Private Residence in Atlanta, Georgia
HERBERT CONSTRUCTION COMPANY, MARIETTA, GEORGIA
Member Since 1992
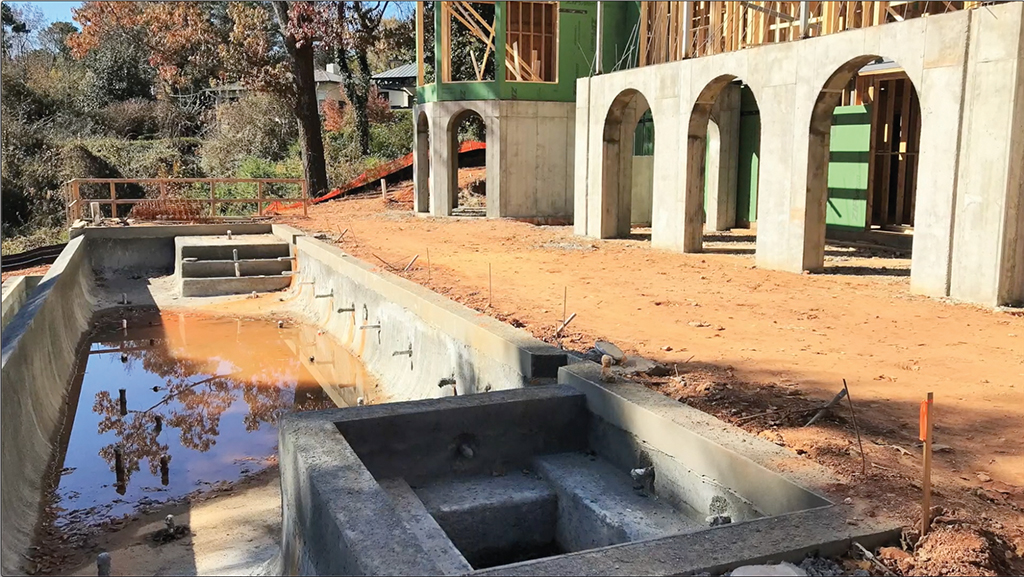
This project required considerable custom-built features. There were seven phases, each with its own estimate, and the company had to deal with bad soil (which had to be removed and replaced with stone) and install retaining walls to build up the road for access before beginning the foundation proper.
A total of 830 linear feet frame this 4,169-square-foot plan. The project required 562 cubic yards of concrete and over 56,000 pounds of steel. Wall heights stepped a total of eleven times (from 2 feet up to 15 feet) for five wall thicknesses (from 8 to 16 inches).
The phases of construction were carefully planned so as to keep the site and the complicated design under control. The first phase saw the construction of a 14-inch-thick by 4-foot-tall wall made for the pool with multiple radius walls. During phases two and three, two retaining walls were built — these were required for site access and for building the roadway up. One wall had a 106-foot radius with a heavy design and 378 vertical feet of radius corners, the other wall was 16 inches thick and 16 feet tall with a radius section sloping 13 feet downward to 7 feet.
Phase four was constructing the main basement walls, which were 11 feet tall and approximately 400 linear feet.
In phase five, the basement slab, thickened to six inches in some areas with additional reinforcing and helical piers due to poor soil conditions, totaled 3,770 square feet with a double-mat grid of #5 rebar.
The sixth phase consisted of building arched walls and footings for the back patio area. In all, 16 arched openings of six different sizes were placed in walls from 12 inches to 16 inches in thickness. The custom-built arched wood blockouts were crafted from Luan plywood to ensure a smooth finish, and seven beam pockets were included to hold I-beams for the covered patio above.
The final phase, phase seven, saw the installation of a retaining wall designed to build up the site for a driveway and to create a walkway to the basement level. This wall sloped from 4 feet to 12 feet tall.
This job required technical elevations because of jumps and radius walls. The arched openings did not have an assigned set radius, so, through trial and error, the arch was determined using CAD. Combined with the rest of our station, the result was unmatched accuracy.
______________________________________________________________________________
SINGLE-FAMILY RESIDENTIAL FOUNDATION < 2k SQ. FT.
