The Survey Says…
Reinforcement Trends Facing the Market
by James Baty, Executive Director
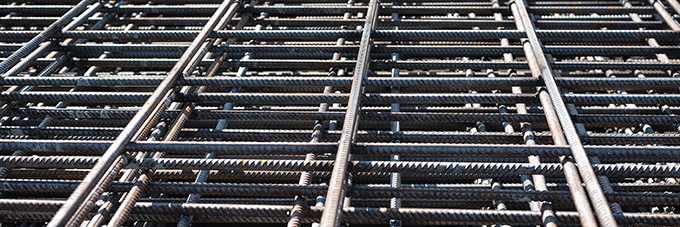
World of Concrete 2020 has come and gone. The Las Vegas Convention Center in Nevada serves as the annual home for WOC, a show that draws an average of 60,000 people each year. It continues to prove itself to be the global concrete industry’s most significant annual event.
Attendees at WOC this year were caught up in a wave of discussion and activities pertaining to labor savings. The most pervasive conversation topic among contractors in the cast-in-place industry had to have been, “What options can I pursue to offset the lack of skilled laborers I’m able to hire?” Not surprisingly, each of you reading this would likely agree — everyone is facing significant labor force challenges. What perhaps was surprising at this year’s event, however, was the subject that most contractors seemed to be testing. Concrete reinforcement — which is, for all intents and purposes, a requirement for all concrete projects — jumped to the forefront of discussions held in and around the booth for #CFAConcretePros, the home of the Concrete Foundations Association. The two most common questions about reinforcement were: 1) “What do you think of the glass-fiber rebar?” and 2) “Does anyone use rebar tying equipment?” In our search for answers, we found the products at WOC 2020 to be intriguing and engaging, but broader research of this market was conducted through surveys about experience and interest. In this article, I will summarize the premise of reinforcement as a requirement as well as the results of the survey our staff recently conducted. This article can also help prepare individuals seeking to become Certified Residential Foundation Technicians1 through the American Concrete Institute (ACI).
Concrete Basics
Any concrete basics course will tell you there are three truths to concrete: It is gray; it gets hard; it cracks. A fourth fact should be added: It can’t be stolen (compliments of a field manager for a Wisconsin-based contractor, quoted at a recent course). Most courses continue by explaining that concrete is often described or specified in terms of its compressive strength. For instance, in the International Residential Code2 and in ACI 332 – Code Requirements for Residential Concrete,3 the minimum compressive strength of concrete is set at 2,500 psi for a 28-day design strength. This is the standard for concrete, as it is relatively common to test the strength of concrete by crushing cylinders at different ages (7 days and 28 days being the most common times to test).
Concrete, while strong in resistance to compression (crushing) forces, is relatively weak in resisting forces in the opposite direction. When concrete cracks, it does so most often from the two forces we describe as tension and flexural. In fact, the engineering community knows that the tensile and flexural strength of concrete is only about 10% of its compressive strength. In order to control cracking in concrete, then, steel reinforcement has traditionally been added.
The first force, tensile, is most often an axial force created internally within the concrete due to shrinkage. Concrete is delivered into the forms as a near liquid. The chemical process of hydration consumes water in a reaction with the cementitious material, and water is evaporated from the concrete matrix by the climate. Between 7% and 18% of the concrete volume is water, with a residential code target ratio of 0.45 water to cementitious material (w/cm). The consumption and evaporation of water results in shrinkage that is generally assumed to be ¼ an inch for every 20 feet. Reinforcement is then prescribed to limit the cracks that occur naturally from this shrinkage and to control them from becoming problematic to the long-term behavior and performance of the concrete.
The second force, flexural, is best seen as the force created by backfill or wind pressure against a concrete wall or the load carried along an unsupported beam. As this load pushes or is applied against one face of a concrete member, bending results. In order for bending to occur, one side becomes shorter and the opposite side longer. The concrete face becoming shorter is called the “compression face,” as there is a force pushing inward from the ends. The face that becomes longer is called the “tension face,” and at a certain level of stress, like the crack produced from shrinkage, the face will crack. Reinforcement is prescribed to increase the amount of force the concrete can take once the cracking begins to occur from the anticipated force and to work with the concrete for long-term load behavior.
