What Should You Expect from 2014?
Codes, Standards, Rules, Regulations and Insurance…It is All Changing
It really doesn’t matter that your profession is the concrete industry. Were you in just about any industry, the rules for doing business and the parameters that shape your industry are likely to be changing such that business next year, perhaps even tomorrow, will most certainly be different than it is today.
Anthony Robbins is quoted as having said “If you’re not growing, you’re dying.” Perhaps a derivation of this might be “If you’re not changing, you’re being passed by.” Oddly enough, that seems to be the case as we all know that “Change is inevitable” – dd. In fact, perhaps the best way to prepare for 2014 and all of the changes that you will have to account for is best embodied by Albert Einstein who stated, “The world as we have created it is a process of our thinking. It cannot be changed without changing our thinking.” In essence, we must adapt to the changes we are given for they are nothing more than responses to the thinking continually occurring with change in mind for a changing world.
Although no one can deny that enough has changed in 2013, there are some very important characteristics of the construction environments in which you work as well as the business environments that you manage to be sure you have prepared for in the coming year. Here are a few we have been involved in or tracking and will most certainly be expanding for greater knowledge as more becomes available.
SILICA REGULATIONS – OSHA
While it seems every aspect of the construction site is already controlled for the minutia that might happen to replace common sense and responsibility? The impending regulations for control of air-borne silica are yet further example of the exhaustive measures contractors now must face.
The rule is based on the facts that inhalation of very fine particles of crystalline silica put workers at risk for silicosis, lunch cancer, COPD and even kidney disease (www.OSHA.gov). The Assistant Secretary of Labor for OSHA, Dr. David Michaels has been quoted saying, “Exposure to silica can be deadly, and limiting that exposure is essential.” The basis for regulation is the prediction that the proposed rule will save nearly 700 lives and prevent 1,600 new cases of these diseases per year.
A two-part rule, one for general industry and one for construction focuses on the processes that introduce these “respirable” particles of silica. OSHA has set up a website for information at https://www.osha.gov/silica/. Here you can gain access to the research, the proposed rule making and the remaining steps. However, the short and sweet of it for construction professionals as summarized by OSHA’s Fact Sheet for the proposed standard for construction. Under this rule, employers would have to:
- Measure the amount of silica that workers are exposed to if it may be at or above an action level of 25 μg/m3 (micrograms of silica per cubic meter of air), averaged over an 8-hour day;
- Protect workers from respirable crystalline silica exposures above the PEL of 50 μg/m3, averaged over an 8-hour day;
- Limit workers’ access to areas where they could be exposed above the PEL;
- Use dust controls to protect workers from silica exposures above the PEL;
- Provide respirators to workers when dust controls cannot limit exposures to the PEL;
- Offer medical exams-including chest X-rays and lung function tests-every three years for workers exposed above the PEL for 30 or more days per year;
- Train workers on work operations that result in silica exposure and ways to limit exposure; and
- Keep records of workers’ silica exposure and medical exams.
How does this impact the concrete foundations industry? How many concrete saws does your company own? How many foundations have your workers cutting out a notch, altering a wall profile, sanding a surface, cutting concrete blocks and a myriad of other processes that introduce the silica cut or abraded from the hardened concrete into the air.
In response to requests for an extension on the rulemaking, the deadline to submit written comments and testimony is being extended from Dec. 11, 2013, to Jan. 27, 2014, to allow stakeholders additional time to comment on the proposed rule and supporting analyses. Additional information on the proposed rule, including five fact sheets and procedures for submitting written comments and participating in public hearings, is available at https://www.osha.gov/silica/. Members of the public may comment on the proposal by visiting http://www.regulations.gov.
FALL PROTECTION – OSHA
Although it should not be a surprise to any concrete professional in the residential industry, there are still hundreds of questions being asked about the implications of the requirement for fall protection. What measures are implemented on your jobsites to provide active or passive fall protection for your workers? By the rule making completed in 2010, this industry suddenly became responsible for implementing any combination of six active fall protection measures during the construction of cast-in-place concrete foundations. These include scaffold brackets, personal fall arrest, guardrails, safety nets, ladders and aerial lifts. Under practical study and exposure to greater risk, many CFA members have generated evidence that these systems cannot provide worker safety due to technological or physical restrictions to their safety parameters or they induce greater worker stress and risk during their installation, if they can achieve protection at all.
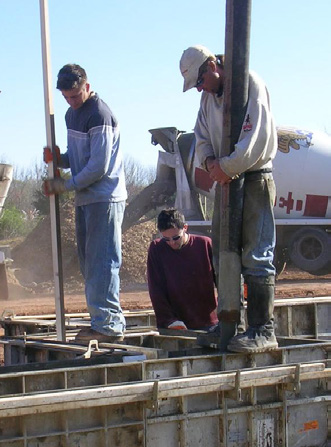
“Wall walkers” or “Wall shufflers” are an acceptable form of fall protection under 1926.502k provided a company has a formalized plan.