Sweetwater Lake in Ninevah, Indiana
CUSTOM CONCRETE OF WESTFIELD, INDIANA
Member Since 1986
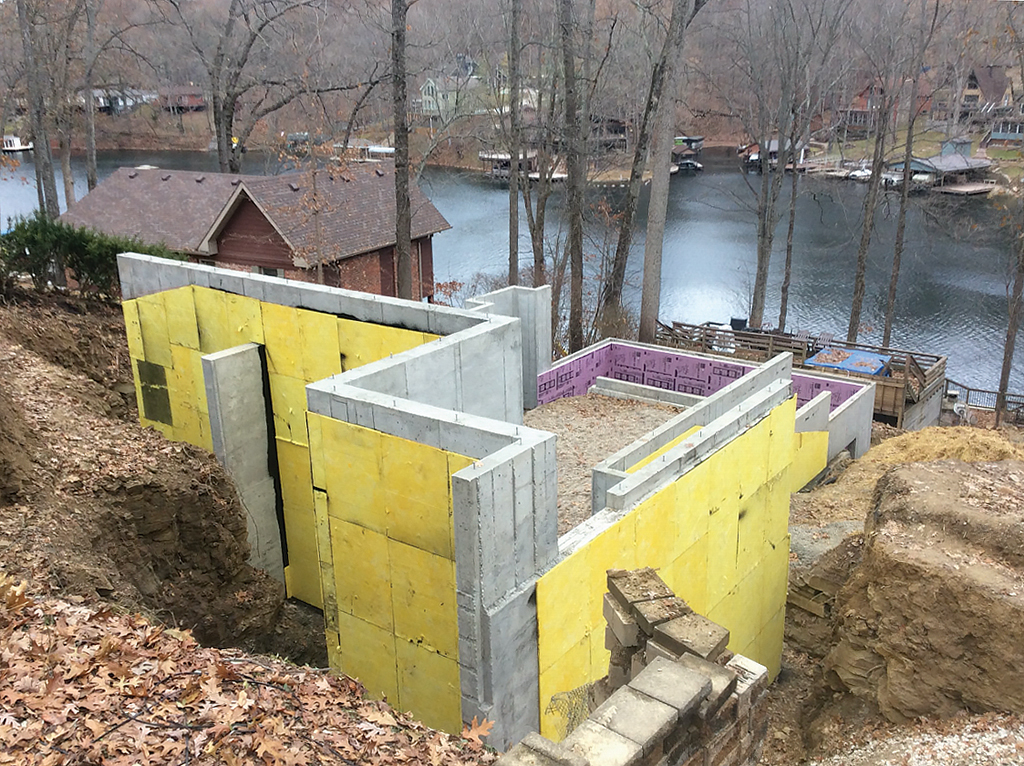
With a name like Sweetwater Lake, it should not come as a surprise that this project is located on a lake lot in southern Indiana, which is known for hard shale and limestone. The lot had a substantial amount of fall toward the lake, and the owner was hoping to save a portion of the lot’s pre-existing block basement foundation. The original plan was to add to the front of this existing basement.
This small footprint only enclosed 1,840 square feet, and in only 346 linear feet of wall, the wall stepped thirteen times from 1 foot up to 19 feet and 8 inches. Wall thicknesses were 8, 10, and 12 inches for a total concrete volume of 136 cubic yards with 8,257 pounds of steel.
Due to county building code requirements, the original foundation could not be kept, so we moved into demolition and hauled materials off site. When we proceeded with excavation, we soon encountered hard shale and limestone, which required a large excavator with a hammer. This unexpected obstacle greatly slowed down the project’s excavation phase.
In order to maintain access on the small lot throughout construction, we left off the garage foundation until the end of the project, facilitating access for our form delivery truck cranes, concrete pumps, and gravel conveyors. Adding to the challenge, the existing gravel drive was steep and tight for large trucks and equipment. When the walls were finally poured and stripped, the gravel conveyed, and the basement slab poured, we proceeded to add the attached garage foundation, which required 12-by-16-inch-tall retaining walls.
The walk-out basement included nearly 200 feet of 24-by-12-inch footings with #5 dowels that were 12 inches o.c., all installed on limestone rock. The extreme terrain made navigating and forming these footings difficult, but with CAD and total station layout, we were able to install these footings with precision.
