Controlling the Costs Surrounding Worker Place Injury is in Your Hands
…you should consider that all injuries take a toll on your company. When considering work place injuries, you should examine your pre-accident and post-accident planning.
A new client recently told me during one of our first meetings, “Every day is risk”. That same new client two months later grieves over a fatality on their job site. The story behind the event goes like this… A contractor hired a sub-contractor to perform routine work. The contract with the building owner who hired the contractor states that the contractor is responsible for OSHA compliance. The contract between the contractor and sub-contractor states that the sub-contractor is responsible for all OSHA safety standards. The contractor relied on the sub-contractor’s agreement regarding the OSHA compliance. Following the fatality, and during the OSHA inspection, it was determined that no fall protection was installed prior to the commencement of work. Assigning responsibility for safety compliance in contracts is easy to do. It is, however, no guarantee that it will get done. Unfortunately, on that day the sub-contractor chose to avoid safety compliance caught up to them as a worker plunged to his death while walking backwards with no fall protection.
We have to focus on the following thought – Safety, while always a major consideration; it is said so often it sometimes losses its practicality. We know that production and safety go hand in hand and we know that you care about your workers; we also know you are running a business and need to be profitable, and sometimes, safety takes a backseat to production. Insurance carriers classify construction risks based on what they know to be true within the industry, meaning what each of you do individually will collectively impact all of you in the long run.
A Manhattan judge Friday found general contractor Harco Construction guilty of manslaughter in the trench-collapse death of immigrant worker last year in a verdict that could set a tougher new standard for criminal liability on construction sites. Judges Kirke Bartley also found the New York City company owned by Kenneth Hart guilty of criminally negligent homicide and three of four counts of reckless endangerment, boosting Manhattan District Attorney Cy Vance's effort to use criminal prosecutions to stem construction deaths in New York City.
This article is a follow up to the emerging risks article written for the last issue of Concrete Facts concerning “Emerging Risks”. CFA members taking the recent Heat Map Survey identified work place injury as one of the top three risks that impact their company’s bottom line. We all know that not all injuries are life-ending or permanently debilitating, but you should consider that all injuries take a toll on your company. When considering work place injuries, you should examine your pre-accident and post-accident planning.
Pre-Accident
Do you believe that your company culture is safety first? Take a moment to think about whether your safety program is an active part of each and every day your company operates or if it is in a file drawer tucked away for the next new employee to sign when they begin working? Unfortunately, during the majority of visits I make to contractors, the answer is the later of the two scenario’s, and the truth is that safety manual is a procedural document viewed as necessary, but not a routine plan implemented on all job sites. I’m challenging you to consider how you run your operation and think about the following questions:
- Do you consider the cost of safety compliance as equally important to production?
- Can you be competitive in your marketplace while being safe?
- Are your employees thinking about safety prior to engaging in a task?
- Is management committed to a safety culture?
- When accidents occur are you responsible?
- Do you blame the insurance company for paying claims?
- Do you believe that being a safe company can lead to a more productive workforce?
The research institute examined 2012 claims data (the most recent available) for injuries lasting six or more days and ranked the injuries by total workers’ compensation costs.
Let’s look at the ‘10 Leading Causes and Direct Costs of Workplace Injuries’ in 2012:
- Overexertion; paid costs $15.1B (25.3%)
- Falls on same level; paid costs $9.19B (15.4%)
- Struck by object or equipment; paid costs $5.3B (8.9%)
- Falls to lower level; paid costs $5.12B (8.6%)
- Other exertions or bodily reactions; paid costs $4.27B (7.2%)
- Roadway incidents involving motorized land vehicle; paid costs $3.18B (5.3%)
- Slip or trip without fall; paid costs $2.17B (3.6%)
- Caught in/compressed by equipment or objects; paid costs $2.1B (3.5%)
- Repetitive motions involving microtasks; paid costs $1.84B (3.1%)
- Struck against object or equipment; paid costs $1.76B (2.9%)
Production and project budget goals are often the source or at least a culprit of more than half of all injuries. Can you structure a valuable balance between production and safety? Do you post signs at your company that encourage “Safety First”? Do you incentivize your employees to put safety first as a practice on job sites? If so, do you walk the walk as well?
Or is the answer through other signs the message is really “Production First”? Obviously, no one would actually post contradictory signs that say, “Production First.” The hidden message takes other forms such as production pressures and number one crew status based on production output which then carries the underlying message that suggest production is the real No. 1 priority.