Work continues on the acceptance criteria and implementation of Alternate Fall Protection plans per section 1926.502(k) of OSHA’s rule. Here contractors implement a series of training, decision making, application and awareness measures to maintain the presence of fall protection on job sites under the responsibilities of trained, informed and even certified personnel.
If your company has not investigated your fall protection and determined the effective course of action, you should do so immediately and this winter is as perfect a time as any. CFA members have access to an Alternate Fall Protection Plan Kit developed to aid in the understanding and delivery of the essential components of a successful implementation. As this rule matures and as OSHA plans inspections more broadly, it will become more severe in its impact on employer responsibility. Additional work is underway to investigate a national plan or acceptance criteria for concrete foundation delivery and this may become a part of the current certification programs offered through the CFA and ACI.
CONCRETE DURABILITY REQUIREMENTS – ACI 332 STANDARD
Since its inception in 2004, the ACI 332 document Code Requirements for Residential Concrete, an acceptable alternative to the provisions of the International Residential Code, have applied concrete durability requirements similar to that of the IRC using weathering probability and a loosely-defined geographic map to set the minimum requirements.
With the pending release of ACI 332-13, the durability requirements for residential concrete will become more widely addressed to represent the breadth of exposure conditions. Concrete is prescribed by this new version of the code to be variable based on exposure to freeze/thaw cycling, sulfates and corrosive environments.
This is a similar approach to that taken by ACI 318 and offers the concrete professional and jurisdictions a more specific control of mix design for the anticipated exposure conditions. It also means that geographic reference based on maps is no longer the simple method of selecting the minimum strength requirements for concrete. Performance of concrete mix designs is largely the direction of this code and requiring greater knowledge of the conditions for delivery and service.
WORKPLACE INJURY AND ILLNESS TRACKING – OSHA
Underway is another OSHA proposed ruling that would require employers to keep a greater volume of records for workplace injuries and illness. Under this proposed rule, OSHA hopes to “improve both workplace safety and health through the collection of useful, accessible, establishment-specific injury and illness data to which OSHA currently does not have direct, timely and systematic access.” This will be accomplished by amending the workplace recordkeeping regulations and add requirements for electronic submission.
While this may be seen as only increasing the amount of clerical activity and record-keeping in an already paper laden environment, OSHA suggests that this will “not add to or change any employer’s obligation to complete and retain injury and illness records.” Their purpose is in increasing the transmission of these records to OSHA or OSHA’s designee.
The docket number for this proposed ruling is OSHA-2013-0023. It is advisable to communicate your concerns for this either electronically at www.regulations.gov or by fax to (202) 693-1648. You must include the docket reference in your response. It is likely that the CFA will only increase our recommendation for communication of concerns on this issue and we are also interested in learning your thoughts. Email me at jbaty@cfawalls.org to share your concerns privately with us. There will also be a discussion thread on this in our public “Concrete Foundations” group at LinkedIn.
COMPLIANCE SAFETY ACCOUNTABILITY (CSA)
Much information has been released by this Association on the potential impact CSA will have on your businesses. While it was instituted initially for large commercial carriers, as the efficiency of the Federal Motor Carrier Safety Administration (FMCSA) and Departments of Transportation has increased, their focus has begun to broaden. All companies that employ CDLs should expect to be impacted by this new carrier and driver rating system.
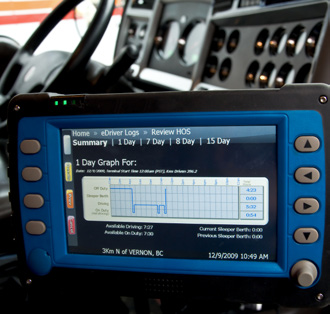
Typical electronic logging device currently pursued as a mandate by FMCSA for all commercial trucks.
Among the most recent mandates affected by this effort, the Electronic Log Mandate is certainly one you should be paying attention to. The FMCSA is attempting to complete work on a mandate in 2013 to require all truck drivers to use an electronic logging device.
Similar to the issues related to workplace recording, federal agencies are working to become as efficient as possible in the collection of data generated by the market. This particular mandate has four primary elements:
- Setting standards for the EOBR devices themselves,
- The requirement that drivers use them,
- Requirements for other hours-of-service support documents, and
- Measures to mitigate harassment of drivers by either carriers or enforcement officials.
Final ruling on these issues was expected in September but has yet to be confirmed to be in effect. CFA member, Foley Services (www. foleyservices.com), is a resource companies can contact to find out up to date information on rules and regulations affecting the transportation industry. Matt Wrobel, Vice President for Foley was present during the Annual Convention in New Mexico this past August to address the conference on the facts surrounding CSA. An update on these issues is being planned for the 2014 Annual Convention in Sandusky, Ohio (July 31 – Aug 2).
There will be more rules, regulations and changes to your business. As the authority for your industry, we are committed to keeping abreast of as many of these as possible and making sure you have access to the information that can make or break your success. If you are aware of additional pieces of legislation, code or rule making that should be made available to the industry, be sure to contact CFA Headquarters through any of our media outlets or contact points to start this discussion.