Cold Weather Concrete Pumping Tips
How to prevent or deal with concrete freezing in the concrete pump, which can stop the flow of concrete through the pipeline
American Concrete Pumping Association & Schwing America, Inc.
as seen at For Construction Pros.com
Cold weather pumping can present a variety of problems as compared to pumping in moderate temperatures. Most obvious, of course, is if the concrete freezes in the boom or other parts of the unit such as the hopper – thus stopping the flow of concrete through the pipeline.
One way to avoid this from happening is to mix the concrete using very hot water to keep the concrete from freezing during the delivery and waiting period. When priming, slurry should also be mixed with hot water. If the slurry freezes against the walls of the pipeline, it can restrict the flow of concrete causing a blockage. The pumping company can contact the ready mixed company and arrange for the first driver to be loaded with hot water for use when mixing the slurry.
Some companies will also wrap their boom pipeline with insulation. In most cases, the insulation is a foam tube cut to accommodate the pipeline, placed around the pipe, and taped together. The foam holds in the heat of the concrete allowing it to flow as normal.
Another way to keep the pipeline from freezing is to pre-heat the boom pipeline using the exhaust stack from the unit’s engine. Using an exhaust hose specifically made to withstand high temperatures, the boom operator slips the heat resistant hose over the exhaust pipe and places the other end into the tip hose of the boom – allowing its warm air to flow through the pipeline and exit from the hopper. With this procedure, it is important that airflow has an open pathway for exiting. Without an open path, the hot air from the exhaust will be forced backward and create excessive back pressure on the engine of the truck.
If the concrete should freeze in the boom, pumping will stop until the machine has been warmed up. Fortunately, concrete will stop setting when it has frozen. Once the machine has been moved to a warm place and allowed to thaw, it must be cleaned out before fresh concrete can be added and pumping resumed.
Concrete can also freeze in the unit’s hopper preventing it from entering the pipeline. When this happens, the consequences will be the same as if concrete froze in the boom. The concrete must be allowed to thaw and the hopper cleaned out before fresh concrete can be added.
Calcium chloride or other similar type additives are typically used to accelerate the setting of concrete. When using an accelerator, the concrete must be kept alive using the same techniques used for pumping on hot days. As temperatures during the day begin to rise, you should consider decreasing or stopping the use of an accelerator because the concrete can “flash” just like in hot weather.
Although calcium chloride accelerates the setting of concrete, if it freezes, the setting stops. Once the machine begins to thaw, the concrete will begin to set again even more quickly than when on the job because it is now in a warm area. Time should not be wasted when cleaning a machine under these circumstances.
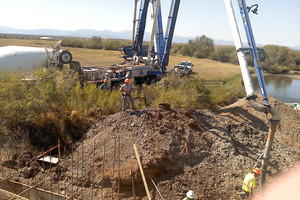
Some companies will also wrap their boom pipeline with insulation, which is often a foam tube cut to accommodate the pipeline, placed around the pipe and taped together. The foam holds in the heat…
It is also possible to pre-heat a separately laid pipeline in much the same manner as pre-heating boom pipe. Using a high-temperature resistant hose, warm air is diverted from the truck’s exhaust into the pipeline allowing it to flow throughout the system and escape out the end.
If the motion of the concrete is stopped in a frosted pipe, the heat will radiate from the concrete so quickly that the entire line can freeze completely in a matter of moments. Usually if this happens, the pour cannot be completed until the slick line is replaced, and the concrete sitting on the job will often be rejected before it can be pumped. Many dollars can be lost when this occurs.
Safety procedures
Never stand on ice-coated pipes or other round objects and use caution on the pumping unit’s decks and steps. Workers are reminded to wear the appropriate cold weather personal protective equipment and to always wear insulated gloves when handling icy pipes and clamps that can slip causing injury.
Extreme caution is especially needed during and after cleanout as all areas surrounding the pumping unit might be coated with ice as a result from the water that was used to clean out the pipes and accessories. Serious injury can occur as result from slips and falls.
Pumping concrete in temperatures as low as -10° Fahrenheit, and even lower, is not only possible but routine in many parts of the world. However, the pump’s manufacturer may prohibit use of the boom when temperatures fall well below sub-degree temperatures and the pumping company should be aware of the specific temperature restriction of their respective manufacturers. Use of the boom in extreme cold conditions will cause the steel of the boom to become brittle and cause it to crack from normal boom bounce.
Prior to the pump arriving on the jobsite, it is a good idea to communicate with your employees and/or the pumping company to discuss any conditions, such as extreme temperatures, which may have an effect on the safety and performance of the pour. Work to develop a plan which will not only ensure a successful pour but one that enables you to obtain the maximum benefits of placing concrete with a concrete pump.
Source: Schwing America, Inc.Manufacturer’s Operating Manual for Concrete Pumps
Jim, thanks for the advice to use hot water when pumping concrete in the cold weather. I also appreciate that you suggest speaking with employees and the pumping company about any conditions that might make the job unsafe. It seems like it is important to discuss all of the possible options and outcomes before starting work.
That is interesting that the pump needs to be insulated for it to work properly. It never occurred to me that the concrete could freeze inside the pipe as it was being pumped in extreme cold weather. A simple thing like blankets could really save you a lot of trouble if used properly. Thanks for these awesome concrete tips!
I thought it was interesting that in order to stop the concrete from freezing in the pipeline, you use hot water in the mixing process. That is probably the simplest way of keeping the concrete above freezing temperature but you will need to work quickly to make sure the concrete doesn’t freeze while you are working. Another way you suggest keeping the concrete warm is to pre-heat the boom pipeline using the exhaust stack from the engine. You have to be careful with this, though, because without proper care you could hurt the engine and the pipeline.
I never realized that there were different problems that could arise while pumping concrete in the cold. You mentioned that if the pipe freezes, you have to make sure that it gets thawed out. Are there different ways to do that onsite safely, or do you always have to take it somewhere warm? It seems like doing this all in the cold would be pretty tricky but when people are trained the right way, it seems possible!
Thanks for tips! I’m probably super spoiled living out here in California and don’t really get too much super cold weather. However, we do get a handful of days that can get pretty darn cold and to us it’s a bit of a shocker. So this tip are very helpful. Thanks!