Your culture must integrate safety and production so employees are empowered to make the safe choices to make sure it really is “Safety First” at your company. Consider this loss as an example of why you should put safety first.
A four-million-dollar settlement was awarded to a worker on a swing stage scaffold who was going to quickly go up and make a quick fix and made the decision not to tie off to spare time. An apprentice iron worker above accidently cut the cable on the swing stage, when the secondary cable caught hold of the swing stage the force caused the worker to slam into the bottom of the scaffold and that same force crushed both of his ankles.
The injured worker has not walked since the accident described above. Ten minutes of solid safety training and implementation would have prevented this accident. Think about how you communicate your safety message through your company, what you can change, and whether it could be the answer to eliminating some work place injuries.
Do you falsely protect your company with the thought — It will happen to someone else, but it will not happen to me… General housekeeping on a jobsite drives a lot of frivolous injuries. Rebar on the ground caused a worker to trip and hit his head on the ground just in the right spot. He became a paraplegic within three days of the incident and the total cost of the claim was seven-million dollars before his death five years after. Trips and falls are real hazards that take a few minutes to correct. When the message is production first, employees hurry, and tend to walk over things verses moving them into their proper location. I once had a client tell me that before they hired anyone they would spy on the condition of the inside of their vehicle to see if they were neat enough to work for their company, odd, but effective thinking for housekeeping on a job site.
Post-Accident
Common Insurance Company Myths
- Insurance companies pay workers’ compensation claims because they like paying big settlements to injured workers so that they can charge you more money in the future in premiums.
- Insurance companies control the outcome of workers’ compensation claims, (in actuality, you do).
- Adjusters are solely responsible for managing workers’ compensations costs.
The fact is you can make the biggest impact on your workers’ compensation claim payment totals by actively managing your employee’s, safety compliance, training, and attitude by having a credible Return-to-Work Program.
Proper Treatment of Injured Employees Is an Important Element of Successful Return-to-Work Programs
In a study titled ‘It Pays To Be Nice: Employer-Worker Relationships and the Management of Back Pain Claims,’ published in the February 2007 edition of The Journal of Occupational and Environmental Medicine, Richard J. Butler PhD; William G. Johnson PhD; and Pierre Cote DC PhD discovered that workers’ satisfaction with their employer’s treatment of their disability claim is more important in explaining successful return-to-work outcomes than satisfaction with health care providers or expectations about recovery. The researchers added that dissatisfied workers have worse return-to-work outcomes because they are more likely to have lost time claims and multiple instances of joblessness.
The study found that the 64 percent of workers polled who were satisfied with their employer’s response had a medical claim only, while the 56 percent polled who expressed dissatisfaction had lost time claims in addition to the medical claims. For those workers who do have at least one lost time claim there is a lower likelihood of frequent injury-related absences. Only 32 percent of those satisfied with their employer’s response had multiple episodes of injury related absences, as opposed to 58 percent of those dissatisfied with their employer’s response who had multiple absences.
The best way to give the injured worker this sense of belonging is through frequent expressions of sincere regard and regular communication that keeps them in the loop. If the return-to-work program incorporates these two elements, it will accomplish the goal of reducing the probability of lengthy lost time.
In the end, it really is easier than it sounds. Safety culture is a top down mentality, from the owner of the company to the supervisors on the jobsite. As the owner, you must insist on the highest standard and hold your supervisors fully accountable for safe workplaces. As the owner, you have to stop yourself when evaluating production goals to make sure that safety compliance is a fair cost consideration in every job, and that it is an efficient process that won’t delay work performance when handling job safety. When making this evaluation, understanding that safety compliance has a cost is essential. Equally essential is knowing that the higher cost will always come when safety programs and procedures fail or are non-existent. Production and safety can work hand in hand but one deserves priority over the other at all times. At the end of the day, you want your employees to go home to their families and you want to be able to sleep at night. You have the ability to control Best in Class claims outcomes by taking ownership of the claim and your employee’s path to returning to work.
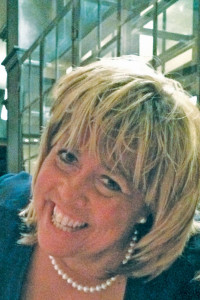
ABOUT THE AUTHOR Kristen Long is Managing Director of the Midwest Region – Construction Practice for Arthur J. Gallagher of Chicago, www.ajgrms.com. A.J. Gallagher is the broker for CFA Core360, the CFA’s member-only insurance program for complete and individualized business insurance lines specific to the cast-in-place concrete industry. You can reach Kristin at Kristen_Long@ajg.com.