Survey Results
The science and engineering of concrete systems recommends reinforcement for virtually every type of concrete application. What does this have to do with labor, and why did it attract so much interest from contractors at the World of Concrete? This can be understood by looking at two elements of traditional steel reinforcement usage: weight and time. In a recent survey, the CFA studied the annual consumption of steel reinforcement. A sampling of 54 companies across the United States reported a total of 211,613 tons of steel reinforcement used annually, a surprisingly large number. Staggeringly, 200,000 tons of that was reported by one CFA member from California. If this contractor’s input is set aside, the industry average is 219 tons per year with 8 tons per year being the lowest reported weight and 1,000 tons the highest (aside from that residential contractor in California).
Where do you fit on this scale? Based on the current CFA contractor membership, we can project an estimated annual consumption of 240,000 tons of steel reinforcement. A former CFA board member and the contributor of the smallest quantity in the survey, Bill Mulready of C & B Foundations in Connecticut, said, “Years ago we maybe used less than a ton of rebar in a year with many more foundations. . . today, we are seeing a lot more than just rebar in footings and walls.”
With all of this weight inventoried, loaded on trucks, delivered to job sites and then unloaded stick by stick by your workforce, is it any surprise why so many companies were looking at the non-steel reinforcement bars found at WOC 2020? Owens Corning, the manufacturer of PINKBAR®, has recently joined the CFA as a National Associate member to begin promoting labor force improvement.
“PINKBAR™ has roughly 1/4 the weight of a comparable steel reinforcement bar, most traditionally #4 or #5 in the residential marketplace,” states Ashish Gandhi, Business Manager for PINKBAR™ Fiberglass Rebar. “We have already seen the response by concrete contractors to the significant stress reduction this product brings their workforce and are excited for the opportunity to partner with the CFA to rationalize this to a broader audience. Companies cannot overestimate the value of lowering the weight that has to be hauled and placed on these job sites within the most common bar sizes.”
Bearing in mind the two different elements of steel reinforcement described earlier, the product is used in the residential concrete industry in three major areas: slabs, footings and foundation walls. Each respondent affirmed that 100% of their steel reinforcement was distributed between these applications. Figure 1 shows the percentage of each application of steel presently being used. The weighting shows that the overwhelming majority of steel applications is in foundation walls. In fact, the aggregate totals show that 68.9% of all steel is placed in walls, 31.4% in footings, and only 16% in slabs-on-ground.