As mentioned earlier, our walls stepped 13 times, ranging from 19 feet and 8 inches tall to 1 foot tall. To retain the high upper grade despite the severe fall of the grade toward the lake, we had to pour a wall that was 12 inches by 19 feet and 8 inches at the front of the lot as a part of the basement wall. This wall extended up through the first floor, supporting the second-floor system. We worked with the framer to establish the correct wall height. The wall then stepped with the grade from 19 feet and 8 inches down to 9 feet; we kept that height through the fireplace and then stepped down further to 5 feet for the “four seasons” room. The garage’s side walls stepped from 19 feet and 8 inches down to a 16-foot common wall and then down to 9 feet. The walls continued at this height to a large window and concluded at the “four seasons” room.
This property overlooks a beautiful lake, so it is no surprise that the owners wanted to take full advantage of the view. With an abundance of topographical fall, we were able to install this walk-out basement to complement the lot’s terrain and the view.
______________________________________________________________________________
ABOVE-GRADE ALL-CONCRETE SINGLE-FAMILY RESIDENCE
North Tropical on the Intercoastal Waterway, Florida
TCB WALLS INC. OF MELBOURNE, FLORIDA
Member Since 2019
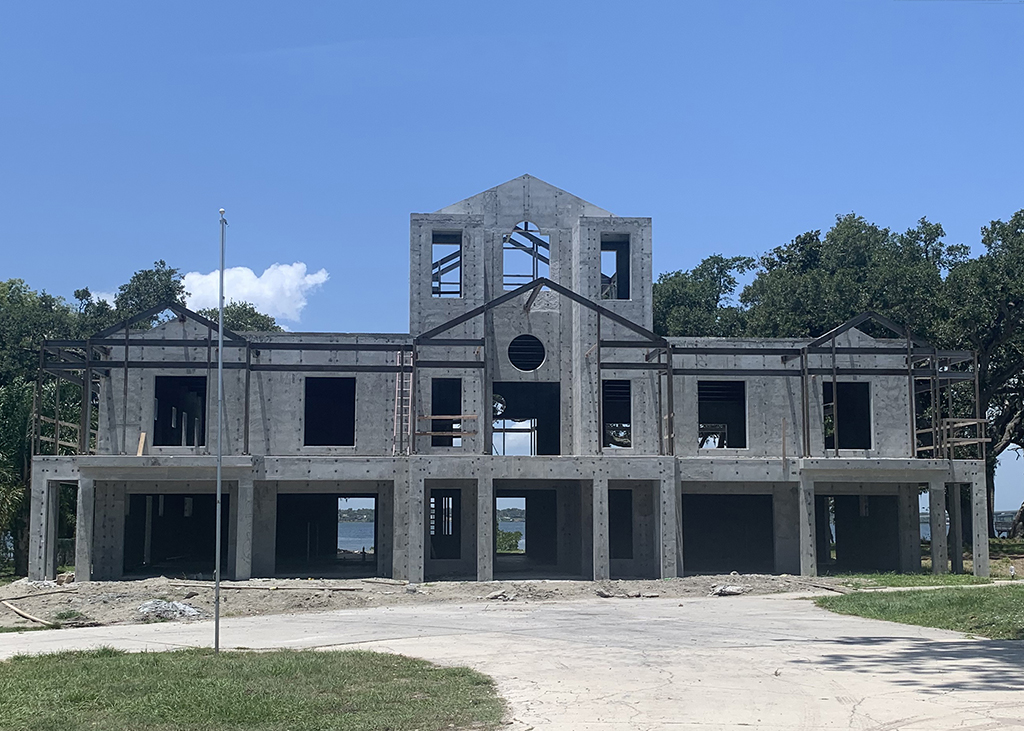
This above-grade concrete home was built in the state of Florida, where a reliable market is developing for the durability and security realized with all-concrete shells.
This job had a little bit of everything going on, and no single aspect was considered out of the ordinary. However, combining so many complicated items in one job made the project more unique in scope. The project consists of over 1,300 total linear feet of concrete wall throughout its 15,000-square-foot footprint, and the project totaled over 380 cubic yards of concrete.
The desire was for a stormproof “bunker” that would also provide protection from other potential threats. “It’s what we do, and we were involved from the initial conceptual drawings,” said Timothy Ball, president of TCB Walls Inc. “Extensive time was spent prior to each phase to allow the crews to run them smoothly.” This included working diligently and meticulously to have all questions answered and all info in hand before sending a crew out to start a phase.