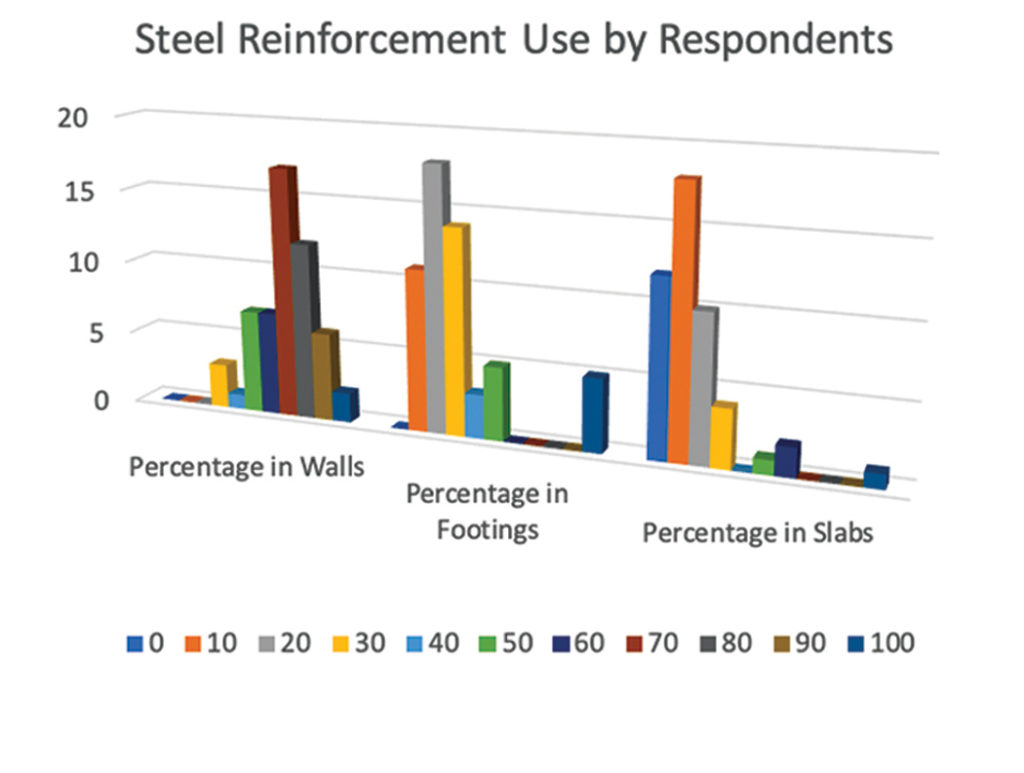
When selecting steel reinforcement for slabs-on-ground, there is a decision to be made between the principle types of rebar: welded-wire mats and rolled-wire. While the latter was a common product a couple of decades ago, construction quality has moved the industry further and further away from such a decision. Realizing that a contractor may use more than one type of product depending on the project design, specifications, and their own preference, the survey quantified the current market. 86% of respondents reported that they use steel rebar in slabs. 69% said welded-wire mats — a rigid, thick-gauge product that has a much higher load capacity before bending — was used on projects. Still, 20% of respondents reported continuing to use a rolled-wire fabric or mesh to reinforce slabs-on-ground. An indication of the need for continuing education in the industry, several contractors added comments related to the inability to ensure placement of steel when it is the rolled product. In total, 44.7% of the slabs-on-ground market appears to be using steel rebar while 48.4% is using a combination of the wire reinforcement options.
In addition to the steel reinforcement percentages noted above, a percentage that amounts to roughly 7% remains. Our survey inquired about the use of fibers in the marketplace. It is worth mentioning that many projects, particularly slabs-on-ground projects, may use a combination of fiber reinforcement (for durability and plastic surface shrinkage performance) and steel reinforcement (for load, shrinkage and temperature movement performance). There are also structural fibers in the marketplace, as has been represented during Concrete Foundations Convention, most recently with Helix™, presented in Denver in 2019. There will be further education offered in Charleston in 2020 (July 23–25) for a broad range of fiber products and application considerations. The survey sought to separate experience with traditional reinforcement products from that of experience with the increasing variety on the market for randomly mixed and steel alternatives. Figure 2 demonstrates that highest familiarity is with the synthetic, non-structural fibers, and there are varying lower levels of experience in structural products.
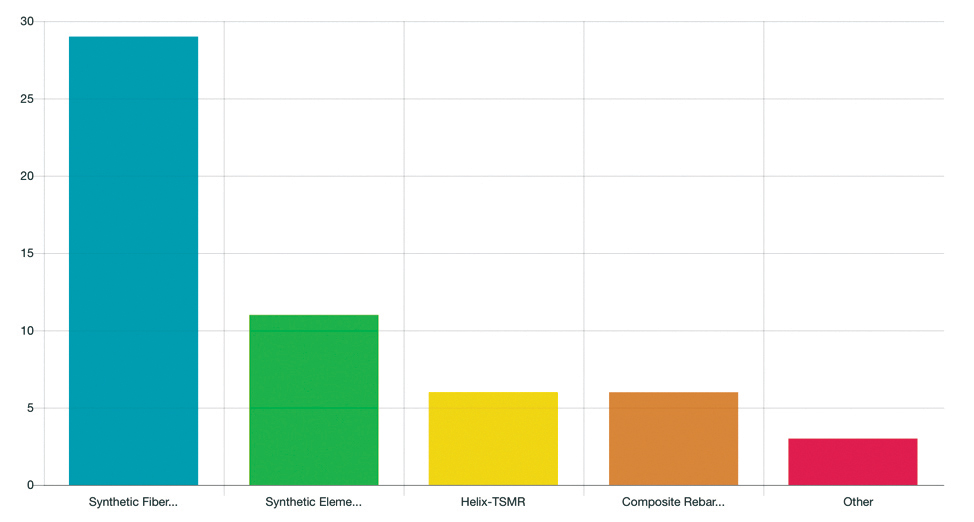
While these products, often described as reinforcement “replacement” products, are a strong source of interest for reducing the cost of labor and the pressures on limited workforce engagement, companies representing them are quick to point out their advantages in addressing the real reinforcement needs for concrete. Each has specific properties that, when properly applied, reinforce concrete more appropriately than the current steel reinforcement approach.
The survey’s final research goal was to determine the methods for securing reinforcement when using traditional steel. The residential concrete codes call for all steel reinforcement to be secured in place, which is often assumed to mean tied in place. There are traditional, or at least historical, methods for tying steel in place. One of these is the use of rolls of wire, cut and twisted around steel using pliers. Another is a tie known as the “loop tie,” which uses ends of pre-tied loops bent around steel at an intersection, then grabbed with a hook-end tool and spun or twisted until tight. There is also a new form of technology that has been increasing in popularity over the last decade, perhaps best described as a mechanical tie gun. Any intersection of steel is quickly grabbed by wire that shoots out of this gun and spins together tightly in a split second. A single crew member can secure an entire framework of steel reinforcement in half the time it takes three laborers hand-tying. Through the survey, it is evident that this growth of technology has had a significant impact on the labor market, as 48% of all respondents are already using mechanical tie systems. Max USA, a leading manufacturer of the tie gun technology, has recently joined the CFA as a National Associate.
“Being first to market with a battery powered rebar tying tool, MAX has witnessed the growth in the use of mechanical rebar tying technology; and for great reason,” states Denene Williams, National Marketing Manager for the company. “MAX battery powered rebar tying tools offer major benefits for reinforcing steel ironworkers and the businesses that employ them. Companies that have bought into the technology have seen an increase in production capacity, reduction in labor costs, and a decline in back and musculoskeletal injuries amongst their ironworkers. The latest model, the TwinTier, is a dual wire feeding rebar tier that significantly reduces the consumption of wire previously necessary to tie rebar intersections.”
The staff from Max USA will be on hand during Concrete Foundations Convention this year to begin reaching the 51% who are still tying by hand. Of this percentage of respondents, only 5% are still using rolls of wire hand cut and pieced together for each connection.
Perhaps the most intriguing survey question asked respondents what they thought was the main cause of the lack of use of alternatives to steel reinforcement in their marketplace. In Figure 3, we see a diverse spread of the most common reasons, barriers or hurdles.
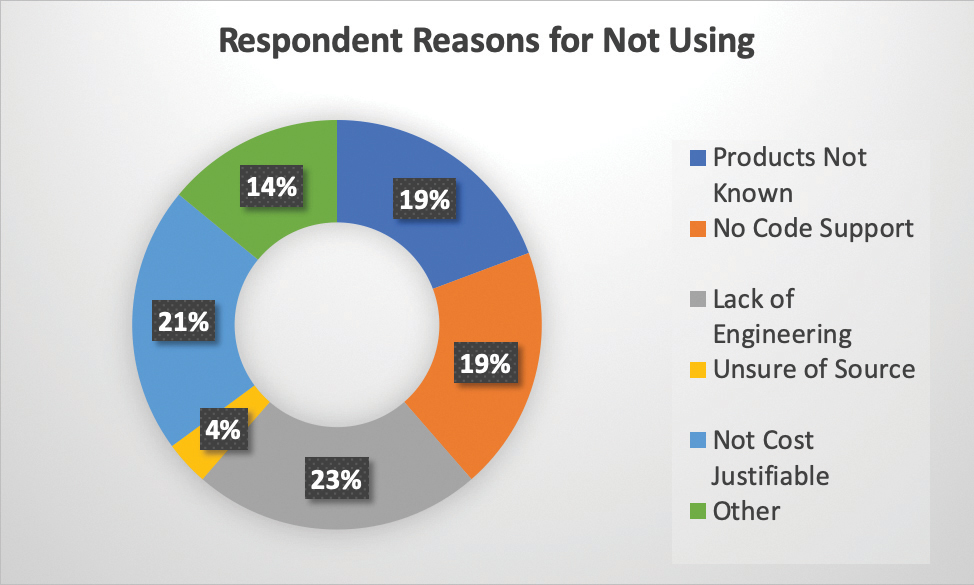
Lack of engineering (23%) was the most common reason respondents gave for a company(s) not using alternatives to steel reinforcement to date, although the reasons are similarly distributed.