One of the special materials incorporated in the project was helix-twisted micro-steel reinforcement (TSMR), which was used extensively in the structural design. MMFX rebar was used in the structural decks around the entire structure to mitigate future corrosion issues, since the project is located on an intercoastal waterway in a saltwater environment. All concrete on the project used a high-early 5,000-psi mix, and all 28-day breaks came in around 8,000 psi.
The use of a lull with personnel baskets and cranes was vital to being able to reach some of the places on this project, as there were access restrictions protecting trees (some of which are over 100 years old) growing all around the project area.
“It is just really cool for a small company like us to be recognized for all our hard work on a national platform,” said Ball. “I feel like all the members of our team will be even more proud of the work that we do than normal. It’s going to be something for all our employees to talk about with other trades and competitors. I believe this award will elevate the project locally for our customer as well.”
______________________________________________________________________________
COMMERCIAL FOUNDATION STRUCTURE
Crossover Work Foundation
CUSTOM CONCRETE OF WESTFIELD, INDIANA
Member Since 1986

This commercial structure project is the first industrial project undertaken by Custom Concrete. The move into this market segment challenged the team, both from a scheduling perspective and a safety perspective. The team drew from experience from past projects to help them successfully handle the challenges created by scheduling and access. Relying on the general contractor gave them confidence and understanding in managing all safety requirements.
Although small — just over 1,100 square feet — this project consisted of more than 600 cubic yards of concrete and 35 tons of steel reinforcement. The footings alone had over 6 tons, consisting of #8 and #10 bars. The cast-in-place walls were 8 feet tall, some of them at 12 and 16 inches in thickness.
The most significant challenge in this project’s construction was the restricted access. All deliveries were managed through security checks, and only the daily usage was permitted on site — no schedule storage was permitted. Since the equipment for handling the materials could not be used near the installation site, the location complicated the installation of steel reinforcement, requiring most of the 35 tons to be hand-delivered down into the forming. This distance also meant that all forming baskets had to be placed into the hole using a large crane. Most of the concrete was placed under roof at a considerable distance from safe access. Our team devised a plan to use two concrete pumps set in tandem, so deliveries to one could be pumped to the next and then on to the placement positions.
The pad itself was complicated at 24 inches in thickness with double-mat reinforcement. The placement alone was time-consuming and tedious. This pad required nearly 300 inertia blocks, each isolated using 4-inch foam with 1.5-inch gaps on both sides created using ¾-inch plywood. As this was an industrial foundation project, accuracy was critical for both the footing and the finished wall elevations. Angle iron was embedded around the entire interior perimeter at the seam where the wall meets the ceiling. Coordinating this with a general contractor whose schedule was much different from ours required careful communication to set expectations and manage conflict resolution.
______________________________________________________________________________
The Best of the Rest
With a near record number of entries this year, including a whopping 11 projects in the over-5,000-square-foot category, many great works of cast-in-place concrete were recognized by the participants evaluating the entries. This year, seven honorable mentions were also selected. These included:
ABOVE-GRADE CONCRETE HOME
Main Street Residence
PURINTON BUILDERS INC., EAST GRANBY, CONNECTICUT
Member Since 1999
______________________________________________________________________________
SINGLE-FAMILY RESIDENTIAL FOUNDATION, 2,000 TO 5,000 SQ. FT.
I-4 Chatham Hills
CUSTOM CONCRETE, WESTFIELD, INDIANA
Member Since 1986
K-83 Chatham Hills
CUSTOM CONCRETE, WESTFIELD, INDIANA
Member Since 1986
______________________________________________________________________________
SINGLE-FAMILY RESIDENTIAL FOUNDATION, OVER 5,000 SQ. FT.
Cook Residence
SCW FOOTINGS & FOUNDATIONS, SALT LAKE CITY, UTAH
Member Since 1978
Victory Ranch Lot #202
SCW Footings & Foundations, Salt Lake City, Utah
Member Since 1978
Private Residence
HERBERT CONSTRUCTION COMPANY, MARIETTA, GEORGIA
Member Since 1992
Deer Crossing Lot #33
SCW FOOTINGS & FOUNDATIONS, SALT LAKE CITY, UTAH
Member Since 1978