“I think even though I know they conform to codes, the building inspectors here would not be accepting of them,” said one respondent. “Rebar they can see in place before the pour. Alternatives would require documentation or inspections outside of their scope.”
Another respondent said, “All foundations are structurally engineered and engineers require rebar reinforcing.” In truth, the residential concrete industry is both prescriptively directed and, when necessary, engineered with steel reinforcement. This is the standard building inspectors have been trained to use, and it is the standard they anticipate for inspections. However, building codes should create space for innovation and approval of systems not addressed by the code through alternative material submittal and approval. The IRC states:
R104.11 Alternative materials, design and methods of construction and equipment. The provisions of this code are not intended to prevent the installation of any material or to prohibit any design or method of construction not specifically prescribed by this code. The building official shall have the authority to approve an alternative material, design or method of construction upon application of the owner or the owner’s authorized agent. The building official shall first find that the proposed design is satisfactory and complies with the intent of the provisions of this code, and that the material method or work offered is, for the purpose intended, not less than the equivalent of that prescribed in this code in quality, strength, effectiveness, fire resistance, durability and safety. Compliance with the specific performance-based provisions of the International Codes shall be an alternative to the specific requirements of this code. Where the alternative material, design or method of construction is not approved, the building official shall respond in writing, stating the reasons why the alternative was not approved. [Emphasis added]
Any alternative to the prescribed methods must be submitted, evaluated and either approved or rejected with reasons for non-approval stated, which the interested party can work to remedy now or in the future. Remember, codes like the IRC (and thereby inspections) have specific intent:
The purpose of this code is to establish minimum requirements to safeguard the public safety, health and general welfare through affordability, structural strength, means of egress facilities, stability, sanitation, light and ventilation, energy conservation and safety to life and property from fire and other hazards attributed to the built environment, and to provide safety to fire fighters and emergency responders during emergency operations.
Innovative systems and products are a major reason why the Concrete Foundations Convention (Charleston, SC 2020) exists and why the advocacy of the CFA on behalf your business is such an important membership benefit. There are many more systems that contribute to this industry’s labor force reduction goals specifically related to reinforcement. For example, there are footing form brackets, like Accufooting Brace, and connectors that space, snap, and secure reinforcement for ICF and removable forms. At the Concrete Foundations Convention, so many of these systems and ideas are present, and there is plenty of time to discuss them (and it has less of a hectic pace than that of WOC).
Want to know more about this survey data or the goals and opportunities for labor force savings? Contact James Baty, the executive director for the Concrete Foundations Association.
1. Residential Concrete Foundation Technician certification program offered by the American Concrete Institute, 38800 Country Club Drive, Farmington Hills, MI 48331 | Phone: 248-848-3700 | www.concrete.org
2. 2018 International Residential Code® For One- and Two-Family Dwellings, International Code Council, Inc., 4051 West Flossmoor Road, Country Club Hills, IL 60478-5795 | Phone 1-888-422-7233 | www.iccsafe.org
3. ACI 332-14: Residential Code Requirements for Structural Concrete (ACI 332-14) and Commentary, American Concrete Institute, 38800 Country Club Drive, Farmington Hills, MI 48331 | Phone: 248-848-3700 | www.concrete.org
I’m a CNST Professor in NorCal and I found this article interesting. Look forward to others. Butte College is the school. Our program is fairly new and is both hands-on and academic. Please put me on appropriate mailing lists to share with my students. Cheers. I’m not a robot.